Das Verpacken von Smartphone-„Griffen“, sogenannten PopGrips, war bei iClick ein sehr arbeitsintensiver und monotoner manueller Prozess. Inzwischen setzt der US-Werbemittelhersteller auf die kollaborativen Eigenschaften von Zweiarmrobotern, die die Abläufe erfolgreich automatisieren.
Mit dem PopGrip liegt ein Smartphone viel besser in der Hand. Der kleine runde Griff klebt an der Unterseite und verfügt über einen Schaft, der sich wie ein Balg dehnen lässt. Versierte Vermarkter erkannten schnell das Potenzial als erstklassiges Marketinginstrument.
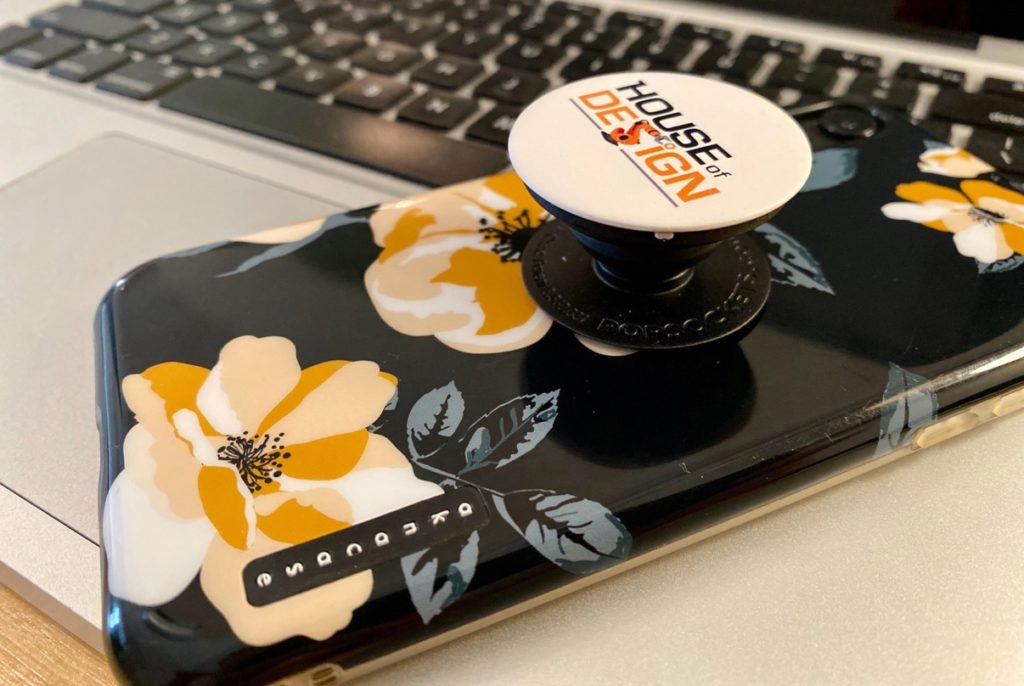
Mit einem PopGrip liegt ein Smartphone perfekt in der Hand. (Bild: iClick)
Die mobile Werbefläche ist so preiswert, dass man sie auf Messen, Veranstaltungen oder über viele andere Kanäle verschenken kann. Dank dieser Dynamik katapultierten sich die PopGrips zum begehrtesten Produkt von iClick, einem in Seattle ansässigen Anbieter von Werbeartikeln.
Endmontage- und Verpackungsprozess
Aufgrund der wachsenden Nachfrage musste eine effiziente Lösung für das Konfektionieren und Verpacken gefunden werden. Dabei wird ein mit dem Logo des jeweiligen Sponsoring-Unternehmens versehener PopGrip auf einer individuell bedruckten Karte positioniert. Diese enthält in der Regel Bedienungsanleitungen und Werbeinhalte und wird anschließend in einen Kunststoffbeutel verpackt.
