Bahlsen has given its „PiCK UP!“ biscuit bar a packaging update and expanded its existing machinery to include two bar packers from the packaging machine manufacturer Schubert. A major advantage is that the previous secondary packaging made of labels on the top and bottom could be replaced by folding cartons made of cardboard.
Whether for a sudden hunger pang, a short break or the Sunday coffee table – with a large selection of wafers, biscuits and cakes, the Hanover-based biscuit manufacturer Bahlsen has been ensuring high-quality products for over 130 years. To ensure that the sweet treats reach the consumer undamaged, the company has been working with the Crailsheim machine manufacturer for several years.
For the long-established company, enjoyment and doing good for the environment are not mutually exclusive. In addition to its own commitment to quality and continuous innovation, the biscuit manufacturer has also made sustainability a focus of its activities. The company works with carefully selected partners around the world who already act responsibly in the cultivation of raw materials such as cocoa or sugar.
In addition to the ingredients, however, the packaging of the products also plays a decisive role in sustainable action. For „PiCK UP!“, the popular chocolate biscuit, Bahlsen therefore wanted new packaging machines with which production can be switched to more environmentally friendly packaging.
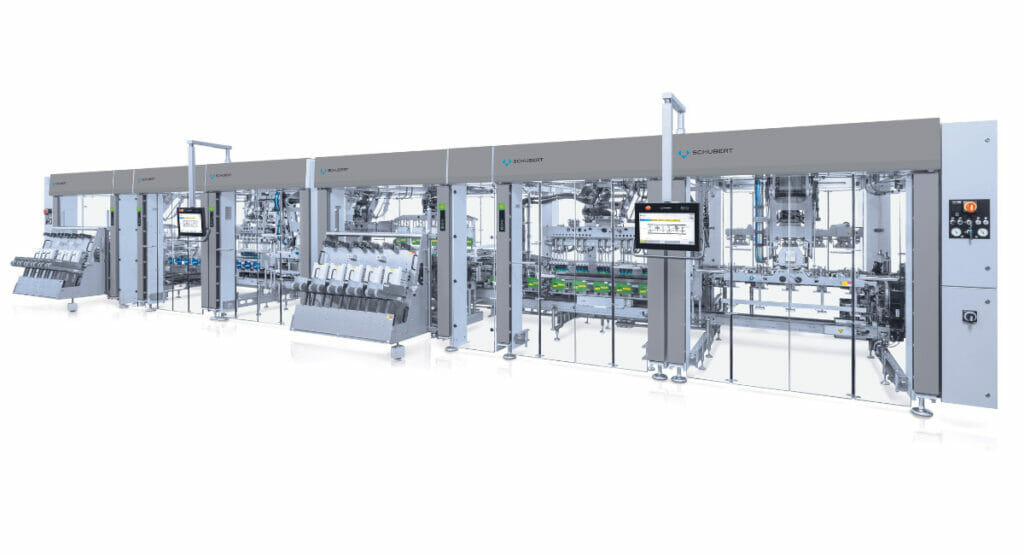
Folding boxes for chocolate biscuit enjoyment
Up to now, the „PiCK UP!“ bars were packed in tubular bags, grouped and labelled. In order to produce more sustainably, the company wanted to replace this secondary packaging with folding cardboard boxes in the future. Bahlsen was therefore looking for a new automation solution that would, above all, protect the sensitive biscuit bars from damage and breakage during the packaging process. In addition, the confectionery company decided on thinner films for the tubular bags in order to achieve material savings by reducing the amount of film.
This should also be possible with the machine update. Irrespective of the requirements for the packaging machine itself, Bahlsen also had special conditions with regard to the machine location: the space in the production was very limited due to many columns and low ceilings, so that a compact, narrow design of the line was required.
