Wer nach einer effizienten Alternative zum Thermoformen sucht und Ressourcen und Kosten einsparen will, wird beim Spritzpräge-Verfahren fündig. Bei der Herstellung dünnwandiger IML-Becher kommt der elektrische Allrounder 720 A von Arburg zum Einsatz. Bei dieser Anwendung lassen sich Materialverbrauch und Teilegewicht reduzieren, und die Becher sind recycelbar.
Der Verfahrensablauf ist komplex und erfordert ein detailliertes Prozesswissen sowie eine hoch positioniergenaue und reproduzierbar arbeitende Spritzgießmaschine. Der elektrisch angetriebene Allrounder 720 A mit 3.200 kN Schließkraft ist mit einer Spritzeinheit der Größe 1300 ausgestattet, die gezielt auf Leistungsstärke optimiert ist. Dank hochpräziser Servomotoren des Arburg Schwesterunternehmens AMKmotion sowie des Antriebs der Arbeitsachsen über Planetenrollengewindetriebe werden hohe Einspritzvolumenströme und Einspritzgeschwindigkeiten von bis zu 400 Millimetern pro Sekunde erreicht.
Minimierte Wandstärke
Die elektrische Hochleistungsmaschine fertigt mit einem 4-fach-Spritzprägewerkzeug von Brink im Spritzpräge-Verfahren dünnwandige, je 400 Milliliter fassende IML-Rundbecher aus PP-Monomaterial. Der eingesetzte Kunststoff ist Biomasse-bilanziert und ISCC-zertifiziert. Zur Prozessüberwachung ist das Werkzeug mit sechs hochauflösenden induktiven Wegmess- und Prägesensoren ausgestattet. Das Label wurde mit der neuesten Next-Cycle-Technologie des belgischen Herstellers MCC Verstraete NV produziert. Es kann beim Recycling vollständig vom PP des Bechers getrennt werden. In die Fertigungszelle ist ein Side-Entry-Robot von Brink integriert, der die Labels einlegt, die fertigen Becher entnimmt und auf ein Förderband stapelt.
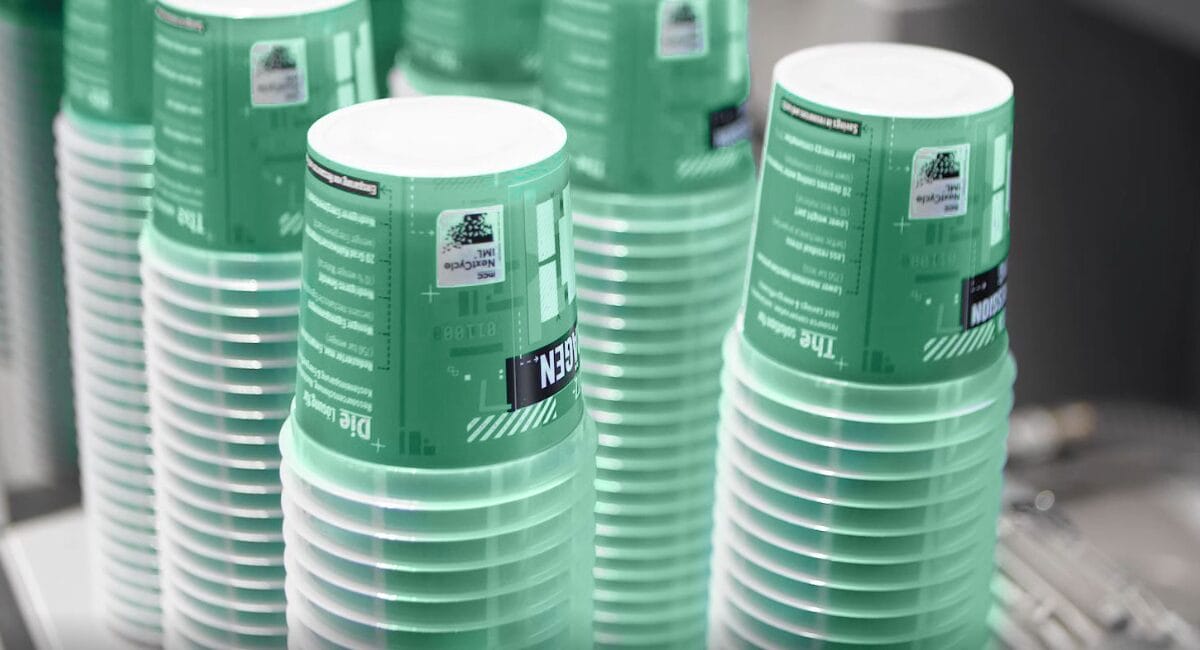
Die PP-Monomaterial-Becher sind recycelbar und mit einer Wandstärke von 0,37 Millimeter besonders leicht. (Bild: Arburg)
In einer Zykluszeit von 3,95 Sekunden entstehen vier je 10,8 Gramm schwere Spritzteile mit nur 0,37 Millimeter seitlicher Wandstärke. Der Becher mit Thermoformgeometrie zeichnet sich durch ein Fließweg-Wandstärken-Verhältnis von 380 : 1 aus, was in dieser Form nicht im herkömmlichen Spritzgießverfahren herstellbar wäre. Weiter liegt das Gewicht eines herkömmlichen spritzgegossenen und nicht spritzgeprägten 400-Milliliter-Becher bei 13 Gramm und das Fließweg-Wandstärken-Verhältnis bei nur 280 : 1.
