Sind bei der Herstellung von Lebensmitteldosen noch Materialeinsparungen möglich? Neueste Untersuchungsergebnisse eines Gemeinschaftsprojekts zeigen, dass das Potenzial für eine weitere Dickenreduzierung bei der Herstellung dreiteiliger Dosen wohl längst noch nicht ausgeschöpft ist.
Innerhalb des letzten Jahrzehnts schien die Abnahme der Ausgangsmaterialstärke für die Herstellung von Lebensmitteldosen aufgrund von Verschließproblemen ein gewisses Ende erreicht zu haben. Meist setzte die Faltenbildung bei der Verarbeitung von dünneren und höherfesten Materialien die Grenze des Verfahrens. Aber ist das tatsächlich so?
Um dies zu untersuchen, hat sich ein branchenübergreifendes Konsortium zusammengeschlossen. Das geförderte Forschungsprojekt wurde mit wissenschaftlicher Begleitung und Koordination durch das Fraunhofer-Institut für Werkzeugmaschinen und Umformtechnik (IWU) realisiert.
❚ Materiallieferanten (thyssenkrupp Rasselstein GmbH, Tata Steel)
❚ Verschließmaschinenhersteller (Cantec GmbH & Co. KG, Lanico Maschinenbau Otto Niemsch GmbH, Gebrüder Leonhardt GmbH & Co. KG Blema Kircheis, Ferrum Ltd. – Canning
Technology)
❚ Werkzeuganbieter (MAIKO Engineering GmbH, Albert Schmutzler GbR)
❚ Dosenhersteller (CAN-PACK S.A., Auxilliar Conservera S.A., International Packaging Association, Glud & Marstrand A/S) sowie
❚ Messsystementwickler (CMC-KUHNKE GmbH, F+K Werkstoffürfung und Labor GmbH)
❚ Compoundlieferanten (Wakol GmbH, Henkel Adhesive Technologies).
Basis der Untersuchung bei Lebensmitteldosen
Die Untersuchung wurde an einer dreiteiligen Lebensmitteldose mit dem Durchmesser 70 Millimeter durchgeführt. Für diese Lebensmitteldosen ist die Materialfestigkeit TH550 in der Dicke von 0,17 Millimetern für die Dosendeckel der industrielle Standard. Im Rahmen des Projekts wurden fünf verschiedene Deckelmaterialien untersucht, so auch Deckelmaterialien mit einer reduzierten Dicke von 0,15 Millimetern mit höherer Festigkeit (im Bereich von 600 N/mm² bis 650 N/mm²) und maximaler Dehnung (zwischen zwei und ca. zehn Prozent).
Alle Dosendeckel wurden unter identischen Bedingungen für Innen- und Außenlackierung sowie mit demselben Compoundsystem auf derselben Anlage und mit denselben Werkzeugen beim Industriepartner CAN-PACK S.A. hergestellt. Die Dosendeckelmaße lagen alle in den erforderlichen Toleranzen.
Im Mittelpunkt der Untersuchung stand das Rollenverschließen, da dies die gebräuchlichste Verschließtechnologie ist. Die Betrachtung der Standard-Industrierolle für die erste Verschließoperation im Falzprozess zeigte die bekannten Schwierigkeiten und Probleme in den industriellen Tests: Je höher die Materialfestigkeit und je geringer die Materialdicke, desto mehr neigen die Materialien bei der Verschließoperation 1 zur Faltenbildung.
Prozessinnovation mit virtuellen Methoden
Im Rahmen des Projekts wurde eine FE-Analyse durchgeführt mit dem Ziel, die wesentlichen Einflüsse und Ursachen für das Faltenbildungsverhalten zu beschreiben. Es konnte festgestellt werden, dass ein wesentlicher Einfluss auf die Anzahl und Größe der Falten im Verhältnis der Materialhärte und der Rollengeometrie liegt.