Two fully automated, flexible bar packers
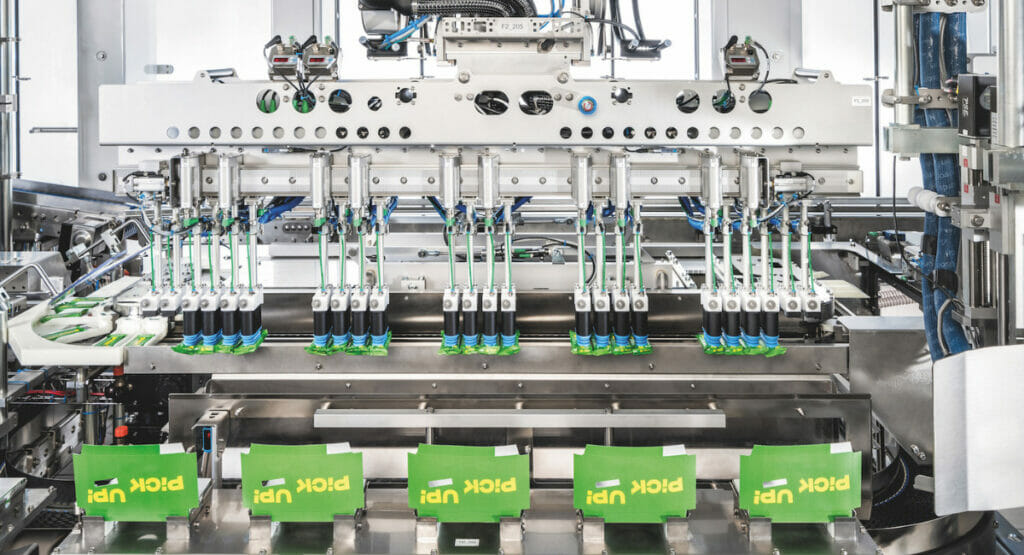
In order to master the many challenges, Schubert was involved in the packaging development of the folding boxes in this project. This enabled the packaging specialist to optimise the new packaging in the best possible way, especially with regard to machine runability. For example, the box blanks were designed with creasing and scoring lines for easy and fast erecting and the layout of the blanks was optimised. As a supplement to the previous production lines, Schubert finally designed a packaging system for its customer with two identical bar packers that are positioned one behind the other, take up little space in the hall and can pack independently of each other in parallel.
Efficient processes in the machine
The entire packaging process with the essential steps of erecting, filling and sealing now runs fully automatically in the system. Thanks to the robot technology and the use of the transmodule, Schubert guarantees an interface-free packaging process.
The gentle product handling and the controlled process from start to finish increase the efficiency of the line and minimise waste. At the same time, the redesigned folding boxes and the thinner films of the tubular bags enable the manufacturer to save the impressive amount of 112 tonnes of plastic per year. All in all, this means a big step towards sustainability for the biscuit manufacturer and meets the consumers‘ desire for more environmentally friendly packaging.
Robots work hand in hand
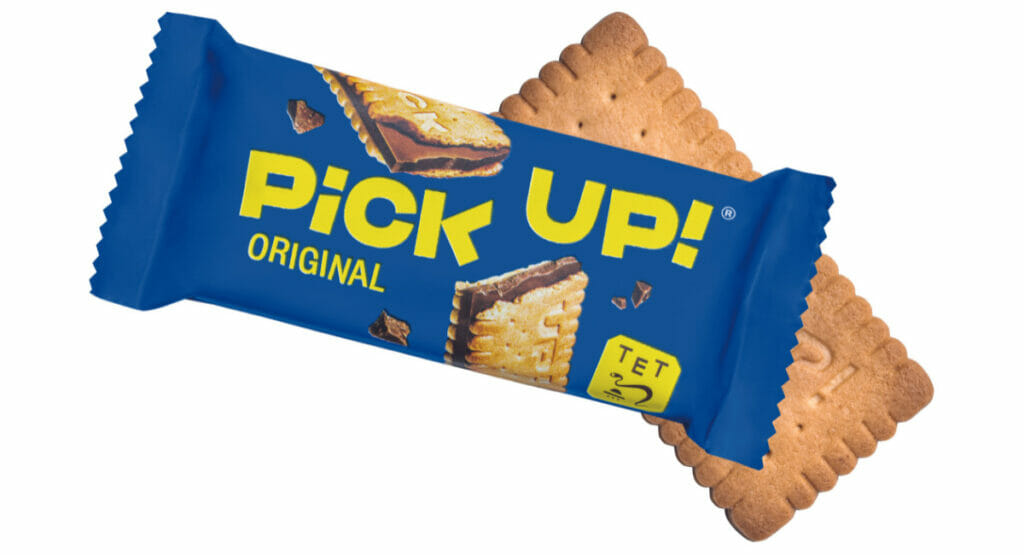
With the new packaging solution, the biscuit bars already packed in tubular bags are now placed in the secondary packaging in the bar packers, which each consist of three machine frames. First, the flat blanks are fed into the system via a magazine. Depending on the format, a robot removes up to six blanks from the magazine and transfers them to another robot that erects the cartons. The folded boxes are then placed on the transmodule transport robot and transported to the filling station. In parallel, the snack bars are fed into the process via a feeder and pre-grouped. A robot then picks up several bars at the same time with a suction pad and transports a predefined number of pieces, depending on the format, into the open boxes. The transmodule then moves them to the last step, the sealing. There, the sales packs are closed with a flap presser in a process specially designed for low boxes.