Spritzprägen mit Vorteilen
Zunächst fällt beim Vergleich zwischen Spritzgießen und Spritzprägen und identischer Zykluszeit von 3,95 Sekunden der verringerte Einspritzdruck von 1.450 bar beim Prägen gegenüber 2.200 bar beim klassischen Verfahren auf. Beim Teilegewicht zeigt sich ebenfalls ein deutlicher Unterschied: Beim Spritzgießen beträgt das Teilegewicht ohne Banderole 13 Gramm, beim Spritzprägen dagegen nur 10,8 Gramm. Daraus resultiert auch einen geringerer Energieverbrauch: Beim Spritzgießen beträgt dieser 0,67 kWh/kg, beim Spritzprägen dagegen nur 0,37 kWh/kg. Der Materialverbrauch liegt bei dem geringeren Teilegewicht im Spritzprägeverfahren mit modifiziertem Design rund 20 Prozent unter dem beim Spritzgießen. Die elektrische Maschine verbraucht beim Prägen 34,76 Kilogramm Material pro Stunde, beim Spritzgießen sind es ab 45,57 Kilogramm. Hier lassen sich also die meisten Kosten einsparen.
Umfangreiche Sensorik im Vierfachwerkzeug
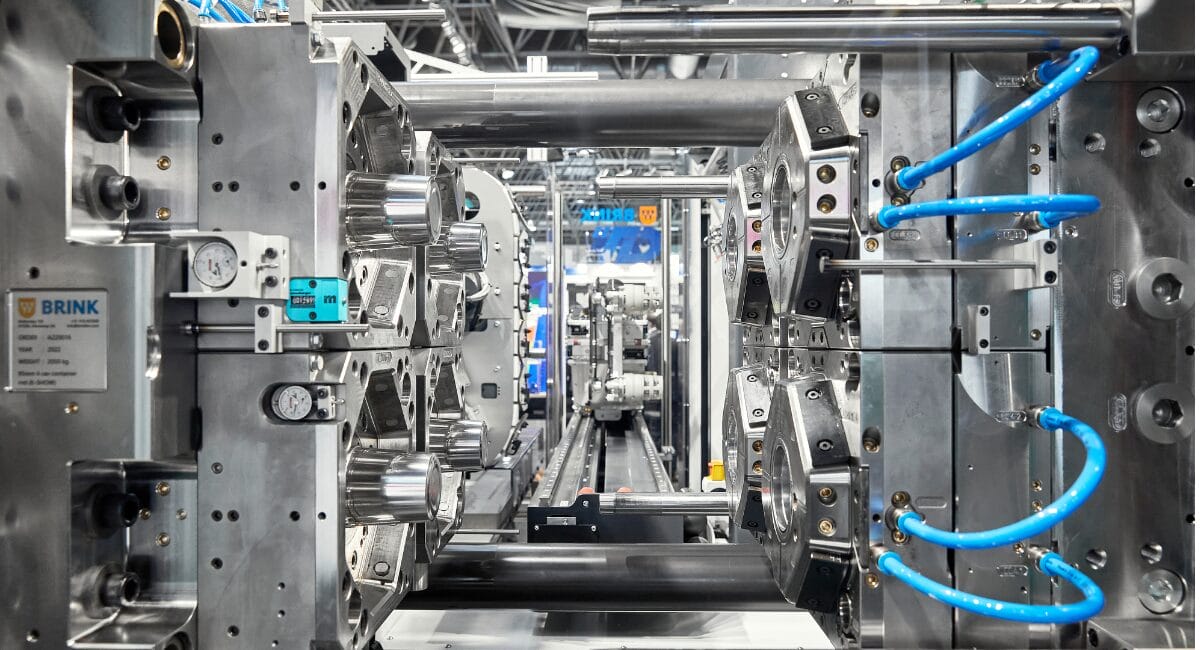
Beim Werkzeugproduzenten Brink entstehen in einer Zykluszeit von 3,95 Sekunden gleich vier Dünnwandbecher. (Bild: Arburg)
Das Werkzeug ist mit der Prägefunktion über ein Federpaket auf der festen Formseite ausgestattet. Dabei wird der Prägevorgang über eine zusätzliche Trennebene im Werkzeug realisiert, um den im herkömmlichen Spritzprägen häufig auftretenden Kernversatz zu vermeiden. Der Prägevorgang erfolgt über die Schließeinheit, der maximale Prägespalt öffnet um 1,9 Millimeter. Erst wenn die Schmelze in der Kavität ist, schließt es komplett. Dieses Verfahren erfordert weniger Einspritzdruck, was den Werkzeugverschleiß reduziert. Es kann mit Werkzeugtemperaturen von 20 statt zwölf bis 14 Grad Celsius gearbeitet werden. Vier Prägeweg-Sensoren an jeder Werkzeugecke überwachen die Prägesequenz mit einer Messgenauigkeit von einem Mikrometer. Die Prozessüberwachung erfolgt über die Gestica-Steuerung.
Ressourcenschonend und recycelbar
Bei der ressourcenschonenden Fertigung von dünnwandigen IML-Bechern für die Verpackungsindustrie wurde besonderer Wert auf ein materialsparendes Bauteildesign und Energieeffizienz gelegt. Dank der vollelektrischen Packaging-Maschine in Kombination mit Spritzprägen verbessert sich die Energiebilanz um 20 Prozent bei Reduktion des Bauteilgewichts. Deshalb wird bei dieser Anwendung im Spritzprägen gearbeitet. Im Vergleich zum klassischen Spritzgießen erfordert dieses Verfahren weniger Einspritzdruck. Die Qualität der Becher verbessert sich durch verringerte innere Spannungen zusätzlich. Anders als beim Thermoformen kommen zudem keine vorproduzierten Folien zum Einsatz, und es wird kein Stanzabfall produziert.