Suppliers such as the long-established German company Uhlmann Pac-Systeme meet the complex requirements in the field of pharmaceutical packaging with innovative strength and solution expertise. With the new PTC 200 packaging centre and digitally based services, the company from Baden-Württemberg addresses the complex field of strategic requirements in which pharmaceutical companies, generics manufacturers, CDMOs and packaging service providers operate today.
The pharmaceutical packaging sector is facing a whole bundle of strategic and technical challenges. What is needed are solutions that allow companies to react flexibly to changing market requirements – and to do so without compromising process stability and compliance with legal and regulatory requirements. Even before the COVID pandemic and the global increase in vaccine development and production, parenterals were one of the most dynamically growing segments in the pharmaceutical market. This has not changed since the pandemic subsided: The number and market share of medicines that do not enter the patient’s organism via the intestine, but are administered as injections, infusions or inhalations, continues to grow.
While vaccines are usually produced and packaged in relatively large batches, many other parenterally administered drugs fall into the area of personalised medicine. This means that the quantities produced and packaged here are significantly smaller than for other drug classes. In addition, therapeutically successful parenterals often change their dosage form in the product cycle: the aim of the manufacturers is to develop an infusion, which may only be applied by medical professionals in the clinic, into a product that can be easily administered in a doctor’s office or is even suitable for self-medication. This means for the filling or packaging companies: The products that pass through the filling and packaging lines change more frequently. This means more changeover, cleaning and clearance effort – and thus a growing risk for the stability of the processes.
Increased pressure from politics and society
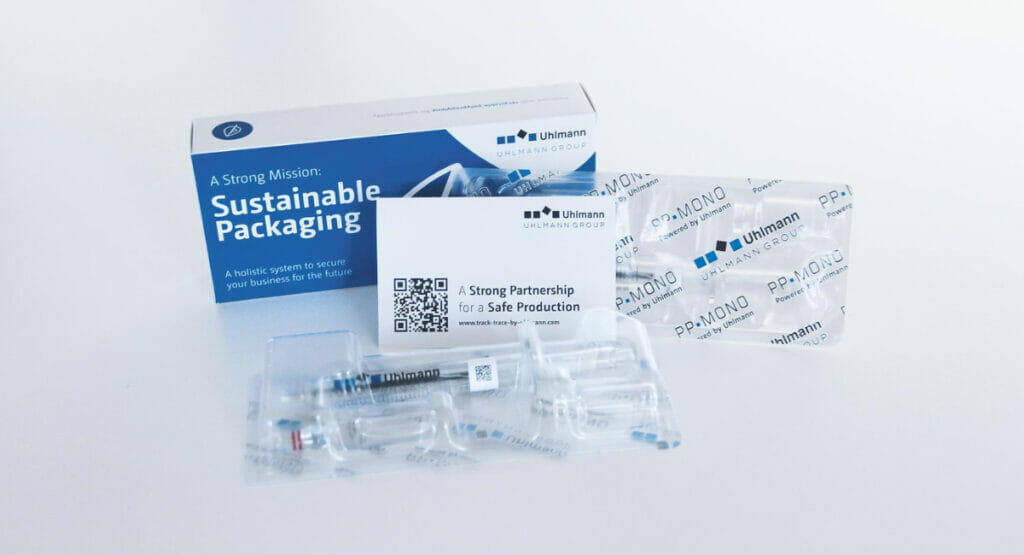
But parenterals place special demands on process safety: Primary packaging such as syringes, vials and ampoules are often made of glass and fragile. Even minor inattention or inaccuracies in the process can lead to failures in the machine running time or in the packaged products. The active ingredients are also usually highly sensitive to vibration or temperature fluctuations. To ensure the efficacy of the drug, packaging lines must not only work with corresponding precision and stability, but the entire process must also be seamlessly monitored and documented. In addition, there are the regulatory requirements for device tracking and product counterfeit protection: Depending on the regulatory requirements, all companies involved in the production, filling, packaging process and delivery must make the central process data traceable down to the individual vial or ampoule.
Until recently, sustainability criteria played almost no role in the design and implementation of packaging for parenterals. In this way, parenterals are no different from other medicines and medical devices: Particularly from a regulatory point of view, the focus in packaging development was sensibly on its protective function and safe handling. Here, conventional, often poorly recyclable multi-material packaging made of plastics and cardboard could hardly be beaten in terms of costs, process reliability and user-friendliness. This situation is currently changing. Worldwide, the focus on recyclable and environmentally friendly packaging solutions with the smallest possible CO2 footprint is being significantly increased, and pharmaceutical and medical products are no longer exempt from this. After all, the pharmaceutical industry is responsible for more than four percent of net annual greenhouse gas emissions – and is even ahead of the automotive industry. Medical professionals, patients and the general public are also increasingly demanding more sustainable processes and solutions from the pharmaceutical industry.
