Just in time for the start of the new year, Weber Maschinenbau GmbH, Breidenbach, has announced that it has changed its name to Weber Food Technology GmbH. This means that the company’s identity is now also directly visible in the company name and transparent worldwide. But what is behind it?
Food producers around the world are constantly driving forward the automation of their production and are demanding that they obtain processing and packaging lines from a single source. Machine and plant manufacturers in the food industry must also adapt to this and adjust accordingly. Weber has already responded to this development in recent years with a comprehensive transformation from machine manufacturer to solution provider, positioning itself more internationally and placing the needs of customers even more strongly at the centre of all activities and developments. The main focus here is on the development and provision of solutions for food processing, particularly for fresh food with a critical shelf life.
We spoke to Tobias Weber, the eldest son of company founder Günther Weber and CEO of the company, about the development steps, the results already achieved, plans and visions. He is also the driving force behind the company’s technical direction.
Your company has established a leading position within the industry in the area of sliced meat production and later packaging but has also continuously expanded its portfolio in recent years to include solutions for other areas such as piece goods, snacks and convenience products. Mr Weber, what were the main features of the development stages?
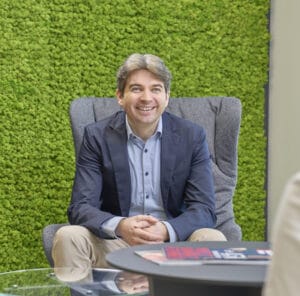
(Image: Weber Food Technology)
Tobias Weber: In principle, it was a gradual process. However, the starting signal for the major and rapid changes was given in 2017, when we integrated the packaging machines into our portfolio. From then on, we realised quite clearly that our customers no longer wanted to buy machines, but solutions. Accordingly, our goal was no longer „just“ to assemble machines into a line, but to design the entire line ourselves and supply it from a single source. In order to fulfil this aim, we had to develop many new products along the slicing line and the process. That in itself is a major challenge because you want to be quick to market with every development. But despite our ambition, it was always important to us not to lose sight of our customer promise. And that is to offer uncompromising quality, pioneering innovations and outstanding service. In concrete terms, this means that quality must be right and must not be neglected due to the speed of development. Our service technicians had to be made fit for many new products within a very short space of time, and at the same time, we have greatly expanded our team of service technicians.
Another point I would emphasise is that project complexity also increases when you offer complex systems. This has a major impact on the entire company. Everything has to be planned and the entire organisation has to be adapted to new processes and working methods, new ways of working together and higher-level responsibilities.
Being quick to market with new products, maintaining high quality, building up the service team and adapting to the complexity of the processes were therefore the biggest challenges. What has already been achieved in the course of the transformation? Are there any solutions that you would particularly emphasise?
Tobias Weber: Firstly, I would mention our core area of sliced meat production. Here, we now supply everything from a single source, from product preparation to labelling the finished packaging. A current example is the slicing and packaging of bacon. The new complete solutions that we have recently launched on the market eclipse everything previously known in bacon production in terms of performance and degree of automation. And that’s not so easy, because not all bacon is the same. Both the blanks and the packaging forms differ greatly from country to country. All of this requires completely different automation solutions, which is why we have different solutions in our portfolio that are tailored to the requirements of each target market.
We have also developed and implemented fantastic solutions in the area of food automation. One highlight is certainly our solution for automatically filling, sandwiching and packaging baguettes. We cut open the baguette roll, unfold it, cover it with several layers of different sliced products, close it, place it in the packaging, pack it for the first time, add a sauce and finally pack the product. That’s what we mean by a complete line. This was one of our biggest projects last year and is a further development beyond just cold cuts.
We are also launching more and more solutions on the market in areas that no longer have anything to do with cold cuts, such as the automated packaging of piece goods.
