Gutes Design mit hoher Benutzerfreundlichkeit verbinden, den Kunststoffverbrauch minimieren und fossile Ressourcen schonen: Diesen Zielen entsprechend entwickelt Pöppelmann FAMAC Lösungen für die Praxis. Die drei Ansätze „ReDuce“, „ReUse“ und „ReCycle“ setzen dafür den Rahmen.
Durch ressourcenschonende Artikelkonzepte und effiziente Produktionsverfahren wird der Materialeinsatz reduziert. Produkte werden für eine mehrfache Verwendung konzipiert. Und wo es möglich ist, wird durch innovative Recyclingkonzepte eine Kreislaufwirtschaft angestrebt. Wir haben Jörg Wilke, den Entwicklungsleiter bei Pöppelmann FAMAC, zur Produktentwicklung nach Eco-Design-Maßgaben befragt. Er ist bereits seit 27 Jahren im Unternehmen tätig und verantwortet insbesondere die Produkt-/Prozessentwicklung im Bereich Verpackung.
Herr Wilke, wenn ein Kunde mit einer Anfrage zu Ihnen kommt: Welche Voraussetzungen müssen erfüllt sein, bevor die Entwicklungsabteilung „starten“ kann?
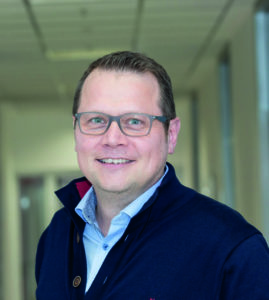
Jörg Wilke, Leiter Produkt-/Prozessentwicklung.
(Bild: Pöppelmann)
Jörg Wilke Für uns ist zunächst die Spezifikation des Produkts wichtig: Wird es z. B. heiß oder kalt abgefüllt, evtl. pasteurisiert oder schockgefrostet? Wie wird es gelagert? Diese und weitere Fragen haben u. a. Einfluss auf die Materialwahl. Häufig müssen wir darüber hinaus eine Reihe Vorgaben berücksichtigen – von den Parametern einer bereits vorhandenen Abfüllanlage bis hin zu ganz konkreten Kundenvorstellungen bezüglich der Optik. Um die Machbarkeit abzuklären und die Rahmenbedingungen zu definieren, haben wir einen detaillierten Fragebogen, unseren Quick-Check, entwickelt. Aber ganz gleich unter welchen Voraussetzungen: Unser Ziel ist immer, die bestmögliche Lösung für den Kunden zu finden.
Welche Möglichkeiten stehen prinzipiell zur Verfügung?
Jörg Wilke Wir bieten unseren Kunden von der Produktentwicklung bis zur Serienfertigung alle Prozessschritte unter einem Dach. Das hat viele Vorteile, so müssen z. B. keine sensiblen Daten an Dritte weitergeben werden, die gesamte Terminschiene liegt in unseren Händen, und wir sind unabhängig von Zulieferern. Dadurch können wir Verpackungsentwicklungen innerhalb kürzester Zeit realisieren.
Und wie läuft das in der Praxis ab?
Jörg Wilke Im ersten Entwicklungsschritt werden Ideen formuliert und in Entwürfe umgesetzt. Unsere Produktdesigner erstellen 3D-Visualisierungen und fotorealistische Abbildungen für den ersten optischen Eindruck. Im nächsten Schritt produzieren wir mittels Rapid Prototyping und Rapid Tooling Anschauungsmuster: Im 3D-Druck fertigen wir Prototypen der Verpackung und/oder setzen ihn zur Herstellung von Werkzeugen ein, die wir zur Fertigung erster Muster aus Serienmaterial nutzen.
Rapid Prototyping ist für kleine Produktmengen gedacht, mithilfe von Rapid Tooling lassen sich Prototypen in größeren Mengen fertigen, die dann schon für Testbefüllungen bereitstehen. Häufig finden diese beiden Prozesse auch parallel statt. Schließlich wird in unserem hauseigenen Werkzeugbau ein Vorserienwerkzeug aus Stahl oder Aluminium gefertigt, mit dem wir Produkte für umfangreichere Testläufe herstellen. Auf diese Weise optimieren wir die ersten Entwürfe.
Produktentwicklung unter Eco-Design-Maßgaben
Wie werden die Kunden in die Prozesse eingebunden?
