The Optima group of companies has holistically adapted the Total Care service programme to customer needs. Whether for fast production start-up, long-term support, spare parts supply, efficiency improvement or digital support during maintenance: the right solution is available for every challenge.
The company has risen to the challenges and managed to develop into a total solution provider for its customers: fully comprehensive along the entire life cycle of the machine. The thinking behind the comprehensive Optima Total Care service programme is clear. The focus is placed on the success of the customers and their safe production through excellent services, because at Optima, „We care for our customers“ is more than a slogan, it’s a promise.
Firmly anchored in the customer's factory
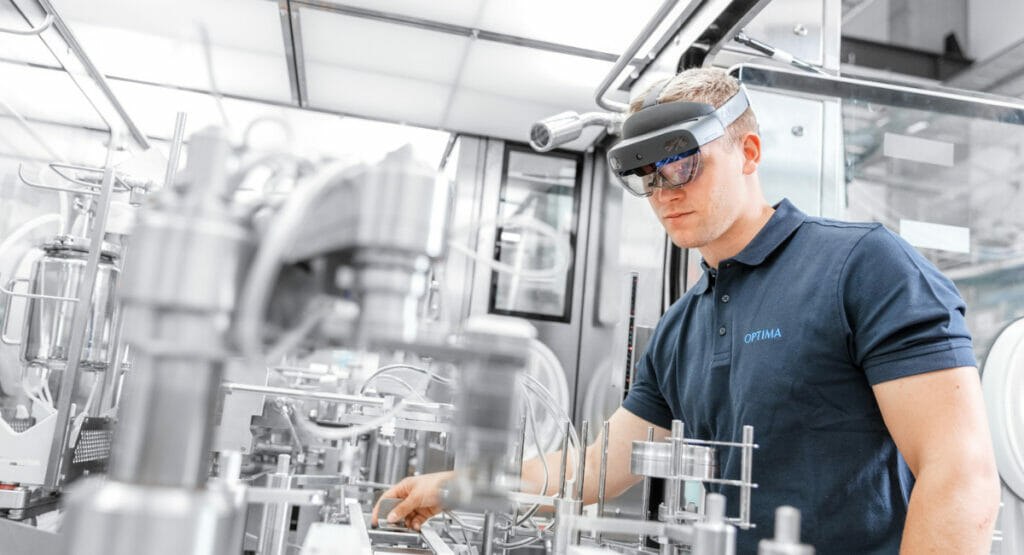
In order to be able to support customers even better and faster, the services were adapted and optimised to the roles in the factory. For example, the production manager of a globally operating company (let’s call him Tom) has difficulties keeping production efficiency at a high level. One reason for this is that the format change over time used to be too long.
The digital Optima Change Over Assist offers the solution. With its help, even inexperienced machine operators can navigate quickly and safely through a complex format change. This makes problems with constantly changing format changes and frequently changing personnel a thing of the past. If Tom only knew that the Change Over Assist is only one of countless little helpers of the Optima Service.
