Der Dortmunder Abfüll- und Verpackungsspezialist KHS GmbH beteiligt sich an zahlreichen Forschungs- und Entwicklungsprojekten zu den Themen digitale Vernetzung und Linienoptimierung. In enger Kooperation mit den Kunden und in Vernetzung und Kooperation mit externen Forschungsinstituten und Universitäten geht es dabei um Ziele wie die Steigerung der Anlageneffizienz oder die Reduzierung von eingesetzten Ressourcen wie Materialien oder Energie.
Aktuell unterstützt KHS beispielsweise das Projekt eines Forschungskonsortiums, bestehend aus Wissenschaftlern der TU Dortmund, der Ruhr-Universität Bochum sowie des Fraunhofer-Instituts für Materialfluss und Logistik (IML), zur additiven Fertigung in der Instandhaltungslogistik. Mittels 3D-Druck sollen komplexe Bauteile hergestellt werden, die mit herkömmlichen Verfahren nicht produziert werden könnten. Auch die Ersatzteillieferung wird mit additiver Fertigung beschleunigt.
Dr.-Ing. Matthias Schopp, Head of Engineering Systems bei KHS (Bild: KHS-Gruppe)
„Übergeordnetes Ziel unserer Forschungsaktivitäten ist es, unsere Anlagen und Maschinen noch energieeffizienter und ressourcenschonender zu gestalten, sodass unsere Kunden auch in Zukunft von den Projekten profitieren“
Dr.-Ing. Matthias Schopp, Head of Engineering Systems bei KHS
Maschine lernt die Flaschenformen selbsttätig
Erst kürzlich wurde wiederum das Forschungsprojekt „DnSPro“ aus dem Bereich „Industrie 4.0“ erfolgreich abgeschlossen. Ziel war die Entwicklung eines Füllsystems, das mit diversen Sensoren und einer intelligenten Steuerung ausgestattet ist. Kern der Entwicklung ist die Optimierung des Abfüllprozesses durch „Machine Learning“. Die Maschine soll sich quasi von selbst auf ein neues Produkt einstellen und sich optimal an die jeweils gefragte Flaschenform anpassen, sodass der Füllprozess schneller und effizienter wird. Bei DnSPro kooperierten fünf Industrieunternehmen mit der Hochschule Ostwestfalen-Lippe und der Ruhr-Universität Bochum.
Neue Impulse für die Steigerung der Anlageneffizienz erhofft sich KHS wiederum vom mit Bundesmitteln geförderten Forschungsprojekt „EnAP“. Bei diesem sollen Energiesparkonzepte und Anlagenoptimierungsverfahren erarbeitet werden, die in pneumatisch und elektrisch betriebenen Handhabungssystemen zum Einsatz kommen. Besonders die Getränkeindustrie soll davon profitieren und ihre Gesamtbetriebskosten senken können.
Assistenzsysteme verhindern Fehlbedienungen
Die Mensch-Maschine-Zusammenarbeit steht wiederum im Mittelpunkt des Projektes „CyProAssist“. Dessen Ziel ist die Entwicklung eines Assistenzsystems für die Produktion, das den Menschen bei der optimalen Anlagenbedienung unterstützt. „Wir wollen den Maschinenbediener dahingehend unterstützen, dass Fehlbedienungen vermieden beziehungsweise Fehlerzustände schnellstmöglich abgestellt werden, um eine hohe Anlagenverfügbarkeit zu ermöglichen“, erläutert Matthias Schopp.