Jörg Wilke Eine partnerschaftliche Verbindung ist die Voraussetzung für ein gutes Ergebnis: Um die Erwartungshaltung unserer Kunden vollständig erfüllen zu können, zeigen wir mögliche Grenzen frühzeitig auf. Jeder Entwicklungsschritt findet dann in enger Abstimmung statt. Häufig gibt es beim Kunden interne Zielkonflikte, z. B. zwischen Marketing und Produktion. Unsere Aufgabe ist es, die verschiedenen Wünsche und Vorgaben abzugleichen und eine Lösung zu entwickeln, in der sich alle Seiten wiederfinden. Es zahlt sich aus, zu Beginn ausreichend Ressourcen in die Entwicklungsarbeit zu stecken.
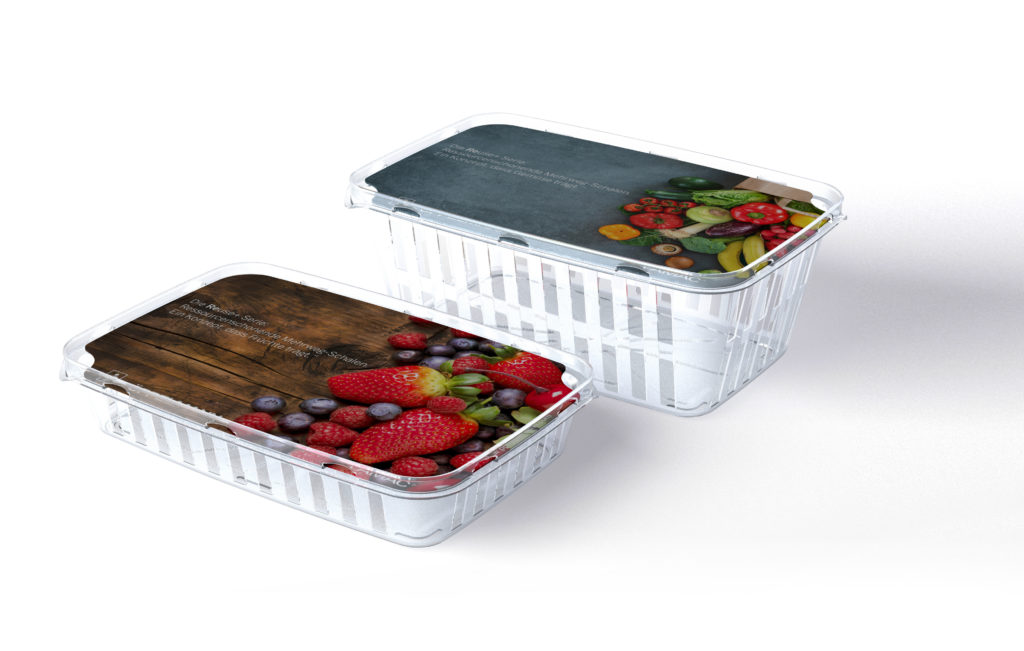
ReUse+-Serie mit reduziertem, ressourcenschonendem Materialeinsatz und Mehrfachnutzung: wiederverwendbare Verpackungen für Obst und Gemüse. (Bild: Pöppelmann)
Gibt es Projekte, die besonders anspruchsvoll waren und bei denen das Unternehmen besonders stolz auf die Lösung ist?
Jörg Wilke Ja, dazu zählen viele unserer aktuellen Entwicklungen, die unter Eco-Design-Maßgaben entstanden sind: In Kooperation mit einem Kunden haben wir in unserer ReDuce+-Serie einen Eimer in Gitterstruktur für Snacktomaten erstellt, der bis zu 30 Prozent Material einspart und so auch Logistikkosten und DSD-Gebühren senkt. Dieses Konzept entwickeln wir gerade weiter zur ReUse+-Serie: Mehrwegschalen in Gitterstruktur aus recyclingfähigem Kunststoff für Obst und Gemüse, die Einwegschalen im LEH ersetzen sollen. In einem aktuellen Projekt entwickeln wir außerdem einen Deckel für eine Verpackung aus dem Molkereibereich weiter, um Funktionalität und attraktive Optik mit reduziertem Materialeinsatz zu vereinen.
