At the K 2022 in September Milliken presented its latest DeltaFlow Viscosity Modifier. The solid concentrate is designed to help polypropylene recyclers by increasing the melt flow rate of rPP for injection molding processes.
This serves to reduce energy use, enhance circularity and advance our goal of creating a healthier future. The newly developed DeltaFlow grades use the latest viscosity-modification chemistry. The technology also has lower volatile organic compounds (VOCs) and improved organoleptics and could nicely complement the advances being made in recycling machinery, according to Allan Randall, Global Product Line Manager. As communicated earlier this year, as an additional sign of our commitment to the recycling industry, Milliken is further expanding production capacity in the German manufacturing plant by 60 percent.
Recycled polypropylene – encompassing recyclers, compounders, converters, and brand owners – is the key target market for this product. DeltaFlow-optimized resins allow for lower processing temperatures, which can enable converters to significantly reduce processing temperatures, reduce energy use, boost productivity and improve processability. Brand owners stand to benefit, as well. DeltaFlow enables rPP to feasibly replace virgin resin in many end-use applications. This allows brands to use more rPP in their products, thereby helping them to meet their sustainability goals.
“Demand in the market for recycled content is only increasing. These products enhance the properties of rPP and make it more suitable for more applications, thereby helping to close the loop in more end uses. Our goal is to enable more and better utilization of rPP. This product line helps to deliver on that promise.”
Allan Randall
Source: Milliken
More packaging news
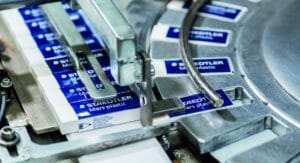
A contract with a handshake is valid
Managing director Tina Gerfer of Wilhelm Rasch Spezielmaschinenfabrik has modernized the company and successfully guided it through difficult times.
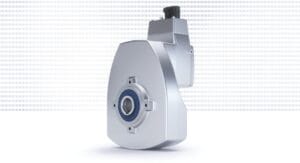
Asynchronous servo solutions for the packaging industry
From primary packaging to final packaging, electric drives play an important role. With a broad portfolio, Nord Drivesystems supports customers.
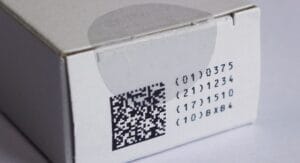
Label Durability
Labels offer many functions which can get lost due to label removal. PTS assesses labels and cardboard for durability and tamper evidence.
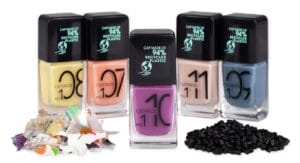
More design for recycling for cosmetics packaging
Packaging for decorative cosmetics is very special. The Forum Rezyklat calls for the recyclability of packaging to be taken into account when designing it.
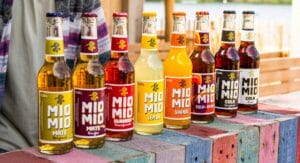
Innovation Barometer 2024
According to a survey conducted by Aktionsforum Glasverpackung 2024 is set to be a highly innovative year for glass packaging.
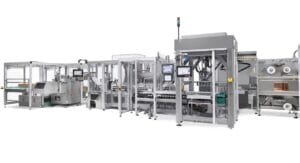
Flexible packaging system for natural cosmetics
Sustainability is part of Weleda’s identity. IWK is also contributing to this with its new flexible packaging line for many natural cosmetic products.