Double effect: sustainable and economical
The switch to cardboard, thinner foils and a new system not only improves sustainability, but is also very economical for Bahlsen. The high-performance solution can process up to 850 biscuit bars per minute. Thanks to the high working precision of the robots, which place the biscuit bars very precisely in the packages, the new packaging cartons could be designed without much empty space. In addition, the biscuit manufacturer can use a variety of formats for its specialities: Overpacks with eight different product arrangements are possible. A major format change is only necessary with a different pack base and can then be carried out in just 20 minutes.
Bahlsen is more than satisfied with the new system. After all, thanks to the wide range of box formats and heights and the ability of the robot-assisted machines to process an overcapacity of up to ten percent from the pre-process, the solution also impresses with its flexibility and efficiency. The fact that a machine with such high performance was designed by Schubert for a challenging location is equally appreciated by the company.
More packaging news
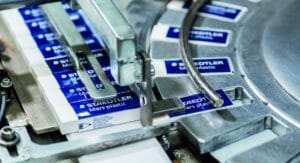
A contract with a handshake is valid
Managing director Tina Gerfer of Wilhelm Rasch Spezielmaschinenfabrik has modernized the company and successfully guided it through difficult times.
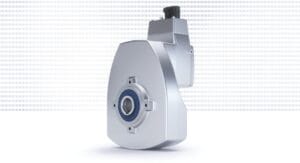
Asynchronous servo solutions for the packaging industry
From primary packaging to final packaging, electric drives play an important role. With a broad portfolio, Nord Drivesystems supports customers.
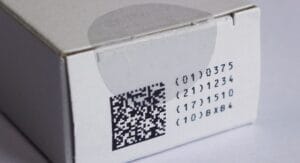
Label Durability
Labels offer many functions which can get lost due to label removal. PTS assesses labels and cardboard for durability and tamper evidence.
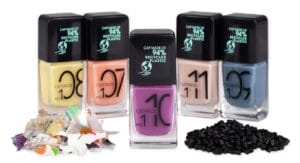
More design for recycling for cosmetics packaging
Packaging for decorative cosmetics is very special. The Forum Rezyklat calls for the recyclability of packaging to be taken into account when designing it.
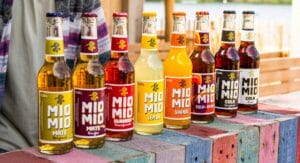
Innovation Barometer 2024
According to a survey conducted by Aktionsforum Glasverpackung 2024 is set to be a highly innovative year for glass packaging.
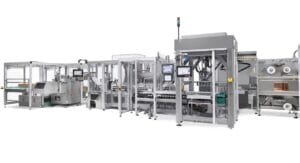
Flexible packaging system for natural cosmetics
Sustainability is part of Weleda’s identity. IWK is also contributing to this with its new flexible packaging line for many natural cosmetic products.