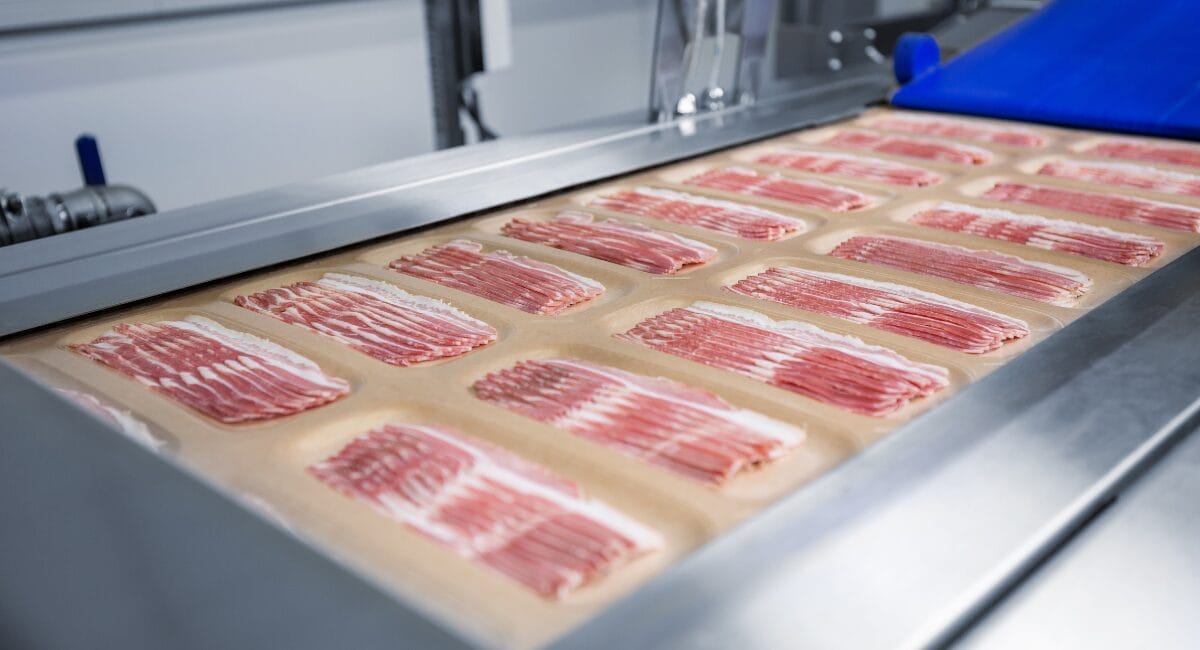
With Weber PaperTech technology, paper-based bottom films can be moulded much better, more stable and deeper into packaging. (Image: Weber Food Technology)
Why did you choose this point in time for the renaming?
Tobias Weber: The transformation has been seamless. Last year, we merged all of our German companies into one company in order to minimise the high administrative costs. The fact that the various individual components of a line were manufactured at different company locations, for example, the camera for the scanner in Braunschweig, the slicer in Wolfertschwenden, the slicer blade in Groß Nemerow, the buffer in Neubrandenburg, the picking robot in Breidenbach and the packaging machine in Werther, caused an enormous amount of bureaucracy. The processing resulted in a veritable madness of quotations, order confirmations and invoices. And after the merger, we thought: The whole thing deserves a new name that reflects „more than mechanical engineering“. Weber Food Technology expresses our identity much better and is also meaningful internationally. But despite all the changes: Weber remains Weber.
What projects are you currently working on? Which users are they tailored to?
Tobias Weber: Our home is sliced meat production and we are growing from here. We are focussing primarily on enquiries from our existing customers. These could be customers from the cheese sector, for example, who now want to cut and pack cheese cubes in addition to sliced cheese, or customers from the meat and sausage sector who are interested in the automated packaging of piece goods.
The field of alternative proteins is also very interesting. Our major advantage here is our in-house knife production and development with our own materials laboratory. Slicing products made from alternative proteins is usually very demanding. This requires, among other things, a perfectly suitable slicer knife. And if anyone can develop a knife specifically for these products in the shortest possible time, it’s us. Another aspect is that today we don’t even know for sure whether we will be slicing or dicing. We may soon be looking at 3D-printed products. We want to be ready for that too.
