Die Firma Osko setzt bei der Großserienfertigung von Pflanztöpfen künftig auf einen vollelektrischen Allrounder 720 A. Die Hochleistungsmaschine von Arburg erreicht hohe Einspritzgeschwindigkeiten von bis zu 400 Millimetern pro Sekunde und ist damit auch für den Einsatz im Verpackungsbereich interessant. Hinzu kommt ein im Vergleich zu marktüblichen Hybridmaschinen um bis zu 45 Prozent reduzierter Energiebedarf.
Sales Manager Packaging bei Arburg, Joachim Branz, rät: „Wer in Zeiten hoher Strom- und Materialpreise energieeffizient und ressourcenschonend fertigen will, sollte neben den Anschaffungskosten auch die Energiekosten im Blick behalten. Das gilt umso mehr, je niedrigpreisiger die Produkte und je größer die Stückzahlen sind.“ Kurze Zykluszeiten in Verbindung mit deutlich reduziertem Energiebedarf können den vorwiegend hybriden Maschinenpark von Verpackungsartikelherstellern künftig zugunsten vollelektrischer schnelllaufender Maschinen verschieben.
Neue Spritzeinheit bringt vollelektrischen Antrieb
Die Firma Osko setzt am Standort Ochtrup im Münsterland, Deutschland, auf einen elektrischen Allrounder 720 A in der Leistungsvariante „Ultimate“ mit der neuen Spritzeinheit in Größe 1300 und 3.200 kN Schließkraft. „Wir wollen bei der Fertigung dünnwandiger Pflanztöpfe eine optimale Zykluszeit erreichen – und das bei gleichzeitig beträchtlichen Energieeinsparungen“, definiert Osko-Inhaber Ralf Ostkotte die Zielsetzung für den vollelektrischen Neuzugang im Maschinenpark. Einspritzgeschwindigkeiten von bis zu 400 Millimeter in der Sekunde sowie sehr hohe Fließweg-Wandstärken-Verhältnisse sind dank der präzisen Servomotoren des Arburg Schwesterunternehmens AMKmotion möglich. Das Vierfachwerkzeug für die Anwendung stammt von der schweizerischen Firma Glaroform, die Automation vom Arburg-Partner Brink.
45 Prozent reduzierter Energiebedarf
