Stichwort Reshoring: Die Margen bei der Verarbeitung pharmazeutischer Pulver sind niedrig und die Produktionsbedingungen komplex. Das hat zu einer Verlagerung der Produktion in kostengünstigere Märkte geführt. Wie lassen sich vor diesem Hintergrund Lieferengpässe, wie sie immer wieder aufgetreten sind, vermeiden? Und wie kann die lokale Produktion erneut angekurbelt werden?
Pharmazeutische Pulver bilden die Basis für zahlreiche Antibiotika, die für eine umfassende medizinische Versorgung unerlässlich sind. Antibiotika wie Cephalosporine oder Penicillin sind bei häufig auftretenden Krankheitsbildern wie Lungen- oder Mandelentzündungen ein bewährter Therapieansatz. Um den Magen-Darm-Trakt zu umgehen und die Wirkung des Medikaments zu steigern, erhalten Patienten häufig Infusionen auf Basis pulverförmiger Antibiotika. Erst kurz vor der Verabreichung entsteht durch Zugabe von reinstem Wasser die Infusionsflüssigkeit.
Gerade diese Pulverform macht den Herstellungsprozess höchst komplex: Beim Abfüllprozess hantieren die Bediener mit Pulvern, die leicht stauben. Um sicherzustellen, dass es nicht zu Kreuzkontaminationen kommt, muss auf strikte Trennung unterschiedlicher Wirkstoffe und Chargen geachtet werden. Zudem dürfen die Bediener der Anlage auf keinen Fall mit den teils toxischen Substanzen in Berührung kommen.
Abfüllung pulverförmiger Antibiotika
Vor allem bei der Abfüllung von Penicillin sind die Vorgaben besonders streng: Laut US-amerikanischer FDA etwa sind Hersteller dazu verpflichtet, Anlagen und Equipment, in denen das Antibiotikum abgefüllt wird, zu isolieren, auf separate Luftzufuhr und -filtration zu achten und regelmäßige Tests auf Rückstände des Medikaments durchzuführen.
Oft sind sogar getrennte Fabrikhallen nötig, um die Einhaltung dieser Vorgaben zu gewährleisten. In diesem Fall müssen die Hersteller separate Büroräume und Kantinen für die verschiedenen Schichten schaffen, um die Sicherheit ihrer Mitarbeiterinnen und Mitarbeiter zu gewährleisten. Dies bedingt einen enormen finanziellen Aufwand.
Unausgewogene Verteilung der Produktion
Viele Antibiotikahersteller wollten oder konnten sich in der Vergangenheit auf derartige Investitionskosten nicht mehr einlassen. So setzte laut einer Studie zur Versorgungssicherheit mit Antibiotika von Pro Generika (durchgeführt von Roland Berger 2018) bereits vor Jahrzehnten eine Abwanderung globaler Produktionskapazitäten nach Asien ein. In den 1980er-Jahren begann man etwa in China damit, die heimische Antibiotikaproduktion zu subventionieren. Bald traten Skaleneffekte auf, die es Herstellern ermöglichten, große Mengen von Antibiotika zu niedrigen Preisen zu produzieren.