„Our goal is to ensure the success of our customers and thus deliver tangible added value. With our overarching service offering Optima Total Care, we are able to live up to this claim. Only by responding to our customers and their requirements can we achieve great things together.“
Dr Stefan König, Managing Director at Optima packaging group GmbH
Focus on lifetime production readiness
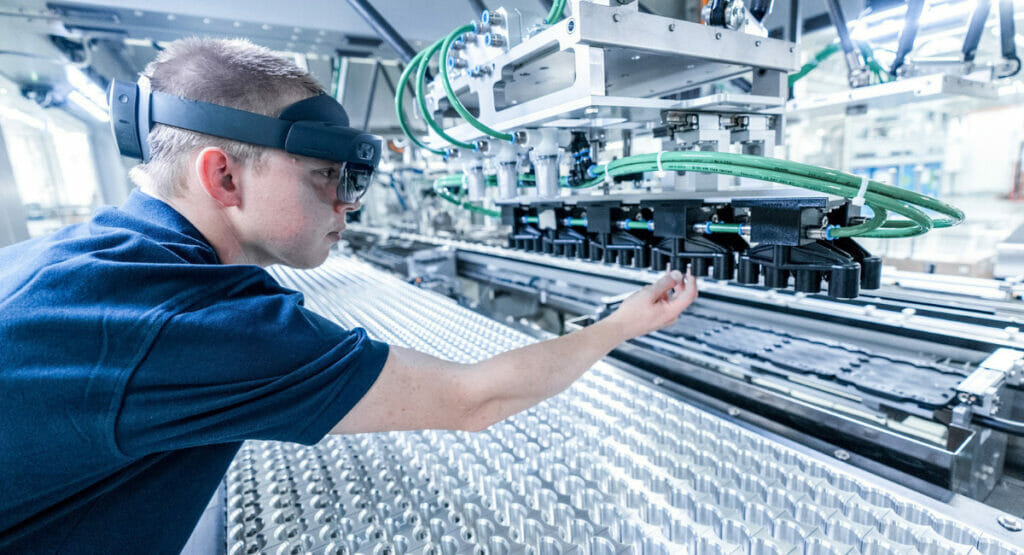
Optima is committed to providing customised and expandable service solutions as well as maximum availability. To this end, the service portfolio has been sharpened and is now based on four pillars that combine classic and digital services and are always geared to the needs of the customers:
- Core Services
Core Services safeguard production by bringing in and commissioning, optimal spare parts supply as a „Global Supply Chain Partner“, planning overhauls, new formats, upgrades or industry-leading maintenance systems such as digitally supported reliability-based maintenance concepts. Current guidelines and safety standards are adhered to, resources are saved, profitability and productivity are improved and unplanned stops in production are reduced to almost zero: All in all, this is unique in the packaging industry. - Knowledge Services
Knowledge transfer through seamless and intuitively provided content helps machine operators through everyday production. Employees are trained quickly and efficiently through training, video instructions and smart instructions. Specially trained „Subject Matter Experts“ take knowledge transfer to a new level for customers. Information is provided digitally and can be found quickly and easily. In the event of a malfunction, the system indicates the location of the fault directly through video monitoring of the processes: The machine guides the operator quickly and in a solution-oriented manner. - Efficiency Services
The demand for overall plant efficiency is very high. Efficiency Services ensure that the plant is permanently operated with maximum availability and potentials are quickly and easily identified. Remote support with concrete instructions in the event of malfunctions as well as process and efficiency analyses based on data are now part of daily business at Optima. This is how production succeeds at world champion level. - Advanced Services
Feasibility studies and simulations or research and development activities are carried out jointly at the customer’s request as a „next level“ already in the project phase in order to optimally adapt the development of the plant to the customer’s needs. Through expertise in consulting and product development, for example when new or alternative materials are to be used, Optima can thus provide its customers with a competitive advantage.
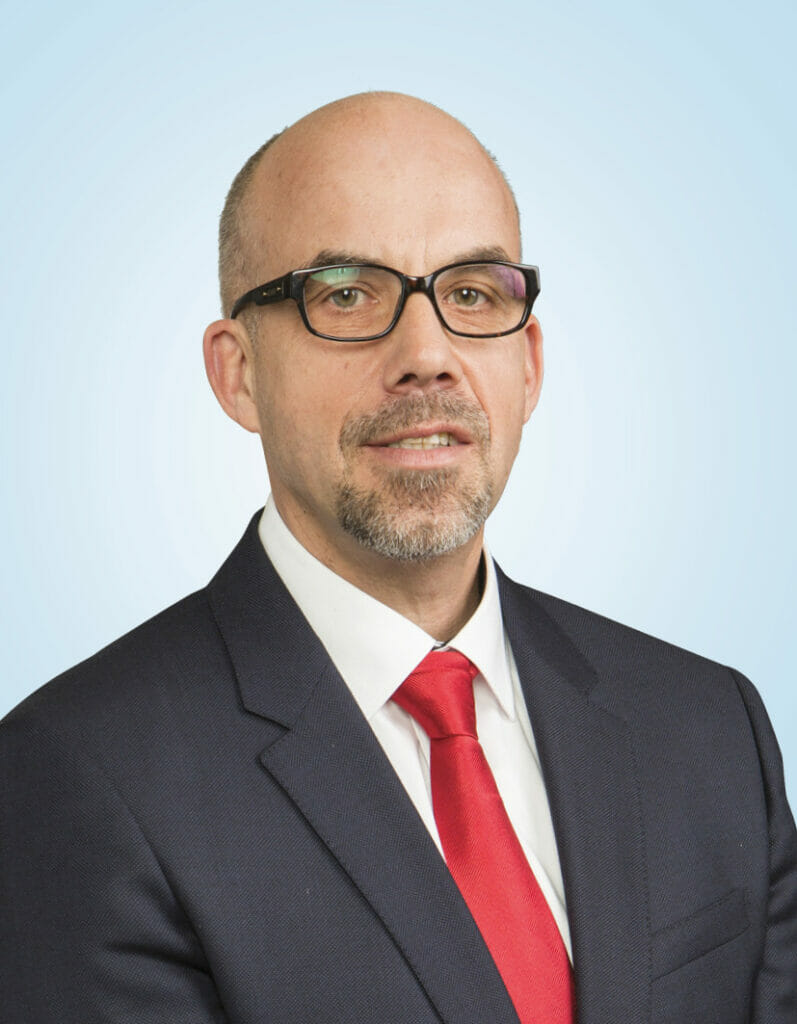
