Modern automation and robotics solutions enable an optimal balance between productivity and user-friendliness. This provides solutions that are scalable both upwards and downwards. In this way, they contribute to making packaging and palletising processes fit for the factory of the future.
New strategies and technologies are needed to ensure the efficiency of packaging processes for products with a large number of variants in small individual quantities – keyword: High-Mix-Low-Volume (HMLV). For manufacturing companies and co-packing service providers who have to realise this packaging variety, there are a number of things to consider before a shelf-ready mix pack can be delivered. To meet growing consumer demand for more variety, this approach is now present in all fast-moving consumer goods (FMCG) markets, especially in higher-priced product segments such as personal care or confectionery.
Robot-assisted automation solutions provide shooting assistance
Smart robot-based automation solutions can help reduce the need for the manual labour involved in high-volume and low-volume production. Such solutions include robotic picking, packing, palletising, machine tending and optimised automated intralogistics. Robot-based automation provides companies with the flexibility, productivity and reliability they need to deal with ever-shorter product life cycles, changing packaging designs, different packaging sizes and product variants. Various typical application challenges and solution options show what this can look like.
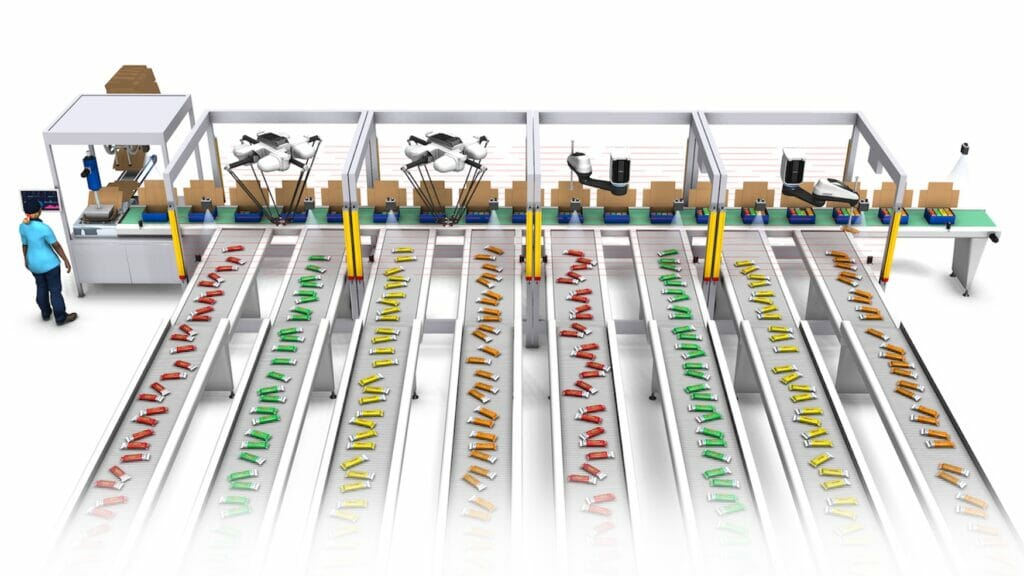
Mixing products in secondary packaging
When mixing different single-variety products in a display carton, the integrity and correctness of the multipacks must be ensured. Manual processes are very flexible, but could compromise quality. Another requirement is the transport of goods and consumables. For example, the inflow of the various goods to be packaged must take place quickly, but the packaging material must also be available at set speeds. To master this interplay, pick-and-place technology for secondary packaging processes is the obvious choice. For example, to handle the inflow of different goods, Omron combines a complete range of different robotic automation technologies into a single, fully integrated packaging system. Integrated algorithms make it possible to coordinate the different production lines and optimise flow rates. No programming skills are required, as the graphical user interface (GUI) is easy to understand and use. With the help of a recipe manager, the line can also be configured for several products and switched between them at the touch of a button. For users, this means more flexibility, fewer machine idle times, a reduction in the workload for employees and less costs and complexity in the (re)packaging line.
Material replenishment on the line
Optimal replenishment on the line is the key to improving overall equipment effectiveness (OEE). But waiting times at machines or intermediate storage are only one side of the coin: the manual activities involved in these tasks are often not very ergonomic and could pose safety problems. It therefore makes sense to improve line side replenishment (LSR) while avoiding operators having to perform these repetitive tasks. In addition, automating the supply of consumables minimises their intermediate storage and waste during repackaging.