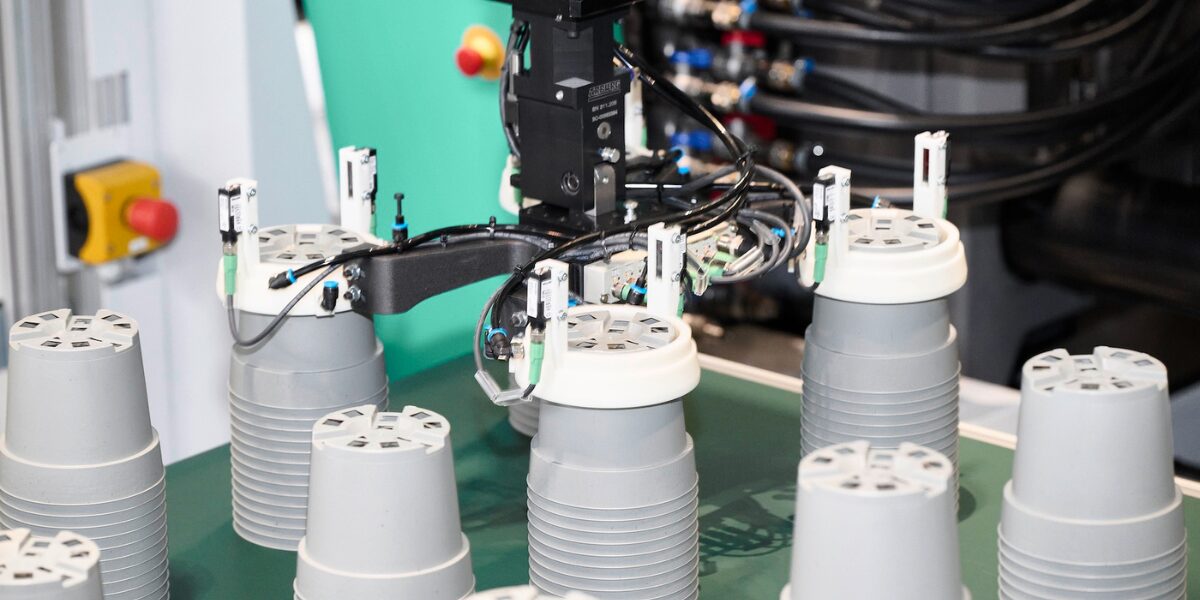
Der Greifer für die schonende Entnahme der Pflanztöpfe wurde mit einem 3-D-Drucker TiQ und einem Freeformer von Arburg additiv gefertigt. (Bild: Arburg)
Wie ist es nun um den Energiebedarf vollelektrisch versus hybrid bestellt? Um diese Frage zu klären, haben die Arburg-Experten im Vorfeld einen elektrischen Allrounder 720 A mit Spritzeinheit 1300 mit einer marktüblichen hybriden Packaging-Maschine im gleichen Schließkraftbereich (3.200 bzw. 3.300 kN) verglichen. Ergebnis: Bei gleichbleibender Prozess- und Bauteilqualität betrug der Energiebedarf der hybriden Maschine rund 68 kWh, während der vollelektrische Allrounder mit rund 37 kWh und damit einem um rund 45 Prozent reduzierten Energiebedarf auskommt. Dieses Einsparpotenzial hat Osko erkannt, um auf einem Markt mit bekannt geringen Margen zukunftsfähig möglichst wirtschaftlich und zugleich nachhaltig zu produzieren.
Post-Consumer-Rezyklat zu Pflanztöpfen
Die Nachfrage nach den Pflanzgefäßen von Osko GmbH ist weit über Deutschland und die benachbarten Niederlande hinaus hoch. Hohe Aufmerksamkeit erhielt auch das Exponat, das auf den Arburg Technologie-Tagen 2024 präsentiert wurde und je vier dünnwandige Pflanztöpfe mit rund 0,45 Millimeter Wandstärke aus 100 Prozent Rezyklat fertigte. Zum Einsatz kam Post-Consumer-Rezyklat (PCR) auf Basis von PP aus Kunststoff-abfällen aus der haushaltsnahen Sammlung. Digitale Funktionen in der Gestica-Steuerung sorgen für stabile Prozesse und eine gleichbleibend hohe Spritzteilqualität. So gleicht z. B. der „aXw Control RecyclatePilot“ schwankende Materialqualitäten aus und stellt eine gleichbleibend konstante Formfüllung sicher. Bei den zugesetzten Farben und Additiven wird darauf geachtet, dass die Pflanztöpfe recyclingfähig bleiben und sich nach Gebrauch wieder dem Dualen System zuführen lassen.