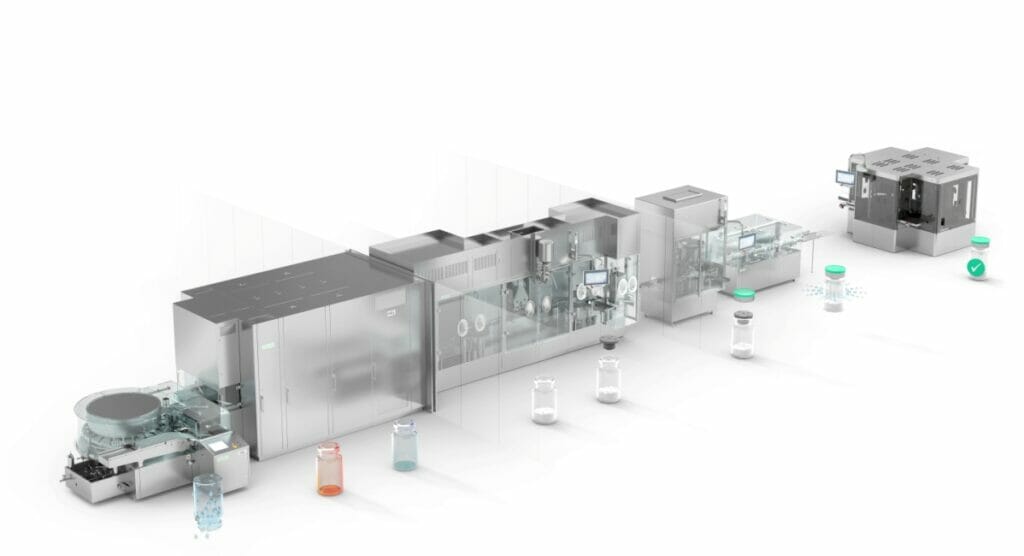
Die Investitionen für komplette Produktions- und Abfüllanlagen sind immens hoch. (Bild: Syntegon Technology)
Zeitgleich wurde die Herstellung von Generika in der westlichen Welt kostenintensiver. Zunehmend anspruchsvollere Audits etwa entwickelten sich zu einem immer größeren Kostenfaktor. Auslaufende Patente westlicher Hersteller erhöhten zudem die Nachfrage am Markt für ökonomisch tragbare Produktionskapazitäten. Viele Hersteller fanden diese in China und Indien.
Österreich zeigt, wie es geht
Die Coronapandemie hat deutlich vor Augen geführt, dass derartige regionale Abhängigkeiten zumindest problematisch sind: Bei Lieferengpässen müssen Ärzte häufiger anstelle spezifisch wirkender Arzneimittel etwa Breitbandantibiotika einsetzen, die die Wahrscheinlichkeit einer Resistenzbildung erhöhen. Um dieser Entwicklung entgegenzusteuern und eine stabilere Verfügbarkeit auf dem Markt zu gewährleisten, fordern Antibiotikahersteller, Ärzte- und Apothekerverbände und nicht zuletzt die Politik, die Produktionskapazitäten wieder globaler zu verteilen.
Wie das gelingen kann, ist in Österreich zu beobachten: Dort unterstützt die Regierung mit der Generika-Division Sandoz von Novartis in Kundl den einzigen Standort in Westeuropa, der Antibiotika sowohl herstellt als auch abfüllt, mit weitreichenden Investitionen. Für das neueste Projekt sind es öffentliche Mittel in Höhe von 50 Millionen Euro. Das gesamte geplante Investitionsvolumens beläuft sich sogar auf über 150 Millionen Euro.
(Bild: Syntegon Technology)
„Gerade die Coronapandemie hat verstärkt gezeigt, wie abhängig die globale Versorgung von einzelnen Regionen ist – und könnte jetzt als eine Art ‚Wachrüttler‘ dienen, um entsprechende Initiativen zu beschleunigen.“ Markus Heinz, Produktmanager Vial Liquid & Powder, Syntegon Technology
Wirklich absehbar ist es zum jetzigen Zeitpunkt noch nicht, ob weitere Länder dem Beispiel Österreichs folgen werden. Doch es besteht Hoffnung: Einige national initiierte Projekte, beispielsweise in Indien, den USA oder Italien, zur Förderung der lokalen Medikamentenherstellung mit öffentlichen Geldern sind bereits angestoßen worden (darunter auch antibiotische Pulver). Wenn hierbei in den Ausbau bereits bestehender Produktionsstätten investiert wird, könnte ein ganz kleiner Teil der Produktion bereits in weniger als drei Jahren relokalisiert werden.
