From primary packaging to final packaging, electric drives also play an important role in all processing phases in the packaging industry. With a broad portfolio of synchronous and asynchronous solutions, Nord Drivesystems supports realising different requirements. The slimline asynchronous servo solutions also meet the demanding requirements for precision and dynamics in the food sector. This saves customers space in the control cabinet, reduces cabling costs and relieves the load on the higher-level PLC.
Head of Marketing at Nord Drivesystems (Nord), Jörg Neimand, explains: „Our solutions in the packaging industry cover the primary, secondary and end-of-line sectors. We have many years of experience in the industry and develop high-quality and sustainable drives that meet the requirements of various applications in the packaging industry.“ The company’s global network offers worldwide service, supporting customers locally on-site from development to commissioning.
Drive technology in hygienic design
In the primary packaging sector, food, pharmaceuticals and other hygiene-sensitive products are often packaged. Drive systems in these applications must therefore be easy to clean and resistant to chemical cleaning agents and possible contamination. „To meet the requirements in the primary packaging sector of the food and beverage industry, we offer our FDA-certified drives up to protection class IP69K,“ says Niermann.
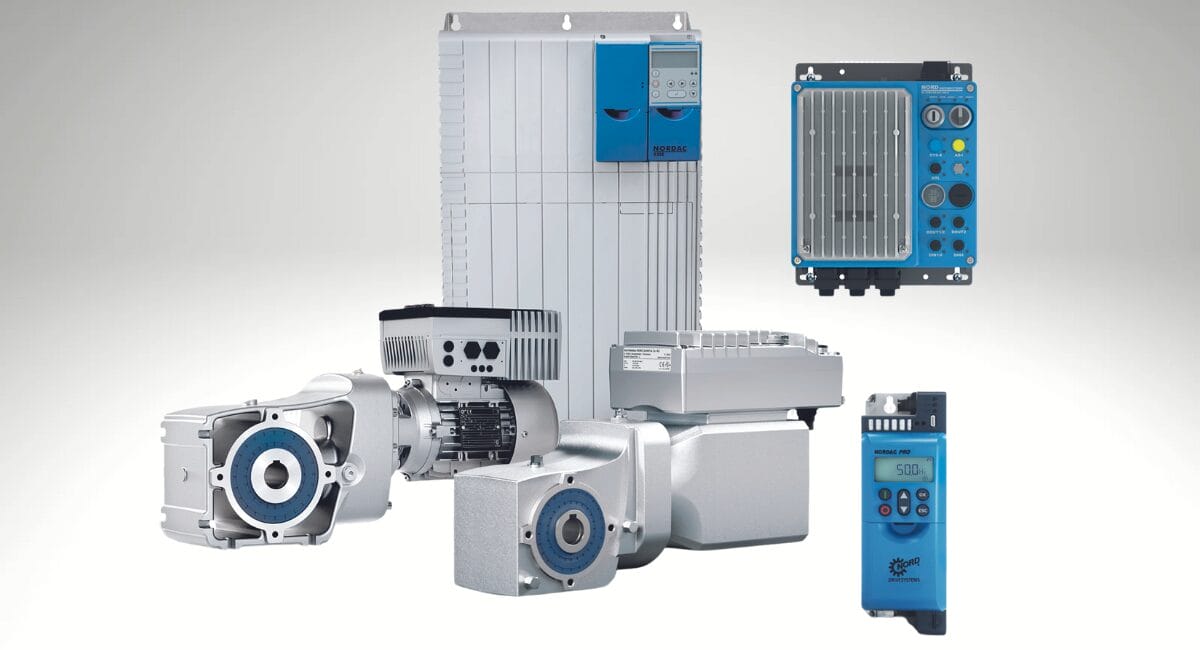
Nord’s portfolio includes decentralized drive electronics up to 22 kW, for the control cabinet up to 160 kW. (Image: Nord Drivesystems)
Nord also has modular and flexible worm gearboxes from the UNIVERSAL SI or SMI series with smooth surfaces in its portfolio. Further advantages are their low weight in the aluminium version, their high overload capacity as well as their low-noise operation and smooth running. Nord’s patented DuoDrive with its hygiene-friendly design can also be used in splash water areas. It combines a highly efficient IE5+ synchronous motor with a single-stage spur gear. With its optimized system efficiency and high power density, it is ideally suited for conveying applications in the splash water zone of the primary packaging area. Together with the simple plug-and-play commissioning, this results in a significant reduction in the total cost of ownership (TCO) compared to other drive systems.
