Mit „digitalen Zwillingen“ lassen sich Entwicklungs- und Inbetriebnahmeprozesse von Maschinen und Anlagen deutlich beschleunigen. Auch Unternehmen der Verpackungstechnik setzen Simulationssoftware ein.
Simulationssoftware verbessert und beschleunigt Entwicklungs- und Produktionsprozesse. Im laufenden Betrieb einer Anlage oder bei der Entwicklung werden alle Prozessschritte in einem sogenannten digitalen Zwilling abgebildet. Etwaige Fehler werden in einem kontinuierlichen Inbetriebnahmeprozess analysiert und beseitigt. In der Packaging-Branche haben unter anderem Bosch Packaging Technology, Krones und Somic ihre Prozesse mit Simulationssoftware der Münchner „machineering GmbH & Co.KG“ optimiert. Immerhin können Inbetriebnahmezeiten um bis zu 75 Prozent und Durchlaufzeiten um bis zu 15 Prozent reduziert werden.
Simulationssoftware ab der ersten Idee einbinden
Bei der Planung neuer Anlagen sollte die Simulationssoftware bereits ab der ersten Idee in die Entwicklungsprozesse integriert werden. Das Münchner Unternehmen „machineering“ betont, dass ihre Software „industrialPhysics“ prädestiniert dafür ist, als bereichsübergreifende Plattform zu fungieren. „IndustrialPhysics“ ermöglicht es, zu jedem Zeitpunkt den aktuellen Entwicklungsstand zu verifizieren und auf Realisierbarkeit mit weiteren Bereichen zu überprüfen. Die Fachbereiche Mechanik, Elektrik und Software können zeitgleich auf dieselben Modelle zurückgreifen und sie in ihren nativen Entwicklungsumgebungen bearbeiten. Die gemeinsame Weiterentwicklung wird schließlich mittels der Simulation sofort im Zusammenspiel getestet.
Erleichtert wird Anwendern die Nutzung von „industrialPhysics“, indem es in immer mehr Konstruktions- und Entwicklungssoftware eingebunden ist. Erst im Dezember 2017 gab „machineering“ bekannt, dass man künftig mit der Solidpro GmbH kooperiere. Das Unternehmen der Bechtle-Gruppe stellt mit „Solid Works“ ein weitverbreitetes CAD-Softwarewerkzeug her.
Konsistente Entwicklung wird sichergestellt
Softwaregestützte Simulationen verändern die Anlagenentwicklung. Anstatt wie bislang häufig üblich bei der Inbetriebnahme eines Systems einen Weg zu beschreiten und im Fehlerfall einen Schritt zurückzugehen und eine alternative Lösung zu wählen, findet nun eine kontinuierliche Inbetriebnahme statt. Alle Komponenten einer Maschine werden in digitalen Simulationsmedien zusammengeführt und optimiert. So wird die Konsistenz der Entwicklung sichergestellt.
Auch im laufenden Betrieb unterstützt die Simulationssoftware die Maschinenbetreiber. Anlagen können in Echtzeit simuliert werden. Es entsteht quasi ein „digitaler Zwilling“. Hilfreich sind digitale Zwillinge, um etwaige Störungen ohne lange Maschinenstillstände zu lokalisieren und zu beheben. Auch Änderungen können in verschiedenen Varianten virtuell durchgespielt werden, bevor die vielversprechendste Option in die reale Anlage überspielt wird.
„Machineering“ hat mit dem „machineering Digital Twin“ eine Simulationslösung im Angebot, bei der der digitale Zwilling nicht in der Unternehmens-Cloud installiert wird. Stattdessen läuft er als eigenes virtuelles Modul basierend auf Echtzeitdaten direkt im Schaltschrank einer Anlage. Der digitale Zwilling liefert im laufenden Produktionsbetrieb alle notwendigen Daten für einen reibungslosen Ablauf. Auch die Berechnung komplizierter geometrischer Modelle ist problemlos möglich.