Die Rolle der Maschinenhersteller
Ob weitere Regionen und Hersteller diesem Beispiel folgen werden, steht noch in den Sternen. Es wäre für eine regionale Versorgungssicherheit auf jeden Fall hilfreich, wenn hier ähnliche Programme aufgesetzt würden. Dafür braucht es neben den geeigneten Produktionsstätten vor allem umfangreiches Wissen über die Anforderungen der Pulverherstellung und -abfüllung sowie leistungsfähige Anlagen, die sämtliche regulatorischen Vorschriften erfüllen können und zudem auf eine hohe Effizienz ausgerichtet sind.
Natürlich können Maschinenhersteller diesen Herausforderungen nicht im Alleingang gerecht werden. Aber sie können mit ihrem jahrelangen Know-how und technologischen Lösungen auf jeden Fall zu einer vielversprechenden Umsetzung beitragen. Als ehemalige Verpackungssparte der Bosch-Gruppe entwickelt beispielsweise Syntegon Technology für die Pharmaindustrie seit über 60 Jahren ausgereifte Gesamtlösungen. Ganz unterschiedliche Faktoren spielen hier eine wichtige Rolle:
Luftversorgung und Reinigung im Abfüllbereich
Natürlich stellen auch flüssige Pharmazeutika die Abfüllung vor zahlreiche Herausforderungen. Bei pharmazeutischen Pulvern kommt deren Konsistenz erschwerend hinzu: Die fein gemahlenen Wirkstoffe stauben leicht. Um Maschinenbediener sicher zu schützen, sind staubdichte Barrieren und eine abgeschlossene Luftversorgung mit effizienten und leistungsstarken Filtersystemen im Füllbereich erforderlich.
Ein erweitertes UDAF-(Uni-Directional Air-Flow, zu Deutsch: unidirektionaler Luftstrom)-Belüftungssystem etwa reinigt und temperiert die zirkulierende Luft des Abfüllbereichs und reguliert die Luftfeuchtigkeit. Auch die Maschinenreinigung ist bei Pulvern besonders aufwendig. Die feinen Staubteilchen können sich überall in der Maschine festsetzen. Abhilfe schaffen ein offenes Design, leichte Zugänglichkeit sowie die Reinigung und Sterilisation (CIP-SIP) des Produktzuführsystems.
Baugröße als Kostenfaktor
Je größer der Abfüllbereich einer Anlage, desto höhere Kosten fallen für Sicherheitsumschließungen, Filtration, Temperierung, Betrieb, Wartung und Reinigung an. Gerade im Reinraum Klasse B, wo die Pulver üblicherweise abgefüllt werden, zählt jeder Zentimeter. Hier bietet eine vertikale Bauweise mit guter Zugänglichkeit und der Möglichkeit zum Wandeinbau mit Wartungsmöglichkeiten außerhalb des Füllraums enorme Vorteile. Ist der Füllbereich zusätzlich vom Ein- und Auslauf abgetrennt, verringert sich der Raum, der mit steriler Trockenluft entstaubt und gekühlt werden muss.
