Sustainability is part of Weleda’s identity. All areas of the company are committed to sustainable management – from the extraction of product raw materials, their processing, filling and packaging, placing on the market through to recyclable packaging. IWK is also contributing to this with its new flexible packaging line for many natural cosmetic products.
Weleda is the world’s leading manufacturer of certified natural cosmetics and anthroposophic medicines with a product portfolio of more than 1,000 medicines, a large number of manufactory products and 120 natural cosmetics. The company invested in a turnkey packaging line from IWK Verpackungstechnik for the „Skin Food“ and „Pomegranate“ care ranges and other applications at its largest German site in Schwäbisch Gmünd. The particular challenge was the variety of products and their different formats and volumes that were to be filled and packaged on the line. The flexible packaging line is automated and safely processes both aluminium and plastic tubes in different sizes. Collaborating robots (cobots) ensure automated processes at the beginning of the line at the tube filler.
State-of-the-art tube line on a limited area
Weleda’s request to IWK for a high-performance, automated packaging system for filling, cartoning and packaging certified natural cosmetic products were made in the run-up to Weleda’s 100th anniversary. The aim was to replace an outdated packaging line at the Schwäbisch Gmünd site with the largely automated and flexible IWK turnkey system with as little disruption to production operations as possible.
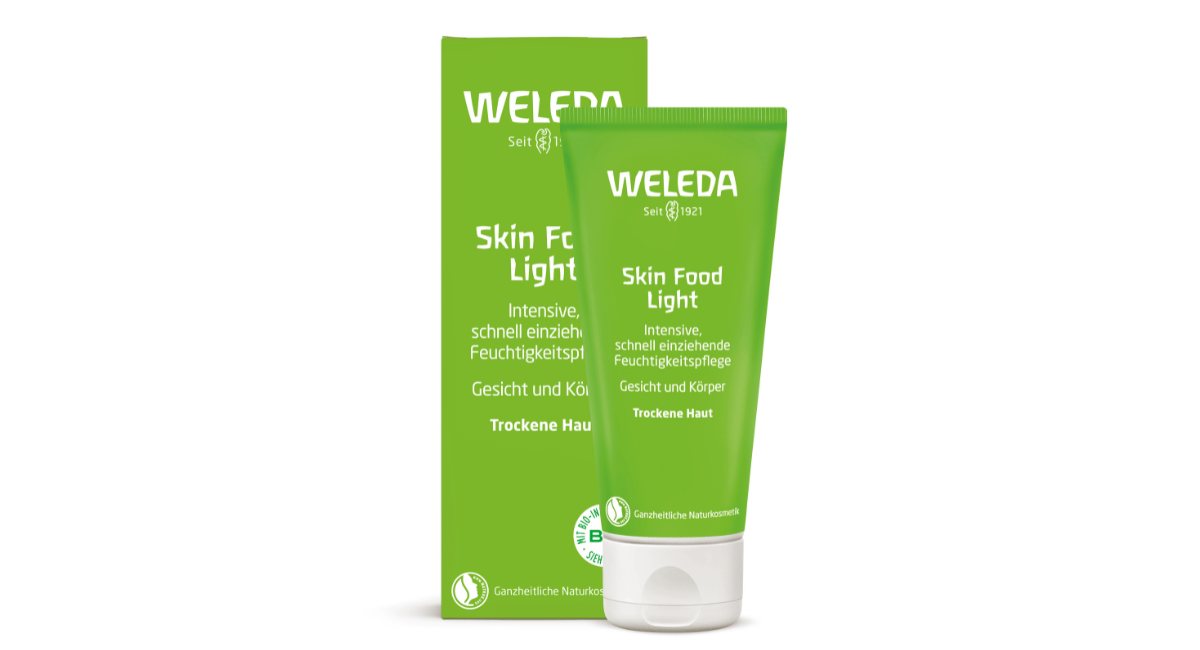
The successful natural cosmetics series „Skin-Food“ from Weleda. The tube is filled on the IWK line and packed in the folding box.
(Image: Weleda)
The entire tube line, including the upstream and downstream automation solutions, had to be designed to fit into the existing production building – a particular challenge. The tube line could not be laid out in a row of machines one behind the other, as is generally the case, but had to be set up in a U-shape due to the limited space available. Creating the technical design was a complex task, even for the IWK product engineers, which was ultimately solved thanks to many years of experience and the excellent cooperation of the Weleda-IWK project team.
At the heart of the technical solution is a flexible IWK FP 64-2 tube line with two filling heads and a maximum filling capacity of 220 tubes per minute with maximum process reliability. The modern control and drive technology with energy-efficient servo drives enables automated height adjustment of the 64 tube holders, precise positioning and safe transportation of the tubes in the work stations as well as quick and easy format changeovers.
Weleda processes sensitive cosmetic products here. The filling area is therefore designed with smooth surfaces in accordance with GMP (Good Manufacturing Practice) guidelines, is easy to clean throughout and has excellent accessibility from all sides. On the commissioned system, Weleda uses dosing cylinders adapted to the required volumes for filling into different tube materials and tube shapes. In general, the IWK FP system in this series can safely process filling volumes from 1.5 to 350 millilitres.
