Frozen pizzas are among the most popular fast-food dishes: However, their delicate ingredients make processing and packaging anything but easy. To overcome these challenges, a major frozen food manufacturer in the USA relies on Syntegon Technology’s system expertise from product distribution to case packers.
Sales of frozen pizza amounted to around $5.47 billion in the USA in 2020, according to Statista data: a profitable business for manufacturers, albeit under tough competitive conditions. To survive economically in this demanding market, high-quality products and efficient production are essential. To reduce costs and increase productivity, a major US frozen food manufacturer commissioned Syntegon to design and install a highly efficient distribution and packaging line, including numerous automated processes. „With the expert support of four international Syntegon locations, we designed a line that is perfectly tailored to the current and future needs of our customer,“ reports Tobias Bruetsch, Senior Account Manager at the machinery expert.
Automated distribution
Syntegon took over the planning of a new distribution and packaging system with a capacity of more than 400,000 pizzas per day. The frozen pizzas are fed from a spiral freezer and transported to Syntegon’s product distribution system (PDS).
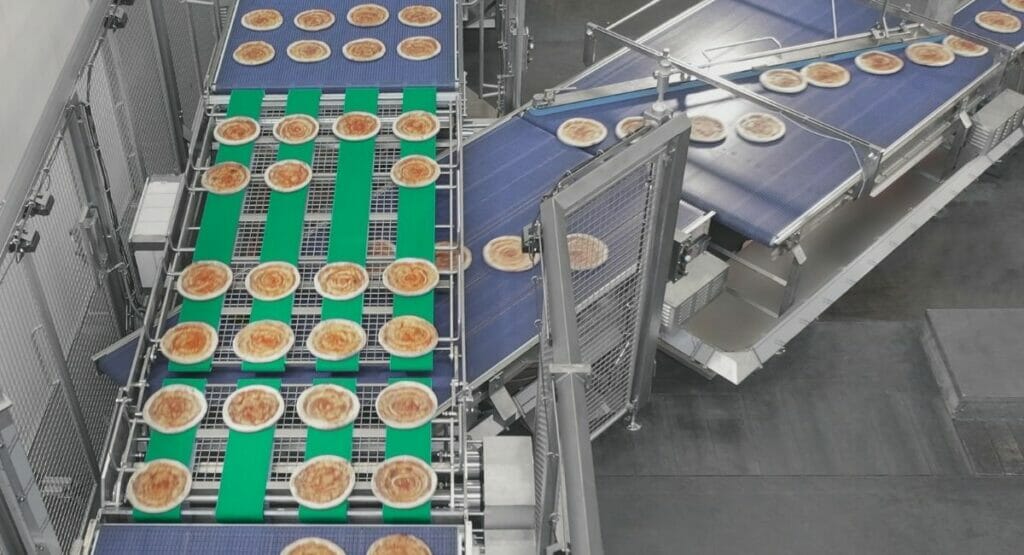
The products arrive at the PDS in random order. There they are arranged in uniform lines and rows before being packed on one of the four packaging lines. The PDS from the Syntegon plant in Beringen, Switzerland, has individually controlled conveyor belts and a sensor-based control system that detects missing products or incorrect arrangements on the conveyor belts. „The automated distribution system stops individual lanes when a product is missing to form a complete row. This replenishes the other distribution lanes and arranges the products correctly to create even rows without gaps,“ explains Hans-Peter Kientz, technical sales manager at Syntegon in Beringen.
Efficiency times four
The finished aligned pizzas arrive in complete product rows via a cross conveyor belt into a packaging branch for shrink film. In order to reduce downtimes and production losses to a minimum, the pizza manufacturer decided to integrate a back-up solution. The result: a distribution system that automatically distributes the frozen products to three packaging branches and detects any disruptions in the production process. If a fault occurs on one of the three lines, the system redirects the products to a fourth line, which is available at all times, to avoid production stoppages. In the event that two lines fail, the system is equipped with an additional conveyor belt at the end where the products are temporarily stored. As soon as the lines are ready for operation again, the system automatically feeds the products to the fourth line.
