Die Pharmaproduktion steht vor ihrem nächsten Entwicklungsschritt: Mithilfe digitaler Werkzeuge können Hersteller schon heute Ausfallzeiten reduzieren, ihre Produktivität steigern und die Flexibilität erhöhen. Als Nächstes folgt auf diesem Weg die intelligente Vernetzung von Menschen, Daten und Technologie. Zwei Faktoren sind entscheidend: Wissen und Maschinen.
Wie stellen sich die Hersteller von pharmazeutischen Abfüll- und Verpackungsanlagen auf diese neuen Anforderungen ihrer Kunden ein? Wir haben beim süddeutschen Maschinenbauunternehmen Bausch+Ströbel nachgefragt.
pj: Bereits auf der Hannover Messe 2017 hat ihr Unternehmen als Partner von Siemens die Möglichkeiten eines digitalen Zwillings präsentiert. In diesem Jahr setzten ihre Entwickler im Verbund der strategischen Allianz Excellence United bei der diesjährigen Achema Maßstäbe mit dem gemeinsamen Industrie-4.0-Konzept. Das Thema Digitalisierung hat bei Bausch+Ströbel also einen hohen Stellenwert?
Dr. Hagen Gehringer: Das ist richtig. Wir verstehen uns schon lange nicht mehr als reiner Hersteller von Abfüll- und Verpackungsanlagen, sondern bieten unseren Kunden aus der Pharmabranche umfassende Lösungskonzepte an. Digitale Werkzeuge gehören hier seit Jahren dazu. Als Beispiel ist hier unser Virtual-Reality-Center zu nennen. In einer Zeit, als andere Unternehmen unserer Branche Virtual Reality noch hauptsächlich im Bereich Marketing einsetzten, arbeiteten wir bereits daran, diese Technologie ganz konkret für unsere Kunden nutzbar zu machen.
Anwendung findet Virtual Reality (VR) nun im gesamten Produktionszyklus unserer Anlagen: von der ersten Vorstellung möglicher Lösungen über die konkretere Projektplanung und das Design Review bis hin zur Schulung des Bedienpersonals unserer Kunden und letztendlich für die Planung von Anlagenmodifikationen. Selbst Strömungssimulationen (CFD) lassen sich hier bereits in einem frühen Projektstatus durchführen.
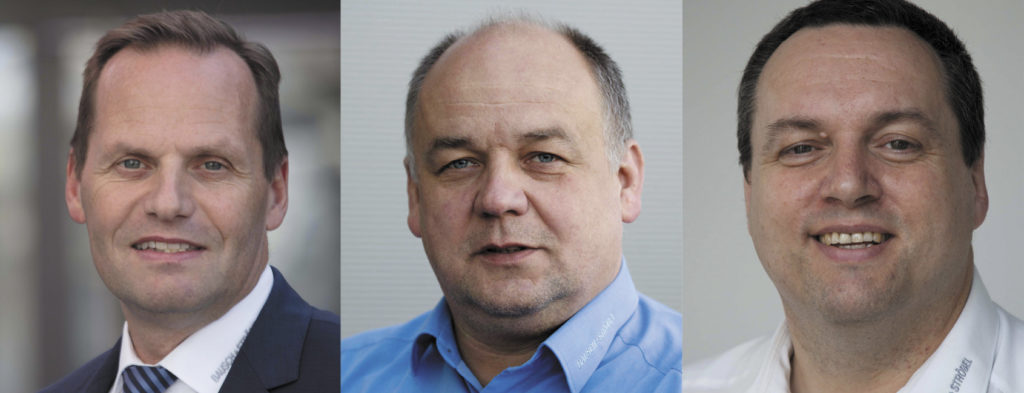
(v.l.n.r.) Dr. Hagen Gehringer (Geschäftsführer Bausch+Ströbel), Erich Bauer (Abteilungsleiter Entwicklung Mechatronik) und Michael Pratz (Abteilungsleiter Training und Qualifikation der B+S-Akademie)
pj: Wie passt hierzu der digitale Zwilling?
Dr. Hagen Gehringer: In unserem VR-Center können natürlich auch Bewegungen simuliert werden. Doch anders als bei unserem VR-Center liegt der Schwerpunkt beim digitalen Zwilling nicht auf der Konstruktion der Maschine, sondern auf der Programmierung. Es handelt sich um ein virtuelles Modell, an dem ganz konkret die Programmierung der Anlage getestet werden kann – und zwar noch bevor diese real gebaut ist. Zu einem hohen Prozentsatz funktioniert das bereits heute. An der echten Maschine müssen nur noch wenige Programmteile getestet werden. Bis 2020 wollen wir die komplette Programmierung mithilfe des digitalen Zwillings erstellen – eine enorme Zeitersparnis für uns und letztendlich für unsere Kunden.
pj: Das Thema Industrie 4.0 geht Bausch+Ströbel zusammen mit seinen strategischen Partnern der Excellence United an. Ist das Thema zu umfangreich für ein Unternehmen?