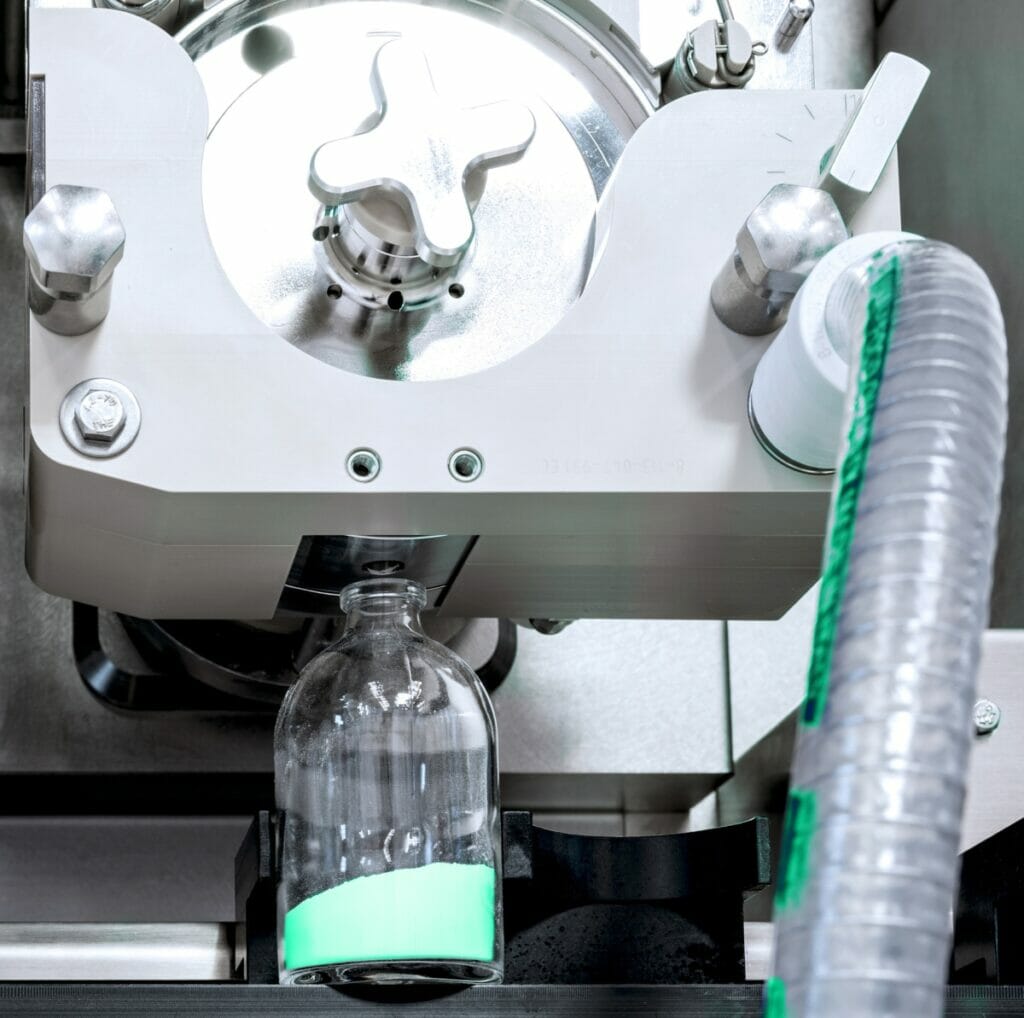
Variabel dosieren: Die Ausstattung mit bis zu drei Dosierstationen für verschiedene Füllvolumen ist möglich. (im Detail ein Druck-Vakuum-Dosierrad). (Bild: Syntegon Technology)
Ein modularer Aufbau, bei dem pharmazeutische Hersteller flexibel zwischen unterschiedlichen Füll- und Wiegemodulen wählen können, bringt weitere Platzersparnis. Neben der Größe ist die Zeit ein weiterer ausschlaggebender Faktor für die Kostenreduzierung: Je schneller Formatteile gewechselt werden können und je weniger produktberührende Teile es zu reinigen gibt, desto schneller kann mit einer neuen Charge begonnen werden.
Schnelligkeit durch variablen Transport
Allein mit etwa 230 Maschinen weltweit unterstützt Syntegon Technology seine Kunden bei der Abfüllung pharmazeutischer Pulver. Je nach Aufgabenstellung kommen optimierte technologische Lösungen zum Einsatz, so auch beim Transport innerhalb des Abfüllprozesses.
So kann die AFG 5000 von Syntegon bis zu 480 Vials pro Minute verarbeiten. Dafür wurde vom Unternehmen ein einzigartiges Transportsystem entwickelt, das sicher zwischen kontinuierlichem und getaktetem Transport variiert: Während die Vials kontinuierlich einlaufen, passt das Transportsystem die Geschwindigkeit im weiteren Verlauf präzise dem Rhythmus der einzelnen Arbeitsstationen wie Befüllen, Wiegen oder Stopfensetzen an. So lassen sich Verzögerungen im Arbeitsablauf vermeiden.