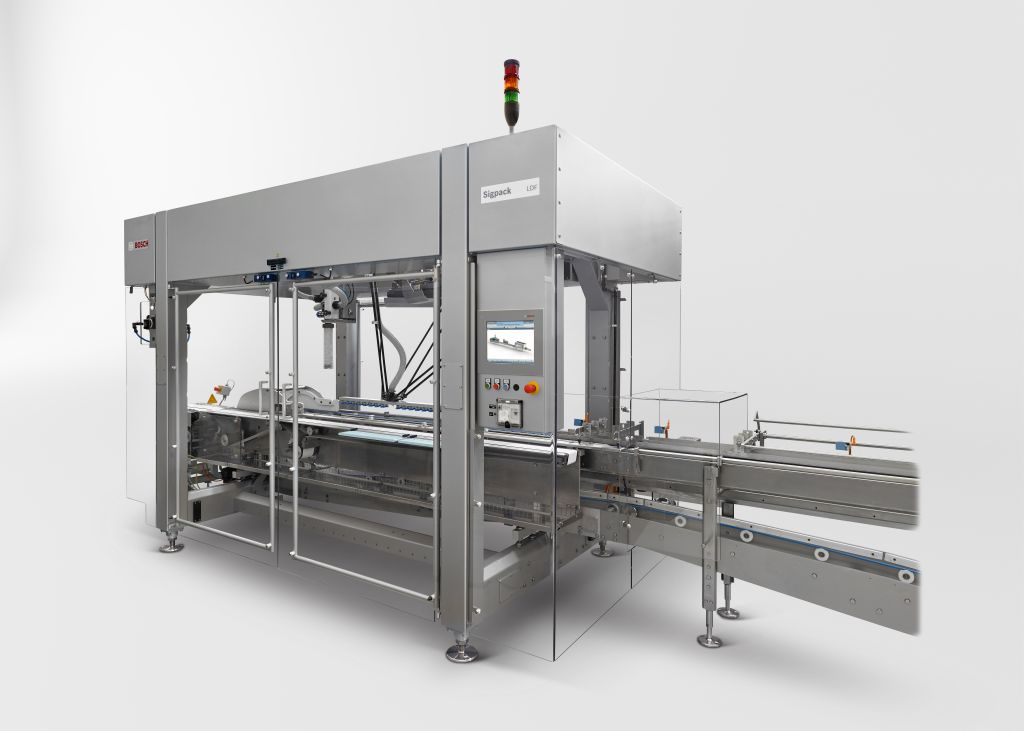
„Bosch Packaging Technology“ entwickelt seine Steuerungssoftware parallel mit einem „Hardware in the Loop“-Modul. (Bild: Robert Bosch GmbH)
Bosch Packaging Technology testet Steuerungssoftware virtuell
Im Verpackungsbereich setzt beispielsweise Bosch Packaging Technology auf „industrialPhysics“. Der Maschinenbauer wollte seine Steuerungssoftware bereits frühzeitig im Entwicklungsprozess testen, um die mechanische und elektrische Montage nicht durch die erst spät erfolgende Software-Inbetriebnahme zu verzögern. Nun laufen beide Entwicklungsprozesse parallel. Die Software wird mit einem „Hardware in the Loop“-Modul (HIL) entwickelt. „Der HIL-Softwaretest an der virtuellen Maschine inklusive der Simulation des Produkttransports stellt für uns sicher den größten Nutzen dar. So können wir frühzeitig Tests an der Steuerungssoftware vornehmen und direkt bei Bedarf reagieren“, sagt Dominik Unger, Verantwortlicher für Simulation bei der Bosch Packaging Technology.
Krones nutzt „industrialPhysics“ in eigenem Simulationstool
Der Verpackungs- und Abfüllspezialist Krones AG optimierte in der Serienfertigung die Inbetriebnahmezeiten seiner Maschinen und Anlagen mithilfe von „industrialPhysics“. In der Produktentwicklung dient die Software dazu, die SPS-Software bereits zu testen, bevor der Anlagen-Prototyp oder der Schaltschrank gefertigt wurde.
Krones geht sogar noch einen Schritt weiter: „Wir haben ein eigenes Tool entwickelt, mit dem wir auf einem möglichst effizienten und effektiven Weg unsere Simulationsmodelle erstellen. Dabei nutzen wir verschiedene Datenquellen und bereiten diese simulationsgerecht für ‚industrialPhysics‘ auf“, sagt Andreas Jeziorowski, als Entwickler bei Krones zuständig für das Engineering, die Entwicklung sowie die Standardisierung der virtuellen Inbetriebnahme.
Somic freut sich über schnellere reale Inbetriebnahme
Bereits seit 2012 setzt der Verpackungsmaschinenhersteller Somic GmbH & Co. KG auf „industrialPhysics“. Die Inbetriebnahme wird virtuell soweit vorbereitet, dass die realen Arbeiten beim Kunden später einfach, schnell und sicher ablaufen können. „Wir wollten mithilfe von Simulation die Inbetriebnahmezeit durch das Testen des Programms ohne die Hardware deutlich reduzieren, eine gleichzeitige Programm- und Maschinenoptimierung ermöglichen sowie eine Qualitätssteigerung im Projektablauf erreichen“, berichtet Eric Lah, Leiter Elektrokonstruktion bei Somic.