Packaging systems that are heavily soiled with adhesive threads are not uncommon. The associated cleaning effort and increased material consumption are usually reluctantly accepted. Instead of getting angry about the symptoms, however, it is better to get to the root of the problem. Adhesives expert Jowat has taken on this issue and, often with just a few optimisations, realises cleaner and thus more resource-efficient and sustainable packaging processes in cooperation with its customers.
Sealing packaging with hot melt adhesives is a success story: Nothing is as efficient, flexible and reliable in the long term. The hot adhesive is applied to the gluing points in the form of dots or beads with the help of nozzles. Often, the undesirable phenomenon occurs here that the actual adhesive bead pulls a hair-thin thread behind it. A common euphemism for this is the term „angel hair“. In professional circles, this is referred to as thread pull or thread breakage.
Problem recognised
The length of these thin threads determines how severe the resulting contamination is in continuous industrial operation. If they measure only millimetres for a single bead, they quickly grow into considerable quantities when large numbers are produced. This not only wastes adhesive, but also increases the cleaning effort. The result is longer maintenance times and production downtimes.
The triumph of PO hotmelt adhesives further exacerbates the problem: because a key characteristic of this technology, in addition to its excellent stability in the melter, is its broad adhesion spectrum. They adhere well to many surfaces – including machine parts. This makes them difficult to clean and maintain. It is therefore all the more important that the adhesives only end up where they serve their intended purpose. Otherwise, in the worst-case scenario, contaminated and thus unsaleable goods are produced and have to be laboriously reconditioned or disposed of.
Numerous factors influence thread breakage. If several of them complement each other unfavourably, the resulting accumulations of threads can form imposing webs. Depending on their extent, they sometimes remind one of the realm of the giant spider Aragog from „Harry Potter“. However, such problems can be remedied without the power of magic by identifying the possible causes point by point and optimising them – from the process to the application equipment to the adhesive itself.
Optimise processes
You should start by checking the process parameters, first with a close look at the processing temperature. This determines the viscosity of the adhesive and significantly influences thread breakage. The temperature in the application head is particularly relevant. Even five degrees Celsius more in this area often shortens the threads noticeably. In general, the temperature control in the last millimetres up to the application is decisive.
Occasionally, the set values do not exactly match the actual temperatures in the machines. One reason for this can be outdated applicators, for example. The length, position and guidance together with the radii of the heated hoses can also cause temperature fluctuations depending on the throughput speed and continuity – a possible cause for irregularly developing threads.
Temperature deviations can also be triggered by environmental factors. Open doors and windows, unfavourably positioned ventilation fans or high process speeds can cause draughts. This can unintentionally cool both the application head and the escaping adhesive, which increases thread formation. In addition, thin threads can be dispersed inside the machine or in the hall due to draughts.
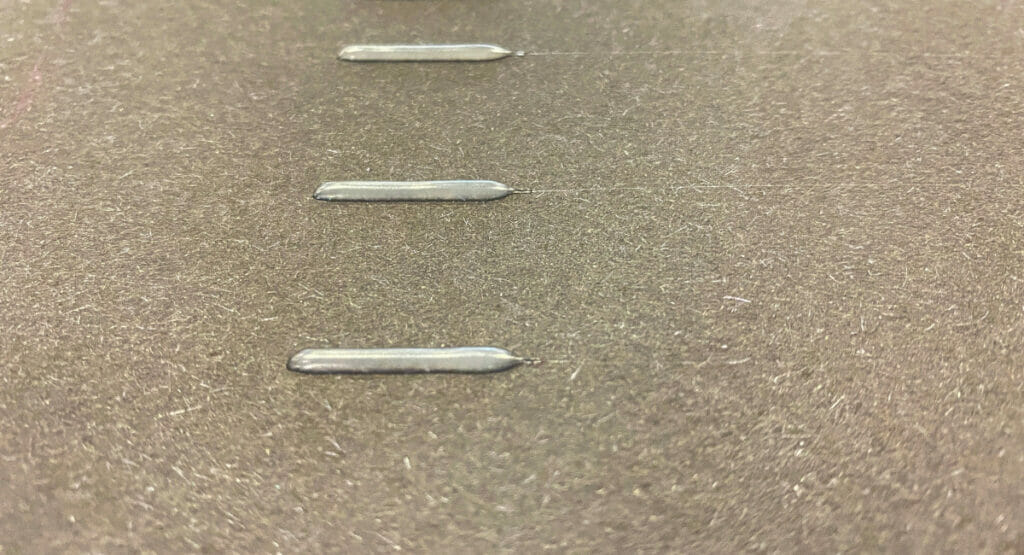
If the distance between the nozzle and the application surface increases, the resulting threads also lengthen. The reason for this is the increased temperature difference in the adhesive application: the adhesive is very hot at the nozzle, but has already cooled down considerably on the substrate due to the distance. This favours long threads. These distances should therefore be reduced to the minimum possible in the process.