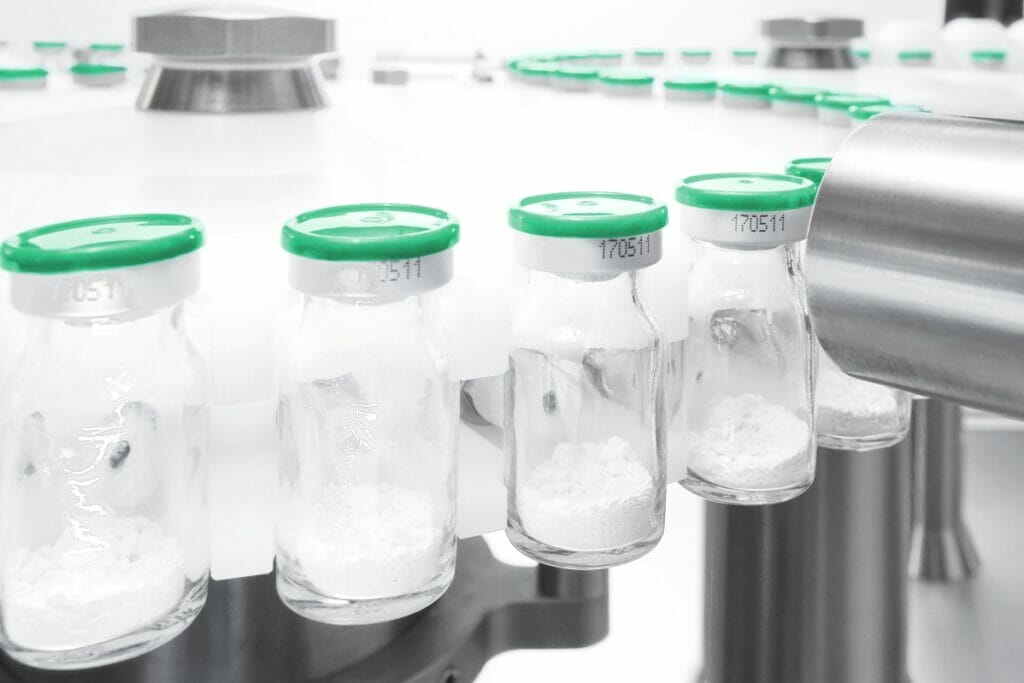
Besonderheit Transportsystem: Das vertikal umlaufende System ist so konzipiert, dass keine Leerlaufzeiten oder Staus entstehen. (Bild: Syntegon Technology)
Das vertikal umlaufende Transportsystem ist so konzipiert, dass keine Leerlaufzeiten oder Staus entstehen. Sobald die Trägersysteme die Vials nach dem Stopfensetzen am Auslauf abgegeben haben, fahren die Shuttles im Schnellmodus wieder zum Einlauf zurück und stehen für den nächsten Transport bereit. Die hundertprozentige In-Prozess-Kontrolle stellt zudem sicher, dass kein unnötiger Produktverlust entsteht – ein weiterer Vorteil für die Herstellung kostensensitiver Antibiotika.
Sicherheit und Effizienz vereinen
Um bei der Entscheidung für eine bestimmte Anlage auf Nummer sicher zu gehen, empfiehlt sich eine frühe Zusammenarbeit zwischen Medikamenten- und Maschinenhersteller. Ihre umfassenden Erfahrungen geben die Spezialisten von Syntegon gern an ihre Kunden weiter, z. B. im „Pulverlabor“ in Crailsheim.
Hier unterstützen die Maschinenexperten bei der Auswahl des idealen Füllsystems, ermitteln die optimalen Einstellparameter oder führen Grundlagenuntersuchungen durch, um höchste Sicherheit für Bediener, Produkt und Patienten mit der erforderlichen Effizienz zu vereinen – und damit zumindest anlagenseitig die Voraussetzungen für eine regionale Produktionsstrategie zu schaffen.