Dr. Hagen Gehringer: Natürlich hätten wir dieses Projekt auch allein gestartet – doch genau für derartige Zukunftsprojekte ist eine solche Partnerschaft sinnvoll, hier kann man Kräfte bündeln, von der Erfahrung der jeweils anderen profitieren. Mit unseren Partnern (alles ebenfalls mittelständische Familienunternehmen und führend auf ihrem jeweiligen Gebiet) haben wir insgesamt etwa 50.000 Anlagen auf dem Markt. Gemeinsam verfügen wir über einen großen Erfahrungsschatz im Bereich der Pharmaproduktion.
In der strategischen Allianz Excellence United bündeln die fünf familiengeführten Unternehmen Bausch+Ströbel, Fette Compacting, Glatt, Harro Höfliger und Uhlmann ihre Kompetenzen und bieten ihren Kunden technologisch führende Lösungen für die gesamte Wertschöpfungskette der Medizinprodukte- und Pharmaproduktion.
Das ist auch der Vorteil unseres Ansatzes: Unsere gemeinsam entwickelte Plattform ist keine Lösung, die von anderen Branchen einfach übernommen, sondern von Grund auf für pharmazeutische Anwendungen konzipiert wurde. Dahinter steckt ein zweijähriger Entwicklungsprozess, der selbstverständlich weitergeführt wird.
pj: Was genau wurde denn nun entwickelt und auf der Achema ausgestellt? Vor dem Cube bildeten sich ja lange Besucherschlangen.
Erich Bauer: Mit weit über 400 Besuchern war der Andrang tatsächlich sehr groß. Das zeigte uns auch, wie groß das Interesse unserer Kunden aus der Pharmabranche an diesem Thema ist. Zu sehen war im Cube unser gemeinsam entwickeltes IoT-Hub: eine offene und modulare Plattform für Softwareentwicklung und Systemintegration.
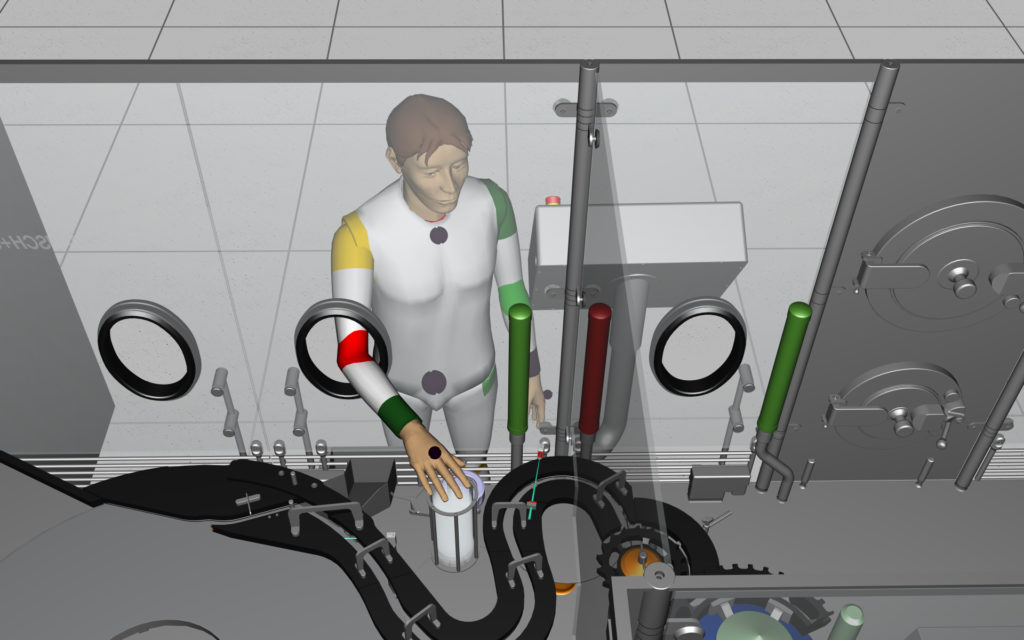
Bei diesen Erreichbarkeitsstudien kann mit wenig Aufwand geprüft werden, ob die Bediener später in angenehmer Haltung ihrer Arbeit nachgehen können oder mit Handschuheingriffen alle wichtigen Teile der Maschine erreicht werden. Diesem Vorgehen liegen Ergonomiemodelle auf der Basis von statistischen Extremwerten zugrunde.
Hier können unserer Anwender sowohl Anlagen der Excellence United vernetzen als auch Anlagen anderer Anbieter integrieren. Das haben wir im Cube anschaulich anhand einer Produktionslinie gezeigt. Der Anwender profitiert von einer zentralen Schnittstelle, über die er kontinuierlich Maschinen- und Prozessparameter erfassen und weltweit verfügbar machen kann (sowohl über eine Cloud als auch über das Firmennetzwerk). Dank der offenen Architektur und des modularen Aufbaus ist der IoT-Hub skalierbar. Anwender können die Plattform sowohl für einzelne Maschinen als auch größere Systeme wirtschaftlich nutzen und durch neue Schnittstellen und Apps erweitern, die individuell oder gemeinsam mit dem Kunden entwickelt werden.
pj: Was werden die nächsten Schritte sein?