Cobots, possibly even in combination with mobile robots, can provide a remedy here, because they support material feeding. The cobot (a collaborative robot that works together with humans and does not have to be separated from them in the production process by protective devices) picks up packaging materials from a position and places them directly on the conveyor belt or in the packaging machine. The consumables no longer have to be unloaded manually. Examples include: Selective Compliance Assembly Robotic Arms (SCARA) which are tasked with loading bottles and other containers or high-speed parallel robotic solutions that align and orient items. This form of automation reduces cost and effort, and also improves production consistency as well as output.
Example from the food industry
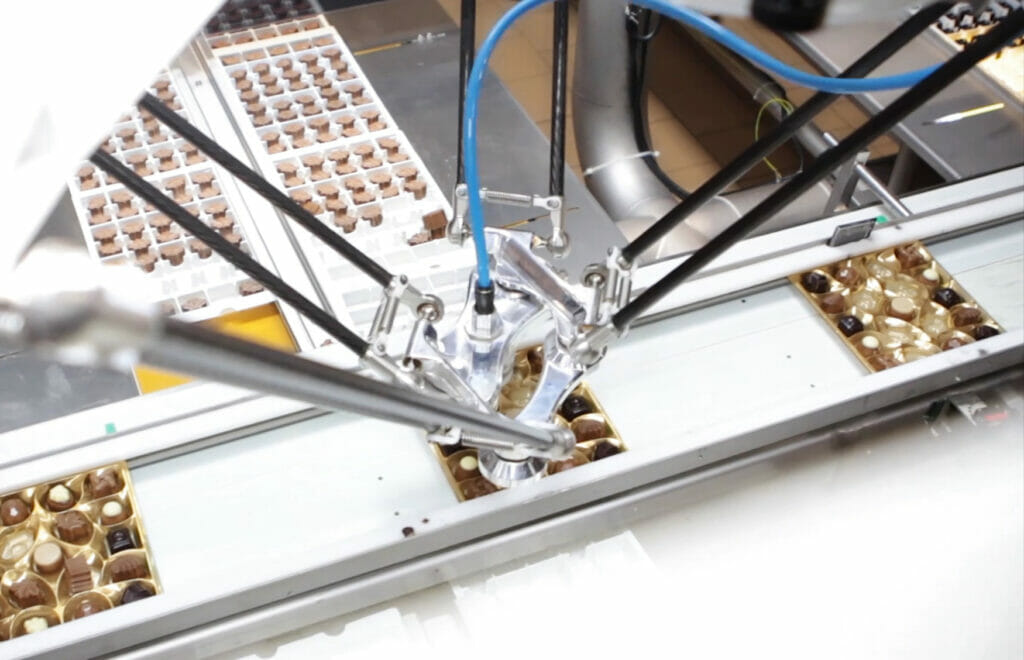
How these challenges are met in practice is shown by the example of a leading global supplier of chocolate, chewing gum, confectionery and biscuits in northern France, which has outsourced its warehousing and co-packing to a logistics service provider. Machine builder, Hugo Beck partnered with Omron to provide a highly flexible packaging solution, consisting of two key components: a pick-and-place system for picking and placing products in the packaging line and unpacking robots that take products directly from the cartons to facilitate supply to the packaging lines. The film packaging machines create the required double or multiple packs in any grouping. Packaging machines and the robotic solutions can be adapted to each new product so that orders can be handled smoothly. Algorithms make it possible to balance the different production lines and optimise throughput. In the recipe manager, the lines are configured for several products and it is switched between them.
Intralogistics and intermediate storage
As a rule, basic processes, such as the production flow in a factory, are already highly automated. However, secondary processes such as the supply of consumables or the disposal of waste are often not at this point, yet. Here, employees still often have to intervene manually and transport materials, for example. Factors such as intermediate storage or occupied production space often involve significant hidden costs for production managers. Innovative robotic solutions can help here to optimise throughput and the availability of the required goods. Material transport can be handled by autonomous mobile robots.