Simple to remedy and yet often neglected is the order position. Beads or dots that protrude over the edge of the packaging have no function. They only increase adhesive consumption and soil the machine parts. Short threads within the glued batches are more tolerable than those trailing behind. When applying adhesive, it is therefore important to ensure sufficient distance from the edge and correct positioning.
However, the optimisation potential for a clean yarn break in the process is limited. Existing line designs set these limits. In principle, of course, a secure closure of the package is always more important than clean lines. So, if the result of the measures taken so far is not yet satisfactory, the following adjusting screws should be addressed.
The influence of the equipment
In addition to the process conditions, the application equipment influences the yarn breakage. Application heads work either electro-pneumatically (air-opening-spring-closing or air-opening-air-closing) or purely electrically without compressed air. All types allow precise application patterns. However, in unfavourable process conditions, application heads with high closing force show advantages in terms of yarn breakage.
Application nozzles are available in many different designs. The capillary volume, i.e., the hollow space in the nozzle, is particularly relevant for yarn breakage. The smaller the volume is in the nozzle tip in front of the valve seat, the more conducive it is to a clean yarn break. In practice, needle-seat valves therefore regularly perform better than ball-seat valves. Experience also documents that problems occur more frequently with multi-channel, slotted or angled nozzles than with short nozzles with only one channel. For a clean thread break, the nozzle is the proverbial eye of the needle.
Adhesive change as an opportunity
If the approaches described so far are not effective or feasible, the only option is to switch to another adhesive. In general, adhesives with low viscosity favour sharp thread breakage. However, other adhesives can be formulated with clever combinations of raw materials that hardly tend to pull threads.
Cleaner alternatives are usually quickly identified. But then it must first be tested whether the new adhesive can meet the prevailing requirements such as short cycle times, high restoring forces, demanding surfaces or special temperature resistance. Jowat carries out these tests for its customers free of charge and relies on decades of practical experience as well as a wealth of modern testing equipment. Experienced application experts from the adhesive manufacturer then accompany the implementation in the production environment. In the best case, the result is a solution that enables far-reaching improvements even beyond the thread tension.
