Mixed and contaminated plastic waste is the biggest challenge for recycling. Now, with Carboliq, a process is in large-scale use that converts plastic waste, for which incineration was previously the only disposal route, back into oil. The company of the same name operates a pilot plant in Ennigerloh and cooperates with Südpack.
Chemical recycling can be an important building block for the circular economy and should always be used when mechanical recycling reaches its limits. Südpack, the Swabian manufacturer of high-performance films for packaging food and medical goods, also sees it that way.
„As early as 20 years ago, my father, the company’s founder Alfred Remmele, had the vision that chemical recycling could be a future technology for the recovery of plastics that cannot be mechanically separated and recycled. Since the state of the art was not yet fully developed at that time, it initially remained with this vision.“
Johannes Remmele, Südpack owner
At that time, the company’s portfolio consisted of far more composite films. In recent years, Südpack has greatly expanded the share of recyclable monostructures, but composite films are still indispensable for many applications. „The much-discussed ‚waste problem‘ that is commonly generated by the production of precisely this packaging is only one aspect – and does not go far enough,“ says Johannes Remmele. „Südpack does not produce waste, but high-quality functional films that make a significant contribution to the protection of food and pharmaceuticals. Films only become waste if it is not possible to set up suitable systems with which these materials can be recycled. And it is precisely for this reason that chemical recycling as a complementary technology is an essential building block.“
Future-proof technology
Südpack has therefore entered into a strategic cooperation with Carboliq, the chemical recycling division of the Remscheid-based company Recenso. The goal: to use the pilot plant for oiling plastic waste, which is operated in cooperation with the waste management company Ecowest in Ennigerloh, Münsterland, to recycle the company’s own streams of recyclable materials that are produced during the manufacturing process of packaging films. The cooperation project has already shown how a plant must be designed to process the different fractions so that they do not have to be sent for thermal recycling. „From today’s point of view, Carboliq is a unique and, above all, future-proof technology – not only in terms of recycling possibilities, but also in terms of energy efficiency and low immission levels,“ Remmele said. „This makes us the only manufacturer of flexible films that has direct access to capacities for chemical recycling. Even more: in combination with our site in Schwendi, where capacities for mechanical processing are available, we are always able to apply the technology that is better in terms of environmental impact and economic efficiency.“
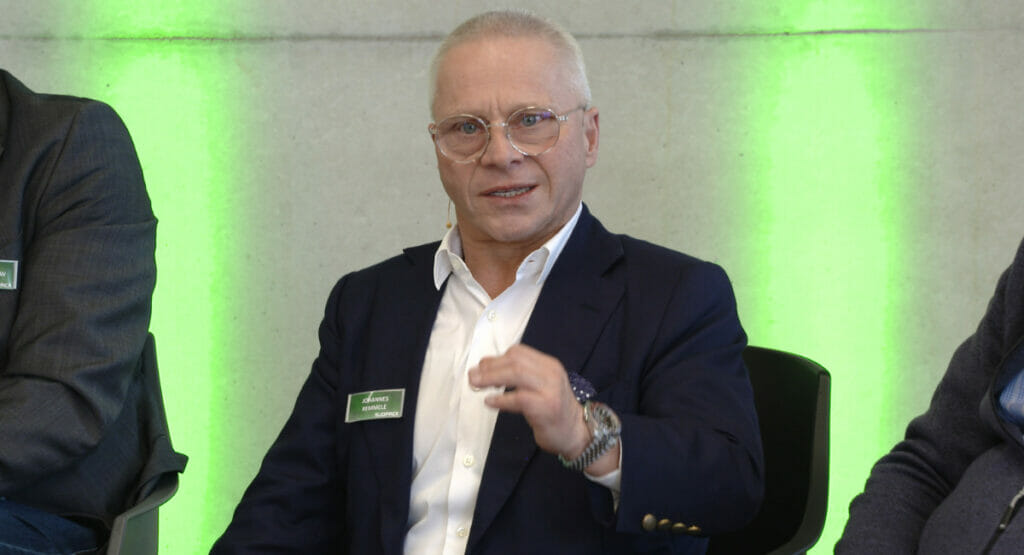
Dirk Hardow, Head of Business Unit Functional Films & Compounds at Südpack, is also convinced: „In the future, it will only be possible to close the loops for food packaging with mechanical and chemical recycling„. In the course of the cooperation with Carboliq, the company has already been able to prove that multi-layer films can be successfully recycled with the process. „The technology is robust and ready for the market.
New plant planned near Cologne
In the material recycling process of direct oiling, the waste material is liquefied in a single-stage process – at process temperatures below 400 °C, the process achieves a high oil yield. The Carboliq process is operated by friction, i.e. by frictional heat. Special rotating units were developed for this purpose, which bring the required energy directly into the material. This circulates in the reactor until the chain lengths are so short that the material evaporates. The vapours are condensed and the condensate is fed into an oil-water separator for phase separation. Carboliq then markets the liquid product under the name CLR (Circular Liquid Resource).
