Eine Vakuumpumpe anstelle fünf, mehr als 50 Prozent Energieeinsparung und deutlich reduzierte Wartungskosten: Über dieses Ergebnis freut man sich am größten Käseproduktionsstandort der DMK Group im nordwestdeutschen Edewecht, nachdem dort ein neues Vakuumsystem von Busch Vacuum Solutions in Betrieb genommen wurde.
Neben Produkten für den Lebensmitteleinzelhandel produziert die DMK Deutsches Milchkontor GmbH Käse für die Großindustrie in 15-Kilogramm-Blöcken. Diese Euroblocks sind 500 Millimeter lang, 300 Millimeter breit und 100 Millimeter hoch. Die Käseblöcke werden in der Verpackungshalle des Unternehmens für den Transport vorbereitet. Dafür werden sie an den vier in der Halle stehenden Verpackungsmaschinen automatisch in Kunststoffverpackungen geschoben. Um diese Beutel zuvor zu öffnen, ziehen an jeder Verpackungsmaschine vier Vakuumsauger die Unterseiten der Beutel auf. Eine einzige MINK-Klauen-Vakuumpumpe von Busch Vacuum Solutions, die Teil eines eigens für diesen Prozess konstruierten Vakuumsystems ist, realisiert dies an allen vier Verpackungsmaschinen.
Lieferant des deutschen Lebensmitteleinzelhandels (LEH)
Als größte Molkereigenossenschaft Deutschlands zählt DMK zu den bedeutendsten Lieferanten des deutschen LEH. An über 20 Standorten in Deutschland, den Niederlanden und weiteren Ländern veredelt das Unternehmen jährlich etwa 5,5 Milliarden Liter Milch, die von mehr als 4.400 landwirtschaftlichen Betrieben stammen. Für seine Hauptmarke Milram produziert die DMK Group Käsesorten wie milden Gouda, nussigen Burlander und herzhaften Müritzer. Darüber hinaus stellt es eine Vielzahl weiterer Molkereiprodukte her. Das Repertoire reicht von deutscher Markenbutter über Quark, Joghurt, Sahne, Kondensmilch bis hin zu Speiseeis und Babynahrung.

Vakuumverpackte Käseblöcke in der Verpackungshalle von DMK. (Bild: Busch Vacuum Solutions)
Vakuum reduziert Energieverbrauch und Wartungsaufwand
Das MINK-System versorgt mit nur einer einzigen aktiven Pumpe alle vier Verpackungsmaschinen gleichzeitig mit Vakuum. Vor der Umrüstung waren für die Verpackung der Käseblöcke vier einzelne trockenlaufende Drehschieber-Vakuumpumpen im Einsatz, je eine an einer Verpackungsmaschine. Diese Pumpen liefen bis zu 24 Stunden an sieben Tagen in der Woche mit voller Drehzahl und waren mit jeweils 75 dB(A) pro Pumpe sehr laut. Sie standen im Verpackungsraum, sodass die Mitarbeiter dort erheblichem Lärm ausgesetzt waren.
Im Verpackungsraum ist die Luft zudem feucht und salzhaltig, da Salz in der Käseproduktion eine wesentliche Rolle spielt. Verstärkte Korrosion und ein erhöhter Verschleiß mechanischer Teile in den Pumpen waren die Folge. „Deshalb war zweimal im Jahr ein Schieberwechsel an den Drehschieber-Vakuumpumpen nötig, und es kam auch immer wieder zu Totalschäden“, erklärt Georg Backer, Teamleiter der Instandhaltung, der nach einer energieeffizienteren, leiseren und weniger reparaturanfälligen Lösung suchte.
Hohe Leistung und berührungsfreies Funktionsprinzip
Die Vakuumspezialisten von Busch empfahlen dem Kunden die neueste Klauen-Vakuumtechnologie, die effiziente MINK MV. Zusätzlich wurde entschieden, die Vakuumanlage in einem separaten Raum unterzubringen. Mit dieser Maßnahme konnte die Lärmbelastung der Mitarbeiter erheblich reduziert werden – obwohl die Anlage mit 68 dB (A) ohnehin schon vergleichsweise leise läuft. Die Pumpe ist so auch der salzhaltigen Feuchtigkeit nicht mehr im gleichen Maße ausgesetzt wie im Verpackungsraum, und die Teile werden geschont.
Darüber hinaus ist in das Vakuumsystem von Busch ein Standfilter integriert, der der Pumpe vorgeschaltet wurde. Er benötigt aufgrund seiner vertikalen Ausrichtung nur wenig Platz, ist leicht zu reinigen und schützt sie zusätzlich vor Beschädigungen durch Verunreinigungen. Besonders freut sich der Instandhaltungsleiter aber über die Energieeinsparungen durch das neue MINK-System. „Im Vergleich zu den Drehschieber-Vakuumpumpen verbrauchen wir nun mindestens 50 Prozent weniger Energie“, resümiert Georg Backer.