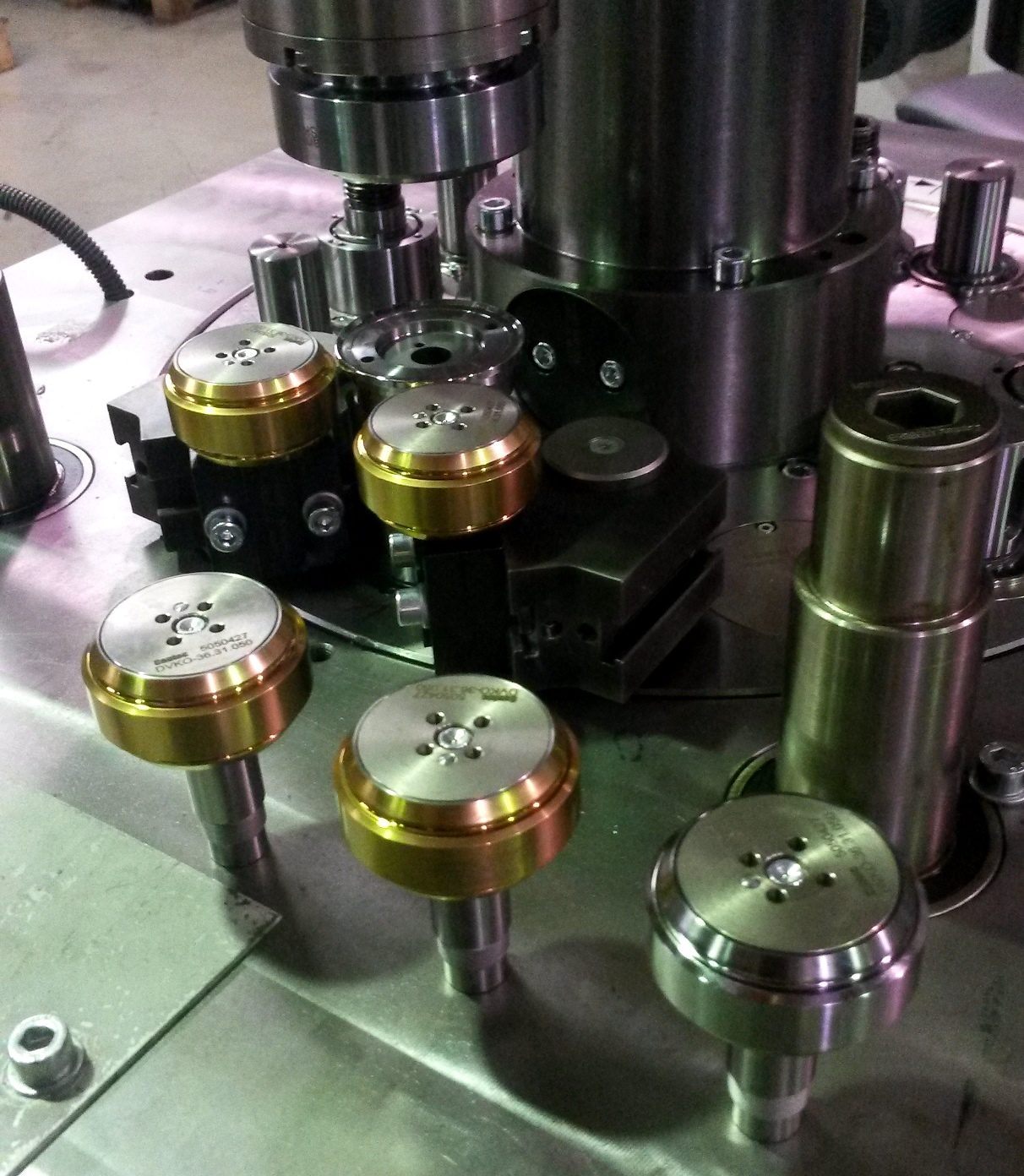
Die Versuchsanlage (Bild: Fraunhofer IWU)
Um die Falten im Rahmen der Prozesssimulation zu minimieren, wurden verschiedene Rollenprofile analysiert. Schließlich wurde ein Rollenprofil optimiert, das zu weniger Faltenbildung beim Falzen aller hochfesten Materialien führte. Dieses optimierte Rollenprofil wurde von den Projektteilnehmern hergestellt und auf verschiedenen Verschließmaschinen dem Praxistest unterzogen.
