Minebea Intec stellt eine neue Generation von Wägezellen vor, die durch elektromagnetische Kraftkompensation eine hohe Messgenauigkeit und Geschwindigkeit bieten. Diese Technologie findet besonders in dynamischen Kontrollwaagen Anwendung.
Minebea Intec hat eine neue Generation von Wägezellen auf den Markt gebracht. Diese basieren auf der Technologie der elektromagnetischen Kraftkompensation (EMK), die für ihre hohe Genauigkeit und schnelle Gewichtserfassung bekannt ist. Am Kompetenzstandort Aachen wurde diese Technologie in Zusammenarbeit mit der Konzernmutter MinebeaMitsumi entwickelt und in die ersten Produkte der WZEDP-Serie integriert.
Industrielle EMK Wägezellen sind für Anwendungen konzipiert, die hohe Anforderungen an Messgenauigkeit und Durchsatz stellen, wie etwa dynamische Kontrollwaagen. Hierbei erfasst eine Wägezelle das Gewicht von Produkten, die über ein Förderband laufen, und wertet diese Daten aus. Die neue WZEDP-Produktserie von Minebea Intec wurde in Aachen perfektioniert. Nach der Akquisition der Sparte Industrial Technologies begann dort die Entwicklung der zentralen Elektronik und des sogenannten Monolithen, die beide Kernelemente der neuen EMK Wägezellen sind.
Monolithischer Sensorgrundkörper mit 3D Frästechnik
Der Monolith, ein Grundkörper aus hochfestem Luftfahrtaluminium, wird aus einem Materialblock gefräst und anschließend vermessen. Er bildet das Herzstück der Wägezelle und ist entscheidend für die Messleistung. Der Monolith enthält Hebel, die dünner als ein Haar sind, was zur Präzision der Wägezelle beiträgt. Ein Team in Aachen entwickelte ein System mit mehrfach übersetzten Hebeln, das von einem lokalen Zulieferer gefertigt wird. Diese Konstruktion eliminiert Verschraubungen entlang der Kraftübertragungsstrecke, wodurch Messfehler wie Driften vermieden werden. Die drei Übersetzungsstufen erlauben hohe Vorlasten, sodass das Produktgewicht mit einer minimalen elektromagnetischen Kraft kompensiert werden kann. Dies reduziert die Erwärmung des Messsystems und ermöglicht bis zu 10.000 eichfähige Schritte über alle Messbereiche.
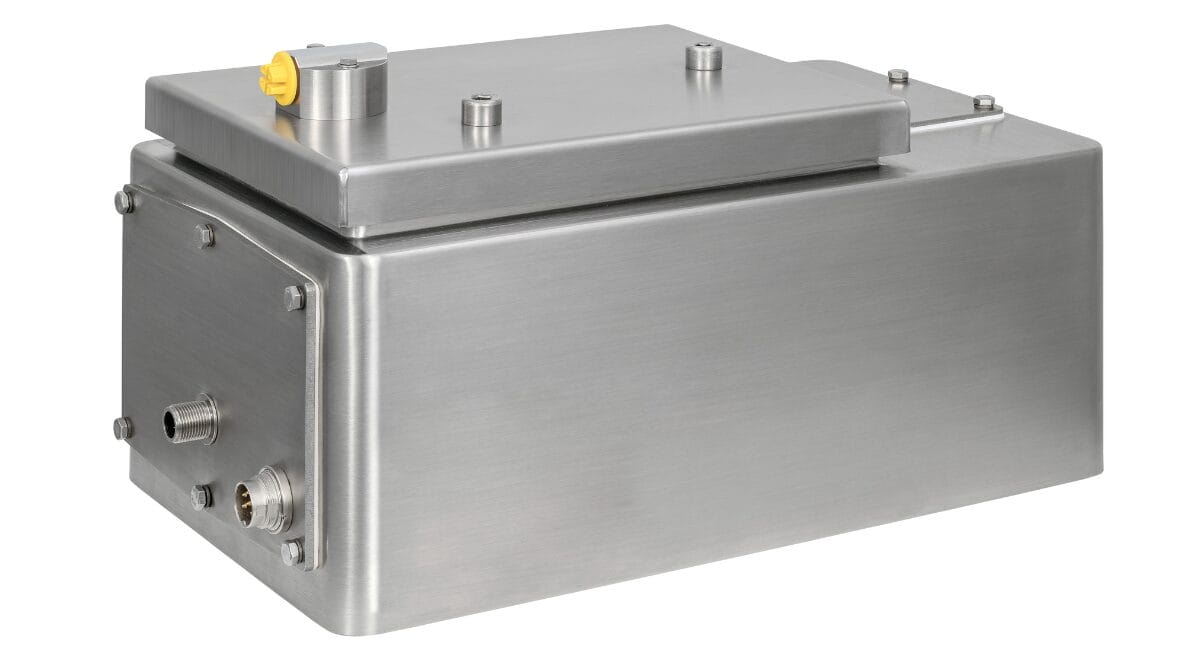
(Bild: Minebea Intec)
Der erfolgreiche Entwicklungsprozess führte zur Anschaffung einer 5-Achs-Fräsmaschine und zum Aufbau einer mechanischen Produktion mit Vormontage dieses EMK Sensors am modernen Produktionsstandort in Košice. Dieser Standort wird zentral von Minebea Intec Aachen geleitet. Nach der Montage der Anbauteile wie Magnetsystem, Spule und Positionsdetektor werden die Sensoren umfassenden Tests unterzogen.
Im Werk Aachen werden die vormontierten Sensoren mit Elektronik, Gehäuse und weiteren Anbauteilen komplettiert. Die vollständigen Wägezellen werden in einer Klimakammer über den gesamten Temperaturbereich getestet. Neben der Nullpunktmessung werden in der Klimakammer Gewichte bei unterschiedlichen Temperaturen automatisiert aufgelegt. Die gewonnenen Daten werden in Korrekturparameter umgerechnet und in der Elektronik der Wägezelle gespeichert. Abschließend wird die temperaturkompensierte Wägezelle nochmals gegen metrologische Daten geprüft.
Die speziell entwickelte Elektronik ermöglicht eine schnelle, dynamische Verwiegung. Digitale Messalgorithmen liefern fertige Gewichtswerte mit einer hohen Datenrate von bis zu 2.000 Messwerten pro Sekunde, was eine quasi Echtzeit-Überwachung erlaubt. Diese Wägezellen können mit einem Transportband kombiniert werden, das besondere Anforderungen an Genauigkeit erfüllt, um eine zuverlässige dynamische Messung zu gewährleisten. Die Wägebänder werden ebenfalls in Aachen entwickelt und gebaut. Die EMK Wägezellen von Minebea Intec sind ab sofort auch für OEM-Anwendungen zur direkten Maschinenintegration erhältlich. Kunden profitieren somit von der gesamten Expertise des Entwicklungszentrums in Aachen.
Quelle: Minebea Intec