In the packaging industry, the phenomenon of electrostatic charging and discharging is one of the daily challenges. Thus, food manufacturers are also dependent on processes to reduce electrostatic charge by means of ionisers – and depending on the application, as precisely, efficiently and energy-savingly as possible.
Manufacturers have to resort to various processes during production, among others, to dissipate the naturally occurring static electricity. „Since electrical charges always seek to balance each other out, forces arise that cause packaging to stick together, for example, or attract particles such as dirt and dust. And especially with food, a particularly high degree of purity must be guaranteed for quality assurance,“ says Tobias Fritsche, Product Application Manager at SMC Deutschland GmbH, Egelsbach.
To meet these requirements, the food industry must therefore resort to ionisers that can be used to reduce the electrostatic charge during the production process. Which type of ioniser should be used depends on the packaging form, the material or the production processes. What is particularly important? An overview of the various methods for the different areas in food packaging is provided by examples from automation specialist SMC.
Rapid discharge on a grand scale
From roller conveyors for films or paper to filling processes for packaging films to polystyrene packaging or conveyor lines for PET bottles: In cases where large packages or packaging materials are processed, static discharge must also take place over a large area. Depending on the application, ionisers in rod or blower design are particularly suitable here. The blowers of the IZF series from SMC, for example, enable a comprehensive reduction of static electricity even around a workpiece. Depending on the material, weight, stability or the possible degree of contamination, rather low volume flows in the range of 190 to a maximum of 800 litres of air per minute or in the high range of 1,300 to a maximum of 4,400 litres per minute are considered.
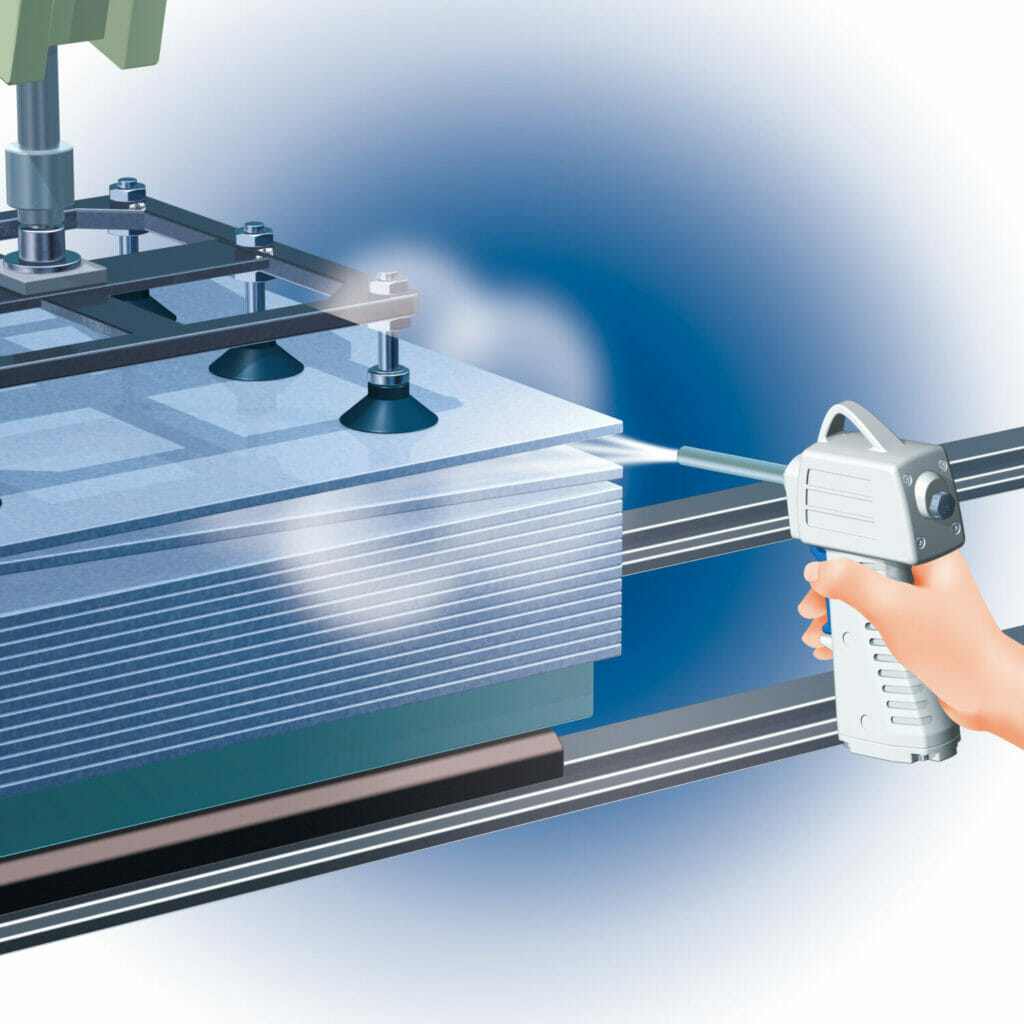
With the latter, static discharge at the highest air flow and a distance of 300 millimetres succeeds from 1,000 to 100 volts in only 0.5 seconds. This ensures stable transport of PET packages, for example, and prevents them from repelling or attracting each other on a conveyor belt and ultimately sticking together, as is the case with polystyrene packages.
