Täglich werden bei der Nürburg Quelle Hermann Kreuter GmbH in der rheinland-pfälzischen Vulkaneifel 450.000 Glasflaschen abgefüllt. Beim Rücklauf setzt das Unternehmen zur Flaschenerkennung inzwischen auf künstliche Intelligenz (KI) von Indspect: Für eine Erkennungsgenauigkeit von deutlich über 99 Prozent hatten die Experten im Vorfeld eine Vielzahl von Bildern erstellt und einzeln manuell ausgewertet. Danach übernimmt die KI …
Zum Einsatz bei der Nürburg Quelle kommen weiße 0,7-Liter-Perlenflaschen und grüne 0,75-Liter-GdB-Flaschen. In den Kisten im Rücklauf befinden sich aber häufig neue 0,75-Liter-Flaschen (N2) sowie Individualflaschen von Mitbewerbern. Von oben und mit normalen Kameras sind sie nicht zu unterscheiden. Um nur die passenden Flaschen zur Abfüllung zu bringen, war viel Aufwand und eine neue KI-Software, die auf einer Hochleistungsgrafikkarte arbeitet, für die Möglichkeit der Erkennung mit Indspect-Prüftechnologie notwendig.
Meilensteine der Entwicklung
Hermann Kreuter senior gründete im Jahr 1932 die Firma Nürburg Quelle als KG. Die Anfangsjahre für das Unternehmen waren schwierig, weil der Firmeninhaber die politische Einstellung der nationalsozialistischen Machthaber nicht teilen wollte. Doch ab 1950 ging es rasant bergauf. Nürburg Quelle wuchs kontinuierlich von zehn Mitarbeitern und einer Million Flaschenfüllungen im Jahr 1950 auf aktuell 115 Mitarbeiter und einen Jahresausstoß von etwa einer Million Hektolitern.
Einen Meilenstein setzt der Mineralbrunnen am 28. November 1968, als er als erster Brunnenbetrieb in Deutschland den praktischen und hygienischen Schraubverschluss einsetzte und so seine Innovationskraft und Kundenorientierung unter Beweis stellte. Sieben Jahre später schreibt der Betrieb am 11. Juli 1975 erneut Geschichte: Die Mineralwasserquelle „Vulkania“ wird als Heilwasser staatlich anerkannt.
