Manchmal muss man die Dinge auf den Kopf stellen, um die beste Lösung zu finden. Genau das erlebte die saarländische Brennerei Eckerts, als es darum ging, ihre Spirituosen schonender zu verpacken. Vom Automatisierungsspezialisten Project A&E wurde eine „Über-Kopf-Lösung“ für den Schutz der Steuersiegel konzipiert und umgesetzt.
Ein kleines angerissenes Papier – sollte ausgerechnet so etwas einem Getränkehersteller richtig große Probleme bereiten? Bei der Brennerei Eckerts aus dem saarländischen Tholey war das der Fall. Denn Jahr für Jahr gab es Zehntausende Euro an Schaden. Der Grund: Flaschen mit Steuerbanderolen wurden durch Tulpengreifer beschädigt und konnten nicht mehr verkauft werden. Sie wurden zur Ausschussware, da ausländische Lebensmittelketten Spirituosen ausschließlich mit einem einwandfreien Steuersiegel verkaufen dürfen – im Gegensatz zum Inland sind in einigen Ländern nämlich solche Steuersiegel Pflicht. Auch das manuelle Prüfen jedes Siegels auf jeder Flasche war höchst ineffizient.
„Eckerts gibt es seit 1890 und steht für Qualität. Die Folgekosten aufgrund der Beschädigungen waren enorm. Eine Speziallösung ohne Tulpengreifer, aber mit dennoch hoher Nennleistung musste her“, betont Tobias Erb, Betriebsleiter, Prokurist und Mitglied der Geschäftsleitung. Das Familienunternehmen hat sich bereits in der fünften Generation der Brennerei verschrieben:
Die Produktpalette reicht von klassischen Kräuterschnäpsen und Likören über moderne Szenedrinks bis hin zu Edelbränden, die in Barrique-, Sherry- oder Eichenfässern über Jahre gelagert werden.
Über-Kopf-Verpackungslösung ohne Berührung des Steuersiegels
Tobias Erb hatte sofort die Project A&E aus dem nordrhein-westfälischen Kranenburg im Kopf, als es um die Neukonzeption ging: „Als gewachsener Betrieb haben wir keinen Platz für voluminöse Standardlösungen. Da drohen außerdem enorme Zusatzkosten, da im Nachgang Anpassungen nötig sind. Bei Speziallösungen vom Team Jansen hingegen haben wir Planungssicherheit: zeitlich, qualitativ und budgetär.“