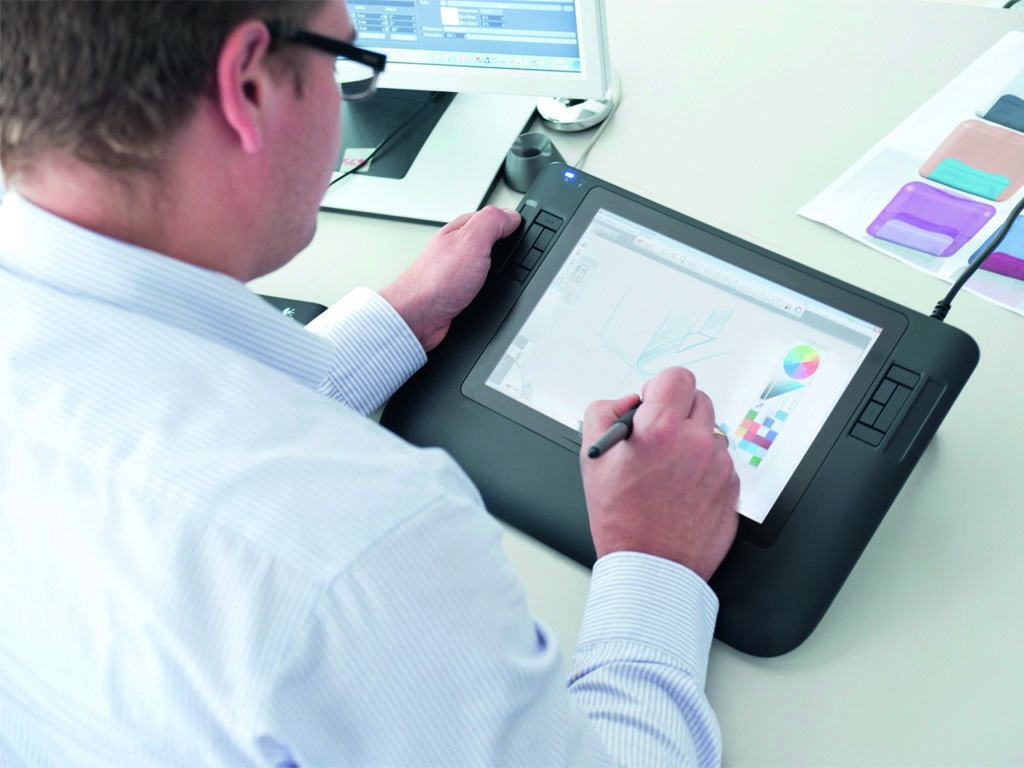
Machbarkeit klären, Rahmenbedingungen definieren: Die Produktentwicklung startet mit dem Quick-Check. (Bild: Pöppelmann)
All diese Entwicklungen, bei denen wir ökonomische und ökologische Aspekte des Produkts entlang seines gesamten Lebenszyklus berücksichtigen und mehr Nachhaltigkeit und Produktfunktionalität mit höchstem Mehrwert für den Kunden vereinen, machen uns sehr stolz.
Im Rahmen der unternehmensweiten Initiative PÖPPELMANN blue bündeln Sie alle Aktivitäten, die sich für einen geschlossenen Materialkreislauf engagieren und den Übergang von einer Linear- zu einer Kreislaufwirtschaft gestalten sollen. Welche Ziele haben Sie sich für die nähere Zukunft gesetzt?
Jörg Wilke Die gesamte Pöppelmann Gruppe strebt an, möglichst Post-Consumer-Rezyklate (PCR) einzusetzen, also Materialien aus den Wertstoffsammlungen. Denn nur so kann eine echte Kreislaufwirtschaft entstehen. Aufgrund gesetzlicher Vorgaben kann die Division Pöppelmann FAMAC, die Verpackungen für Lebensmittel, Kosmetik und Pharmaprodukte fertigt, nur für wenige Produkte Sekundärrohstoffe einsetzen.
Künftig wollen wir auch hier den Einsatz von PCR ermöglichen. Bis dahin lautet das Ziel, Verpackungen zu entwickeln, für die ein nur minimaler Materialeinsatz erforderlich ist und die zu 100 Prozent recyclingfähig sind. Wir glauben daran, dass Kunststoff ein sehr nachhaltiges Material ist – wenn man richtig damit umgeht und ihn verantwortungsvoll verwendet.