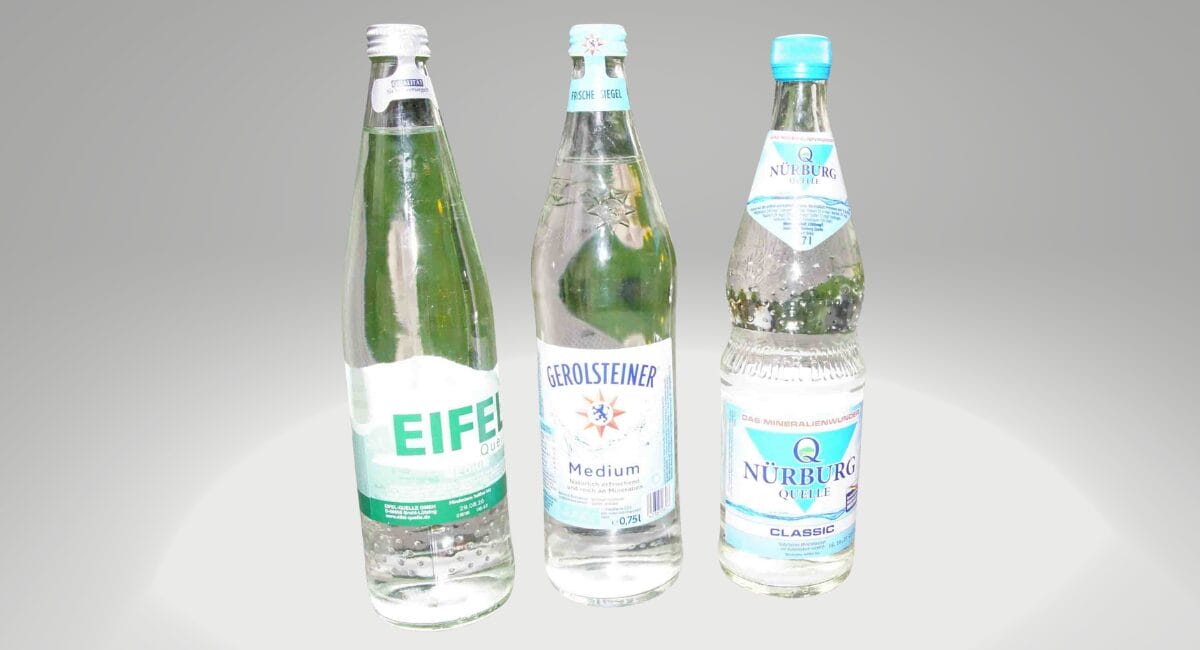
Diese Flaschen muss die Indspect-KI beispielsweise unterscheiden (rechts die der Nürburg Quelle, daneben die anderer Mitwettbewerber).(Bild: broesele | Montage: packaging journal)
Abgefüllt in Perlenflaschen
Jedes Jahr werden weit über 100 Millionen Flaschen abgefüllt, 65 Prozent davon aus Glas. Drei PET-Linien (Einweg- sowie Zwei-Wege-PET) und eine Glaslinie mit einer Leistung von 30.000 Flaschen in der Stunde sind im Werk in Dreis-Brück in Betrieb. Für die Glasflaschen werden braune und grüne 12er-GdB-Kisten eingesetzt.
„Zur Erkennung der ‚guten‘ Flaschen setzen wir seit Jahren auf Kamerasysteme von Indspect. Doch seit einiger Zeit registrieren wir vermehrt die neue GdB-Flasche N2 sowie Individualflaschen anderer Brunnen in unseren Kisten. Diese fremden Flaschen konnten die bisherigen Kamerasysteme nicht mehr differenzieren, sodass wir am Ende viele Fremdflaschen manuell aussortieren mussten.“
Hermann Kreuter, führt Nürburg Quelle als Geschäftsführer in dritter Generation und fragte beim langjährigen Partner Indspect eine Lösung an.
Innovative Erkennungstechnologie
Seit über 20 Jahren konzipiert Indspect aus Neuwied verschiedenste Verfahren zur Überprüfung von Flaschen und Kisten in der Getränkebranche: Kameras, Hochfrequenztechnologie, Laser-Lichtschnitt-Systeme, Ultraschallsensoren und Lichtschranken erkennen Farben, Form und Größe von Gebinden, die Anwesenheit, den korrekten Sitz und intakte Sicherungsringe bei Verschlüssen, Etiketten und deren Datierung sowie die Füllstände. Hinzu kommen die Erkennung von Fremdstoffen und Restflüssigkeiten in den Flaschen, die Vollzähligkeit in den Vollgutkisten, gebrochene Griffleisten, falsche Kistenfarben und Logos, Fremdkörper oder falsche Flaschen beim Leergut.
