Null Fehler sind das Ziel in jedem Unternehmen. Doch jeder weiß, dass dieses Ziel nicht immer erreicht wird. Im Sondermaschinenbau sind Ersatzteile oftmals ein Punkt mit Verbesserungspotenzial. Optima hat sich dieses Themas angenommen und eine spezifische ERP-Lösung entwickelt. Daraus erwächst nun ein Wettbewerbsvorteil.
Sinn und Zweck des Sondermaschinenbaus ist es, die individuell passendsten Lösungen bieten zu können. Die Weiterentwicklung und Optimierung dieser Maschinentypen sind somit über deren Lebenszyklus hinweg nie vollständig abgeschlossen – sei es aufgrund von Anregungen oder Änderungswünschen der Anwender oder wegen intern initiierter Verbesserungen.
Änderungen sind im Sondermaschinenbau also an der Tagesordnung: Davon betroffen sind Elektronik, Mechanik und Software. Was Kunden einerseits maßgeschneiderte Anwendungslösungen und den technisch neuesten Stand sichert, birgt andererseits Fehlerpotenzial. Dies kann sich bei zukünftigen Reparaturen und Lieferungen von Verschleißteilen negativ auswirken – eine Problematik, die im Sondermaschinenbau häufig auftritt. Doch wie kann man diese Situation verändern? Speziell dafür hat Optima den Change-Management-Prozess entwickelt und eingeführt.
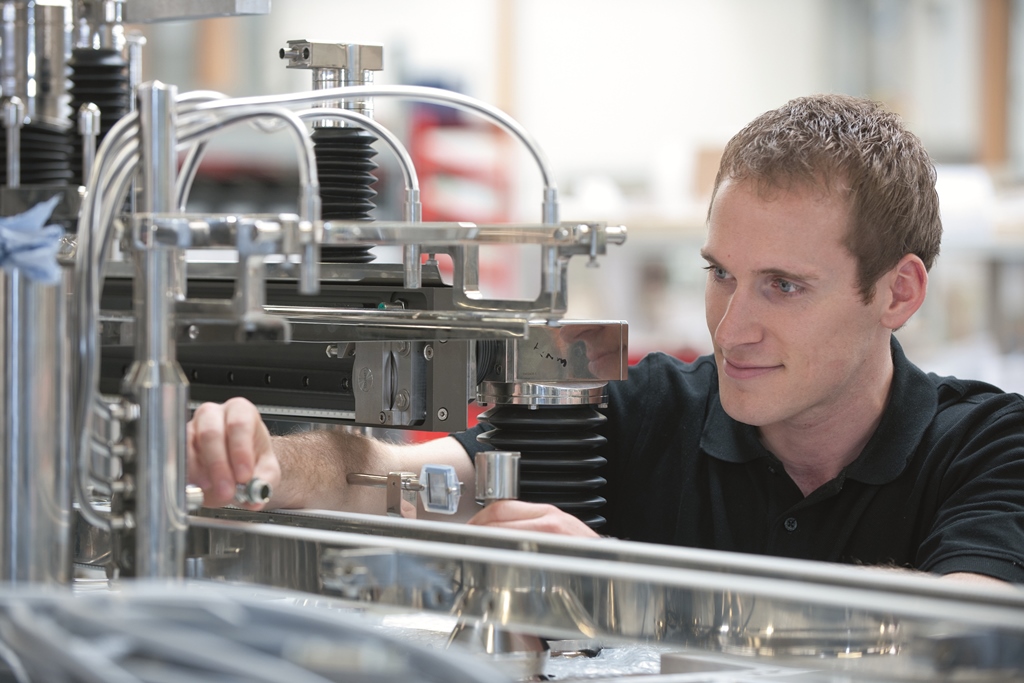
Kein Nacharbeiten: Sämtliche Ersatzteile passen zu den Kundenmaschinen in ihrer aktuellen Version.
Geplant: eine automatisierte Lösung
Konstruktive Änderungen beim Verpackungsmaschinenbauer schlagen sich zunächst im CAD nieder. Tatsächlich besteht jedoch eine enge Verbindung zum ERP-System. Alle Änderungen müssten in logischer Konsequenz ERP-Prozesse auslösen. Da diese komplex sind, kann nur eine automatisierte Lösung sicherstellen, dass beim Besteller am Ende fehlerfreie Teilelieferungen eingehen. Um dieses Ziel zu erreichen, bildete Optima im Juni 2014 eine zentrale Projektgruppe, die sich ausschließlich mit dieser „Change“-Aufgabenstellung befasst.
Ein Eingriff in ein laufendes ERP-System ist heikel. Und bei einem tief greifenden Eingriff, wie er hier anzusetzen war, handelt es sich gewissermaßen um eine Operation am offenen Herzen. Erfahrungen seitens anderer Unternehmen und externer Berater waren und sind nicht vorhanden. Zudem müssen die veränderten organisatorischen Abläufe global in Kraft treten und geschult werden, damit sie greifen können. Allein in den ersten fünf Monaten nach der Einführung wurden bei Optima weltweit nicht weniger als 10.000 Fälle nach dem neuen System bearbeitet. Die bisher eingeleiteten Änderungen betreffen aktuelle Projekte, die sich im Bau, in der Installation oder in Betrieb befinden.
