Sensors installed in the bottling plant are often inconspicuous, yet indispensable for efficient processes. At the traditional Dinkelacker brewery, sensor technology from Leuze is used at almost every station. The demands on the technical components are very high, because they must also withstand strong vibrations and frequent cleaning processes.
The Dinkelacker family brewery in Tübinger Straße in the heart of Stuttgart was founded back in 1888. The high quality standards for their products are also reflected in the technical components used in production. That’s why they rely on Leuze’s application know-how and sensor technology that meets the highest requirements for reliability, robustness and hygiene.
Sensor technology for filling
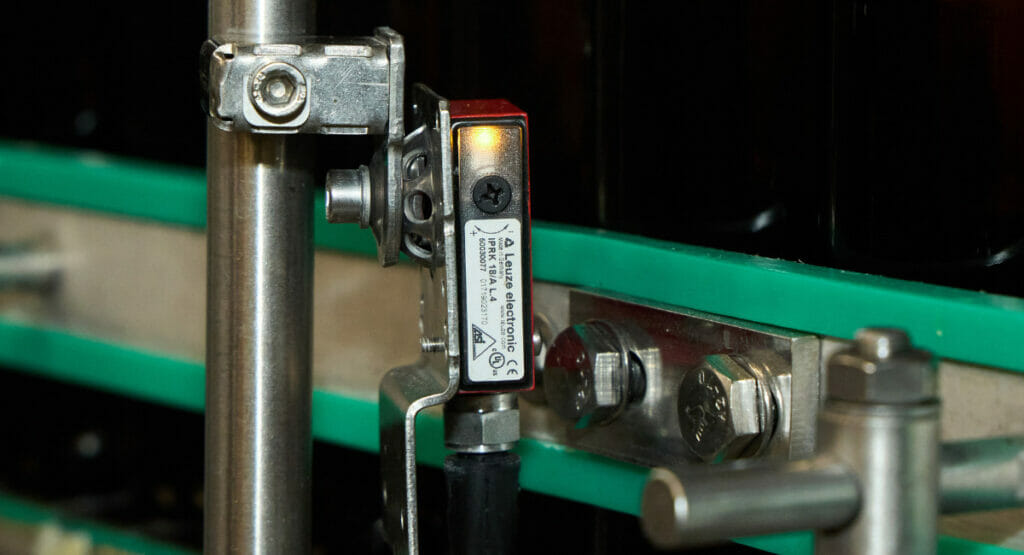
„To ensure trouble-free operation, we depend on particularly robust and reliable sensors. Only selected sensor solutions can cope with this,“ explains Florian Fahr, Head of Technology at Dinkelacker. That’s why the brewery relies on Sensor People technology from Leuze.
„Reflection light barriers of our PRK series (reflection light barrier with polarisation filter) were primarily installed here. This series is particularly suitable for applications in the beverage industry. The metal housing of the optical sensors are not sensitive. Therefore, the devices can work optimally even in harsh environments.“
Andreas Eberle, Local Industry Manager Packaging at Leuze
It is important that the optical switching devices can detect even highly transparent objects such as bottles as well as glossy plastic crates with different imprints thanks to the reflection principle. At Dinkelacker, the Leuze technology has proven its reliability in practice, as Andreas Eberle explains: „Many of the sensors have already been doing their job precisely in the family brewery for decades. Some of them were installed at Dinkelacker in the late 1990s and early 2000s.“ By focusing on one sensor series, the brewery has to stock fewer different spare parts and can react promptly in the event of a defect that rarely occurs. However, should a problem occur, they appreciate the close proximity to Sensor People’s headquarters with immediate support.
