For the production of small batch sizes in conjunction with a broad product portfolio, equipment that offers optimum agility and flexibility is in demand among manufacturers in consumer goods production. For bundling products in film packaging, a new stretch bundler from Pester Pac Automation sets standards in terms of automated processes and sustainable packaging materials.
„Our new stretch bander is intended to be a milestone for sustainable and economical packaging processes in the consumer segment that meets the latest trends and the current requirements of our customers,“ emphasises Frank Resch, Technical Director Business Unit Consumer at Pester Pac Automation GmbH. The development team’s objective encompassed a wide range of parameters: the system should open up new avenues for secure packaging, handling, transport and shelf-ready packaging and thus act more efficiently, sustainably and intelligently than existing solutions on the market. In addition, maximum machine efficiency and fast format changes with short changeover times for the production of small batches were a must.
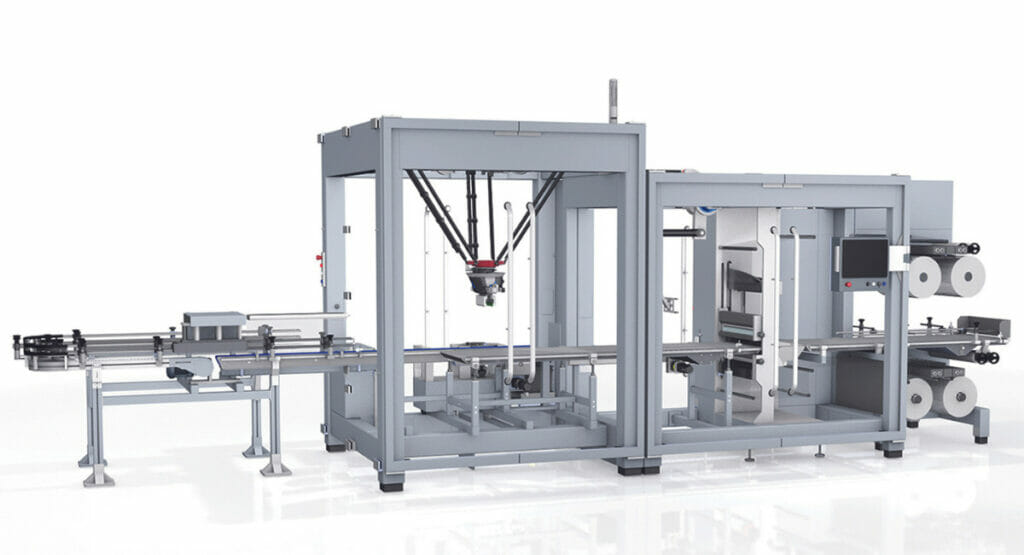
Automation with innovative robot technology
The result is impressive: safe and stable stretch film packs are produced without the use of a shrink tunnel. The flexible PEWO-pack 600 high-speed machine performs at up to 60 packs per minute. This is about 80 per cent faster than with conventional stretching processes. Almost all products from the cosmetics, health care or personal care sectors, such as moulded bottles, aerosol cans, jars or folding boxes, can be processed, and shelf-ready packs are also an option. The new stretch bander can also be integrated quickly and easily into upstream production.