In the next step, a Pack 301 SK form-fill-seal machine from Syntegon’s plant in New Richmond, Wisconsin, USA, wraps the frozen pizzas in shrink film. Shrink-wrapping protects the products from contamination while ensuring that the pizza toppings remain optimally distributed. The machine also has an integrated metal detector that checks the products for foreign objects. Before the pizzas leave this machine, a precise weight check is carried out. It meets all wash-down requirements for optimal hygienic conditions for processing sensitive ingredients such as cheese or meat.
Second and third packaging on one line
The shrink-wrapped pizzas are then taken to the packaging area of the extensive plant: The individual pizzas are first packed into the standard pizza boxes by the Kliklok-Enterprise end-load cartoner from Syntegon’s site in Decatur, Georgia, USA. The Kliklok-Enterprise is equipped with one of the fastest rotating carton feeders in the industry, allowing it to process up to 340 cartons per minute.

In the final packing step, either 14 or 16 packed pizzas are inserted into a transport pack together with the Elematic 3001 from the Syntegon site in Remshalden, Germany. This wrap-around case packer is characterised by its high packing style flexibility: The pizzas can be packed either in trays, trays with inner inverts or wrap-around full wrappers.
Thanks to the highly automated packaging line, the frozen food manufacturer was able to significantly increase the efficiency of its production. With a production output of 340 pizzas per minute, Syntegon’s new line significantly outperforms the existing packaging line, according to the company. To make this possible, Syntegon combined experts and machines from four international locations.
Teamwork makes dreams come true
„We coordinated technologies and team members from three countries, and all experts contributed their individual know-how,“ explains Brad Baker, Sales Manager North America. „Together, we demonstrated our systems expertise and developed a complex, integrated solution for our customer.“
Thanks to good teamwork, Syntegon was able to offer the solution from a single source. The customer had one contact person who coordinated the communication between the four Syntegon branches and the customer. This proved to be a decisive advantage: Syntegon not only delivered an efficient complete package from product distribution to the finished transport packaging, but also maintained close contact with the customer throughout the entire project and accompanied the project implementation holistically.
More packaging news
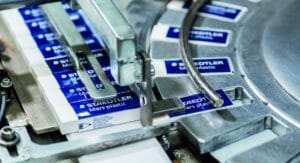
A contract with a handshake is valid
Managing director Tina Gerfer of Wilhelm Rasch Spezielmaschinenfabrik has modernized the company and successfully guided it through difficult times.
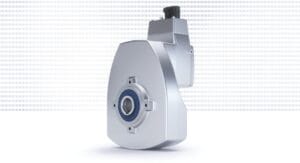
Asynchronous servo solutions for the packaging industry
From primary packaging to final packaging, electric drives play an important role. With a broad portfolio, Nord Drivesystems supports customers.
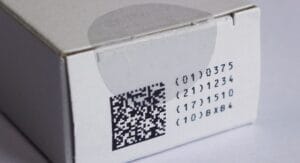
Label Durability
Labels offer many functions which can get lost due to label removal. PTS assesses labels and cardboard for durability and tamper evidence.
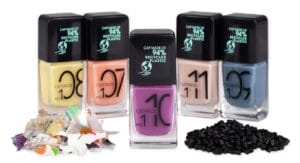
More design for recycling for cosmetics packaging
Packaging for decorative cosmetics is very special. The Forum Rezyklat calls for the recyclability of packaging to be taken into account when designing it.
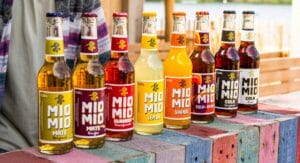
Innovation Barometer 2024
According to a survey conducted by Aktionsforum Glasverpackung 2024 is set to be a highly innovative year for glass packaging.
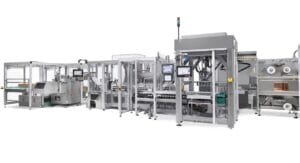
Flexible packaging system for natural cosmetics
Sustainability is part of Weleda’s identity. IWK is also contributing to this with its new flexible packaging line for many natural cosmetic products.