Efficient drive for secondary packaging
In the secondary packaging sector, electric drives have become much more popular than pneumatic drives in recent years. Nord offers efficient drive solutions for the machines used in this area, which are used in the conveyor belt and labelling applications, among others. For example, the manufacturer’s electric motors are an economical alternative to pneumatic cylinders for erecting, loading or closing cartons. Nord’s worm gearboxes for implementing simple and fast movements with large gear ratios are also an advantage here.
Expertise in final packaging
Palletizing machines must function smoothly so that product flows do not come to a standstill and can be flexibly adapted to different applications. They often require dynamic drive solutions and precise positioning in multiple axes.
„For applications with high inertia or long travel distances in the end-of-line area, such as palletizing, pallet stabilization or pallet handling, oversized drives with centrally controlled synchronous motors are often used, where the drive electronics are housed in the control cabinet. We offer more efficient and economical solutions.“
Jörg Niermann
Nord has a modular and flexible product portfolio for packaging machines and supplies drive solutions for various performance levels – including both synchronous and asynchronous motors (IE3 or IE5+) with parallel shaft gearboxes, helical gearboxes or bevel gearboxes and centralized or decentralized frequency inverters.
Servo drives with synchronous or asynchronous motors and motor-mounted frequency inverters enable significantly leaner and more efficient drive solutions than with a classic centrally controlled synchronous motor. The frequency inverters from the Nord modular system are quick to install, easy to operate and compatible with all standard bus systems and control systems. Useful features such as PLC functionality for drive-related functions, an energy-saving function for the partial load range, POSICON positioning control, integrated brake choppers for four-quadrant operation and functional safety with STO and SS1 guarantee a high level of application benefit. The inverters perform open-loop or closed-loop and are designed for the operation of asynchronous and synchronous motors. The precise current vector control can achieve the optimum torque in a wide range of load and speed situations. They can also perform numerous functions and drive tasks.
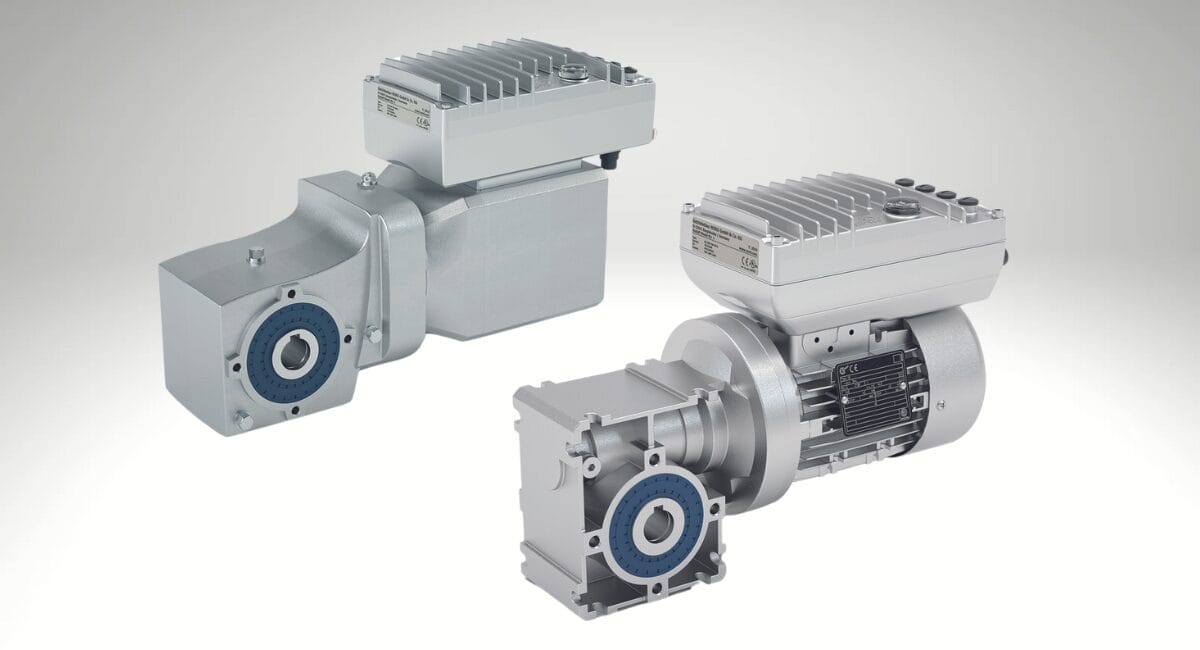
One inverter, two variants: NORDAC ON for operation with asynchronous motors (front in the picture) and NORDAC ON+ for combination with synchronous motors (rear in the picture) (Image: Nord Drivesystems)
