In times of raw material scarcity and uncertainties about their future availability, it is becoming increasingly important to keep them in circulation for as long as possible. Added to this is the changed awareness of consumers who demand sustainable packaging solutions. Fibre-based packaging is particularly popular because it conveys a feeling of naturalness and sustainability. However, not always rightly so, because depending on the material or design, recyclability can be lost. But how can a circular economy be achieved with materials such as paper, cardboard, carton, but also alternative materials such as grass or silphia? The STI Group is also exploring this question, focusing on design for and from recycling.
In the picturesque little town of Lauterbach, Hessen, one half-timbered house follows the next, and it is difficult to choose the most beautiful one. A few hundred metres out of town is the STI Group factory. Here, folding boxes and displays are produced for numerous customers. The cardboard or corrugated board for this often comes from not far away, namely from the Adolf Jass paper mill, which is located in Fulda, a thirty-minute drive away.
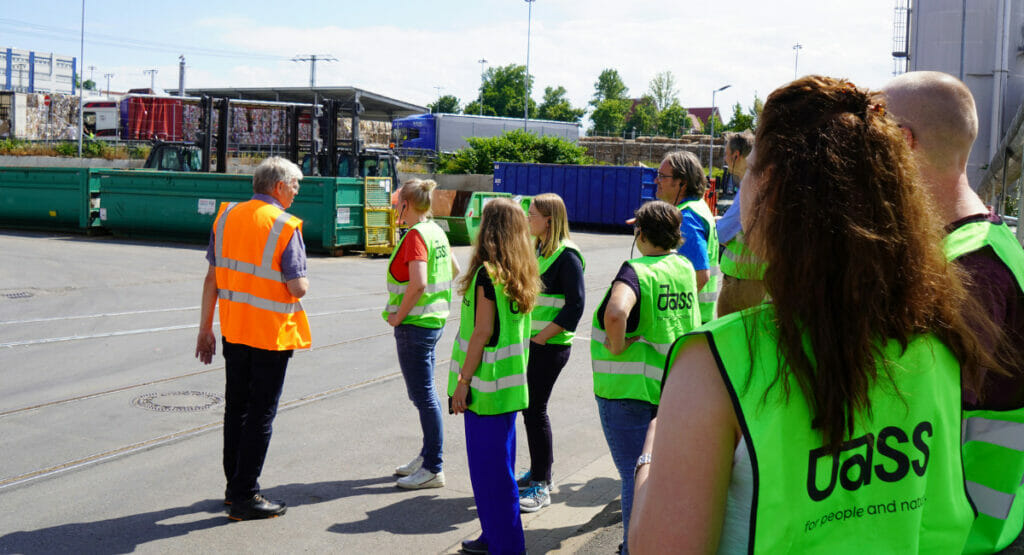
And this is where the packaging of many of the products we see and possibly buy in the supermarket begins. At the same time, it also ends here, because Jass produces new corrugated board from waste paper. Therefore, the creation of the packaging material is both the beginning and the end, and we are right in the middle of the circular economy. In addition, it immediately becomes clear why the design of a packaging must already think about recycling and the end of the first life cycle, because not all waste paper that arrives here can also be recycled. A small part is lost. For the larger part, another life begins as corrugated board.
The cooperation between Jass and the STI Group then results in new packaging made from recycled material. In the printing plant, the corrugated cardboard is married with the printed liners and punched and folded into a wide variety of boxes. When consumers return the packaging to the cycle via the waste paper bin after use, the whole thing can start all over again.
