Offering companies the best possible solutions for coding and marking their products also requires extensive knowledge of new and emerging packaging trends. At the Domino Laser Academy in Hamburg, experts from the company are continuously researching and experimenting with new substrates.
„We spend a lot of time analysing new packaging materials: both based on customer requests and for our own research work. Due to the new European regulations for recycled plastics, about 95 percent of the food packaging samples we have to test currently consist of recycled or recyclable plastics. With our F-Series fibre lasers and U-Series UV lasers, we now have many good solutions for coding these substrates,. However, we expect the demand for compostable solutions to increase in the coming years. Therefore, we want to be prepared to advise our customers in this regard as well and offer solutions for these new materials. „
Dr Stefan Stadler, team leader at Domino Laser Academy
In keeping with this focus, the Domino laser team has received samples of Futamura’s market-leading NatureFlex cellular glass films to assess which of Domino’s laser coding solutions would be the best option for users working with these new substrates in their production lines.
Use of renewable and compostable cellulose films
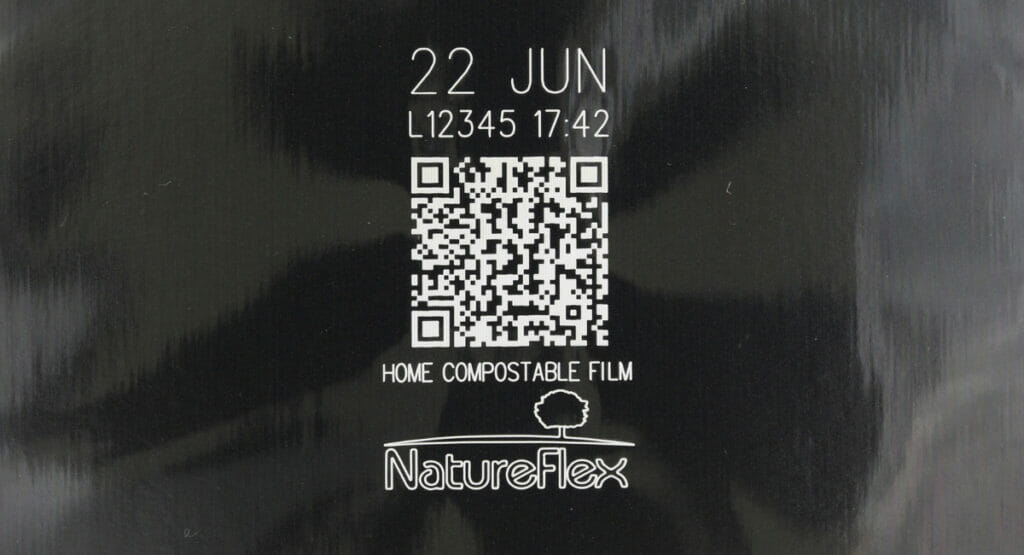
Under the NatureFlex brand, Futamura offers compostable packaging films made from responsibly grown pulp. The company was founded in 1947 in Japan and operates worldwide. The production facilities for cellulose films (cellophane) are located in Japan, the UK and the USA. Typical NatureFlex applications are fresh produce such as fruit and vegetables, where the film can also be used as a wrapper for composting food waste or vegetable peelings. They are also commonly used for non-refrigerated food and beverages. Confectioneries, tea and coffee are just some of the examples where they act as an inner liner for the outer packaging.
The films meet all global standards for industrial composting, including BS EN 13432, and are certified to the OK Compost Home Standard for home composting.
Compostable food films in the test
Domino Printing Sciences (Domino) and Futamura have worked together to assess the suitability of laser coding for NatureFlex compostable film products to provide customers in the food packaging sector with a print-free solution for coding and marking their packaging.
The exact coding requirements for traditional plastic films vary depending on the application, with codes often only required when a film is used as part of the outer packaging of a product. However, for compostable products such as NatureFlex, direct printing on both inner and outer films may be required so that brand owners can inform consumers with text on how best to dispose of the packaging.
„All our NatureFlex films are certified to demonstrate their suitability for industrial and home composting. Many of our customers want to show the final packaging certification as well as additional disposal information for end users on the film.“
Amaia Cowan, Business Development Manager EMEA, Futamura UK
The option of laser coding the NatureFlex flexible film with a simple text is attractive because the coding method does not require any additional materials on the compostable substrate. This should make certification of the final packaging much easier.