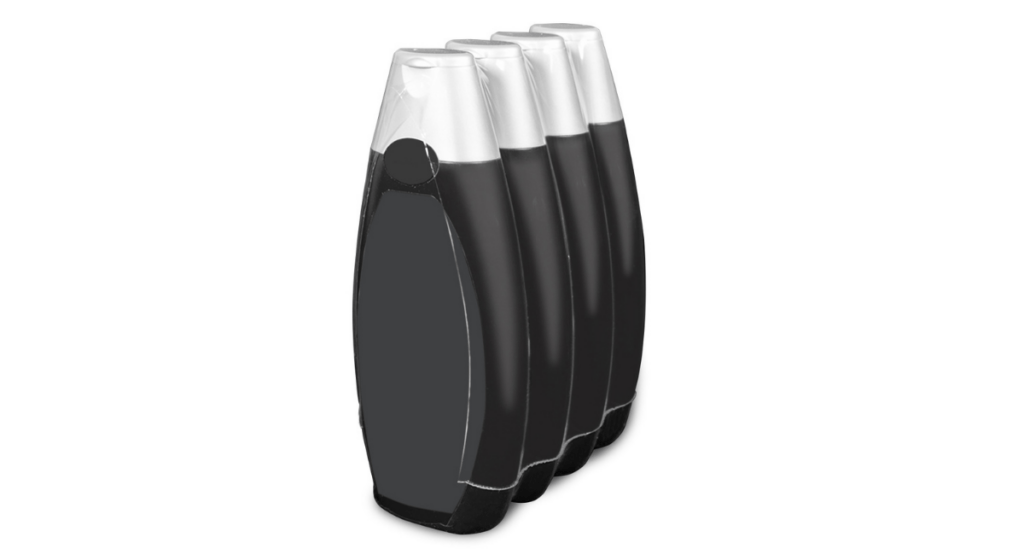
„The new system also offers several advantages in terms of automation,“ explains Resch. By using modern robot technology, the PEWO-pack 600 demonstrates sensitive handling even for high-speed applications. The fully automatic and tool-free format changeover allows a quick and easy changeover for new tasks.
The agile Delta pick & place robot offers flexibility for a variety of different applications. It groups and configures the incoming products in the specified formation. Pester’s specially developed gripper technology enables easy and fast product changeover in less than three minutes. The high-speed stretch-bundler can process 360 products per minute in a single lane with its two robotic units, depending on the product and configuration.
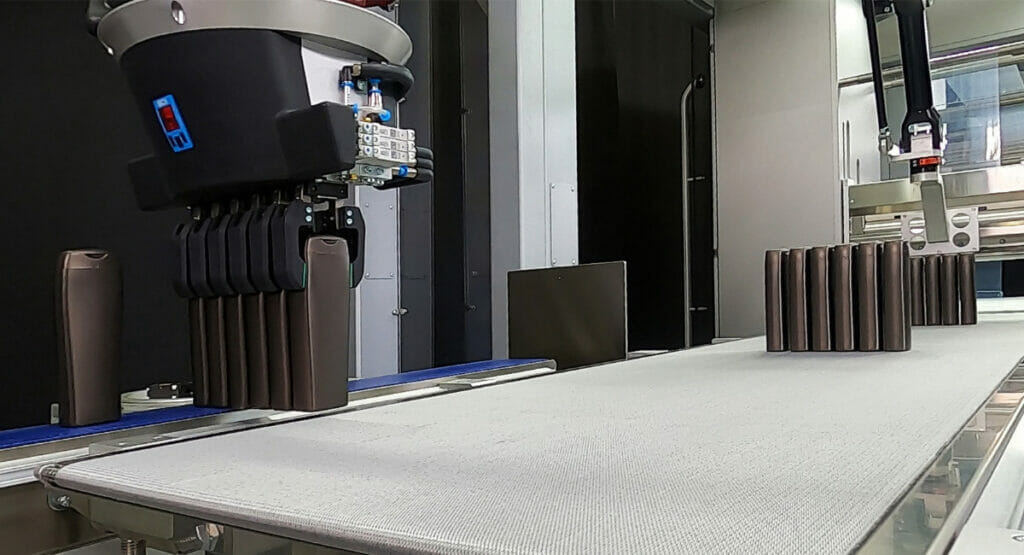
To guarantee optimal control for all components, Frank Resch and his team opted for Rockwell Automation technologies. The central control for the robot enables the simplest operation and maintenance. In previous projects, they had already had the best experiences with the products and solutions and had also learned to appreciate the interoperability.