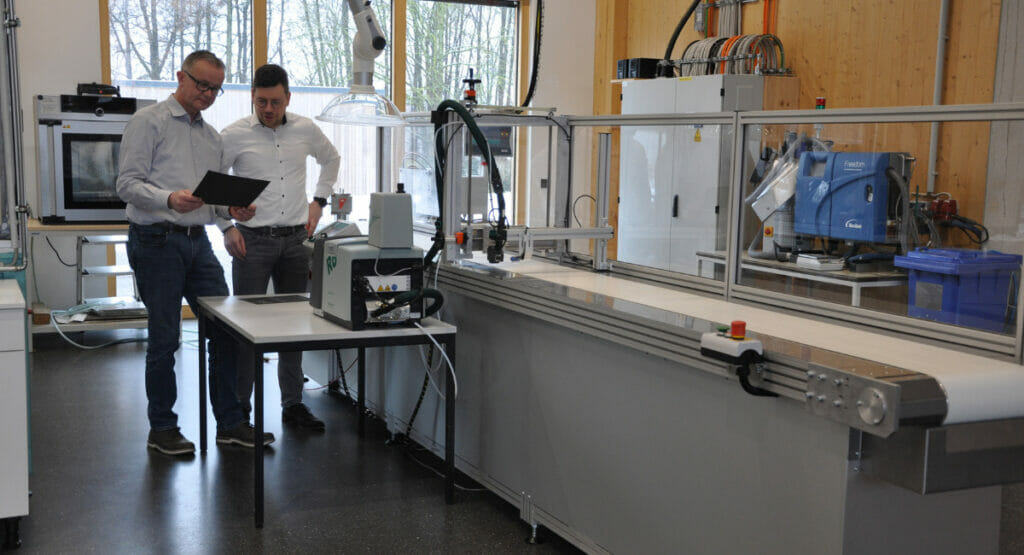
The goal: more sustainable bonding processes
For Jowat, the optimisation of thread breakage is a pivotal point in the development of sustainable adhesives, as processes subsequently consume less material, have less downtime and thus effectively conserve resources. The seriousness of this topic for the Detmold-based adhesive manufacturer is shown not only by several cooperations with science – most recently with the University of Applied Sciences in Munich – and leading mechanical engineering companies, but also by the in-house research efforts made for this purpose. Only last year, Jowat invested in a state-of-the-art facility for the meticulous analysis of thread breakage behaviour. This system simulates a wide range of different process conditions. Whether temperature, pressure, distance, speed or different application heads and nozzles: everything can be flexibly adjusted and set with repeatable precision. This is important because every adhesive reacts differently to the different combinations of these factors.
With regard to the problem of thread tension, one has to state in the end: There are some rules of thumb and general tips, but no panacea. Nevertheless, his extensive knowledge of application technology inspires the adhesive manufacturer to develop new and ever more optimised high-performance adhesives. With the aim of always being one thread length ahead of the market in terms of sustainability.
More packaging news
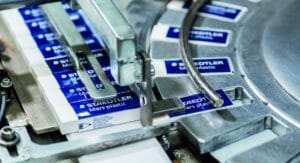
A contract with a handshake is valid
Managing director Tina Gerfer of Wilhelm Rasch Spezielmaschinenfabrik has modernized the company and successfully guided it through difficult times.
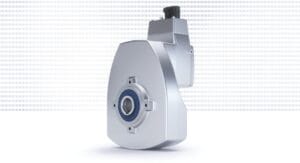
Asynchronous servo solutions for the packaging industry
From primary packaging to final packaging, electric drives play an important role. With a broad portfolio, Nord Drivesystems supports customers.
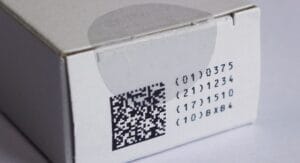
Label Durability
Labels offer many functions which can get lost due to label removal. PTS assesses labels and cardboard for durability and tamper evidence.
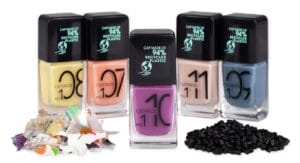
More design for recycling for cosmetics packaging
Packaging for decorative cosmetics is very special. The Forum Rezyklat calls for the recyclability of packaging to be taken into account when designing it.
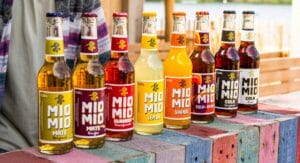
Innovation Barometer 2024
According to a survey conducted by Aktionsforum Glasverpackung 2024 is set to be a highly innovative year for glass packaging.
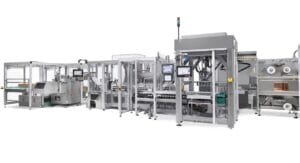
Flexible packaging system for natural cosmetics
Sustainability is part of Weleda’s identity. IWK is also contributing to this with its new flexible packaging line for many natural cosmetic products.