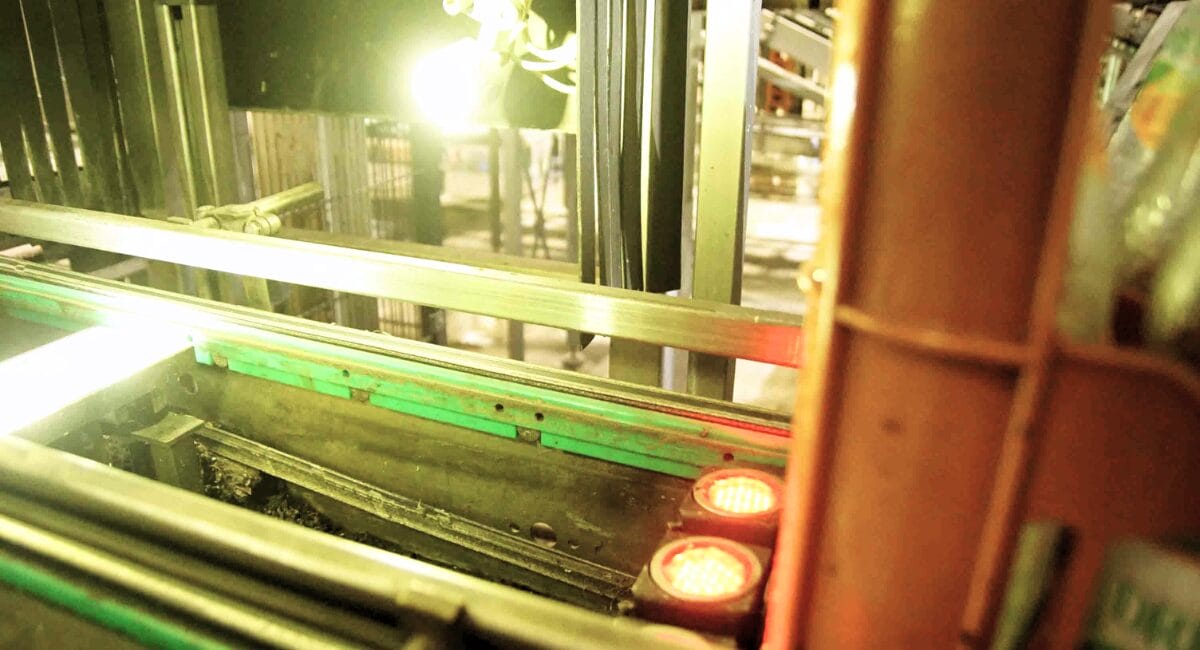
Von unten rot, von der Seite und oben weiß sind die LED-Lampen, die für die Kameras die perfekte Beleuchtung erzeugen. (Bild: broesele)
Eingesetzt werden dazu CCD-Hochleistungskameras in Messbrücken, die Kisten mit den Flaschen fahren darunter im freien Durchlauf hinweg. Genauso wichtig ist die zugehörige Software, die die zum Teil rasend schnellen Signale eindeutig so umsetzt, dass die Flaschen und Kisten durch Ausleitsysteme in jeweils korrekte Bahnen gelangen und die kompletten Ergebnisse eindeutig und nachvollziehbar auf einem großen Bildschirm dargestellt werden, Fehler und Gutflaschen sowie -kisten in übersichtlichen Statistiken gespeichert werden. Hierfür kommen die Steuerungsgeräte Pro, Basic oder Eco (je nach Leistungsanforderung) zum Einsatz.
Problematische Differenzierung – aufwendige Vorbereitung
Bei der Nürburg Quelle setzt Indspect eine spezielle KI-Software ein. „Die gewünschte Perlenglasflasche, die neue N2-Flasche der GdB und die Individualflaschen der Mitbewerber haben annähernd die gleiche Höhe. Zudem sind von oben mit dem Schulterblick die Unterschiede für unsere Kameras fast nicht zu erkennen“, beschreibt Indspect-Geschäftsführer Frank Nicklisch das Problem. KI bedeute aber keineswegs, dass dieses System, wie viele meinen, völlig selbstständig lernt, „sondern wir müssen der Software so viele Variationen wie nur irgendwie möglich an die Hand geben, dass sie daraus die richtigen Schlüsse ziehen und die Flaschen letztlich sicher unterscheiden kann“, hebt Nicklisch hervor. Zunächst müsse also der Mensch jedes einzelne Bild bewerten und das Ergebnis der KI vorgeben.