Industrieversuche bei Projektteilnehmern
Die Industrieversuche wurden von drei Maschinenherstellern (Cantec, Ferrum, Blema) und einem Dosenhersteller (Auxilliar Conservera) im Konsortium durchgeführt. Die verschlossenen Dosen zeigten eine gute Maßhaltigkeit mit den geforderten Maßen und sind hinsichtlich der Faltenbildung analysiert worden.
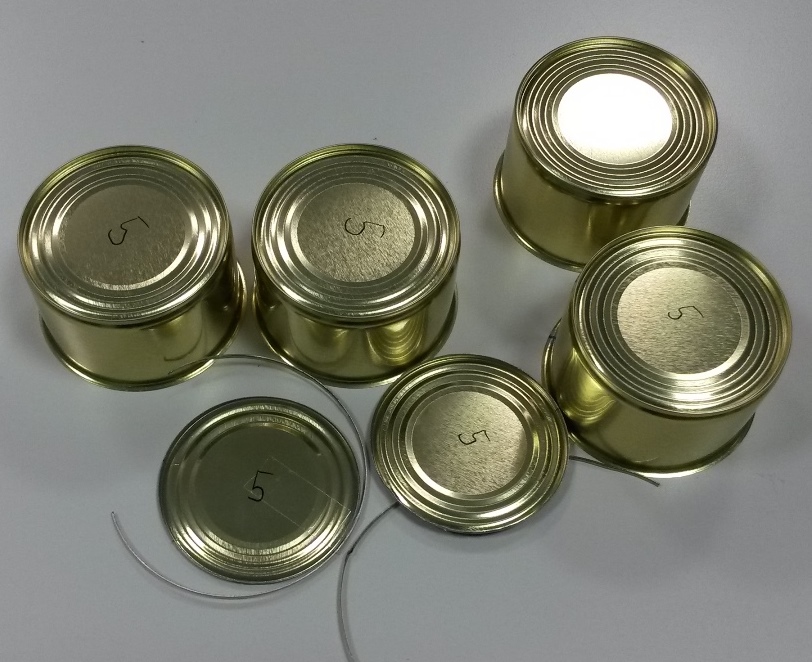
Verschlossene Dosengrößen im Test (Bild: Fraunhofer IWU)
Die gebräuchlichste Art der Prüfung sind die Abstreifmethode und eine anschließende optische Inspektion durch den Maschinenbediener. Hier können subjektive Einschätzungen die Prüfungen beeinflussen, daher wurden im Rahmen des Projekts alle verschlossenen Dosen mit einer neuen röntgenbasierten, zerstörungsfreien Falzmessanlage der Firma CMC-Kuhnke GmbH vermessen. Mit diesem System steht eine objektive Methode zur Messung von Falten innerhalb der Naht zur Verfügung. Alle Industriepartner konnten die Verbesserung des Faltenbildes durch das optimierte Rollenprofil für alle hochfesten Materialien nachweisen.
Funktionsprüfung verdeutlicht das Potenzial
In anschließenden Untersuchungen wurden die verschlossenen Dosen mit allen Versuchsmaterialien einem Beultest unterzogen, dabei konnte ermittelt werden, dass alle höherfesten Materialien zu einer Steigerung des ertragbaren Beuldrucks führen.
