Ein Großteil der zahnmedizinischen Instrumente des Unternehmens VDW wird auf Blistermaschinen von verschiedenen Herstellern verpackt und etikettiert. Um die Abläufe zu optimieren und zukünftig auch sehr kleine Chargen automatisch etikettieren zu können, setzt man auf eine neue Lösung der Intrex Deutschland GmbH.
VDW gilt als einer der ersten Produzenten von Wurzelkanalinstrumenten in ganz Europa und hat als Pionier die Grundlagen der Wurzelkanalbehandlung entscheidend geprägt. Seit seiner Gründung im Jahr 1869 ist das Unternehmen dieser Spezialisierung treu geblieben und setzt mit seinem fundiertem Know-how und Produktinnovationen immer wieder neue Maßstäbe. VDW bietet Zahnärzten ein umfassendes Endo-System aus Produkten und Dienstleistungen, die über alle Behandlungsschritte hinweg ineinander greifen. Die Unternehmenszentrale mit den hoch technisierten Fertigungsstätten befindet sich in München. Von dort aus werden die Produkte in mehr als 80 Länder der Welt geliefert.
Kundenspezifische Chargen etikettieren
Ein Großteil der Instrumente wird auf Blistermaschinen von unterschiedlichen Herstellern verpackt und etikettiert. Problematisch ist dabei die hohe Variantenvielfalt durch kundenspezifische Etiketten, die täglich mehrfache Maschinenumrüstungen notwendig machen. Da die zu etikettierenden kundenspezifischen Chargen aber häufig nur Auflagen von weniger als 200 Stück haben, ist eine Umstellung der Anlagen zu aufwendig. Sehr kleine Chargen müssen manuell etikettiert werden.
VDW suchte deshalb nach Möglichkeiten, die Prozesse Verpacken und Etikettieren zu trennen. Durch eine Empfehlung kam man mit der Intrex Deutschland GmbH ins Gespräch, und dort wurde gemeinsam während einer Entwicklungszeit von zwölf Monaten ein maßgeschneidertes Lösungskonzept realisiert.
Das Szenario: Künftig werden die Produkte nach dem Blistern nicht mehr etikettiert, sondern mit einem Datamatrixcode bedruckt, der alle produkt- und fertigungsbezogenen Daten enthält. Danach werden die Blister in sogenannten Tubes (Boxen bzw. Kartonmagazine) eingelagert. Zum Einsatz kommt der von der Intrex Deutschland GmbH neu entwickelte LSC-100 Etikettierer: Er kann aktuell vier unterschiedliche Blisterformate verarbeiten und auftragsbezogen etikettieren. Die modulare Bauweise ermöglicht eine Erweiterung auf zusätzliche Formate und Produkte.
Gesicherter Datenzugriff
Mit der auf einem IPC installierten KUPvision-Software werden alle Funktionen der neuen Etikettieranlage gesteuert und überwacht. Die Software speichert Informationen wie Benutzeranmeldungen, Auftrags- und Formatwechsel usw. in einem Audit Trail. Zu jedem Eintrag werden Datum, Uhrzeit, Benutzer, Funktionsdaten und Parameter gesichert. Der Audit Trail und die Statistik-Daten können jederzeit abgerufen und auch separat auf einem Datenträger gespeichert werden.
Abwicklung in der Praxis
Für die Abwicklung eines Kundenauftrages erhält der Bediener eine Packliste in Papierform. Durch das Einscannen des Strichcodes auf dem Auftragsblatt werden die produkt- und auftragsbezogenen Informationen aus dem ERP-System der VDW GmbH vom LSC-100 Etikettierer ausgelesen und übersichtlich dargestellt. Der Bearbeiter holt die zu bearbeitenden, in Tubes befindlichen Produkte aus dem Lager. Auf den Tubes sind Datamatrixcodes angebracht, die den Inhalt wiedergeben. Nachfolgend startet er auf der KUPvision Oberfläche einen neuen Auftrag und scannt den Barcode auf der Packliste mit dem Handscanner ein.
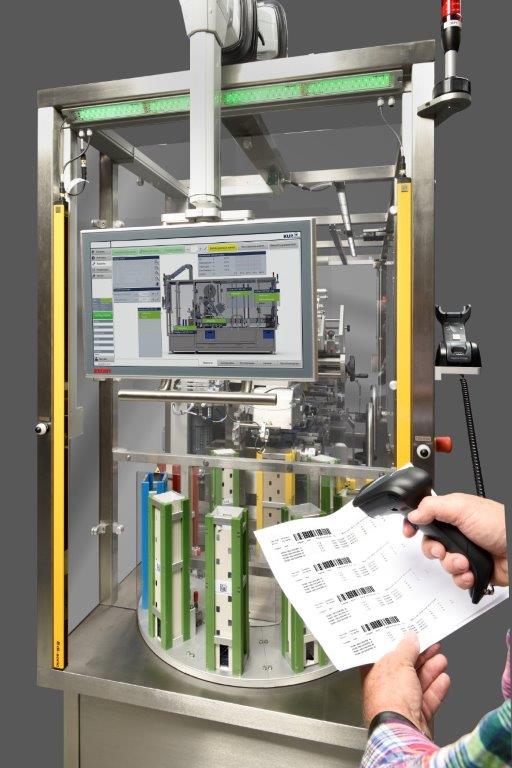
(Bild: Intrex Deutschland)
Bei korrekten Auftragsdaten wird der Bediener mit einer Meldung zum Bestücken eines sogenannten Karussells aufgefordert, das mit insgesamt 10 Magazinen ausgestattet ist. Der Bediener stellt die Tubes in die Magazine dieses Karussells, und danach arbeitet die KUPvision Software vor dem Start noch eine Reihe von Prüfvorgängen ab:
- Vergleich der Datamatrixcodes auf den eingelegten Tubes/Boxen mit den Auftragsdaten
- Zusammenfassung/Übersicht des zu verarbeitenden Auftrags
- Pre-Flight-Check (Prüfung der Labeldaten auf Konsistenz)
- Abgleich aller Etiketten-Layoutdaten mit einem Etikettenmanagementsystem.