Automation across the board
Cobot-supported modules are installed upstream of the tube filling system. The special feature is the flexibility with regard to primary packaging. Both conical and cylindrical tubes can be processed without long changeover times. A DPC depalletizing cobot with two pallet stations continuously feeds the empty tube cartons into the tube feeders. The emptied cartons are then dismantled by a TDC tray disassembly unit to save space. The tube infeed (DPC, TZC and TDC) is controlled centrally. The FP tube filling system is equipped with a Pharmacode scanner and a print mark sensor for image alignment. The empty tubes are placed in the tube holders, aligned and filled. The tubes are then sealed either with folding tools for metal tubes or using a hot-air unit for the plastic versions. The sealed tubes are marked by embossing or laser in the fold and can then be labelled.
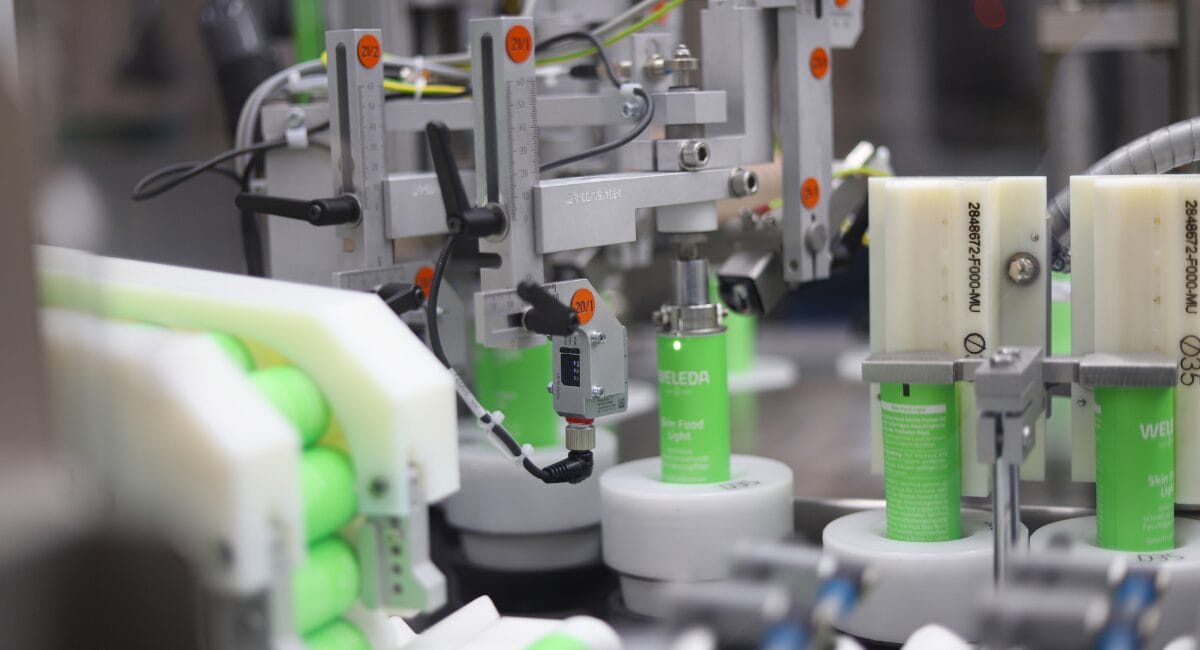
Positioning the empty tubes in the tube holders in the filling area of the IWK FP 64-2 line. (Image: IWK)
Downstream of the filling area is an in-line weighing system with 100 percent weight control including trend control. It offers sufficient space for customer-specific requirements. A pick & place arm then places the so-called good tubes into the forming cups of the XTS linear transport system.The individually driven transport carriages of this collection system ensure that empty spaces from tube filling are compensated for, thus ensuring a constant product flow to the connected IWK FeedCell robot cell. This enables the machine manufacturer to guarantee full packaging units at all times.
The FeedCell, which is flexible for different product configurations, either feeds the tubes to the IWK SC 4 HS horizontal cartoner for packaging individual tubes in folding cartons or places them in the mini-trays provided. These are automatically erected from a flat blank, loaded and closed. Particular attention was paid here to the safe transportation of the folding boxes or mini trays to the finished sales unit in bundles of 5, 6 or 8.
Securely boxed, bundled and packaged
A cycloidal system with counter suction cups patented by IWK ensures reliable erection of the folding carton. The tubes are continuously inserted together with a folded leaflet. The cartons are closed, either embossed or laser marked with variable data and then bundled with film and packed in an automatically erected shipping tray. The mini trays reach the shipping trays without film wrapping. A palletizing system positioned at the end of the line (EOL) then places the individual shipping trays on a pallet according to a predefined pattern, each of which is then provided with a label. These complex production processes are technically highly demanding in themselves and their interdependence. IWK’s project management succeeded in implementing the project without a hitch to the satisfaction of the client, Weleda.