Politicians are also increasing the pressure and are in the process of introducing new regulations for more sustainability. For example, a plastic tax has been in force in the UK since April 2022, and a similar tax will come into force in Italy and Spain in 2023. Other EU states are relying on other financial or regulatory mechanisms to significantly reduce the amount of non-recycled plastic waste. The EU states are thus reacting to a requirement of the EU Commission within the framework of the European Green Deal. But even beyond the EU, the reduction of plastic and plastic packaging has high priority in the climate and environmental strategies of many countries. Strict plastic bans are already in force in some African countries. For the Asian economic area, the introduction of taxes and levies on plastic packaging that can be recycled poorly or not at all is expected.
Flexible packaging of medicines thanks to modular design

For products that are not very sensitive in terms of process technology, such as tablets, it is relatively easy to switch to packaging materials that are easy to recycle. Especially since there are now enough suppliers on the market, especially in the area of monoplastics such as mono-PP film, that a second-source supply is assured. And the success of packaging solutions such as the BEC 400 from Uhlmann Pac-Systeme shows that the demanding handling of mono-PP films has also been reliably solved in the solid blister sector.
Making packaging for parenterals sustainable places even higher demands on the process and material. This is because the parameters of parenterals packaging already described do not change: fragile primary packaging, sensitive active ingredients, high demands on track-and-trace processes, smaller batches and even changing product formats. With the Parenteral Tray Center PTC 200, pharmaceutical manufacturers and service providers now have a cartoning solution that can handle a wide range of packaging materials, formats and closure mechanisms as well as up to six parenteral products.
The gain in terms of sustainability lies primarily in the flexibility of the packaging material: the PTC 200 loads plastic trays just as reliably and safely as trays made of cardboard or paper fibre. Cardboard or paper fibre trays are available in numerous formats and are aligned with international climate protection guidelines – such as the Carbon Disclosure Project (CDP), the United Nations Global Compact (UNGC) and the Global Reporting Initiative (GRI).
But even beyond that, the flexibility of the machine concept is impressive: the modular design of the machine allows the use of up to three different feeder modules and up to six different automatic or manual product feed systems. Thanks to the different, quickly changeable feeding systems, the PTC 200 packs syringes and needles, vials, ampoules and cartridges just as reliably as pens, injectors or other products. This means that the complete life cycle of a medicine can be covered. Customers with the PTC 200 have a similarly broad range of closure options: Push-in closures and tamper-evident closures with hotmelt standard up to the fourth flap are possible, as are folding boxes that can be opened from the top.
Set up or changed over to new product or packaging formats, the PTC 200 is amazingly fast: a complete changeover can be done by two people in half an hour. No special training is required from the personnel operating the PTC 200. The SmartControl operating system guides the operator intuitively through the format changes and provides support during operation. This ensures optimum process reliability and fast commissioning, even by less experienced staff.
More packaging news
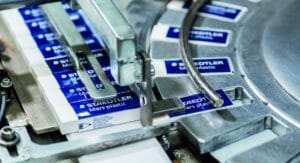
A contract with a handshake is valid
Managing director Tina Gerfer of Wilhelm Rasch Spezielmaschinenfabrik has modernized the company and successfully guided it through difficult times.
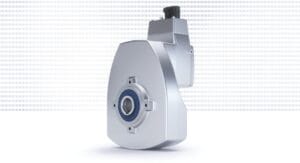
Asynchronous servo solutions for the packaging industry
From primary packaging to final packaging, electric drives play an important role. With a broad portfolio, Nord Drivesystems supports customers.
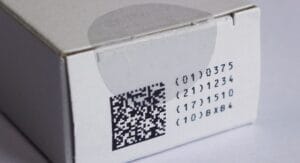
Label Durability
Labels offer many functions which can get lost due to label removal. PTS assesses labels and cardboard for durability and tamper evidence.
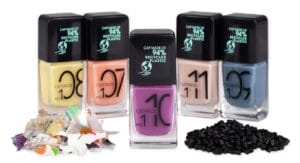
More design for recycling for cosmetics packaging
Packaging for decorative cosmetics is very special. The Forum Rezyklat calls for the recyclability of packaging to be taken into account when designing it.
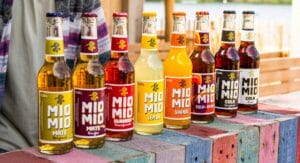
Innovation Barometer 2024
According to a survey conducted by Aktionsforum Glasverpackung 2024 is set to be a highly innovative year for glass packaging.
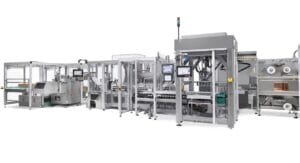
Flexible packaging system for natural cosmetics
Sustainability is part of Weleda’s identity. IWK is also contributing to this with its new flexible packaging line for many natural cosmetic products.