Vollautomatisch verschiedenste Gimmicks auf Zeitschriften aufkleben – diesen Wunsch einer norddeutschen Druckerei konnte das Ingenieurbüro Kock aus Kiel mit zwei Adept-Quattro-Deltakinematiken und der PackXpert-Software samt Bildverarbeitung erfüllen. Pro Stunde verlassen bis zu 5.500 beklebte Zeitschriften die Anlage.
Seit den späten 70er Jahren, als das Comic-Heft Yps erstmals in großem Umfang mit beigelegten Kinderspielzeugen wie kleinen Kompassen aus Kunststoff oder dem „Urzeitkrebs“-Aufzuchtset auf sich aufmerksam machte, greifen verschiedenste Zeitschriften auf solche Gimmicks zurück. In einer norddeutschen Druckerei wurden sie lange Jahre manuell aufgeklebt. Zwei geübte Mitarbeiter brachten es dabei auf durchschnittlich 3.000 Zeitschriften pro Stunde.
Das Ingenieurbüro Kock aus Kiel, ein versierter Sondermaschinenbauer, der bereits mehrere Projekte mit der Druckerei erfolgreich realisiert hat, nahm die Herausforderung an, das Aufkleben einer Vielzahl unterschiedlichster Gimmicks zu automatisieren. Für das ehrgeizige Ziel von 5.500 aufgeklebten Einheiten pro Stunde unter besonderen Rahmenbedingungen kam für Kock nur ein Roboter in Frage: der Adept-Quattro.
Dieser Roboter verfügt über eine patentierte Kinematik, die speziell für High-Speed-Verpackungsaufgaben und Materialhandling entwickelt wurde. Als weltweit einziger Roboter mit 4-Arm-Design erreicht er eine extrem hohe Geschwindigkeit und Beschleunigung auch bei höheren Traglasten über den gesamten Arbeitsbereich, also die ideale Maschine für die Handhabung der Gimmicks.
Vereinzelung und lagerichtige Zuführung
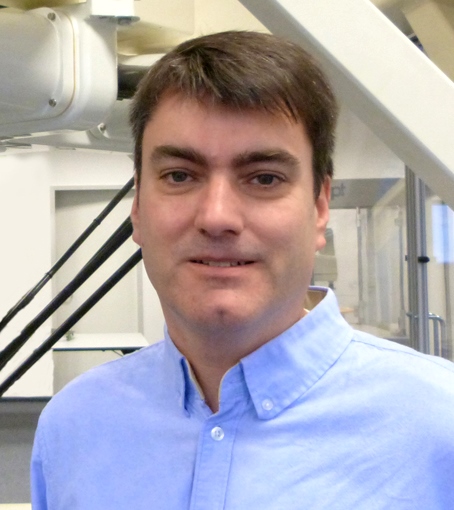
Peter Lange
Peter Lange, Leiter der Applikationsabteilung von Adept, der Kock mit seinem Team bei diesem Projekt unterstützt hat, erinnert sich noch gut an den ersten Kontakt: „Als wir die vielen unterschiedlichen Varianten an Spielzeugen gesehen hatten, beschlichen uns ernste Zweifel. Wir waren zwar sicher, dass unsere Quattros die verschiedenen Gimmicks in der nötigen Taktzeit greifen und aufkleben könnten, aber eben nur dann, wenn das Problem der Vereinzelung und lagerichtigen Zuführung zu lösen sein würde.“
Tatsächlich hatte das Ingenieurbüro die Lösung schon parat, wie Geschäftsführer Kay-Olaf Kock betont: „Wir kennen das Problem, dass sich Produkte, die aufgrund ihrer Größe und flächigen Form keine selbstvereinzelnden Eigenschaften besitzen und sich mit herkömmlichen Zuführsystemen nicht vereinzeln lassen. Für diese Fälle haben wir ein einzigartiges Vereinzelungssystem entwickelt, mit dem sich lose dreidimensionale Produkte für die Weiterverarbeitung durch Roboter aufbereiten lassen.“ Im konkreten Fall werden die in großen Kartons angelieferten Gimmicks in einen Trichter geschüttet, portioniert, vereinzelt, hinreichend geordnet und mit einem gewissen Abstand auf ein Zuführband aufgebracht. Diese technisch überaus komplexe Lösung hat sich als prozesssicher und absolut zuverlässig erwiesen.