„Ursprünglich wurden die PopGrips an einer Station manuell in die Karten eingelegt und dann zu einer anderen Station transportiert, um sie dort in eine automatische Verpackungsmaschine einzulegen“, erklärt Steve White, Executive Vice President of Production bei iClick. „Das war ein arbeitsintensiver Prozess, und selbst mit einem Team von vier oder mehr Personen konnten wir die Nachfrage nicht mehr bedienen.“
Um die Kapazität der Verpackungsmaschine zu maximieren, starteten die Verantwortlichen die Suche nach möglichen Automatisierungslösungen. Nach der Prüfung einer Vielzahl von Optionen stand der zweiarmige ABB-Roboter YuMi im Fokus des Interesses.
Besondere Automatisierungslösung
ABB empfahl iClick an House of Design (HoD), einen ABB-Systemintegrator, der für die Entwicklung innovativer Robotersysteme für ungewöhnliche Anwendungen bekannt ist. Die Experten von HoD konzipierten eine Station mit zwei YuMi-Robotern, die synchron miteinander arbeiten und 24 PopGrips pro Minute einsetzen sowie eintüten. „Die kollaborativen Roboter von ABB erwiesen sich als die beste Lösung“, sagt Steve White. „Mit den zwei YuMis konnten wir zwei manuelle Prozesse zu einem nahtlos automatisierten Ablauf kombinieren.“
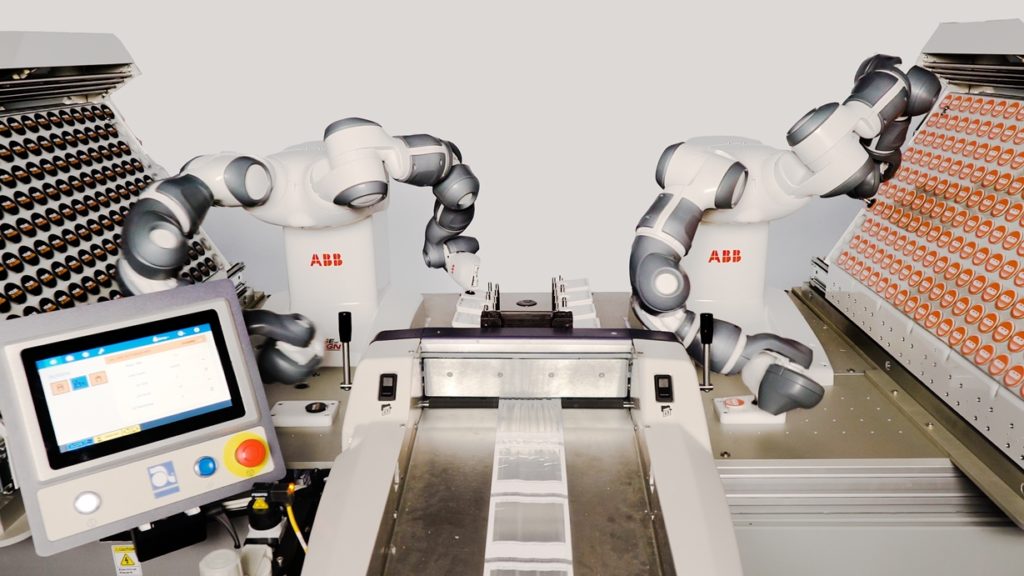
Die beiden YuMi-Roboter sind auf engstem Raum nebeneinander positioniert und erledigen identische Aufgaben. (Bild: iClick)
Die Roboter sind nebeneinander positioniert und erledigen die gleichen Aufgaben. Aufgrund ihrer Nähe sind sämtliche Bewegungen ihrer vier Arme und insgesamt 28 Achsen sorgfältig koordiniert, um die begrenzte Raumkapazität der Station maximal zu nutzen. HoD setzte die Simulationssoftware RobotStudio® von ABB ein, um mit den Bewegungen jedes Roboterarms zu experimentieren und schließlich den optimalen Bewegungsablauf zu programmieren.
