Nachhaltigkeit ist Teil der Identität von Weleda. In allen Unternehmensbereichen setzt man sich für ein zukunftsfähiges Wirtschaften ein – von der Gewinnung der Produktrohstoffe, deren Verarbeitung, dem Abfüllen und Verpacken, dem In-Verkehr-Bringen bis hin zu recyclingfähigen Verpackungen. Dazu trägt auch IWK mit ihrer neuen flexiblen Verpackungslinie für viele Naturkosmetikprodukte bei.
Weleda ist die weltweit führende Herstellerin von zertifizierter Naturkosmetik sowie anthroposophischen Arzneimitteln mit einem Produktportfolio von mehr als 1.000 Arzneimitteln, einer Vielzahl von Manufakturherstellungen sowie 120 Naturkosmetika. Für die Pflegeserien „Skin Food“, „Granatapfel“ und weitere Anwendungen investierte das Unternehmen am deutschen und größten Standort in Schwäbisch Gmünd in eine Turnkey-Verpackungslinie von IWK Verpackungstechnik. Die besondere Herausforderung bestand in der Vielfalt der Produkte und ihren unterschiedlichen Formaten und Volumina, die auf der Linie abgefüllt und verpackt werden sollten. Die flexible Verpackungslinie ist automatisiert und verarbeitet sicher sowohl Aluminium- als auch Kunststofftuben in unterschiedlichen Größen. Kollaborierende Roboter (Cobots) sorgen für automatisierte Prozesse am Anfang der Linie am Tubenfüller.
Moderne Tubenlinie auf limitiertem Areal
Die Anfrage seitens Weleda nach einem leistungsstarken und automatisierten Verpackungssystem zum Abfüllen, Kartonieren und Verpacken zertifizierter Naturkosmetikprodukte an IWK erfolgte im Vorfeld des 100-jährigen Firmenjubiläums von Weleda. Ziel war es, am Standort Schwäbisch Gmünd eine veraltete Verpackungslinie durch die weitgehend automatisierte und flexible IWK Turnkey-Anlage möglichst ohne Störungen im Produktionsbetrieb zu ersetzen.
Die gesamte Tubenlinie inklusive der vor- und nachgeschalteten Automatisierungslösungen sollte so konstruiert werden, dass sie in das bestehende Produktionsgebäude passt – eine besondere Herausforderung. Die Tubenlinie konnte nicht wie generell üblich in einer Reihe mit hintereinander liegenden Maschinen angelegt, sondern musste aufgrund des limitierten Stellplatzes in U-Form aufgestellt werden. Das Anlegen der technischen Konstruktion war selbst für die Produktingenieure der IWK eine komplexe Aufgabe, die am Ende aufgrund langjähriger Erfahrung und dank der guten Zusammenarbeit des Projektteams Weleda-IWK gelöst wurde.
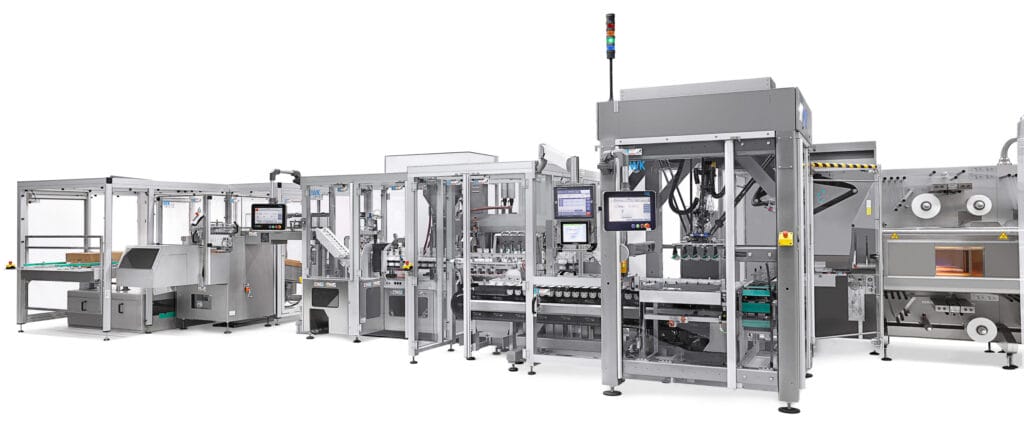
Die neu installierte Füll- und Verpackungslinie IWK FP 64-2 ist flexibel für sich ändernde Formate und Produktvolumina ausgelegt. (Bild: IWK)
Das Herzstück der technischen Lösung ist eine flexible Tubenlinie IWK FP 64-2 mit zwei Füllköpfen und einer maximalen Abfüllleistung von 220 Tuben pro Minute bei höchster Prozesssicherheit. Die moderne Steuerungs- und Antriebstechnik mit energieeffizienten Servoantrieben ermöglicht eine automatisierte Höhenverstellung der 64 Tubenhalter, eine exakte Positionierung und einen sicheren Transport der Tuben in den Arbeitsstationen sowie schnelle und einfache Formatumstellungen.