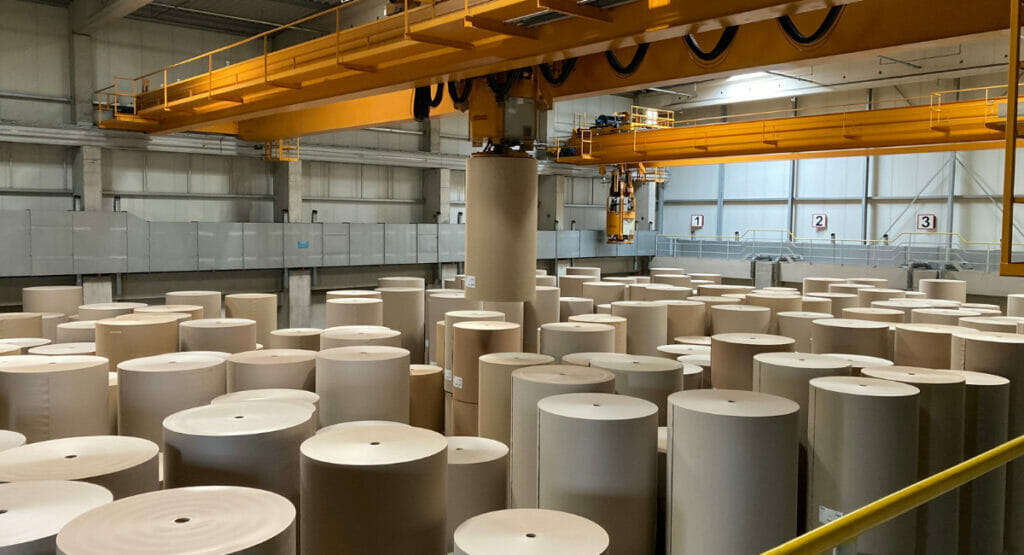
Teamwork makes the dream work
However, for this cycle to work, it depends on the development and design. Here, the experts of the STI Group provide advice and support with their many years of know-how, but they also like to get input from other partners. This was the case at the „Design For/From Recycling“ workshop. What materials other than wood fibres can be used, and what should be taken into account with regard to recycling? Various experts tried to find answers to these questions, among others. Pfleiderer uses grass or wheat as a source of raw materials for its speciality papers, for example. The materials are regionally available, and with the use of wheat straw pulp, a residual material is used that is produced in the harvesting process anyway.
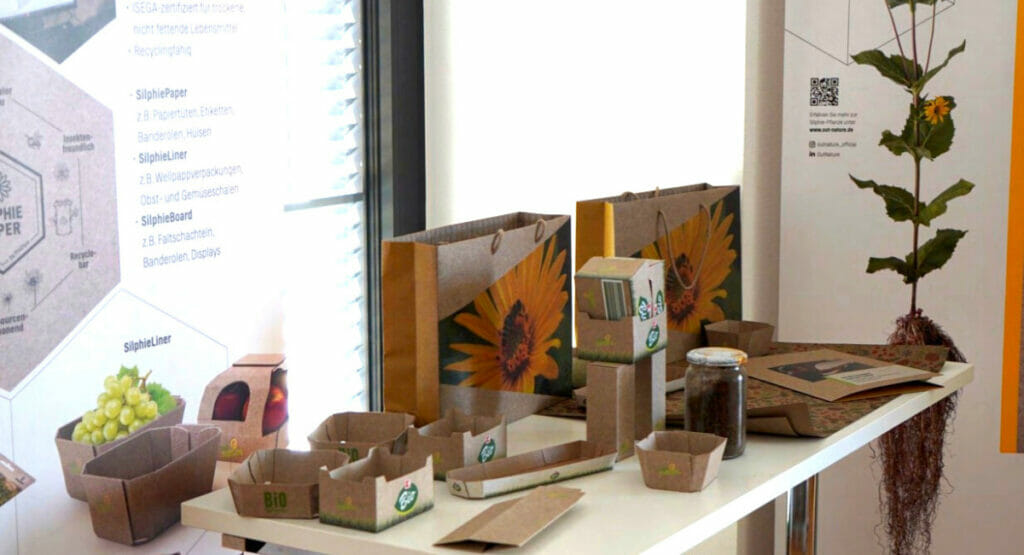
With PreZero, the Schwarz Group has a company that deals with ideas from energy management to logistics. This also includes the OutNature brand, which is dedicated to the use of the silphia plant in paper production. The plant not only serves as a fibre supplier for paper production, but is also an energy crop and finds further use in biogas plants. Together with the STI Group, folding boxes for cress and tomatoes have already been developed and produced. The paper is also used in display solutions for the Always and Gilette brands.
Finding the right material
So, what is important when designing packaging? Primarily the packaging material. It is here that there are always creative and new solutions that can bring new challenges at the same time. Andreas Milk from the design agency, Milk, presented a primary packaging that disappears or can become part of the packaged product. Those who order Soupa Soup receive a box with a bag as primary packaging that contains the ingredients for a soup. Here is what makes it particularly convenient for the consumer: the bag and its contents are simply boiled in a pot of water for three minutes when the soup is prepared and it dissolves. The packaging therefore disappears and the consumer does not have to worry about disposal.