Six different versions of the NatureFlex compostable film were analysed by Domino coding experts to determine which laser coding solution would be most promising for further suitability testing.
In search of the optimal solution
„First, we performed a spectroscopic analysis of the substrates to find out which wavelength of light interacts best with the substrate material. This allowed us to determine which laser we should use for the further tests. I had expected an etched, engraved code on the surface of the substrate, as with laser coding of PET bottles, but instead the laser changed the colour of the foil, resulting in a crisp, white code.“
Dr Stefan Stadler
The films were then subjected to further suitability tests to determine the minimum laser power and coding speed required to produce a readable code. The results were encouraging and showed that the lowest power Domino CO2 laser, the D120i, is capable of coding the substrate at only 40 per cent laser power, even at high production speeds.
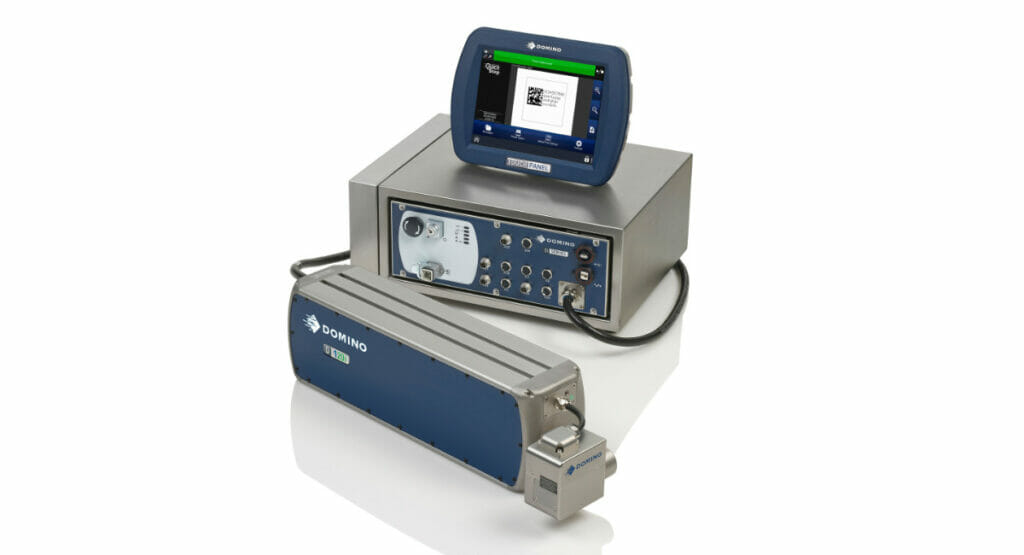
Preserve the integrity of the film
After coding with the D120i, the NatureFlex foils were analysed using microscopic 3-D images to get a closer look at the structure of the code. „This type of 3-D image allows us to measure the depth of the laser engraving to ensure that the substrate is not perforated or compromised. The laser had a foaming effect on the NatureFlex foils, which led to an increase in the foil thickness in the irradiated areas of about 11.5 micrometres,“ Stadler reports. The microscopic images showed that the film had no structural damage.
In addition to the microscopic 3D images, the samples were also analysed using FT-IR spectroscopy to determine whether the laser coding led to chemical additions in the material. To do this, samples of the uncoded and coded NatureFlex film were exposed to different infrared wavelengths and the results of the two samples were compared: The code on the material is the result of a physical change in the material and not a chemical change. Consequently, the laser coding process did not create any additional chemical substances in the material.
Futamura was provided with the coded materials to make a further evaluation and preliminary assessment of the moisture barriers of the coded films. The data indicated that the coding had little effect on this specific property.