Weleda verarbeitet hier sensible Kosmetikprodukte. Daher ist der Abfüllbereich nach den GMP-Richtlinien (Good Manufacturing Practice) mit glatten Oberflächen ausgelegt, durchgängig gut zu reinigen und exzellent von allen Seiten zugänglich. Auf dem beauftragten System werden von Weleda auf die benötigten Volumina angepasste Dosierzylinder zur Abfüllung in unterschiedliche Tubenmaterialien und Tubenformen eingesetzt. Generell kann das IWK FP-System dieser Baureihe Füllmengen von 1,5 bis 350 Milliliter sicher verarbeiten.
Automatisierung auf ganzer Linie
Dem Tubenfüllsystem vorgeschaltet sind Cobot-gestützte Module. Die Besonderheit liegt in der Flexibilität bezüglich der Primärverpackung. Sowohl konische als auch zylindrische Tuben können ohne lange Umstellzeiten verarbeitet werden. Die Leertubenkartons bringt ein Depalettierungs-Cobot DPC mit zwei Palettenplätzen kontinuierlich in die Tubenzuführungen ein. Die geleerten Kartons zerlegt anschließend eine Tray-Demontage TDC sehr platzsparend. Die Steuerung der Tubenzuführung (DPC, TZC und TDC) erfolgt zentral.
Das FP-Tubenfüllsystem ist mit einem Pharmacode-Scanner und einem Druckmarkensensor zur Bildausrichtung ausgestattet. Die Leertuben werden in die Tubenhalter verbracht, ausgerichtet und befüllt. Das Verschließen der Tuben erfolgt anschließend entweder mit Falzwerkzeugen für Metalltuben oder mittels Hot-Air-Einheit für die Kunststoffvarianten. Die verschlossenen Tuben werden mittels Prägung oder Laser im Falz gekennzeichnet und können anschließend etikettiert werden.
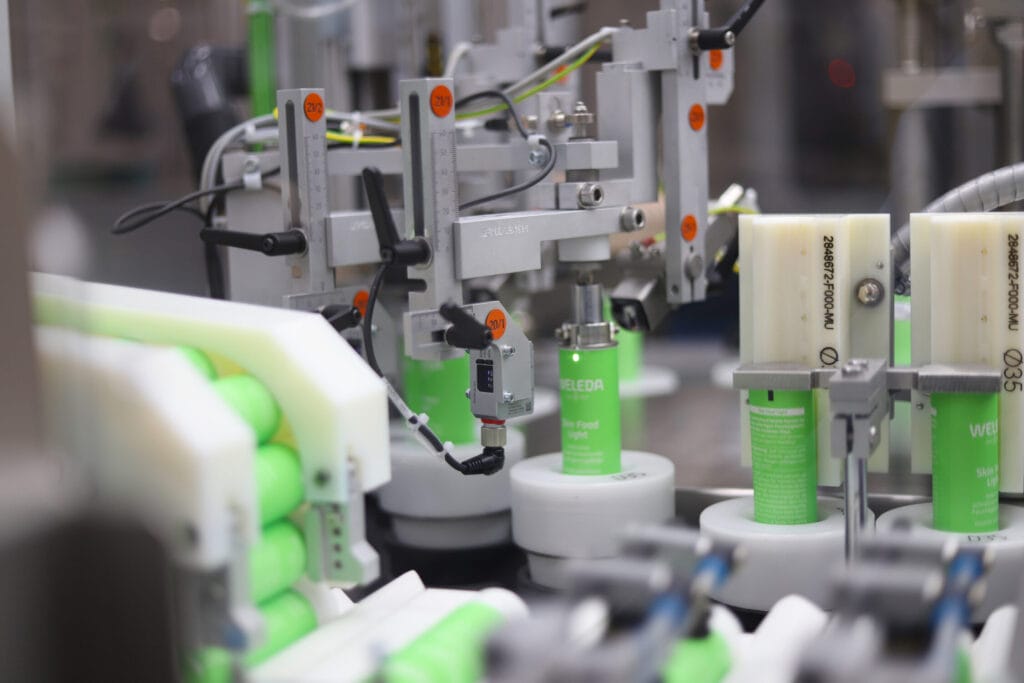
Positionieren der Leertuben in den Tubenhalten im Füllbereich der Linie IWK FP 64-2. (Bild: IWK)