Kontrollierte Auftragsproduktion
Die Maschine startet mit der Produktion des Auftrags, dabei werden die Blister zum Abstapeln von unten mit einem „Fahrstuhl“ angehoben und von einem Zuführarm des Bandauflegers mechanisch entnommen. Die Zuführung ist zweiarmig angeordnet und mit jeweils zwei pneumatischen Saugmodulen ausgestattet. Wenn das erste Saugmodul ein Produkt auf das Förderband legt, wird gleichzeitig ein weiteres Produkt vom Karussell genommen. Anschließend wechseln die Arme ihre Position und wiederholen den Vorgang. Jedes Produkt wird auf dem Transportband platziert und durch auf dem Transportband befestigte Stollen bewegt, um eine stabile Position während des Etikettierens zu gewährleisten.
Um sicherzustellen, dass die dem Auftrag entsprechenden richtigen Blister auf das Band gelegt wurden, wird der Datamatrixcode auf den Blistern kontrolliert. Diese Datenprüfung erfolgt mit dem Prüfsystem COGNEX® Typ DataMan. Als gut befundene Produkte bleiben zur Weiterverarbeitung auf dem Transportband, Schlechtprodukte werden ausgeworfen.
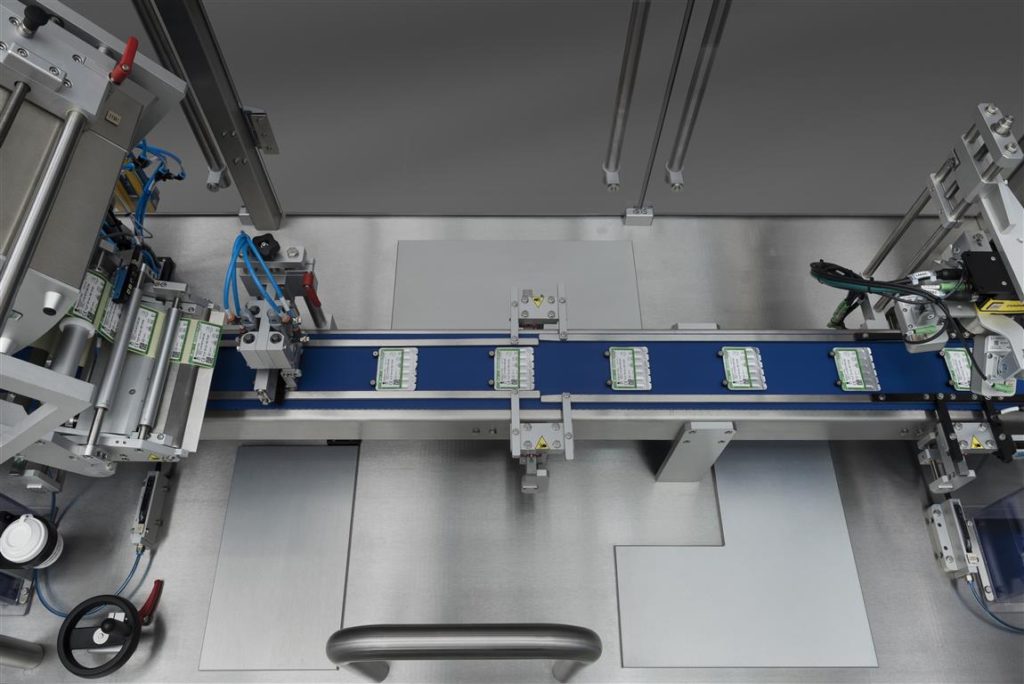
(Bild: Intrex Deutschland)
Anschließend bedruckt das Etikettiersystem intrex® 200+ die vorgefertigten Grundetiketten im Thermotransfer-Druckverfahren (Domino V320i) mit auftragsspezifischen/variablen Daten und etikettiert damit die Blister auf dem Transportband. Zur Qualitätsprüfung der Drucke und der aufgebrachten Etiketten wird die Kamera In-Sight 7905 von COGNEX eingesetzt. Sie kontrolliert die bedruckten Etiketten auf Vollständigkeit und Lesbarkeit. Als gut bewertete Produkte bleiben auf dem Transportband, Schlechtprodukte werden ausgeworfen.
Die erste Maschine wurde jetzt erfolgreich bei VDW in Betrieb genommen, weitere Anlagen sind in Planung. Das nachfolgende Verpacken der etikettierten Produkte erfolgt im Unternehmen aktuell noch von Hand, aber auch hier sind automatisierte Abläufe bereits in Planung.