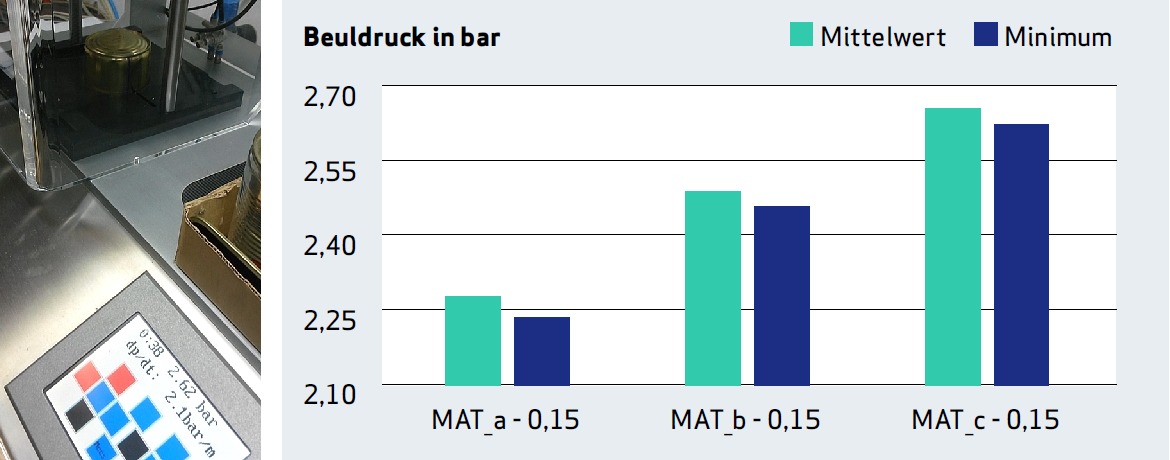
Beultest (Bild links) und ertragbare Beuldrücke (Grafik rechts) beim Standardmaterial (MAT_a) und bei Testmaterialien mit höherer Festigkeit und unterschiedlichen Dehnungen (MAT_b und MAT_c). MAT_c weist hierbei eine höhere Dehnung auf. (Bild: Fraunhofer IWU)
Zudem wurde festgestellt, dass die Materialien mit hoher Festigkeit und hoher Dehnung ein höheres Potenzial für die Dickenreduzierung aufweisen.
Gewichtseinsparung von bis zu vier Gramm pro Lebensmitteldose möglich
Innerhalb des Projekts konnte also der technologische Nachweis für die Senkung des Materialeinsatzes bei gleichbleibender Funktionsanforderung und besserer Prozessstabilität erbracht werden. Die Industrieteilnehmer schätzten, dass mit einem Deckelmaterial der Festigkeit von 650 N/mm² und hohen Dehnungen eine Absenkung der Deckelblechdicke um 0,02 Millimeter bei gleicher Funktion möglich ist.
Die Auswirkung dieser Reduzierung der Deckeldicke um ca. 20 Mikrometer würde an einer Standarddose mit dem Volumen 425 Milliliter zu einer Gewichtseinsparung von vier Gramm pro Dose führen, was bei den im Markt eingesetzten Milliardenstückzahlen zu einer bedeutenden Materialreduzierung auflaufen würde und entsprechende Kostenersparnisse erzielen könnte. Zukünftigen Serienversuchen sollen die Ergebnisse bestätigen.
Der ausführliche Abschlussbericht des Projekts ist bei der Forschungsvereinigung Stahlanwendung e. V. (FOSTA) zu erhalten.
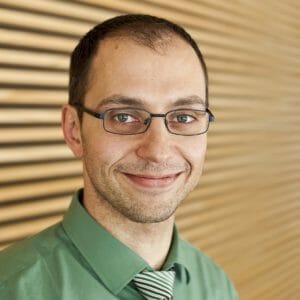
Autor dieses Gastbeitrags ist Dipl.-Ing. Thomas Lieber. Er ist Gruppenleiter im Bereich Blechbearbeitung und Grundlagen am Fraunhofer-Institut für Werkzeugmaschinen und Umformtechnik (IWU) in Chemnitz.