Project management with synergies
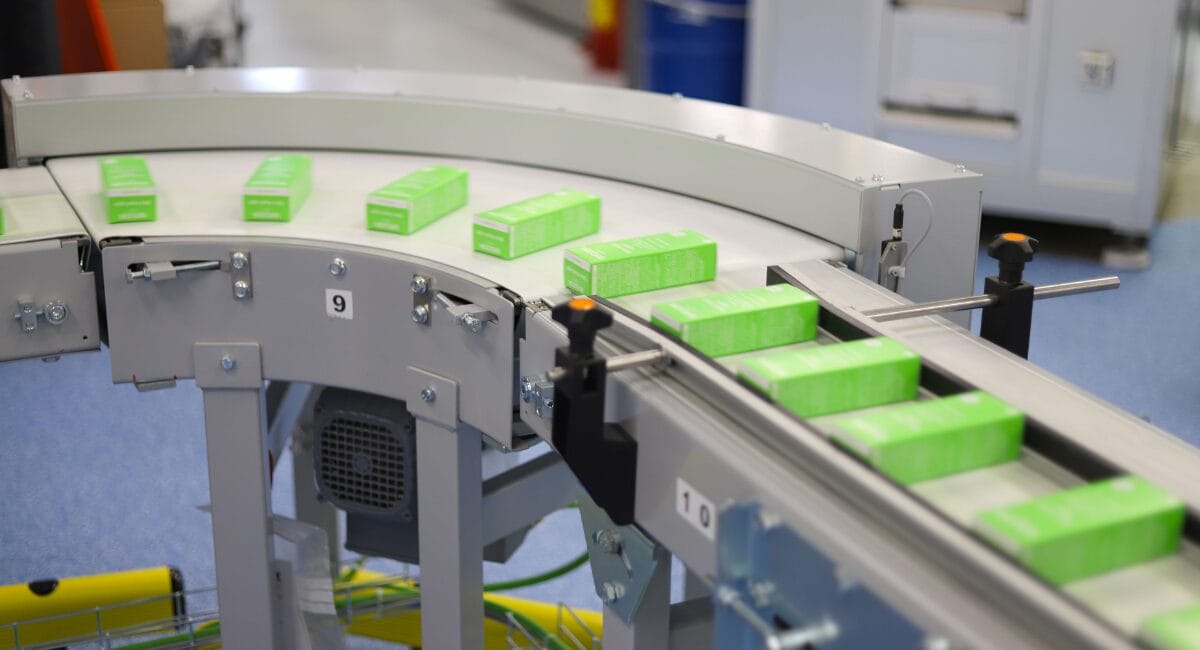
Filled folding cartons on their way to being bundled into shipping units. (Image: IWK)
„The project was an absolute novelty for our production area. The order value, team size and number of machines in a line were unprecedented. All the employees involved were highly motivated to support this investment and innovation,“ says Weleda’s Industrial Engineering Team Leader Paola Nell, describing the situation for the team involved in the project. The turnkey line for natural cosmetics was commissioned even before the global coronavirus pandemic. What nobody could have foreseen at the time were the unforeseeable project safeguarding measures due to the pandemic in the coming period.
However, it turned out that those responsible at Weleda and IWK in the joint project management team had an excellent rapport and communicated very well with each other. Despite the adverse circumstances, IWK facilitated a two-week training course for production and technology on-site in Stutensee. This was necessary because Weleda placed very high demands on the documentation. The effort involved was comparable to that in the pharmaceutical sector.
„Here too, IWK fulfilled all our wishes and delivered comprehensive documentation in top quality.“
Paola Nell
However, it was not only the pandemic-related difficulties, including a lockdown during commissioning, that caused the team problems. During the project’s lifespan, there were several changes to the primary and tertiary packaging materials and also a relocation of two tube formats from external to Weleda in-house at the start of production.
„Thanks to IWK’s expertise and experience and the motivation of the fitters to work on the machines with Maske for three weeks at a time, the project was a complete success. Even after acceptance, IWK was always on hand and continued to support us by phone, email or short-term on-site visits. If only all projects went this well.“
Paola Nell
Logistical masterpiece
Following the successful training of the Weleda employees and the factory acceptance test (FAT) in Stutensee, the next step was to dismantle and transport the machines to Schwäbisch Gmünd in eight forty-ton trucks. The sequence of the machines to be transported was crucial to ensure that the installation on site would be successful due to the limited space available. During this phase of the customer project, in particular, additional service providers were added who had to be instructed precisely. Thanks to their extensive experience and numerous completed projects, those responsible at IWK knew exactly what needed to be taken into account when planning, transporting and precisely moving the Weleda packaging line into the customer’s premises.
„Together with the forwarding company, we measured and determined the exact positions of the individual machine locations at Weleda. That was millimetre work. I would particularly like to emphasize IWK’s competent project management, which coordinates such large-scale projects with different suppliers perfectly.“
Barbara Otrzonsek, Area Sales Manager at IWK
Two years after commissioning, the IWK packaging line is running in stable condition and produces around 80,000 units of the highly successful Skin Food range every day. The project managers at Weleda are satisfied and pleased with the performance, even though the complexity of the seven formats means there are always challenges to overcome. An internal continuous improvement project (CIP) at Weleda continues to support and promote the success story of the line.