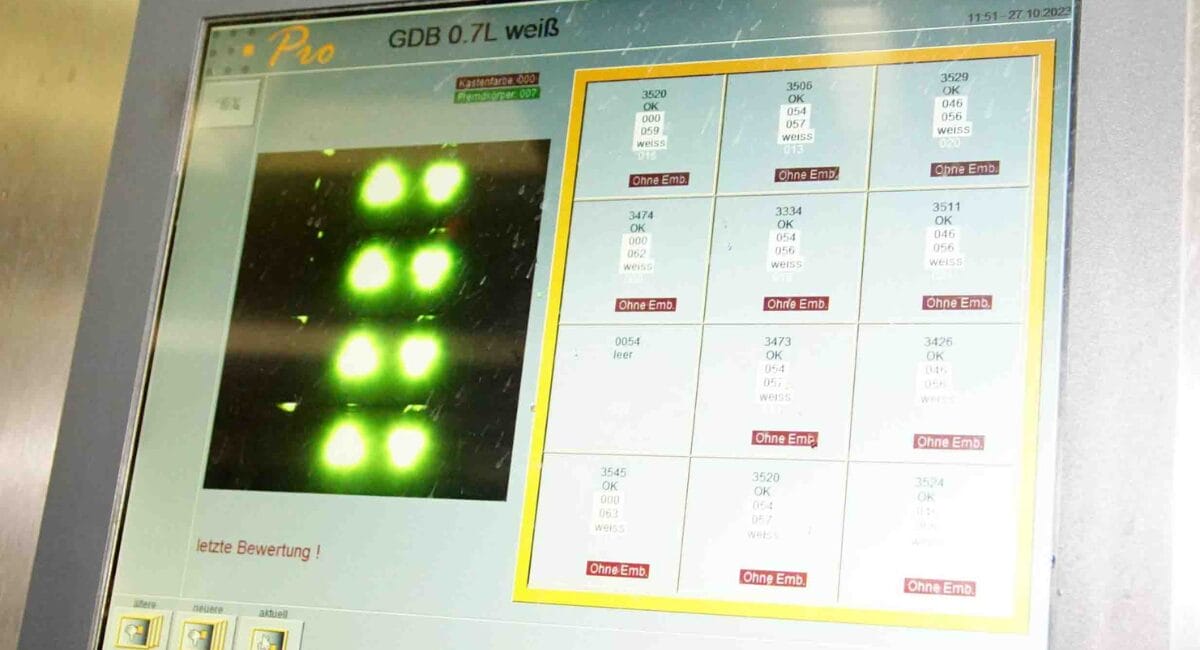
Das Bedienpersonal kann jederzeit den Stand der Erkennung sehen und kontrollieren.
(Bild: broesele)
Schon am Stammsitz in Neuwied begann Indspect daher, unzählige Fotos der verschiedenen Flaschen von oben zu erstellen. Jedes einzelne Bild wurde dann manuell ausgewertet und der oft minimale Unterschied markiert. Dann bauten die Indspect-Ingenieure ihre vier CCD-Kameras und die Elektronik an der Linie der Nürburg Quelle ein und machten weitere Fotos. „Insgesamt waren es zwischen 25.000 und 30.000 Bilder, die wir geschossen und einzeln ausgewertet haben“, berichtet Nicklisch. Erst dann waren sie zufrieden und erreichten eine Erkennungsgenauigkeit von deutlich über 99 Prozent bei einer Leistung von 30.000 Flaschen oder 2.500 Kisten in der Stunde.
„Aus diesen vielen Informationen und Unterscheidungsmerkmalen zieht die KI beim Trainieren des Modells nach und nach ihre eigenen Schlüsse und wird so immer besser.“
Überzeugendes Ergebnis
Kisten, die keine Fehlflaschen aufweisen, fahren direkt zum Auspacker und zur Waschmaschine. Kisten mit Nichtproduktionsflaschen gelangen auf ein separates Band zur Palettierung, um später erneut der Produktion zugeführt zu werden. Kisten mit mehr als einer fremden Flasche erreichen über ein drittes Band die Sortierung:
„Wir sind mit dem neuen System von Indspect sehr zufrieden und haben so viel weniger Fremdflaschen im Prozess. Perfekt wäre die Lösung natürlich dann, wenn 100 Prozent der falschen Flaschen aussortiert werden könnten.“
Hermann Kreuter