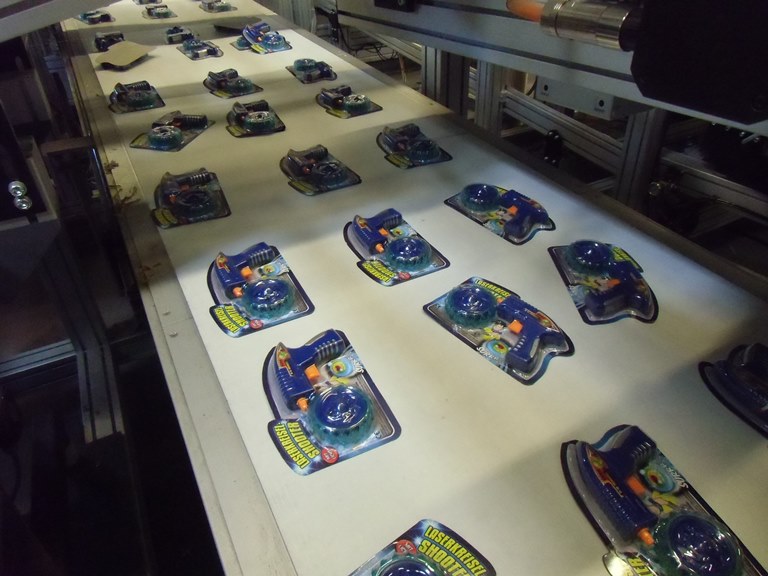
Die Bildverarbeitung in einem Kameratunnel übernimmt die Produktidentifikation und bestimmt die Lage auf dem Band.
Produktidentifikation und Geschwindigkeit
Das Zuführband transportiert die Gimmicks anschließend durch einen Kameratunnel. Die integrierte Bildverarbeitung übernimmt die Produktidentifikation und bestimmt die Lage der Gimmicks auf dem Band. Das System erkennt dabei auch, welche Teile in der richtigen Lage, also mit der Klebeseite nach unten auf dem Band liegen und dadurch von den Robotern gegriffen und aufgeklebt werden können. Falsch liegende Teile, deren Klebeseiten nach oben zeigen, verbleiben auf dem Band, werden automatisch lagerichtig ausgerichtet und der Anlage erneut zugeführt.
Ein interessantes Detail ist, dass die Bildverarbeitung nicht nur Lage und Position der einzelnen Gimmicks erkennt, sondern auch die Information, wie viele richtig liegende Teile sie erkannt hat, liefert. Auf der Basis dieses Wertes passt die Steuerung automatisch die Geschwindigkeit des Zuführbandes so an, dass genau so viele Gimmicks zugeführt werden, wie die Roboter verarbeiten können.
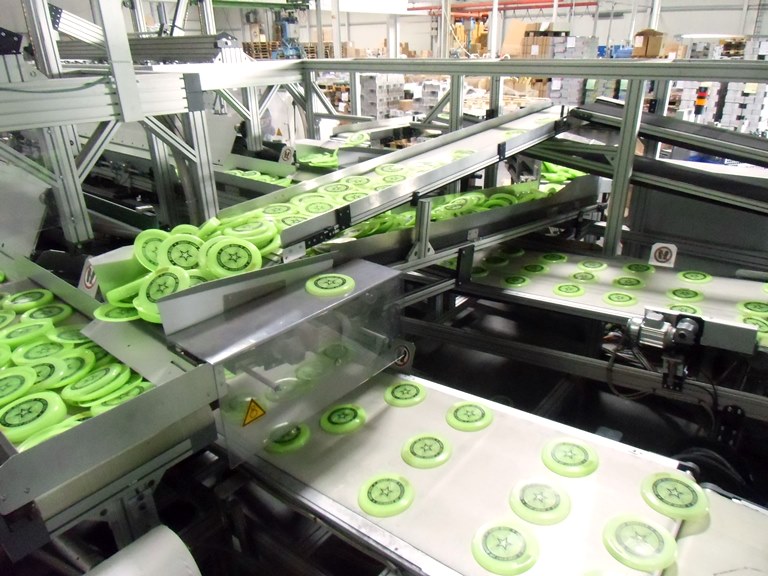
Portioniert, vereinzelt, hinreichend geordnet und mit einem gewissen Abstand gelangen die Teile auf das Zuführband.
Aufkleben im Vorbeiflug
Um die ehrgeizige Bestückungsleistung erreichen zu können, kommen zwei baugleiche Adept-Quattro s650H zum Einsatz, die jeweils über ein eigenes Zuführband verfügen und im ständigen Wechsel die Zeitschriften bekleben. Sobald einer der Roboter mit seinem Vakuumsauger ein Gimmick vom Zuführband aufgenommen hat, berechnet die Software Position und Geschwindigkeit der nächsten für den Roboter erreichbaren Zeitschrift. Der Deltaroboter verfährt dann zum darunterliegenden Zeitschriftentransportband, fährt kurz mit dem jeweiligen Heft mit und legt das Teil nach Erreichen der definierten Position aus einer Höhe von etwa drei Millimetern mit einem Druckluftimpuls auf die mit einem kleinen Klebepunkt versehene Stelle ab. Das Gimmick wird also nicht direkt vom Roboter auf die Zeitschrift gedrückt, sondern dank perfekter Synchronisation des Roboters mit dem Zeitschriftenband berührungslos über einen Blasimpuls aufgebracht.