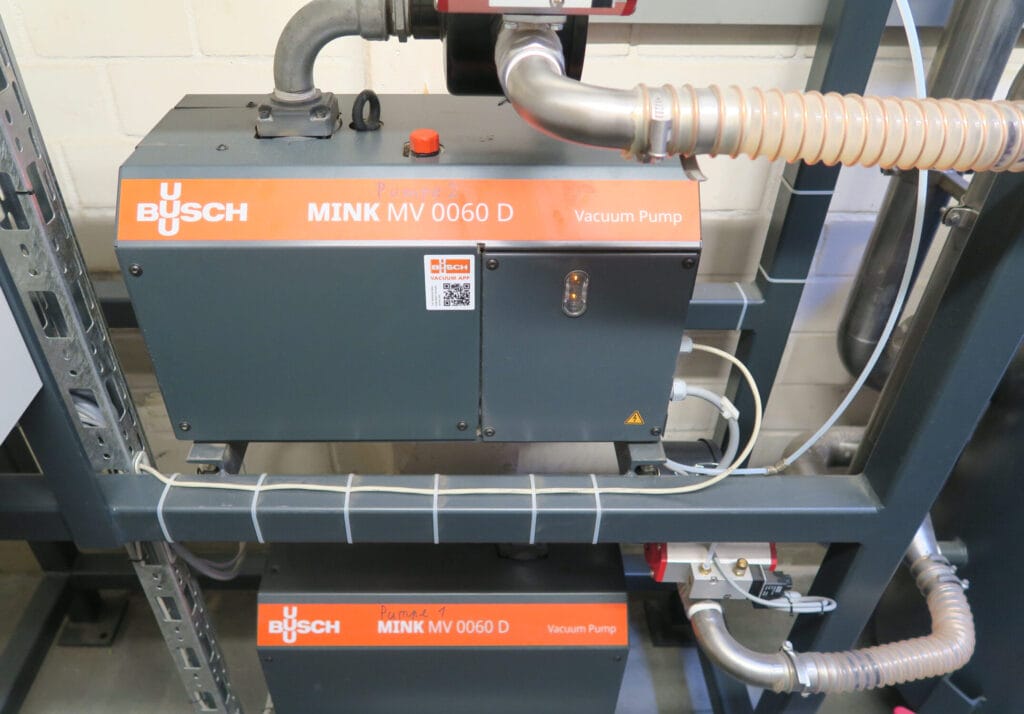
Das Vakuumsystem im Einsatz bei DMK. (Bild: Busch Vacuum Solutions)
Dank des berührungsfreien Funktionsprinzips der MINK benötigt diese keine Schmiermittel oder Betriebsflüssigkeiten im Verdichtungsraum, sodass es keinen Verschleiß gibt, der sich negativ auf die Leistung auswirken könnte. Dadurch sind MINK-Vakuumpumpen besonders energieeffizient und können annähernd wartungsfrei betrieben werden. Dies zeigt sich auch bei DMK, wo keine Pumpenausfälle mehr aufgetreten sind, seit die Vakuumversorgung beim Käseverpacken auf das neue System umgestellt wurde. Durch das neue System hat sich deshalb auch der Wartungsaufwand der Vakuumversorgung für Georg Backer und seine Kollegen deutlich reduziert. „Früher waren zehn Reparaturen pro Jahr nötig, und wir mussten im Schnitt fünf neue Vakuumpumpen kaufen. Jetzt warten wir stattdessen nur noch maximal einmal im Jahr und haben trotzdem null Störfälle,“ betont der Teamleiter der Instandhaltung.
Außerdem verfügt das bei DMK eingesetzte System über einen intelligenten Antrieb mit Drehzahlregelung. Das bedeutet, dass ihr Motor zu Beginn der Evakuierung der Beutel, in die der Käse verpackt wird, mit hoher Drehzahl läuft, sodass möglichst viel Luft angesaugt wird. Sinkt der Druck in den Beuteln, geht auch die Drehzahl des Pumpenmotors zurück. Dadurch wird weniger Energie verbraucht als bei einer ungeregelten Vakuumpumpe, deren Motor immer mit voller Drehzahl läuft. Auf diese Weise werden Energieverbrauch und Betriebskosten zusätzlich minimiert.
Zusätzliche Betriebssicherheit
Das neue System arbeitet an sieben Tagen in der Woche bis zu 24 Stunden täglich. Um jederzeit eine lückenlose Vakuumversorgung gewährleisten zu können, verfügt es über zwei identische MINK MV, von denen fast immer nur eine in Betrieb ist. Die andere dient als Back-up. Da das System bisher noch nicht ausgelastet war, entschloss sich DMK dazu, zusätzlich einen Kartonaufrichter einzubinden. Dieser wurde zuvor von einer eigenen Vakuumpumpe versorgt, um die Faltzuschnitte anzuheben und aufzustellen. Aber auch jetzt ist die Leistungsfähigkeit des MINK-Systems noch immer nicht voll ausgeschöpft, sodass es weitere Funktionen übernehmen könnte.