Quality and sharpness make the difference
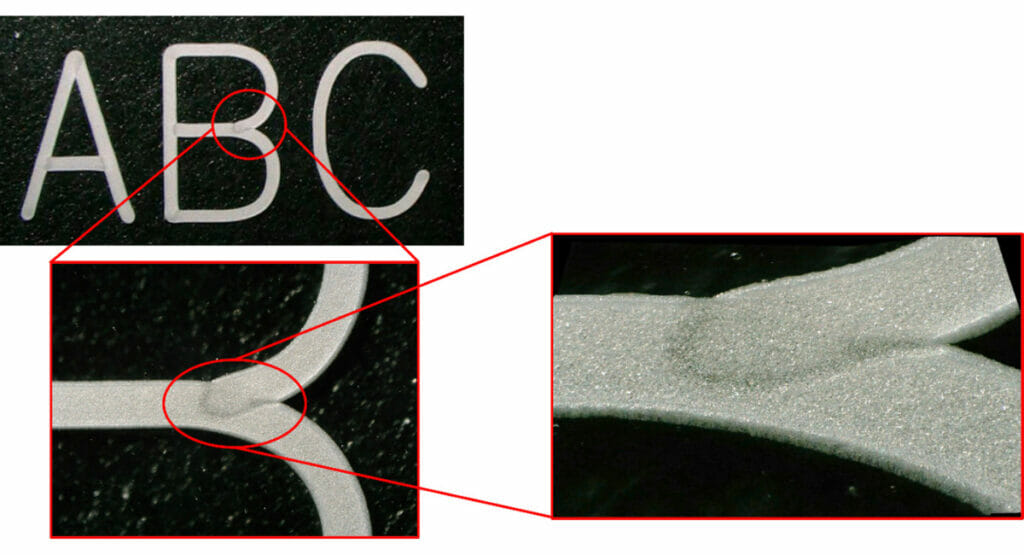
„Product coding and marking are extremely important to our customers, but are outside our area of expertise. That’s why we were very happy to work on this project with a company like Domino that takes a scientific approach to substrate testing and coding,“
Amaia Cowan
The quality and sharpness of the codes make laser coding on NatureFlex flexible film a good choice for food manufacturers who want to create simple codes such as best before dates and batch codes as well as more complex designs and texts such as graphics and scannable 2D codes. „The results of the project are very positive,“ she concludes. „Thanks to this new coding method, information for consumers can be applied directly to the film without printing it. Since no additional materials are added to the compostable films, the certification of the final packaging is easy,“ adds the responsible person.
Where is the journey going?
The project with Futamura and the NatureFlex compostable film is an exciting development in laser coding for sustainable substrates and just one example of how Domino is supporting its customers on their journey towards sustainability.
„We want to stay at the forefront of developments in new and emerging packaging materials, ensuring that we can meet the needs of our customers in all industries. We have a vision for our Laser Academy as a centre of excellence for substrates by being able to invest in the scientific testing and coding of new materials based on our exploratory research, as well as in response to direct customer requests. „
Stefan Stadler
More packaging news
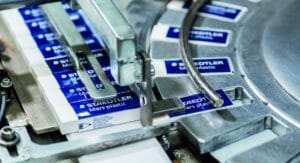
A contract with a handshake is valid
Managing director Tina Gerfer of Wilhelm Rasch Spezielmaschinenfabrik has modernized the company and successfully guided it through difficult times.
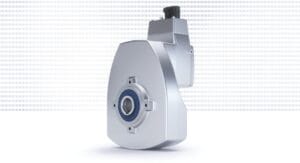
Asynchronous servo solutions for the packaging industry
From primary packaging to final packaging, electric drives play an important role. With a broad portfolio, Nord Drivesystems supports customers.
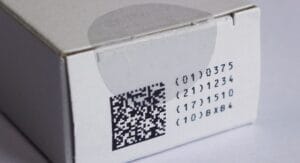
Label Durability
Labels offer many functions which can get lost due to label removal. PTS assesses labels and cardboard for durability and tamper evidence.
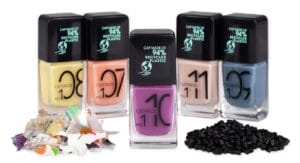
More design for recycling for cosmetics packaging
Packaging for decorative cosmetics is very special. The Forum Rezyklat calls for the recyclability of packaging to be taken into account when designing it.
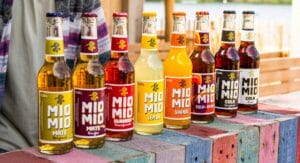
Innovation Barometer 2024
According to a survey conducted by Aktionsforum Glasverpackung 2024 is set to be a highly innovative year for glass packaging.
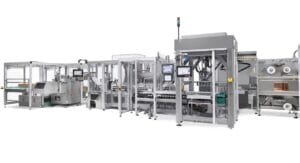
Flexible packaging system for natural cosmetics
Sustainability is part of Weleda’s identity. IWK is also contributing to this with its new flexible packaging line for many natural cosmetic products.