The simplest variant includes an IE3 asynchronous motor with a gear unit tailored to the application and a plug-in decentralized NORDAC BASE SK 180E frequency inverter (0.25 to 2.2 kW). For standard applications, Nord also offers an IE3 asynchronous motor with a suitable gear unit and a NORDAC ON SK 300P (0.37 to 0.95 kW), for positioning applications the NORDAC FLEX SK 200E (0.55 to 22 kW) frequency inverter and for energy saving requirements a highly efficient IE5+ synchronous motor in combination with the NORDAC ON+ SK310P.
Asynchronous motors with decentralized frequency inverter
In the past, the Dutch mechanical engineering company SYMACH relied entirely on central drive controls. This required control boxes mounted on the top of the machine, which took up a lot of space and caused additional costs. They also hindered access during maintenance work, so the company decided to convert and has been using Nord’s compact drive units ever since. On the recommendation of the drive expert, the decision was made to use dynamic and lean asynchronous technology instead of the oversized centrally controlled synchronous drives as part of the modernization.

The NORDAC FLEX is the most flexible inverter from Nord. It has a wide range of available outputs, a large range of functions and a wide range of accessories. (Image: Nord Drivesystems)
SYMACH palletizing machines place each product individually on the pallets. A specially designed head enables precise and gentle handling. The three to four-meter-high machines are fed via a conveyor belt and the goods are picked up by a manipulator. Bags, for example, slide against a fixed stop and are aligned by a centring unit so that the manipulator can drop them exactly at the programmed position. This enables precise and overlapping stacking with optimum stability. Different stacking patterns and speeds can be programmed. The pallet table is lowered during the stacking process until a defined height is reached. The fully loaded pallet is then transported via a roller conveyor to a wrapping machine, also manufactured by SYMACH, and finally wrapped in film.
The geared motors from Nord with frequency inverters from the NORDAC FLEX SK 200E series mounted directly on the motor have proven their worth in controlling the complex motion sequences of the gripper and the centring unit of the palletizing machines and are significantly more economical than the previous solution: „The advantages of this solution are not only lower procurement costs but also greater choice for the machine designers, as asynchronous motors are available everywhere, are easy to maintain and can be easily combined with different types of gear units,“ explains Niermann. In addition, they are easy to replace in the plug-in version. „If you add up all these advantages, palletizers equipped with decentrally controlled asynchronous motors have lower total operating costs than those with servomotors.“ This makes them a good example of further development with added value thanks to Nord’s expertise and products.