Material flow without obstacles
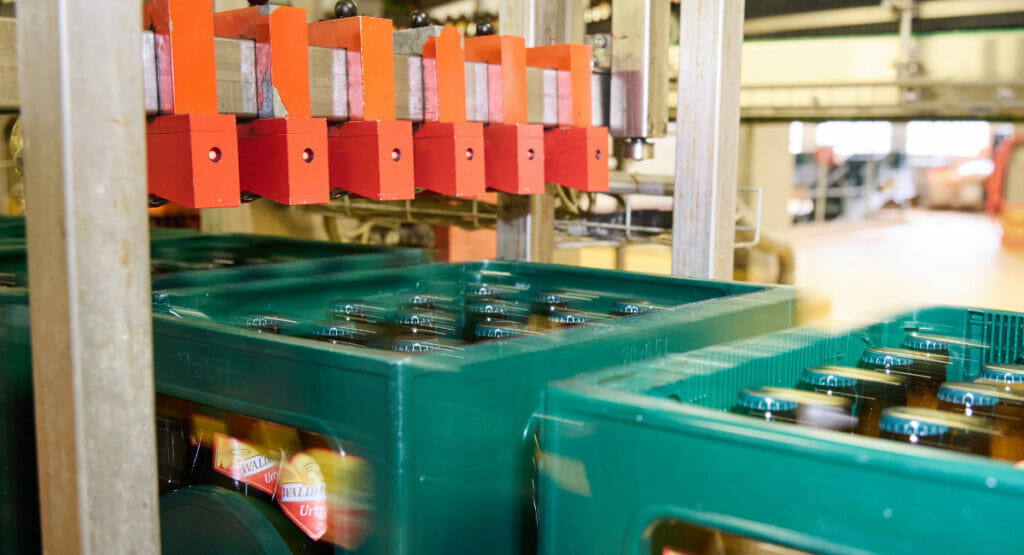
The Leuze sensors are used at various points in the bottling process and each has special tasks. The process begins before filling with the cleaning of bottles, beer crates and kegs. Cleanliness and hygiene play a major role. The PRK optical sensors are installed at the individual conveyor sections and detect pallets, kegs, beer crates or even bottles. This automatically regulates the speed of the belts and prevents jams and collisions.
In the barrel filling area, Dinkelacker has installed around 100 sensors on the conveyors. Up to 240 barrels per hour are cleaned and filled there. Two new robots support the employees here: they lift the empty or full barrels and place them on the conveyor belt or pallets. Dinkelacker installed the new robots at the time of the restaurant closures during the corona pandemic. Additional safety technology from Leuze comes into play with the robots: MLD multiple light beam safety devices secure the work area against unwanted access from outside. Two PRK sensors connected crosswise in front of each robot reliably detect an incoming pallet. They then start the muting function, which briefly bridges the safety light grids so that the pallet can pass through.
Bottle cleaning by express
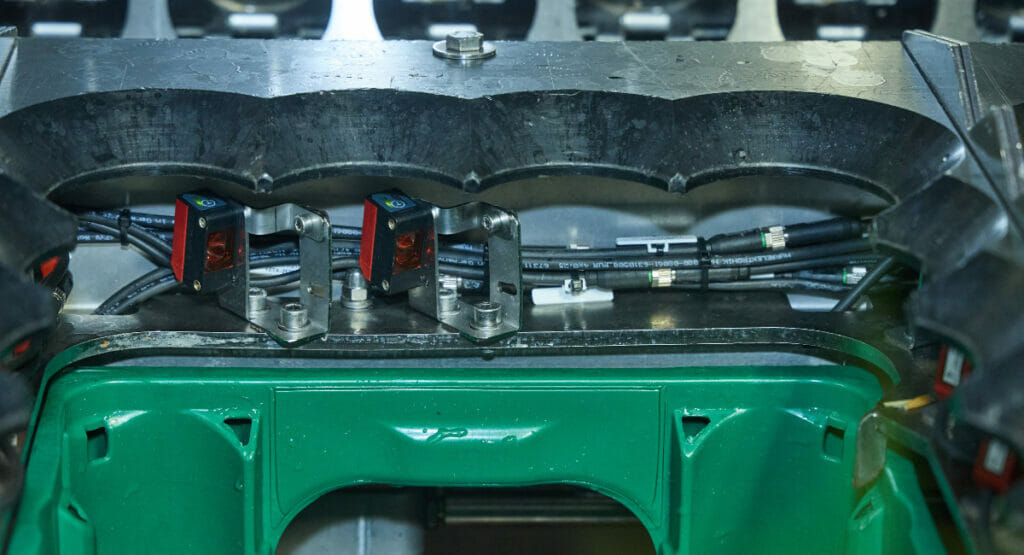
Empty beer crates first run through a special cleaning machine. The previously removed bottles end up in a large bottle washer that can clean up to 72,000 bottles. Here also, Leuze sensors are indispensable for a safe process: the sensors of the PRK series immediately detect when a bottle gets out of line on the bottle washer, stopping the machine then. Safety light curtains also monitor access here. After cleaning, each bottle is checked for residues. If there is still residue in the bottle after the first run or if label residue is still stuck on the outside, it goes through the cleaning process a second time. If the result is not as required, it is sorted out.
Fill fresh and check
Once the undamaged bottles are completely clean, it’s time to fill them. Here, Leuze sensors make it possible to regulate the belt speed. The system calculates the optimum speed based on the distances between two bottles. In the refillable-bottle line, up to 66,000 bottles per hour are filled with beer. That corresponds to 3,300 crates. The swing-bottle line operates on a separate production line. It fills 30,000 bottles per hour, or 1,500 crates every hour. In the further course, a camera system checks whether the quantity of the bottle contents are correct or not. After capping, PRK sensors detect whether each returnable bottle has been correctly crown corked or whether the swing-top bottle has been correctly sealed. Labelling follows: the bottle is aligned and neck, belly and back labels are affixed. Here, nothing is left to chance: While still in the machine, each label is checked for its correct position on the bottle.