„With our service portfolio, we can stand out from the competition and convince customers of our comprehensive services. Having a contact person from day one throughout the entire life cycle of the system is what our customers need. And that’s what we can offer them with our service.“
Michael Weber, Director Service at Optima Consumer
Central customer platform plus process topics
The central customer platform, myOptima, is the heart of the digital orbit. The platform is available at all times and provides access to video instructions, smart instructions and even digitised documentation for the respective equipment. By providing 3D data, duplications of the equipment can be created, allowing machine operators to embark on a digital journey through drawings, circuit diagrams or pneumatic plans.
The targeted optimisation of all production processes needs one thing above all: valid data. With the stand-alone digital process management system OPAL, data is analysed and evaluated, which greatly assists data science managers or process analysts, for example. OPAL records production data such as downtimes, alarms or quantity counters and generates key figures and reports on this basis. Only in this way is transparent production, a basis for improvement measures and increased productivity possible. By now at the latest, it should be clear to Tom why Optima Total Care is not only helpful to him as a production manager. Whether machine operator, process analyst or maintenance staff, Optima Total Care stands for holistic, user-oriented, efficient and safe service – for the entire life cycle of the machine.
More packaging news
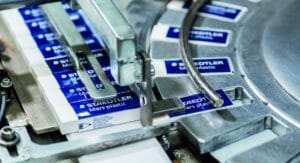
A contract with a handshake is valid
Managing director Tina Gerfer of Wilhelm Rasch Spezielmaschinenfabrik has modernized the company and successfully guided it through difficult times.
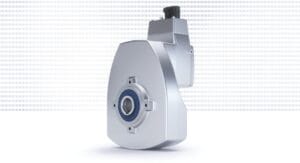
Asynchronous servo solutions for the packaging industry
From primary packaging to final packaging, electric drives play an important role. With a broad portfolio, Nord Drivesystems supports customers.
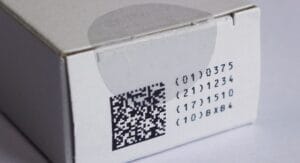
Label Durability
Labels offer many functions which can get lost due to label removal. PTS assesses labels and cardboard for durability and tamper evidence.
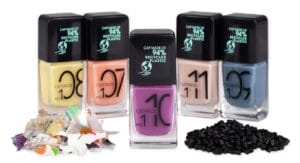
More design for recycling for cosmetics packaging
Packaging for decorative cosmetics is very special. The Forum Rezyklat calls for the recyclability of packaging to be taken into account when designing it.
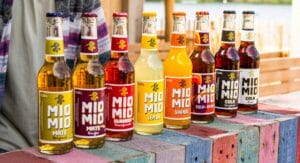
Innovation Barometer 2024
According to a survey conducted by Aktionsforum Glasverpackung 2024 is set to be a highly innovative year for glass packaging.
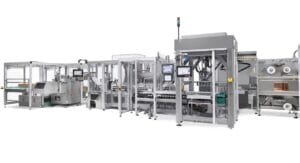
Flexible packaging system for natural cosmetics
Sustainability is part of Weleda’s identity. IWK is also contributing to this with its new flexible packaging line for many natural cosmetic products.