Dem Füllbereich nachgelagert ist eine In-Line-Verwiegung mit 100-Prozent-Gewichtskontrolle inklusive Tendenzsteuerung. Sie bietet ausreichend Platz für kundenspezifische Anforderungen. Anschließend legt ein Pick-&-Place-Arm die sogenannten Gut-Tuben in die Formbecher des linearen Transportsystems XTS. Die individuell angetriebenen Transportwagen dieses Sammelsystems sorgen für einen Leerstellenausgleich vom Tubenfüllen und damit für einen konstanten Produktfluss zur angeschlossenen Roboterzelle IWK FeedCell. Damit garantiert der Maschinenbauer immer volle Packeinheiten.
Die für unterschiedliche Produktkonfigurationen flexible FeedCell führt die Tuben wahlweise zu dem Horizontalkartonierer IWK SC 4 HS zum Verpacken einzelner Tuben in Faltschachteln zu oder legt sie in bereitgestellte Minitrays ein. Diese werden aus einem flachen Zuschnitt automatisch aufgerichtet, beladen und verschlossen. Besonderes Augenmerk lag hier auf dem sicheren Transportweg der Faltschachteln oder Minitrays zur fertigen Verkaufseinheit in 5er-, 6er- oder 8er-Bündel.
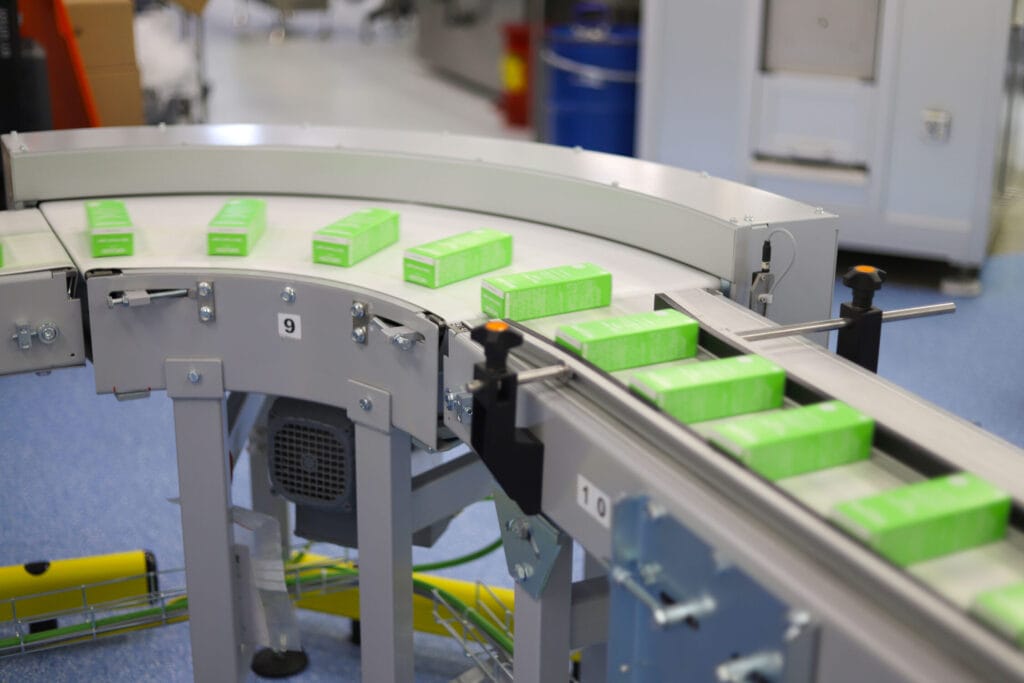
Gefüllte Faltschachteln auf dem Weg zum Bündeln in Versandeinheiten. (Bild: IWK)
Sicher kartoniert, gebündelt und verpackt
Ein von IWK patentiertes Zykloidensystem mit Gegensaugern gewährleistet ein prozesssicheres Aufrichten der Faltschachtel. Zusammen mit je einem gefalzten Beipackzettel werden die Tuben kontinuierlich eingeschoben. Die Schachteln werden verschlossen, wahlweise mit einer Prägung oder einem Laser mit variablen Daten versehen und anschließend mit Folie gebündelt und in ein automatisch aufgerichtetes Versandtray verpackt. Die Minitrays erreichen die Versandtrays ohne Folierung. Eine am Ende der Linie (EOL) platzierte Palettieranlage verbringt dann die einzelnen Versandtrays gemäß vorgegebenem Schema auf eine Palette, die jeweils noch mit einem Etikett versehen wird.