Motivation Energieeffizienz
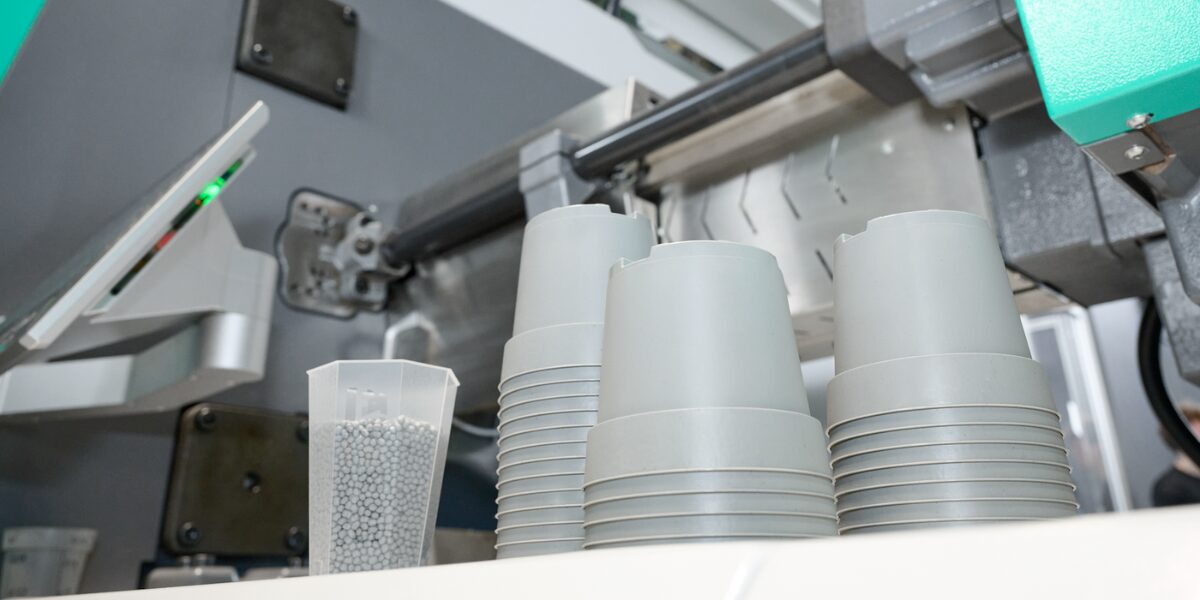
Bei der Großserienfertigung von dünnwandigen Pflanztöpfen aus PCR-Material setzt die Firma Osko auf vollelektrische Spritzgießmaschinen von Arburg. (Bild: Arburg)
„Osko legt besonders großen Wert auf Ressourcenschonung und Energieeffizienz und hinterfragt den erforderlichen Energieeinsatz auf vorbildliche Weise“, beschreibt Joachim Branz das mittelständische Familienunternehmen, das auch einen Großteil des verwendeten Stroms mit Solaranlagen selbst produziert. Ursprünglich im Jahr 1750 von Firmengründer Joan Bernard Ostkotte mit der Produktion von Tontöpfen gestartet, folgte 1984 die Erweiterung um spritzgegossene Kunststoffprodukte. Man hatte erkannt, wie viel günstiger und schneller man damit der wortwörtlich wachsenden Nachfrage nach Pflanztöpfen, Blumentöpfen und Blumenschalen gerecht werden kann. Seit 2005 verzichtet Osko komplett auf Ton und hat sich mittlerweile auf leichte und dünnwandige Artikel spezialisiert.
Während bei den Arburg Technologie-Tagen 2024 ein lineares Robot-System Multilift zum Einsatz kam, setzt man in Ochtrup nun auf eine spezielle Packaging-Automation von Brink mit schnell eingreifendem Side-Entry-Robot. Beim Greifer kommt jedoch weiterhin die additive Kompetenz von Arburg zum Tragen: Die Hauptkomponente, gefertigt mit einem 3-D-Drucker TiQ aus faserverstärktem Kunststofffilament, ersetzt Aluminium. Die vier passgenauen Greifer fertigte ein Freeformer in Hart-Weich-Kombination. Um die Pflanztöpfe zu entnehmen, wird der weiche Greifer-Part mit Druckluft „aufgeblasen“ und damit das Spritzteil fixiert und schonend gehandhabt.
Pionierarbeit im Sinne der Energieeffizienz
Minimale Stückkosten und Zykluszeiten sind Voraussetzung für eine wirtschaftliche Fertigung von Massenartikeln. „In der Regel ist es vor allem eine Frage von Philosophie und Investitionskosten, wenn für Packaging-Produkte vorwiegend hybride Maschinen eingesetzt werden“, beobachtet Joachim Branz und regt an:
„Betrachtet man das Einsparpotenzial gesamtheitlich über einen definierten Zeitraum, können elektrische Hochleistungsmaschinen je nach Einsatzfall die energie- und produktionseffizientere Alternative sein. Daher lohnt es sich, die Prozesse und einzelnen Anwendungen genau unter die Lupe zu nehmen und seinen Maschinenpark planvoll weiterzuentwickeln.“