Speziallösungen, diese sind in der Tat das Terrain von Johannes Jansen, Geschäftsführer der Project A&E. Mit seinem Partner Stefan Opgenorth und inzwischen über 90 Mitarbeiterinnen und Mitarbeitern entwickelt er Sondermaschinen für Kunden im In- und Ausland. „Für Eckerts haben wir eine Über-Kopf-Verpackungslösung konstruiert. Erst werden die Flaschen zu sechst gruppiert. Anschließend wird der Karton von oben über die Flaschen gestülpt“, berichtet Jansen stolz. „Unsere Maschine Propac 2400 erreicht bei Eckerts eine Leistung von über 14.000 Flaschen pro Stunde. Um diese Leistung zu liefern, entwickelten wir für die Maschine auch einen Kartonaufrichter mit einer Taktleistung von 40 Kartons pro Minute.“
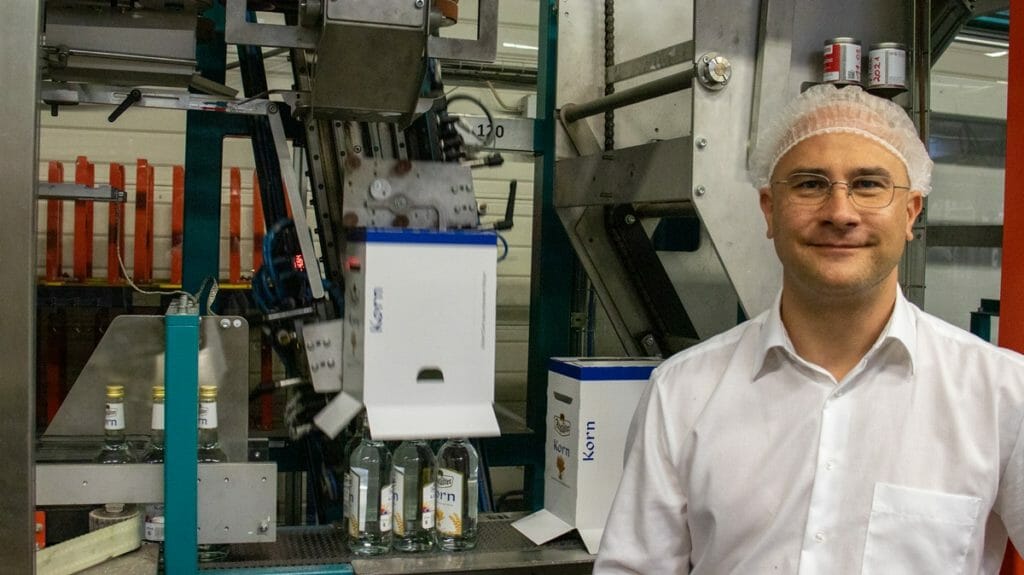
Tobias Erb von Eckerts präsentiert stolz den Propac 2400, den die Project A&E für ihn konzipiert und gebaut hat. (Bild: Project A&E, Kranenburg)
Dieser spezielle Aufrichter sei, so ergänzt Tobias Erb, nötig gewesen, da sonst zwei Standardmaschinen hätten gekauft werden müssen. Andere Optionen wie das „Wrap Around-System“ waren nicht gefragt. „Denn wir wollten bei schon fertig geklebten Kartonzuschnitten bleiben, die nur oben und unten geschlossen werden müssen.“
Schließen der Kartons von unten im Durchlauf
Die Kranenburger wurden mit vielen technischen Herausforderungen konfrontiert. Wie gruppiere ich die Flaschen in Sechsergebinde? Wie transportiert man einen Karton, der nur oben verschlossen, aber unten offen ist? Wie gelingt es, den Karton samt Flaschen im laufenden Prozess von unten zu verschließen?
Der 32-jährige Ingo Rathmann ist Konstruktionsleiter und ein Eigengewächs der Project A&E GmbH. Schon vor zehn Jahren hatte er als Praktikant für den Automatisierungsspezialisten gearbeitet. Das Unternehmen aus Nordrhein-Westfalen ist Spezialist für anspruchsvolle Verpackungslösungen, die sich oft mit ganz individuellen Kundengegebenheiten auseinandersetzen müssen – gefragt ist dieses Know-how unter anderem in der Getränke-, Lebensmittel- und Hygieneindustrie.