„Das Projekt war für unseren Produktionsbereich ein absolutes Novum. Der Auftragswert, die Teamgröße und Anzahl der Maschinen in einer Linie haben wir bisher so noch nie durchgeführt. Alle beteiligten Mitarbeiter waren entsprechend motiviert, diese Investition und Innovation zu begleiten.“
Paola Nell, Weleda-Teamleiterin Industrial Engineering
Die Beauftragung der Turnkey-Linie für Naturkosmetik erfolgte bereits vor der Corona-Pandemie. Was zu diesem Zeitpunkt niemand ahnen konnte, waren die unvorhersehbaren Projektsicherstellungsmaßnahmen bedingt durch die Pandemie in der kommenden Zeit. Es zeigte sich jedoch, dass die Verantwortlichen seitens Weleda und IWK im gemeinsamen Projektmanagementteam einen ausgezeichneten Draht zueinander hatten und sehr gut miteinander kommunizierten. Trotz der widrigen Umstände ermöglichte IWK eine zweiwöchige Qualifizierung für Produktion und Technik vor Ort in Stutensee. Diese war notwendig, da Weleda sehr hohe Ansprüche an die Dokumentation stellte. Der Aufwand war vergleichbar mit jenem im Pharmabereich. „Auch hier hat IWK all unsere Wünsche erfüllt und eine umfassende Dokumentation in Topqualität geliefert“, sagt Paola Nell.
Doch nicht alleine die Pandemiewidrigkeiten inklusive eines Lockdowns während der Inbetriebnahme machten dem Team zu schaffen. Während der Laufzeit des Projekts gab es mehrere Packmitteländerungen bei den Primär- und Tertiärpackmitteln und außerdem zum Produktionsstart eine Verlagerung zweier Tubenformate von extern zu Weleda ins Haus. „Dank der Kompetenz und Erfahrung der IWK und der Motivation der Monteure, mit Maske drei Wochen am Stück stundenlang an den Maschinen zu arbeiten, wurde das Projekt ein voller Erfolg. Auch nach der Abnahme war IWK stets zur Stelle und hat uns weiterhin unterstützt, via Telefon, Mail oder kurzfristigen Vor-Ort-Einsätzen. Wenn doch alle Projekte so gut laufen würden“, fasst Paola Nell rückblicked zusammen.