„Rockwell Automation provided essential support for our new development. With this technology, we were able to achieve the ideal level of automation for our customers‘ requirements.“
Frank Resch
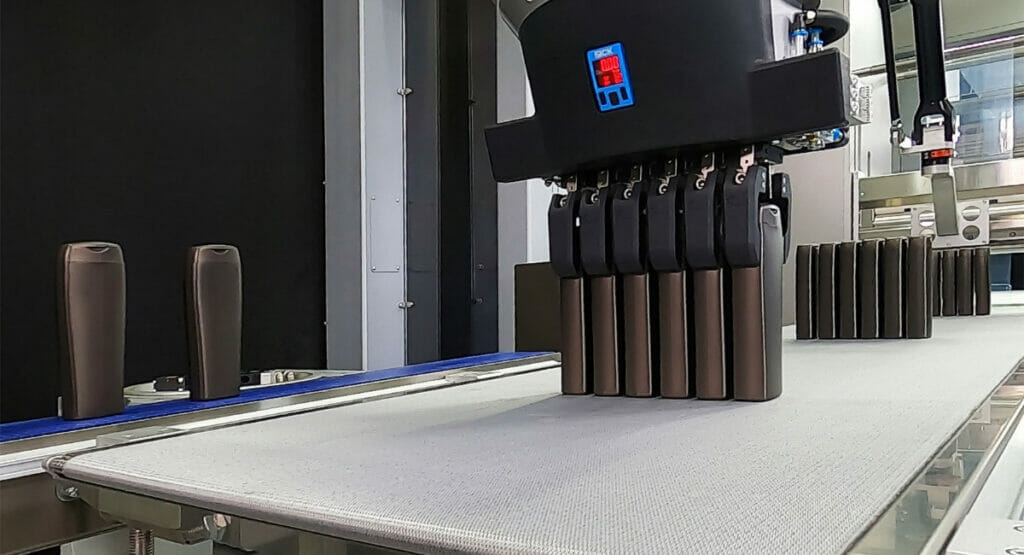
Intelligent operation - digital and simple
One of the most important strategic business areas at Pester is digitalisation. With new digital solutions, the company wants to set standards once again. For example, communication between the machine and the operating personnel is intuitive and simple: „Our machines are equipped throughout with a new HMI generation with interactive 3-D visualisation for intelligent machine operation and predictive maintenance. We also offer real-time process improvement support with our remote service and OEE monitoring,“ explains Resch.
Use of alternative foils
The implementation of sustainable production processes has a high priority at Pester. The innovative stretching line combines numerous advantages for this. An energy-saving packaging process for stable, resource-saving film packs with maximum transport protection of the packaged goods sets forward-looking impulses for end-of-line packaging. The stability and safety of the packaging units required for transport was confirmed in a certified transport test by an independent testing institute.
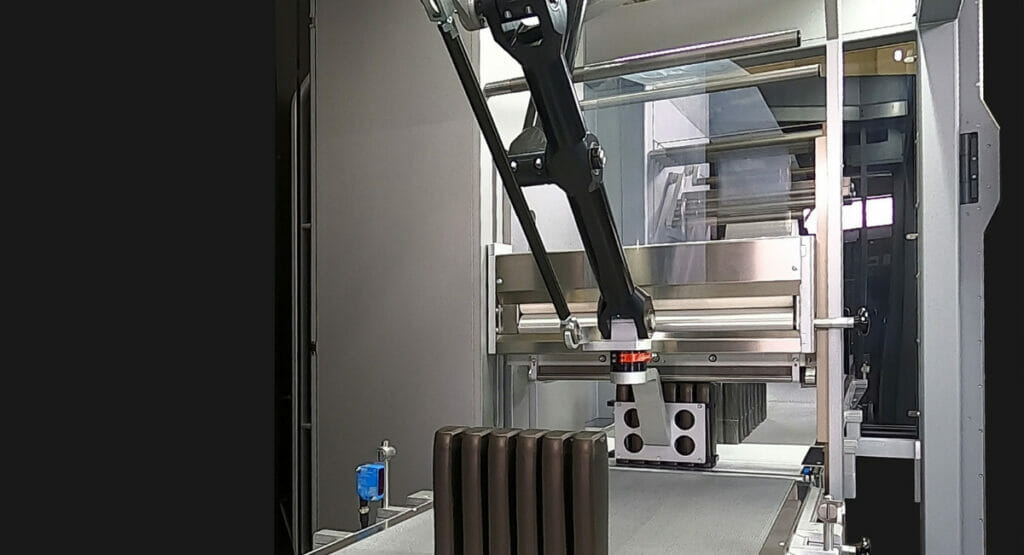
Compared to a conventional shrink-wrapping application, the new machine concept can save up to 75 per cent electrical energy and, thanks to the compact machine design, about 30 per cent of the production area. A reduction in packaging material requirements of between 30 and 50 per cent can be realised, depending on the application. The system can process fully recyclable plastic mono-materials as well as packaging materials with a high recycled content without any restrictions on machine performance.