Damit dies bei einer durchschnittlichen Taktzeit von 1,3 Sekunden pro Roboter prozesssicher funktioniert, haben Peter Lange und sein Team den Ablauf bei den Versuchen mit einer Highspeed-Kamera genau analysiert, denn mit bloßem Auge sind die einzelnen Sequenzen nicht mehr auszumachen. Auf Basis dieser Videoanalysen wurden dann die Abläufe so lange optimiert, bis die gewünschte Bestückungsleistung erreicht war, eine Dienstleistung von Adept, die von Systemintegratoren immer wieder gerne genutzt wird.
Bei dem relativ großen Höhenunterschied zwischen Zuführband und Transportband hätten viele andere Deltaroboter passen müssen. Nicht so der Adept-Quattro s650H. Peter Lange: „Schon der zylindrische Arbeitsraum des Adept Quattro s650H mit 1.300 mm Durchmesser deckt eine Höhe von 215 mm ab. Darunter befindet sich aber ein zusätzlicher kegelförmiger Arbeitsraum mit einer Höhe von 285 mm. Im Zentrum bietet der Quattro s650H dadurch einen Hub von 500 mm – für das Bekleben der Zeitschriften mehr als genug. Gleiches gilt für die Traglast von 6 kg.“
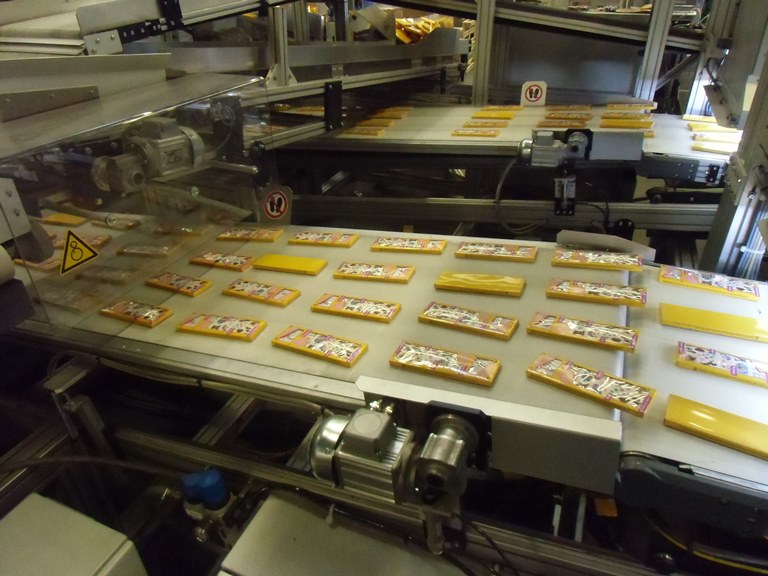
Das Einlernen eines neuen Produkts erfolgt innerhalb einer Viertelstunde.
Bedienerfreundliches Anlagenkonzept
Nachdem die Anlage häufig umgestellt werden muss (in der Regel läuft kein Gimmick länger als einen Tag) haben Kock und Adept auf ein einfaches Umrüsten und Einlernen neuer Produkte geachtet. „Die Bediener müssen oft mehrmals am Tag neue Produkte einlernen. Dabei ändern sich sowohl die Gimmicks als auch deren Positionierung auf den Zeitschriften. Dem Anlagenbauer Kock ist es aber gelungen, die Anlage mechanisch und steuerungsseitig sehr bedienerfreundlich auszulegen. Das Einlernen eines neuen Produkts ist nach einer Einweisung und mit etwas Erfahrung in etwa fünfzehn Minuten erledigt“, betont Peter Lange.
Erheblichen Anteil an der problemlosen Bedienung hat das von Adept zur einfachen Programmierung und Parametrierung komplexer High-Speed-Verpackungsanwendungen entwickelte Softwaretool Adept-ACE PackXpert. Anstelle klassischer Programmierung erfolgt die Parametrierung der anwendungsspezifischen Verpackungsaufgaben über eine intuitiv zu bedienende grafische Benutzeroberfläche. Ganz gleich, ob ein oder mehrere Adept Roboter verwendet werden, verschiedene Kameras zum Einsatz kommen, die Roboter bandsynchron oder im Taktbetrieb eingesetzt werden, das Softwaretool hat für nahezu jede Aufgabenstellung bereits die komplette Funktionalität integriert. Dadurch reduziert sich die notwendige Zeit zwischen Anlagenkonzeption und Inbetriebnahme auf ein Minimum und die Prozesssicherheit der realisierten Verpackungslösung wird erhöht.
Wie gut dies in der Praxis funktioniert, durfte Peter Lange bei der komplexen Klebeanlage selbst erfahren: „Nach der Mitarbeiterschulung und einigen Anrufen während der Optimierungsphase habe ich monatelang nichts mehr von den Bedienern gehört. Leicht beunruhigt griff ich also zum Telefonhörer. Schnell stellten sich meine Bedenken als völlig unbegründet heraus. Die Anlage arbeite schnell und zur vollsten Zufriedenheit, die Bedienung bereite keinerlei Probleme, hieß es. Ein Volltreffer in Sachen Automation also, was will man mehr.“