„Wir verwenden RobotStudio unter anderem für Studien zur Systemkonfiguration und Roboterreichweite, Code-Tests und Frequenzberechnungen. Das Tool stellt auch ein leistungsstarkes Verkaufswerkzeug dar. Damit lassen sich Simulationen erstellen, die unsere jeweilige Projektvision verdeutlichen. RobotStudio zeigt die Zyklusgeschwindigkeit und den Produktfluss anschaulich auf, sodass der potenzielle Kunde sicher sein kann, dass wir sein Fertigungsproblem tatsächlich lösen können“, betont Brandon Schmidt, Vice President Automation & Robotics bei House of Design.
Optimierte Abläufe beim Verpacken von Popgrips
In der neuen Anlage entnimmt ein YuMi-Arm den PopGrip aus der Ablage und legt ihn auf die Zwischenmontagestation. Der andere Arm entnimmt die Karte aus der Kartenstation vom Stapel und schiebt sie in die Nut zwischen der Unterseite und der Oberseite des PopGrip. Mit der gleichen Bewegung hebt er, während er die Karte immer noch hält, die Einheit aus Karte und PopGrip an und schiebt sie in den Beutel. Anschließend erfolgt die IO-Meldung, um dem Einpacker mitzuteilen, dass sich das Teil im Beutel befindet.
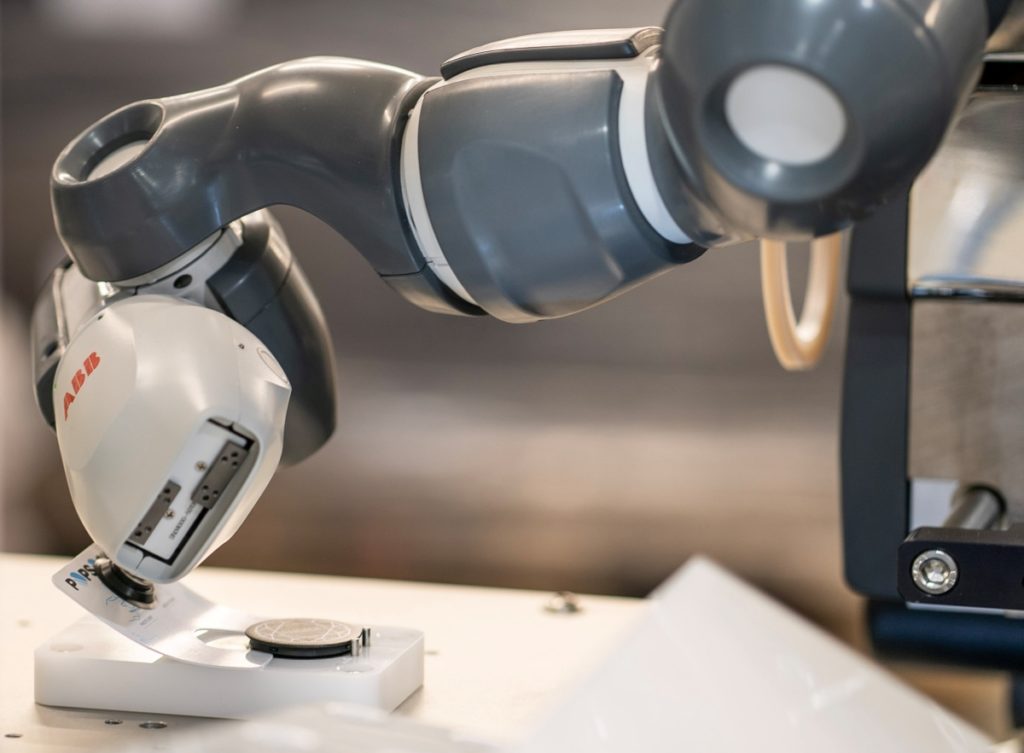
Auf der Zwischenmontagestation wird die Karte eingesteckt. (Bild: iClick)