The ionisers of the IZT40/41/42 series in rod design, for example, enable an even faster reduction of static electricity: the corona discharge takes place in the same order of magnitude in the IZT41 series in just 0.1 seconds. With rod lengths from 160 to 2,500 millimetres and the option of additionally combining them with a nozzle ioniser, they are suitable for various applications. Moreover, due to the separate controller to which up to four ionisers can be connected, they consume less space and thus also offer more flexibility. „This makes electrostatic neutralisation particularly easy, for example with film rolls or film-coated objects, and prevents dust or filling material from sticking, as well as winding errors due to creasing,“ Fritsche points out.
Targeted unloading and cleaning
The cleaning and discharging of the inside of plastic bottles or cups, as well as with conveyor belts that offer very little space and where the electrostatic discharge is only to take place in a limited area, have other requirements. In such cases, nozzle designs are the first choice, as they allow the static electricity to be dissipated very precisely or in hard-to-reach places by means of appropriate attachments. For example, SMC’s IZN10E series can be equipped with various nozzle shapes: From a circular diffusion nozzle to a rod nozzle (either for one-sided or circumferential diffusion) to a bendable hose nozzle.
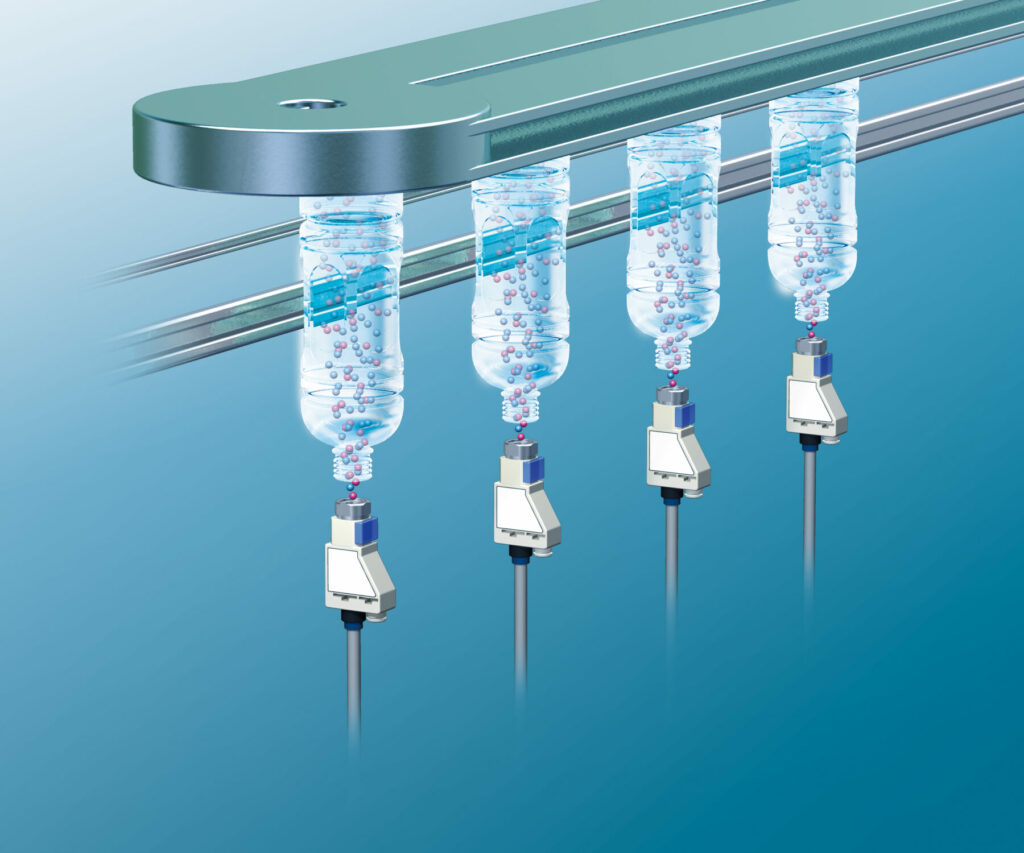
Since they work with compressed air, the ions are transported to the workpiece more quickly, which accelerates the discharge on the one hand and thus makes higher cycle times possible. On the other hand, larger distances to the workpiece can be realised. In addition, dust and dirt particles can be subsequently blown away by the compressed air. Basically, the flow rate varies per supply pressure per nozzle and can be controlled by the user. If, on the other hand, dust or particle swirling is to be prevented, users should resort to devices such as the IZT43 series, which optionally also works without compressed air and thus only dissipates static electricity.
Ionising by hand