A holistic life cycle analysis by the renowned IFEU (Institute for Energy and Environmental Research) shows the ecological advantages of using stretching technology: on average, the alternative packaging system has a material saving of 50 per cent compared to a shrink application with „virgin“ PE films (30 µm). For this purpose, eight relevant impact categories and all known disposal scenarios of the packaging material were examined and compared. Emissions can also be reduced by half.
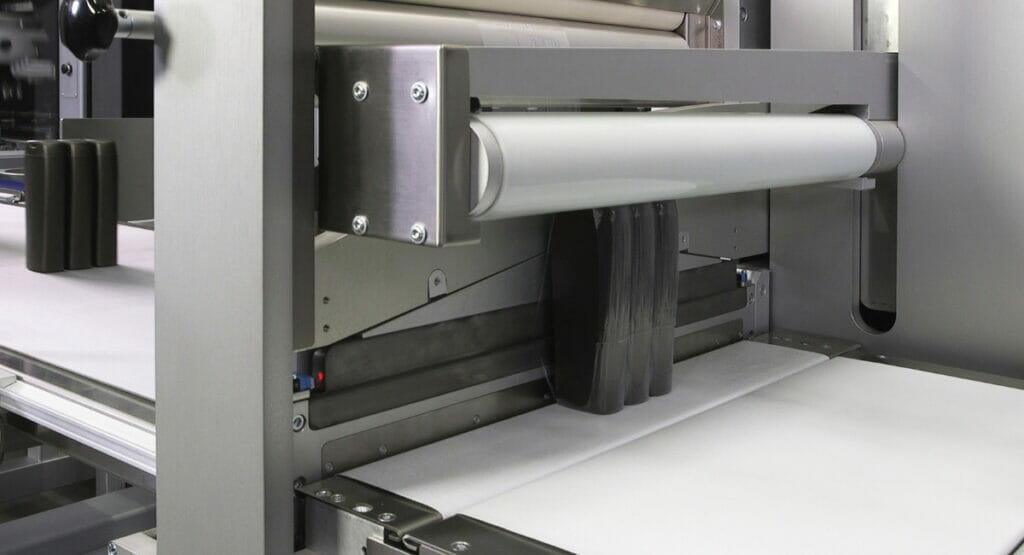
Flexible multi-talent in product handling
The system has been impressing top players in the consumer industry since its market launch at the end of 2021 and is used by well-known companies worldwide. The incoming products are fed to the film curtain via a slide-in unit. There, controlled film transport units are responsible for the stretching process in interaction with the sealing system. The packs, tightly enclosed with stretch film, are stable and sturdy. Various multipacks can be produced, which are transferred to the subsequent packaging process in the required configurations.