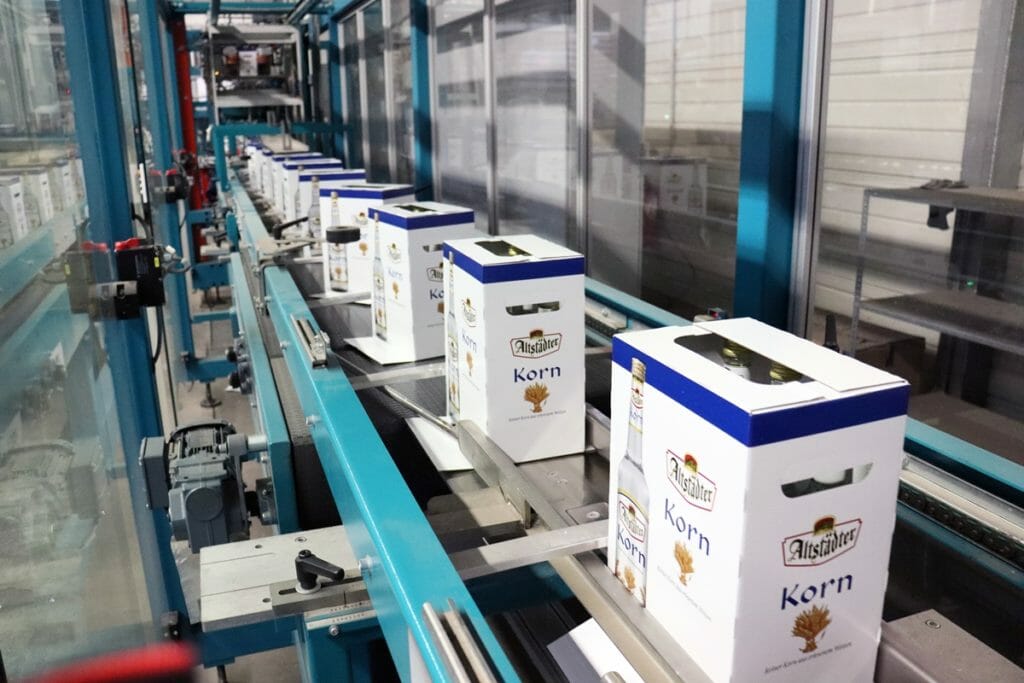
Beim Verschließen des Kartons von unten fährt dieser nun nur noch über eine Art ‚Blechstreifen‘, der schmaler ist als der Karton, sodass die Lasche darunter gefaltet werden kann. (Bild: Project A&E, Kranenburg)
Als Konstruktionsleiter für das Eckerts-Projekt kann Rathmann die Prozesse erklären: „Die größte Herausforderung war, im Durchlauf und kontinuierlich – also ohne zu stoppen – den Karton unter den Flaschen zu verschließen. Er fährt nun nur noch über eine Art ‚Blechstreifen‘, die schmaler sind als der Karton. Dadurch kann die Lasche unter die Produkte gefaltet werden. Am Ende der Blechstreifen ist eine kleine Lücke, dort wird die Lasche unter den Flaschen platziert.“
Spezieller Prozess der Bodenvorfaltung
Notwendig sei für diese Über-Kopf-Verpackungslösung aber schon zuvor ein spezieller Prozess der Bodenvorfaltung: „Die unteren Laschen, die sonst immer gerade nach unten stehen, mussten erst einmal 90 Grad zur Seite ‚vorgefaltet‘ werden, damit der Karton später weit genug über die Flaschen gestülpt werden kann.“ Dieser Prozess passiert im oberen Teil der Maschine.
Rathmann erläutert, was sich im unteren Teil der Maschine tut: „Unten müssen wir die Flaschen, die aus dem Flaschenstrom kommen, zu Sechsergebinden formieren und unter den Karton bekommen. Dafür nutzen wir eine Kombination aus zwei Verfahren: erstens die Eintakt-Sterne, die dafür sorgen, dass immer sechs Produkte in einem bestimmten Abstand von der nächsten Sechsergruppe separiert werden. Danach schieben wir mit sogenannten Mitnehmern die Produkte zusammen, sodass wir dann ein frei stehendes Gebinde aus sechs Flaschen haben. Während die Produkte auf dem Förderband weitertransportiert werden, werden die Kartons über die Flaschen gestülpt.“ Jetzt beginnt der spezielle Prozess, bei dem die oben bereits verschlossenen Kartons nun auch von unten verschlossen werden.
Ingo Rathmann merkt man die Begeisterung für seinen Job an: „Unsere Kunden ermöglichen uns so viele anspruchsvolle und unterschiedliche Projekte“, sagt er. Eine Abfüllanlage für bis zu 2.000 Flaschen pro Stunde, die formatteilfrei einen Flaschenrinser und einen berührungslosen Füller vereint, das sei auch „super spannend“ gewesen. Wo das umgesetzt wurde? Bei Eckerts in Tholey, auf Wunsch von Tobias Erb.