Im niederländischen Broek op Langedijk produziert PepsiCo Kartoffelchips. Beim Transport werden die fragilen Produkte als Sekundärverpackung in Kartons verpackt und gestapelt. Ein neues System, das auf Paletten gestapelte Kartons zuverlässig gegen Verrutschen sichert, sollte die Kosten für Klebstoff und die Kundenreklamationen reduzieren. Der Lebensmittelkonzern entschied sich für eine Hot-Melt-Technologie von Nordson.
Seit 1958 werden im niederländischen Broek op Langedijk Kartoffelchips hergestellt. Die Langedijker Bauern wollten so einen weiteren Absatzmarkt für ihre Kartoffeln erschließen. Im Lauf der Jahre entwickelte sich das Werk zur größten Chipsfabrik Europas. Heute gehört die Produktionsstätte zum Getränke- und Lebensmittelkonzern PepsiCo, der in Broek op Langedijk rund 300 Mitarbeiter beschäftigt. In dem Werk werden u. a. die Chips der Marke Lays‘ hergestellt, in Tüten abgefüllt, in Kartons verpackt, auf Europaletten gestapelt und ausgeliefert. Bis zu zwölf bis 14 Lagen Kartons stehen in Abhängigkeit von ihrer Größe aufeinander.
Sicherheit für fragile Produkte
Mit einer sicheren Palettenstabilisierung lässt sich der Einsatz von Kunststofffolie in der Logistik reduzieren. Um zu verhindern, dass die Kartons beim Transport verrutschen, investierte PepsiCo in den Niederlanden in ein neues System. (Bild: Nordson)
„Wir verfügen über drei Palettiersysteme, die die Kartons vollautomatisch für den Transport zusammenstellen und stapeln. Im Allgemeinen verlädt jedes System 50 Paletten pro Stunde. Bei Bedarf können wir die Menge auf 100 Paletten pro Stunde steigern. Das bedeutet, dass bis zu 1.200 unterschiedlich große Kartons pro Stunde verarbeitet können.“
Martijn van Zuydam, Projektleiter und Spark Line Lead Trainer NWE bei PepsiCo
Der Transport der Kartonpaletten erfolgt im Werk vollautomatisch und führt dann per Lkw über Zwischenlager zur Auslieferung beim Großhändler. Weil er sich mitunter ruppig und äußerst holprig gestaltet, müssen die Kartons sicher und vor allen Dingen rutschfest auf der Europalette übereinanderstehen. Außerdem muss es möglich sein, sie einfach zu entstapeln.
PepsiCo sicherte die Kartons für den Transport bislang mit einem Kaltleimsystem. Doch hier hatten sich zunehmend Schwierigkeiten gezeigt. So gab es immer wieder Unklarheiten bei der Handhabung der Anlage und der dazugehörigen Ausstattung. Hinzu kamen hohe Betriebskosten und Schwierigkeiten in der weiteren Lieferkette, wenn beispielsweise bereits gestapelte Paletten umgestapelt werden mussten. Das Kaltleimsystem ermöglicht dies nur innerhalb eines definierten Zeitraums, und Kartons wurden beim späteren Um- und Entstapeln beschädigt.
Vor diesem Hintergrund und mit Blick auf das Ziel des Konzerns, seine Produkte nachhaltig herzustellen, kümmerten sich die Verantwortlichen darum, den Transport der Paletten zu optimieren und in eine neue, zukunftsträchtige Technologie zu investieren. Die Grundlagen für ein Pflichtenheft hatte ein internes Team – bestehend aus Darko Despotovic, Bediener der Palettiersysteme, Manuel Allan, technischer Experte, und Martijn van Zuydam – im Rahmen eines Six-Sigma-Green-Belt-Projekts erarbeitet. Danach musste das neue System zur Kosteneinsparung beim Klebstoffverbrauch, ohne Beeinträchtigung der Palettenstabilität beitragen. Die Klebstoffmenge sollte in Abhängigkeit der Kartonpositionen auf der Palette anpassbar sein. Ebenso wenn bei einer bestimmten Kartonkombination in der Lieferkette immer wieder ein Problem in einer speziellen Palettenlage auftritt. Schließlich sollte die nachhaltige Lösung zur Verringerung des CO2-Fußabdrucks beitragen.
Modulares Schmelzgerät optimiert Transportverpackung
Die Entscheidung fiel auf die Schmelzgeräte-Technologie von Nordson, denn das Unternehmen zählte bereits zu den bevorzugten Lieferanten und bietet seinen Kunden ergänzend zur innovativen und hochpräzisen Applikationstechnik einen umfassenden Support an. Bei PepsiCo wurde pro Palettierer ein ProBlue-Schmelzgerät in Kombination mit dem P4-Druckmanagement installiert. Hinzu kamen die MiniBlue II SureBead Heißklebeapplikatoren, die PureFlow-Schläuche sowie die RediFlex II Halterungen.