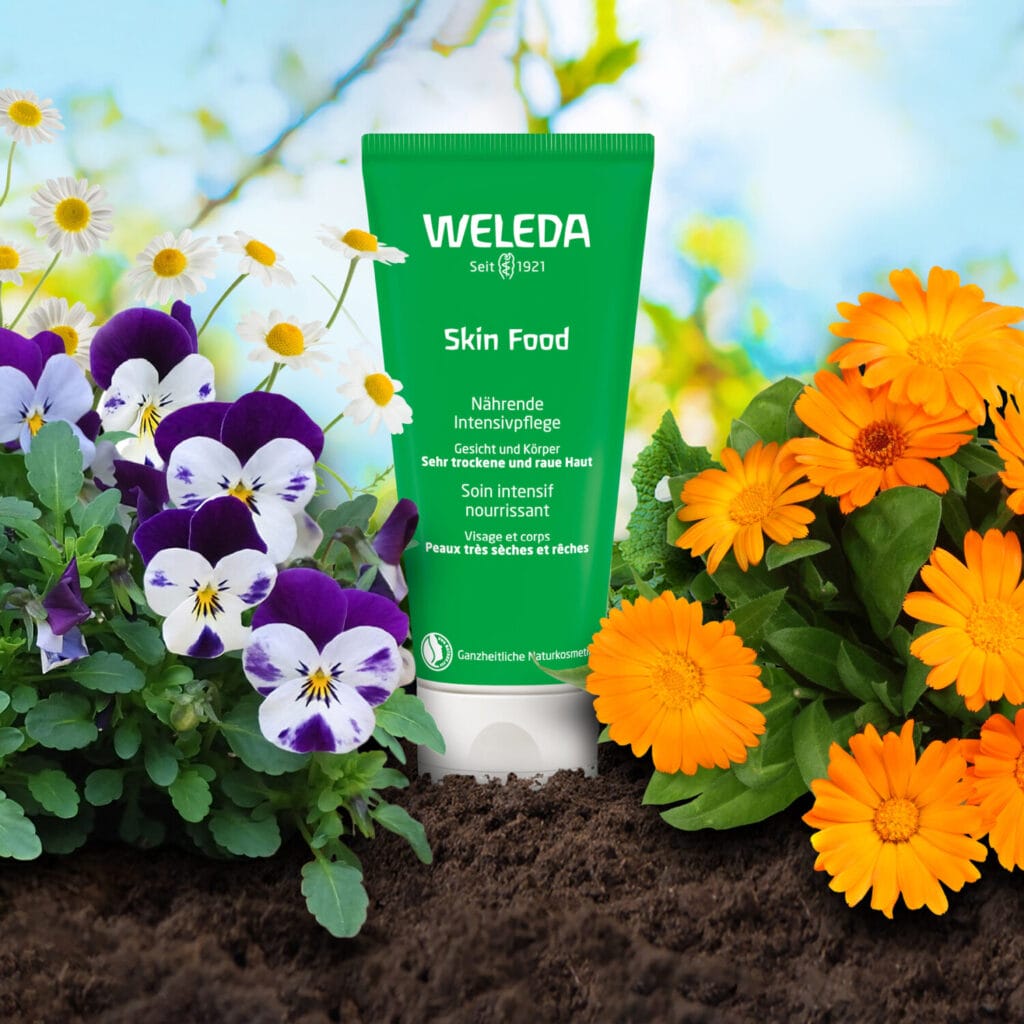
Die Tube der Naturkosmetik-Serie „Skin-Food“ von Weleda wird auf der IWK-Linie befüllt und in die Faltschachtel verpackt.
(Bild: Weleda)
Logistische Meisterleistung
Nach der erfolgreichen Schulung der Weleda-Mitarbeiter und der Werksabnahme (FAT) in Stutensee standen die Demontage und der Transport mit acht Vierzig-Tonner-Lkw nach Schwäbisch Gmünd an. Die Reihenfolge der zu transportierenden Maschinen war entscheidend, damit die Installation vor Ort aufgrund des begrenzten Raums erfolgreich verlaufen würde. Insbesondere in dieser Phase des Kundenprojekts kamen weitere Dienstleister hinzu, die genau instruiert werden mussten. Aufgrund der großen Erfahrung und der zahlreichen abgewickelten Projekte wussten die Verantwortlichen bei IWK genau, was bei der Planung, dem Transport und dem exakten Einbringen der Weleda-Verpackungslinie in die Räumlichkeiten beim Kunden zu beachten war. „Gemeinsam mit dem Speditionsunternehmen haben wir bei Weleda die exakten Positionen der einzelnen Maschinenstellplätze vermessen und bestimmt. Das war Millimeterarbeit. Dabei möchte ich besonders das kompetente Projektmanagement der IWK hervorheben, das derartige Großprojekte mit unterschiedlichen Lieferanten bestens koordiniert“, hebt Barbara Otrzonsek, Gebietsverkaufsleiterin bei IWK, hervor.
Zwei Jahre nach Inbetriebnahme läuft die IWK-Verpackungslinie in einem stabilen Zustand und produziert täglich etwa 80.000 Einheiten der weltweit sehr erfolgreichen Skin-Food-Serie. Die Projektverantwortlichen bei Weleda sind zufrieden und freuen sich über die Performance, auch wenn es aufgrund der Komplexität mit insgesamt sieben Formaten immer wieder gilt, Herausforderungen zu bewältigen. Ein internes Projekt zur kontinuierlichen Verbesserung (KVP) bei Weleda begleitet und fördert weiterhin die Erfolgsgeschichte der Linie.