Erich Bauer: Das Excellence-United-Digitalisierungsteam wird nun – im Verbund mit Anwendern – die Plattform mit dem Ziel weiter ausbauen, die Effizienz der Anlagen und Prozesse noch weiter zu steigern. Ein großes Thema wird hier zum Beispiel „Predictiv Maintenance“ sein, also die vorausschauende Wartung von Anlagen. Die Vielzahl der Daten, die während des Produktionsprozesses geliefert werden, können dazu genutzt werden, z. B. Bauteile zu identifizieren, die zeitnah ersetzt werden müssen.
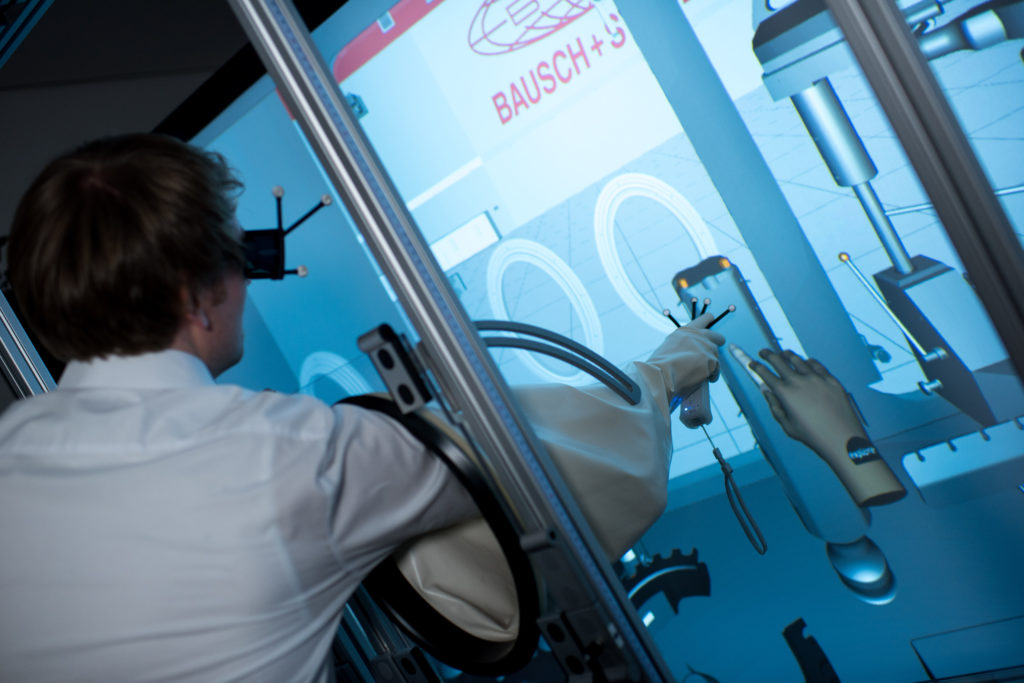
Die bei den Erreichbarkeitsstudien gefundenen Ergebnisse können durch eine subjektive Validierung unter Einsatz von physikalischen Handschuheingriffen abgesichert werden. Zusätzlich werden sämtliche Ergebnisse ausführlich dokumentiert. Virtual Reality kann so die bislang hier eingesetzten Mockups aus Holz oder Pappe ersetzen.
Michael Pratz: Diese große Menge an Daten für den Nutzer so aufzubereiten, dass er einen eindeutigen Nutzen hat, ist die Grundlage einer Vielzahl von Anwendungsmöglichkeiten. Einige haben wir sowohl bei der Achema als auch kürzlich bei der FachPack in Nürnberg anschaulich anhand der Etikettiermaschine ESA 1025 gezeigt. AR (Augmented Reality), MR (Mixed Reality) oder Wearables (tragbare Endgeräte) machen dabei direkt an der Anlage Daten sichtbar und stellen bisher ungeahnte Möglichkeiten für die Kontextualisierung dieser Daten zur Verfügung. Die Einsatzfälle reichen von der Unterstützung der Wartungstechniker bei der Fehlersuche bis zum Prozesstraining, ohne die Anlage physisch zur Verfügung zu haben. Mittels implementierter Trainer-/Trainee-Technologien können ganze Teams gemeinsam virtuell die unterschiedlichen Einsatzszenarien trainieren und steigern neben einer verkürzten Einsatzzeit auch wichtige GMP-Aspekte.
Dr. Hagen Gehringer: In den kommenden Jahren werden wir noch zahlreiche Anwendungsmöglichkeiten schaffen – darunter sicher auch solche, an die wir heute mangels technischer Möglichkeiten noch gar nicht denken. Der Prozess bleibt spannend.