Unpacking and distributing goods
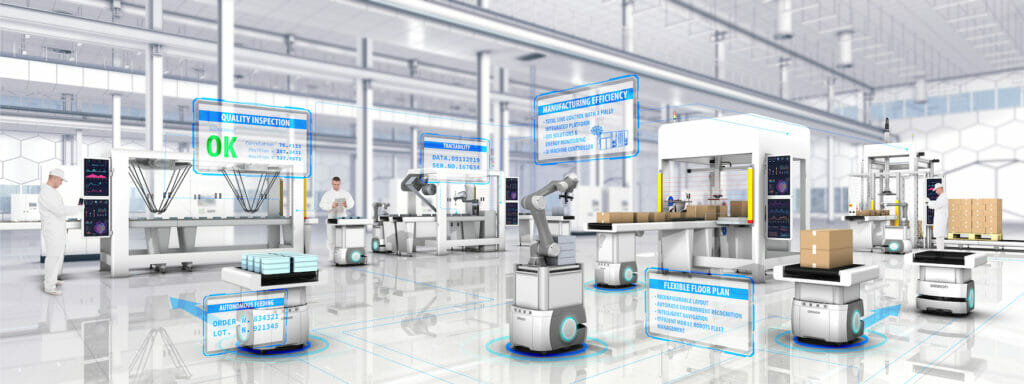
Distribution centres or repacking sites have to face further challenges. These include, for example, the depalletising and unpacking of cartons, the transport of goods that need to be repacked, and the disposal of waste. Fully or semi-automatic handling and robot-assisted transport can reduce a lot of effort here. For example, robots can be used to unload pallets. First, incoming goods are checked. Then, the boxes are loaded either onto a conveyor belt or onto autonomous mobile robots (AMRs), which transport them further. Omron’s AMRs drive autonomously and execute orders based on a picking system. Omron’s fleet manager coordinates the mobile robots and provides traceability, order allocation and data traffic control across the entire fleet. At the same time, cobots can also open outer packaging through automated cutting processes. This involves first determining the size of each incoming carton to automatically find the programmed cutting lines. Packaging lines become more flexible and efficient through the use of such solutions.
End-of-line palletising
For palletising, the market increasingly demands solutions that are easy to install and configure without complicated robot programming. Innovative end-of-line (EOL) palletising solutions support this. Cobots significantly simplify palletising. For example, Omron’s all-in-one solution for automated palletising with collaborative robots includes built-in support software to help users quickly set up their palletising specifications. For example, the drag-and-drop ‚Pallet Node‘ feature included in Omron’s TM-Flow software can be used in a variety of ways, including assembly, loading and unloading, machine tending and, of course, palletising. Users can additionally monitor which row, column and height is associated with the pallet’s movement position. Compared to industrial robots, such a solution requires 50 per cent less floor space.
More packaging news
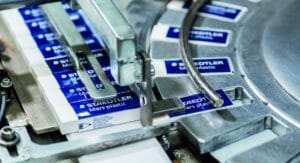
A contract with a handshake is valid
Managing director Tina Gerfer of Wilhelm Rasch Spezielmaschinenfabrik has modernized the company and successfully guided it through difficult times.
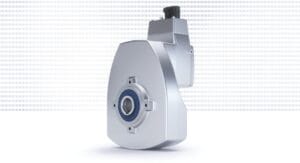
Asynchronous servo solutions for the packaging industry
From primary packaging to final packaging, electric drives play an important role. With a broad portfolio, Nord Drivesystems supports customers.
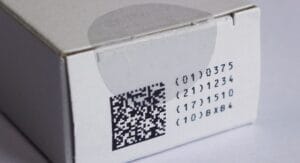
Label Durability
Labels offer many functions which can get lost due to label removal. PTS assesses labels and cardboard for durability and tamper evidence.
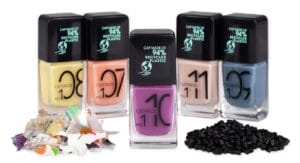
More design for recycling for cosmetics packaging
Packaging for decorative cosmetics is very special. The Forum Rezyklat calls for the recyclability of packaging to be taken into account when designing it.
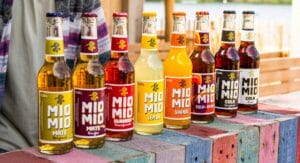
Innovation Barometer 2024
According to a survey conducted by Aktionsforum Glasverpackung 2024 is set to be a highly innovative year for glass packaging.
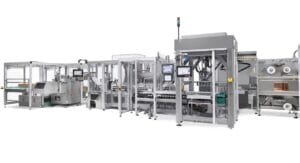
Flexible packaging system for natural cosmetics
Sustainability is part of Weleda’s identity. IWK is also contributing to this with its new flexible packaging line for many natural cosmetic products.