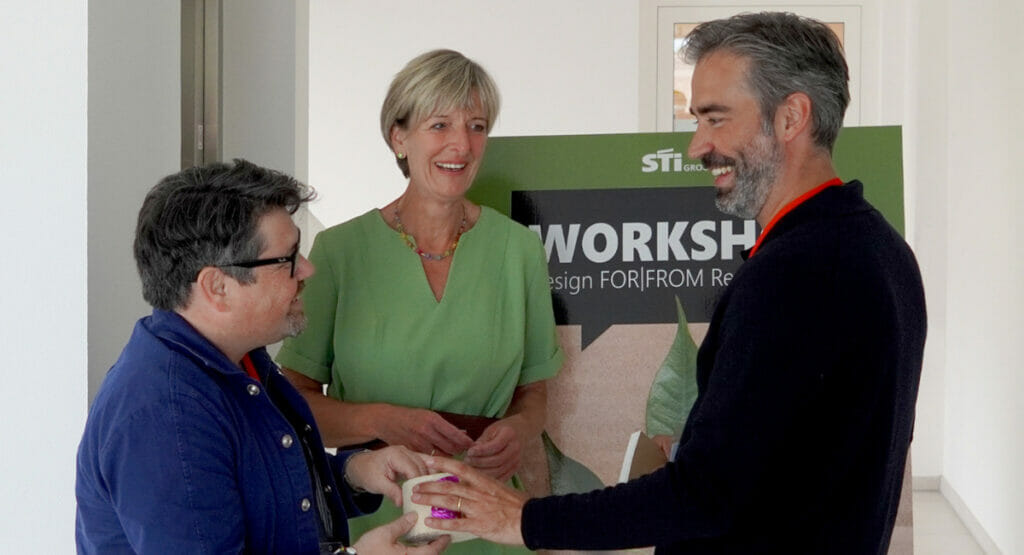
However, regulations on food packaging also bring to light a problem that fibre-based packaging has to deal with time and again: Paper and cardboard must be made of virgin fibre or have a barrier in the case of recycled materials. Since the primary packaging is part of the court, it loses its status as primary packaging and the shipping carton takes on this role. It must therefore have a coating or barrier, but this can pose a difficulty when it comes to recycling. This is where the STI Group comes into play again, as it seeks and develops solutions for such challenges as well. Instead of a PE coating for folding boxes that come into contact with food, the company uses a barrier coating for the Foodbox. This saves resources and ensures complete recyclability.
So, what is the conclusion to be drawn from the workshop? Something is definitely happening. Brands are striving to meet consumers‘ desire for sustainable products. This concerns not only the packaged product as such, but also the packaging. Therefore, this demand is being taken along the value chain from one station to the next, and all partners are researching and developing new ways to make packaging and processes more sustainable. The design thereby arises not only with a view to recycling, but also through recycling, as the materials are to be recycled.
„Sustainability has many facets, and the recyclability of packaging is our top priority. Fibre-based packaging is renewable, has closed loops and existing recycling systems. The workshop showed that there are many additional areas of application for packaging made of cardboard and corrugated board and that composite materials and plastics can often be substituted. The trend is towards lightweight materials – whereby the protection of the products always comes first.“
Claudia Rivinius, Marketing Director at STI Group
More packaging news
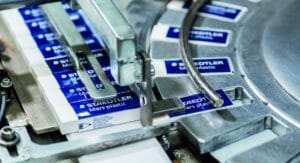
A contract with a handshake is valid
Managing director Tina Gerfer of Wilhelm Rasch Spezielmaschinenfabrik has modernized the company and successfully guided it through difficult times.
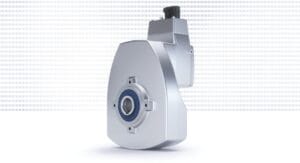
Asynchronous servo solutions for the packaging industry
From primary packaging to final packaging, electric drives play an important role. With a broad portfolio, Nord Drivesystems supports customers.
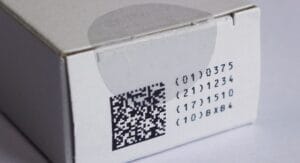
Label Durability
Labels offer many functions which can get lost due to label removal. PTS assesses labels and cardboard for durability and tamper evidence.
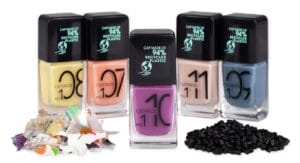
More design for recycling for cosmetics packaging
Packaging for decorative cosmetics is very special. The Forum Rezyklat calls for the recyclability of packaging to be taken into account when designing it.
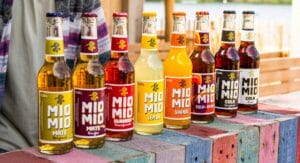
Innovation Barometer 2024
According to a survey conducted by Aktionsforum Glasverpackung 2024 is set to be a highly innovative year for glass packaging.
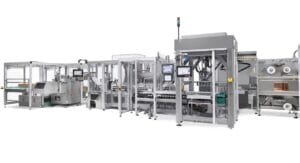
Flexible packaging system for natural cosmetics
Sustainability is part of Weleda’s identity. IWK is also contributing to this with its new flexible packaging line for many natural cosmetic products.