Geschafft: die Umsetzung
Im März 2015 erfolgte der Rollout der neuen Funktionalität des eingesetzten ERP-Systems. Heute existiert in der gesamten Optima-Unternehmensgruppe ein elektronisch gesteuerter Workflow, der mit einem Antrag auf Änderung im System beginnt und einen maximalen Entscheidungszeitraum für den Änderungsantrag vorgibt. Wird die Änderung angenommen, hat dies Auswirkungen auf Zeichnungsdokumente, Stücklisten, Projektdokumentation und weitere Dokumente mehr. In der ERP-Software sind alle Abläufe und Entscheidungsszenarien exakt abgebildet und zwingend vorgegeben. Gleichzeitig besteht intern Transparenz, wer personell in den Ablauf eingebunden ist.
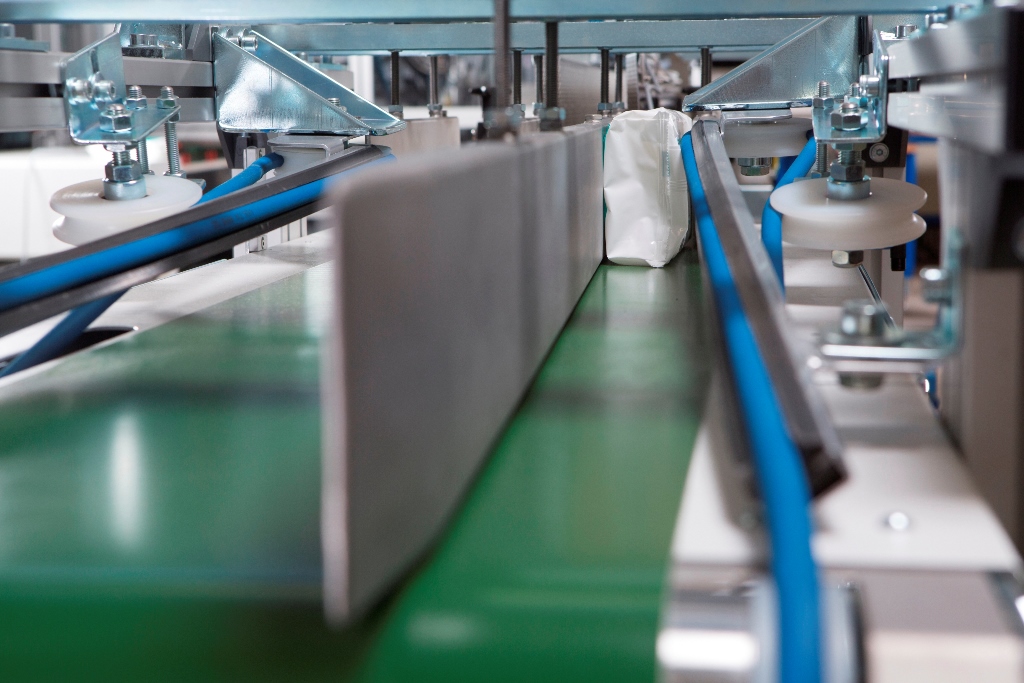
Passgenau wurde ein Upgrade-Kit in eine Maschine von Optima Nonwovens installiert.
Audit: die Anerkennung
Positives Feedback seitens der Kunden gibt es inzwischen. Optima wird, wie heute vielfach üblich, von potenziellen Auftraggebern in Audits bewertet. Die installierte ERP-Lösung ist dabei immer ein großes Plus. Derzeit ist sie die einzig bekannte Lösung am Markt, die dem Betreiber Sicherheit in diesem Umfang gewährleistet.
Maschinendokumentationen befinden sich immer auf dem aktuell korrekten Stand („as delivered“ oder „as maintained“), Teilelieferungen (Module, Ersatz- oder Verschleißteile) passen immer zur kundenspezifischen Version einer Anlage, vereinfachte Abläufe mit Zeit- und Kostenvorteilen. In vielen Verpackungsmaschinen kommen Kamerasysteme zu Kontrollzwecken zum Einsatz. Ein Unternehmen arbeitet bereits mit einem bevorzugten Hersteller zusammen, der bei Optima bisher jedoch noch nicht zum Einsatz kam. Er wünscht diesen bevorzugten Hersteller in seiner neuen Optima-Maschine. Eine andere Situation könnte sein, dass ein Kamerahersteller, der bisher technologisch führend war, von einem anderen Hersteller abgelöst wurde. Optima entscheidet sich, in Zukunft der verbesserten Technologie den Vorzug zu geben. In beiden Fällen hat diese Änderung Auswirkungen auf Software, Hardware, Mechanik und Geometrien. Systematisch werden durch das Change-Management alle erforderlichen Änderungen in den Dokumenten synchronisiert. Dies gewährleistet die größtmögliche Sicherheit für den gesamten Lebenszyklus einer Anlage.Praxisbeispiel: Kamerasystem