For uneven or edgy packaging, a particularly high degree of flexibility is required. „This is where automatic processes reach their limits. Instead, humans still fulfil the best prerequisites for performing such special tasks due to their freedom of movement and comprehension,“ explains Tobias Fritsche. The tools used for this are ionisers in so-called pistol design, which are guided and operated by hand. In order for the manual work to be carried out efficiently and with low stress, both in terms of easy handling and occupational safety, certain requirements have to be met. In addition to high performance, this also includes simple and safe handling. The pistol ioniser of the IZG10 series, for example, weighs only 200 grams in the version with a standard nozzle. Operators also have the option of choosing between the two operating modes „continuous blowing air“ or „impulse blowing air“. On the one hand, this enlarges the field of application, and on the other hand, it fulfils the requirement for particularly economical operation.
More packaging news
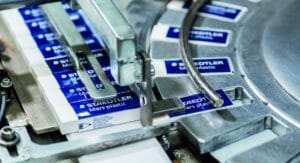
A contract with a handshake is valid
Managing director Tina Gerfer of Wilhelm Rasch Spezielmaschinenfabrik has modernized the company and successfully guided it through difficult times.
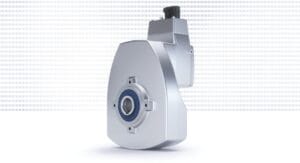
Asynchronous servo solutions for the packaging industry
From primary packaging to final packaging, electric drives play an important role. With a broad portfolio, Nord Drivesystems supports customers.
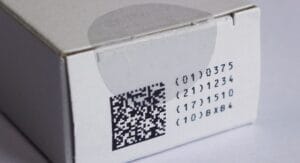
Label Durability
Labels offer many functions which can get lost due to label removal. PTS assesses labels and cardboard for durability and tamper evidence.
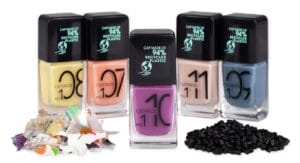
More design for recycling for cosmetics packaging
Packaging for decorative cosmetics is very special. The Forum Rezyklat calls for the recyclability of packaging to be taken into account when designing it.
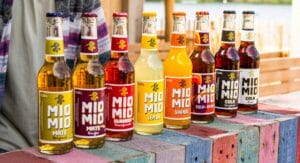
Innovation Barometer 2024
According to a survey conducted by Aktionsforum Glasverpackung 2024 is set to be a highly innovative year for glass packaging.
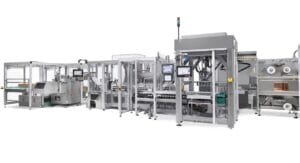
Flexible packaging system for natural cosmetics
Sustainability is part of Weleda’s identity. IWK is also contributing to this with its new flexible packaging line for many natural cosmetic products.