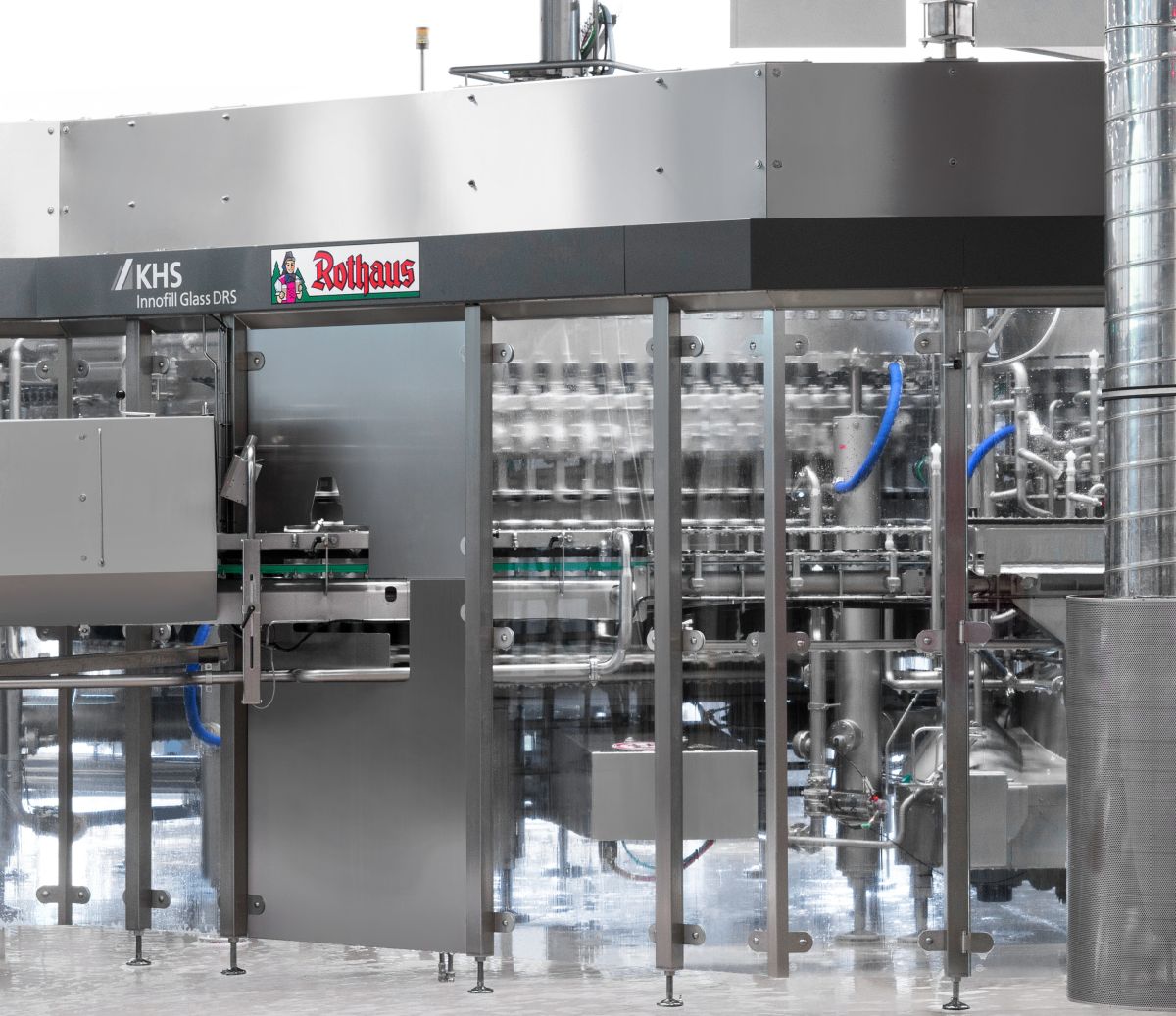
Rothaus setzt auf den Füller KHS Innofill Glass DRS. (Bild: KHS-Gruppe)
Die Erkenntnisse aus vergangenen und aktuellen Forschungsprojektes nutzt KHS auch bei Kundenaufträgen. Der Dortmunder Systemanbieter stattete seinen langjährigen Kunden, die Rothaus-Brauerei, mit einem Glasfüller des Typs „Innofill Glass DRS“ aus und erweiterte ihn um zahlreiche digitale Funktionen. Eine kamerageführte Regelung der Hochdruckeinspritzung erzeugt beispielsweise einen feinen Wasserstrahl, der den Restsauerstoff aus der gefüllten Flasche verdrängt. Dadurch wird die Qualität des Bieres gesichert und die Haltbarkeit verlängert.
Überwacht wird mit der Regelungseinheit auch die Schaumkrone des frisch abgefüllten Gerstensaftes. Auf diese Weise kann Rothaus einerseits den Bierverlust durch übermäßiges Überschäumen reduzieren, gleichzeitig aber auch unzureichend aufgeschäumte Flaschen erkennen und ausschleusen.
Sensoren in jedem Füllventil erkennen Fehler rechtzeitig
Bei ihrer Abfülltechnik profitiert die KHS GmbH außerdem auch vom neu entwickelten Assistenzsystem „DIAS“ (Diagnose-Assistenz). Sensoren in jedem einzelnen Füllventil bieten eine lückenlose Kontrolle und Visualisierung des Füllprozesses. Abweichungen von Sollwerten werden sofort erkannt. Flaschenbruch wird lückenlos erkannt, und beschädigte Flaschen werden automatisch ausgeschleust. Die Sensor-Daten können jederzeit abgerufen und statistische ausgewertet werden. So werden mögliche Fehlerquellen bereits im Vorfeld identifiziert und beseitigt.
Mehr über die KHS GmbH erfahren Sie auf der Homepage http://www.khs.com.