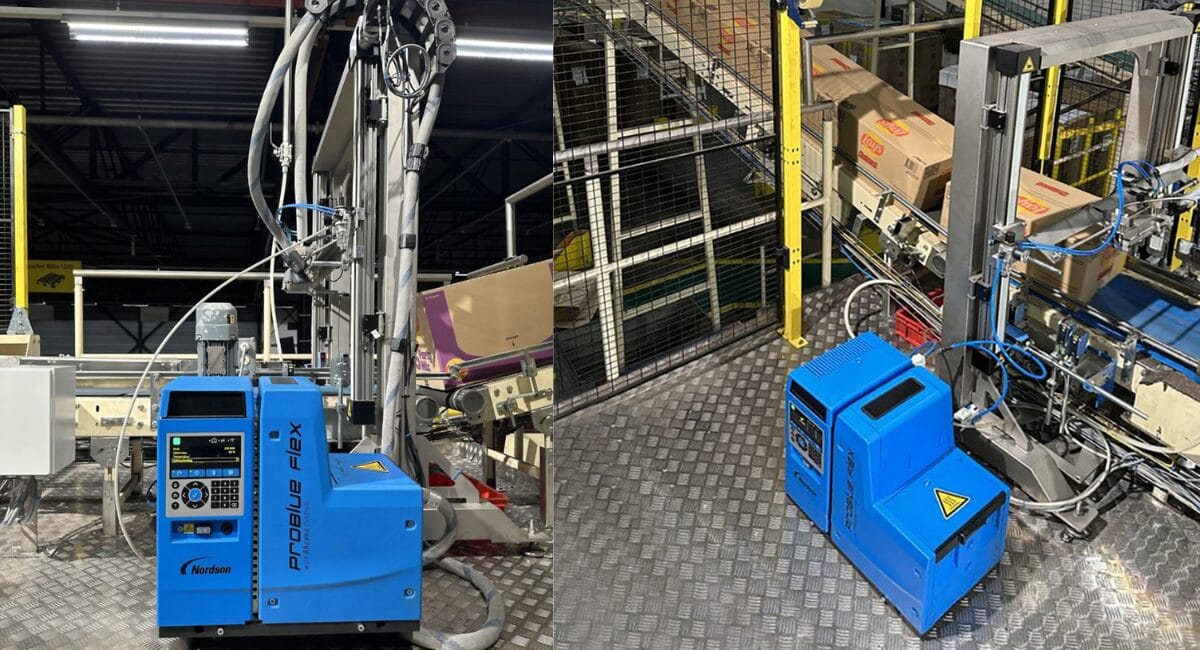
In Kombination mit dem Druckmanagementsystem P4 erlaubt das ProBlue Flex Schmelzgerät die Änderung des elektrischen Steuersignals und der Drücke. So kann die Klebstoffapplikation in Abhängigkeit von der Belastung durch die Kartons programmiert werden. (Bild: Nordson)
„Das ProBlue-Schmelzgerät ist modular aufgebaut, damit es individuell an die Erfordernisse des Anwenders angepasst werden kann“, erläutert Erik van Gulik, OEM & Key Account Manager bei Nordson. Das Gerät zeichnet sich durch eine schnelle Aufheizzeit aus und kann optional mit einem Klebstoff-Tracking-System ausgestattet werden, bei dem Anwender das Volumen und die Applikation des Klebstoffs einfach messen und überwachen können. Das P4-Druckmanagement erlaubt die Änderung des elektrischen Steuersignals und der Drücke sowie die exakte Kontrolle der aufgetragenen Klebstoffmenge. Damit ist es möglich, die Applikation des Klebstoffs in Abhängigkeit von der Belastung durch die Kartons zu programmieren. Das bedeutet, dass bei den unteren Kartons, die durch das Gewicht der darüber gestapelten Kartons stärker belastet sind und sicher stehen, weniger Klebstoff aufgetragen wird als bei den oberen. Letztere können z. B. beim Transport auf der Palette leicht hin- und herschwingen und müssen daher stärker gesichert werden.
Die MiniBlue II SureBead Heißklebeapplikatoren tragen den Klebstoff auch bei hoher Stapelgeschwindigkeit zuverlässig auf und stellen durch ihr präzises Stichmuster die sparsame Verwendung von Klebstoff sicher. PepsiCo verpackt seine Produkte in unterschiedlich großen Kartons, weshalb an jedem Palettierer vier Applikatoren so installiert sind, dass sie unter Berücksichtigung der verschiedenen Kartonmaße den Klebstoff immer an den variierenden Außenkanten auftragen.
Die PureFlow-Schläuche sichern durch den Einsatz einer innovativen Technologie die Qualität des eingesetzten Klebstoffs und verhindern so Materialbeeinträchtigungen wie Aushärten oder Verkoken. Damit tragen sie dazu bei, die Ausfallzeiten zu reduzieren, die durch Schlauchwechsel oder Düsenverstopfung entstehen können. Für den optimalen Durchfluss des Klebstoffs sind sie mit RediFlex II Halterungen verlegt. Im Februar 2023 hat PepsiCo das neue Schmelzgeräte-System in Betrieb genommen.
„Unsere Ziele haben wir damit erreicht und durch den gesenkten Klebstoffverbrauch den CO2-Fußabdruck verringert. Wir sind zwar noch mit der Feinabstimmung beschäftigt, was aber nicht an der Hot-Melt-Technologie liegt, sondern an der Einbindung in das unternehmenseigene Gesamtsystem. Wir gehen davon aus, dass wir allein die Kosten für die Klebstoffe jährlich um rund 40.000 Euro reduzieren können. Wir haben auf jeden Fall die Anzahl der Kundenreklamationen und der Nacharbeiten drastisch verringert. Allein dadurch werden wir voraussichtlich pro Jahr rund 100.000 Euro einsparen.“
Martijn van Zuydam