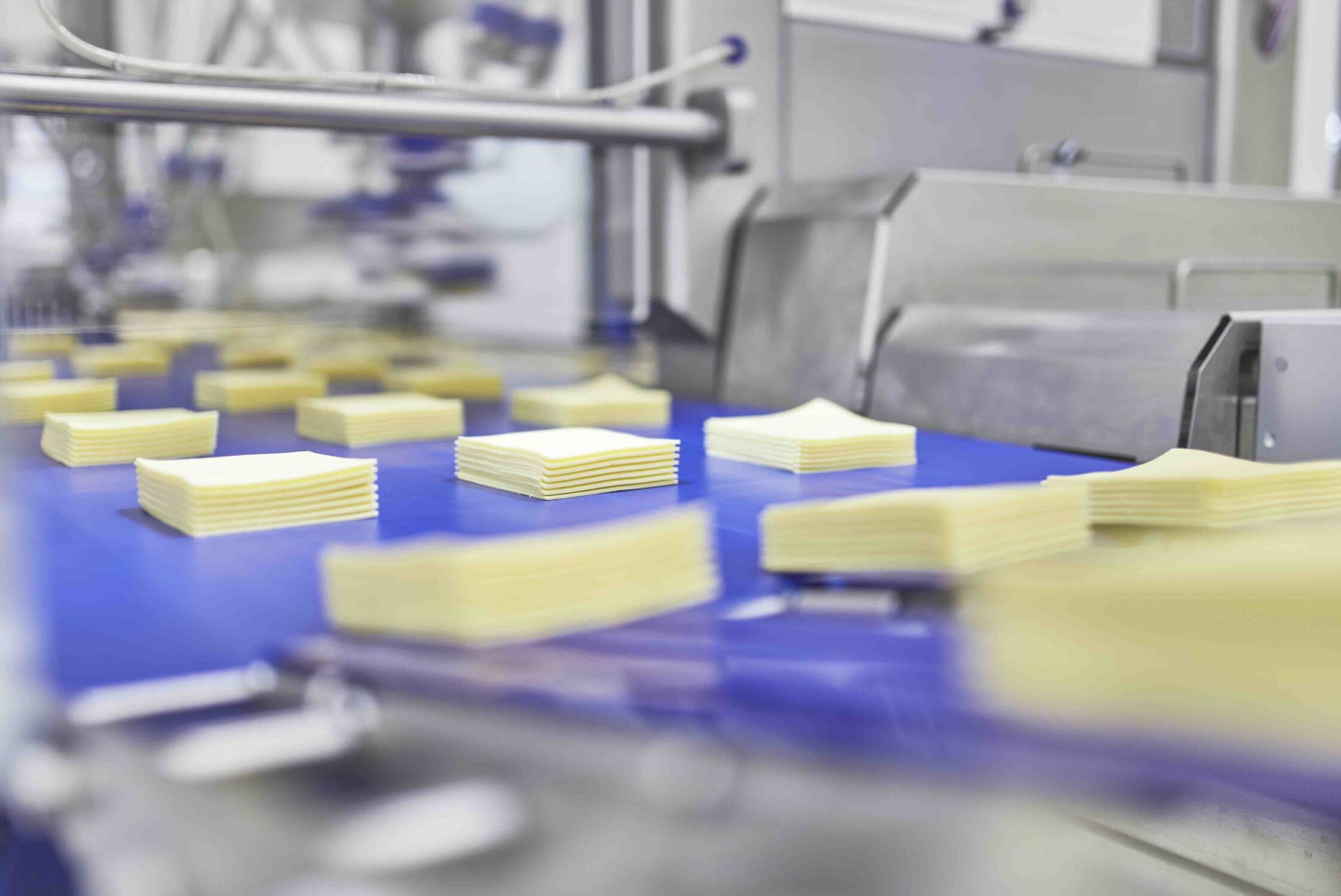
The precise slicing of products made from alternative proteins, such as vegan cheese in this case, is demanding and requires, among other things, a perfectly tuned slicer knife. (Image: Weber Food Technology)
We also see great potential in the automation of snacks and convenience products such as filled baguettes, sandwiches, ready meals and pizza. We are growing very strongly in these fields of application, which are still quite new to us – the last few years have already seen above-average success and we expect strong growth this year too. In the automation sector, we have developed many solutions and realised many projects in recent years and will continue to work on further new solutions. We anticipate the needs and developments of the market and want to be ready with solutions when the market is ready.
You respond to the demands of the market with complete solutions and visionary forward thinking for new product variants. When you think about your goals for the next few years, which visions are particularly important to you (personally and for the company)?
Tobias Weber: It is particularly important to me that we remain relevant as a company in the coming years. That we are needed. I am sure that it will become increasingly difficult for food producers to find enough suitable labour. On the other hand, the global demand for food will continue to grow because the world’s population is growing. Against this backdrop, I think it is extremely important to automate food production as much as possible so that people can be supplied with as little labour as possible. We want to tackle this together with our customers.