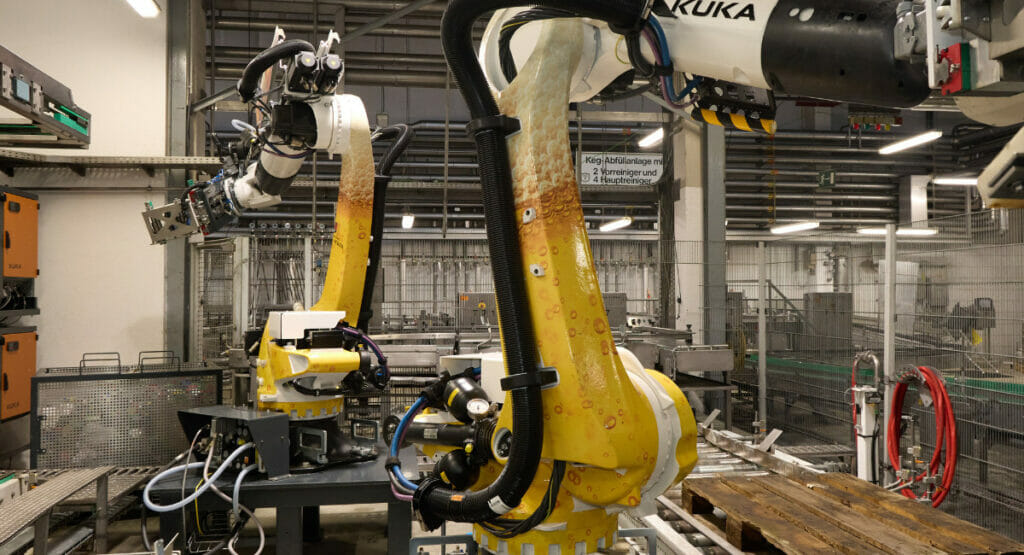
Every box in view
When the packer takes hold, the machine loads several crates at the same time with 20 beer bottles each. Leuze sensor technology is also used at this station: „During the crate inspection, sensors detect in fractions of a second whether a crate is completely filled,“ explains Andreas Eberle. „If a bottle is missing or lying crosswise, the crate is sorted out and the error is corrected manually by an employee.“ When crates are filled with swing-top bottles, they are also aligned with the label to the outside in a visually appealing manner. Leuze sensors detect the labels on the bottles and support the machine in correct positioning. In a final step, the crates are placed on pallets and delivered. Here, sensors are used to detect the presence of the pallets and optimise the material flow.
More packaging news
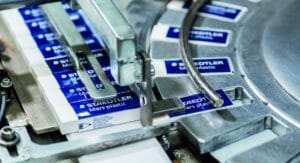
A contract with a handshake is valid
Managing director Tina Gerfer of Wilhelm Rasch Spezielmaschinenfabrik has modernized the company and successfully guided it through difficult times.
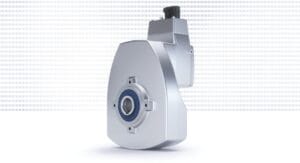
Asynchronous servo solutions for the packaging industry
From primary packaging to final packaging, electric drives play an important role. With a broad portfolio, Nord Drivesystems supports customers.
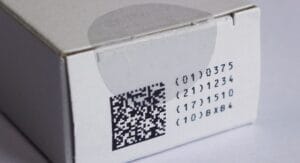
Label Durability
Labels offer many functions which can get lost due to label removal. PTS assesses labels and cardboard for durability and tamper evidence.
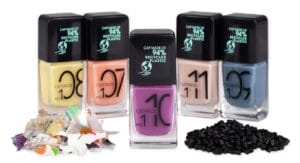
More design for recycling for cosmetics packaging
Packaging for decorative cosmetics is very special. The Forum Rezyklat calls for the recyclability of packaging to be taken into account when designing it.
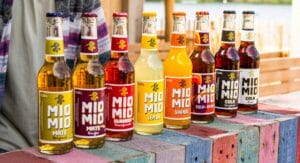
Innovation Barometer 2024
According to a survey conducted by Aktionsforum Glasverpackung 2024 is set to be a highly innovative year for glass packaging.
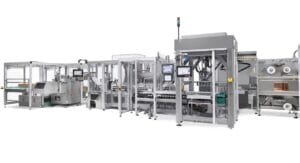
Flexible packaging system for natural cosmetics
Sustainability is part of Weleda’s identity. IWK is also contributing to this with its new flexible packaging line for many natural cosmetic products.