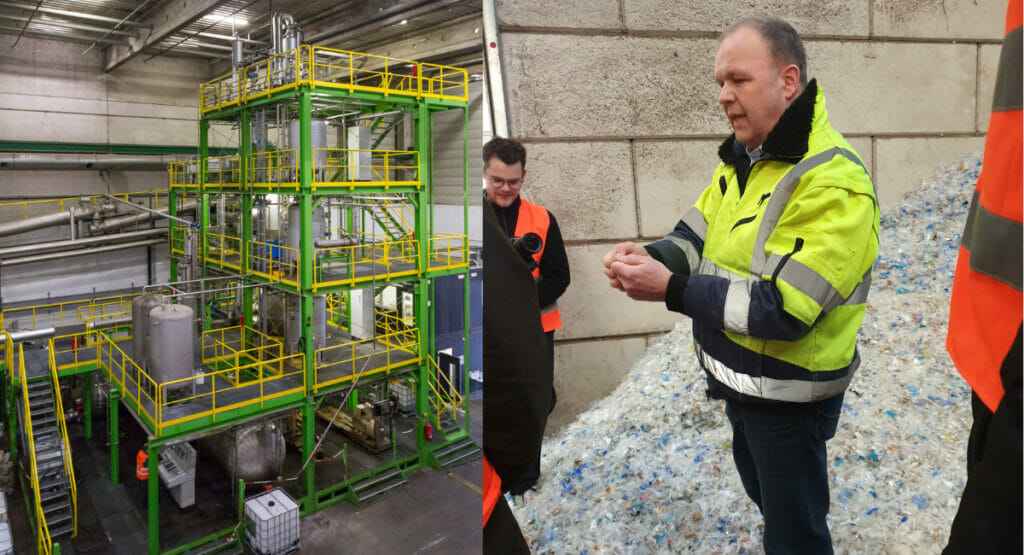
The pilot plant in Ennigerloh has been approved as a recycling plant for fully continuous operation and has been certified according to the ISCC-Plus sustainability criteria since March 2021. And Carboliq already has further plans: „An investment decision is expected to be made soon for the construction of a new plant south of Cologne. It is to be designed for a capacity of 10,000 tonnes of output per year and come onto the market with the first products in 2025,“ explains Carboliq CEO Christian Haupts and calculates: „In Germany alone, more than six million tonnes of plastic waste are generated and treated every year. Statistically, about half is used for energy and materials. If even half of the plastics destined for incineration are reprocessed using the Carboliq process, the recycling rate for plastics increases by more than 50 per cent, CO2 emissions from incineration are reduced by more than 40 per cent and there is a revenue potential from the sale of CLR of more than two billion euros.“
Chemical recycling offers many possibilities
The technology shows a high tolerance to impurities and grade mixtures. Therefore, the Carboliq process is suitable for a wide variety of plastics, including contaminated, mixed or other plastics. As well as for flexible packaging and for the recycling of highly complex multi-layer films made of several types of plastic, which are commonly used in the food industry in particular. „Compared to mechanical recycling, chemical recycling thus offers significantly more possibilities, as it aims at recovering the valuable material components through thermal decomposition. However, we need to know the composition of the infeed in order to run a plant optimally and end up with materials that can be processed in large-scale chemical industrial plants like a cracker,“ says Christian Haupts.
More packaging news
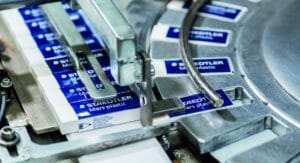
A contract with a handshake is valid
Managing director Tina Gerfer of Wilhelm Rasch Spezielmaschinenfabrik has modernized the company and successfully guided it through difficult times.
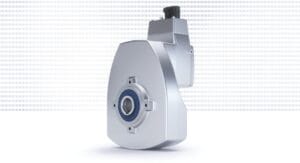
Asynchronous servo solutions for the packaging industry
From primary packaging to final packaging, electric drives play an important role. With a broad portfolio, Nord Drivesystems supports customers.
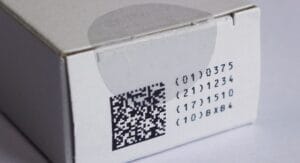
Label Durability
Labels offer many functions which can get lost due to label removal. PTS assesses labels and cardboard for durability and tamper evidence.
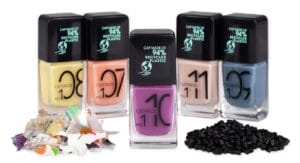
More design for recycling for cosmetics packaging
Packaging for decorative cosmetics is very special. The Forum Rezyklat calls for the recyclability of packaging to be taken into account when designing it.
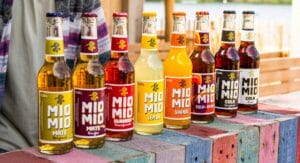
Innovation Barometer 2024
According to a survey conducted by Aktionsforum Glasverpackung 2024 is set to be a highly innovative year for glass packaging.
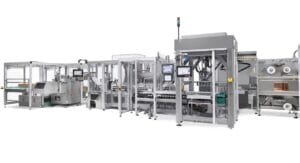
Flexible packaging system for natural cosmetics
Sustainability is part of Weleda’s identity. IWK is also contributing to this with its new flexible packaging line for many natural cosmetic products.