„Da wir zwei manuelle Tätigkeiten zu einem automatisierten Prozess zusammenführen, erledigt die Station die Arbeit von vier Personen und versorgt das automatische Abpacksystem mit voller Kapazität“, hebt Chad Svedin, Projektmanager bei House of Design, hervor. „Das System kann auch gleichzeitig an verschiedenen Aufträgen arbeiten, wobei das IO auf dem Roboter anzeigt, welches von mehreren dedizierten Förderbändern die eingetüteten PopGrips führt.“
Hohe Sicherheitsstandards
Die kollaborativen Eigenschaften und die menschenähnlichen Dimensionen erlauben es, einen YuMi in unmittelbarer Umgebung seiner menschlichen Kollegen zu platzieren. Bei einer etwaigen Kollision mit einem Mitarbeiter unterbricht er die Bewegung sofort. Sein anschließender Neustart ist so einfach wie einen Fernseher per Fernbedienung anzuschalten. Beim Kontakt mit einem Menschen absorbiert und dämpft das mit weicher, abgerundeter Polsterung überzogene Magnesiumskelett von YuMi den Aufprall.
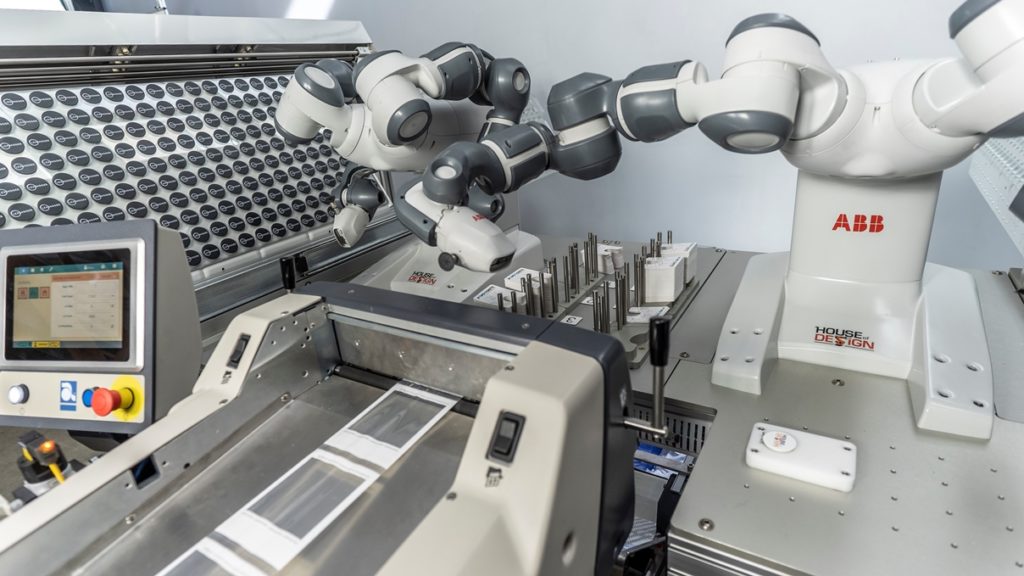
Alle Bewegungen der vier Roboterarme mit insgesamt 28 Achsen werden optimal koordiniert. (Bild: iClick)
Somit entfallen auch Schutzkäfige oder Umhausungen, die normalerweise bei traditionellen Industrierobotern erforderlich sind. Das ist ein wichtiges Kriterium für den Einsatz in der PopGrip-Produktion. „Die Möglichkeit einer offen gestalteten Produktionshalle erleichtert es unseren Bedienern, sich der Station zu nähern, Kartenfächer aufzufüllen, Ausschuss zu ziehen oder weitere notwendige Tätigkeiten auszuführen, ohne den Arbeitsfluss zu unterbrechen“, so Steve White.