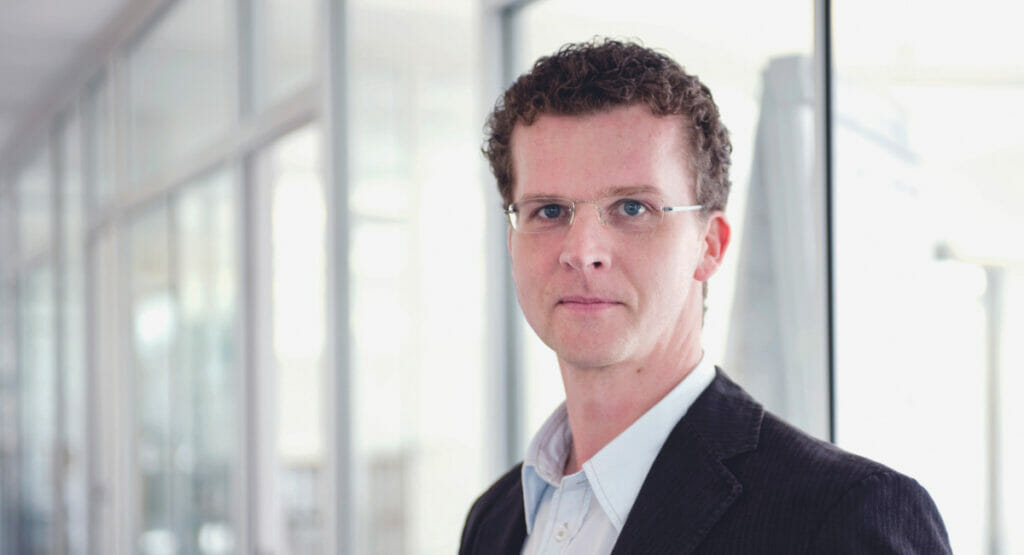
„We have incorporated the latest trends and requirements of our customers into this new development. The system offers the highest flexibility for small batch sizes and is ideal for use in 24/7 operation with reliable machine performance. We have invested a lot of commitment and dedication to detail in this plant and integrated state-of-the-art components at the highest level of automation. The further development of sustainable production processes for our customers is a matter close to our hearts. With this, we are opening up new dimensions for the modern consumer packaging of tomorrow.“
Frank Resch
More packaging news
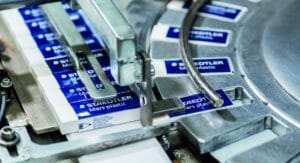
A contract with a handshake is valid
Managing director Tina Gerfer of Wilhelm Rasch Spezielmaschinenfabrik has modernized the company and successfully guided it through difficult times.
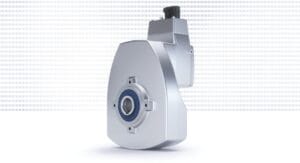
Asynchronous servo solutions for the packaging industry
From primary packaging to final packaging, electric drives play an important role. With a broad portfolio, Nord Drivesystems supports customers.
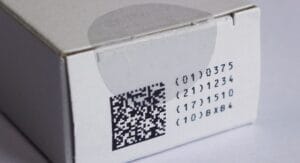
Label Durability
Labels offer many functions which can get lost due to label removal. PTS assesses labels and cardboard for durability and tamper evidence.
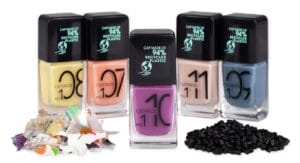
More design for recycling for cosmetics packaging
Packaging for decorative cosmetics is very special. The Forum Rezyklat calls for the recyclability of packaging to be taken into account when designing it.
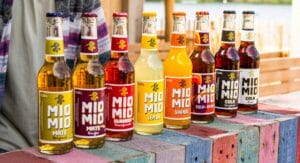
Innovation Barometer 2024
According to a survey conducted by Aktionsforum Glasverpackung 2024 is set to be a highly innovative year for glass packaging.
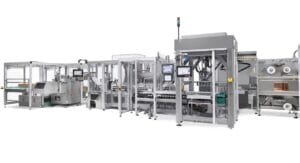
Flexible packaging system for natural cosmetics
Sustainability is part of Weleda’s identity. IWK is also contributing to this with its new flexible packaging line for many natural cosmetic products.