IWK is considered a pioneer in mechanical engineering and was the first company to invent a packaging system for filling and sealing tubes in 1893. This spirit of innovation forms the DNA of the company, which today is known as a guarantor of quality in tube filling and cartoning systems. With energy-efficient technology, digital services and a modern packaging laboratory, it contributes to the conservation of resources.
IWK Verpackungstechnik, based in Stutensee in Baden-Württemberg, is a globally active medium-sized manufacturer of packaging systems. More than 550 people work in the IWK Group and contribute their many years of knowledge and expertise. In addition to the production facility in Germany, IWK maintains a plant in Thailand as well as service and sales bases across several continents. This year, the economically well-positioned company looks back on 130 years of eventful and moving history, all while continuing to move forward into the future with excitement and joy.
The tube makes the difference
28 July 1893 is the founding date of today’s IWK Group. It was on this day that Willem Karel van Dedem, Dutch colonial minister in The Hague, ordered machines and equipment from the company for filling and sealing tubes of an opium factory in what is now Indonesia. The filling product was an opium paste used as an analgesic ointment for wounds. The idea of packaging pharmaceuticals and subsequently cosmetics was born and caught on.
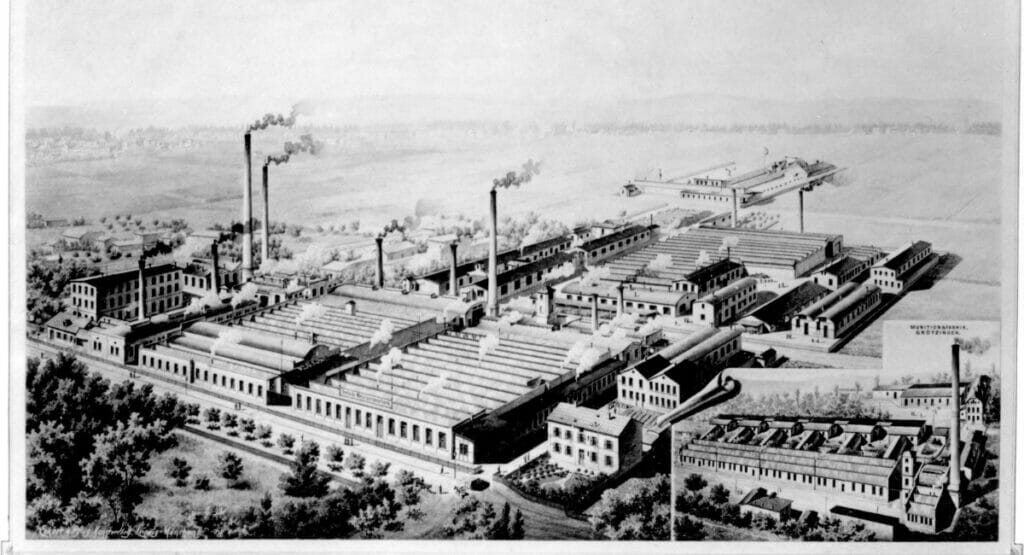
At the beginning of the 20th century, the first luxurious department stores‘ palaces in Germany’s metropolises made shopping an experience. Consumer goods were in demand, cosmetics were in high demand and, of course, these all had to be packaged. The demand for corresponding machines increased accordingly, especially as the cosmetics and pharmaceutical industries discovered the tube, which had previously been used mainly for artists‘ supplies, as a practical functional packaging. So-called beauty creams and especially toothpaste, which came onto the market in Europe and the USA at about the same time, made the tube more and more popular as a means of packaging.
Courageous new beginning
130 years of company history are a time full of changes, innovations and also disruptions. During the two world wars in the first half of the 20th century, civilian production was discontinued.
The entrepreneur Günther Quandt succeeded in making a new start. In Karlsruhe, the first steps were taken to resume the former civilian production programme piece by piece. One of the first orders for packaging machines after the war was a type T 1a tube filling and closing machine. The breakthrough in the field of packaging machines came in 1955 with the development of the first fully automatic packaging line for tubes, consisting of the tube filling and closing machine TF 2 and the cartoning machine K 4, for filling toothpaste and packing it into the folding box.
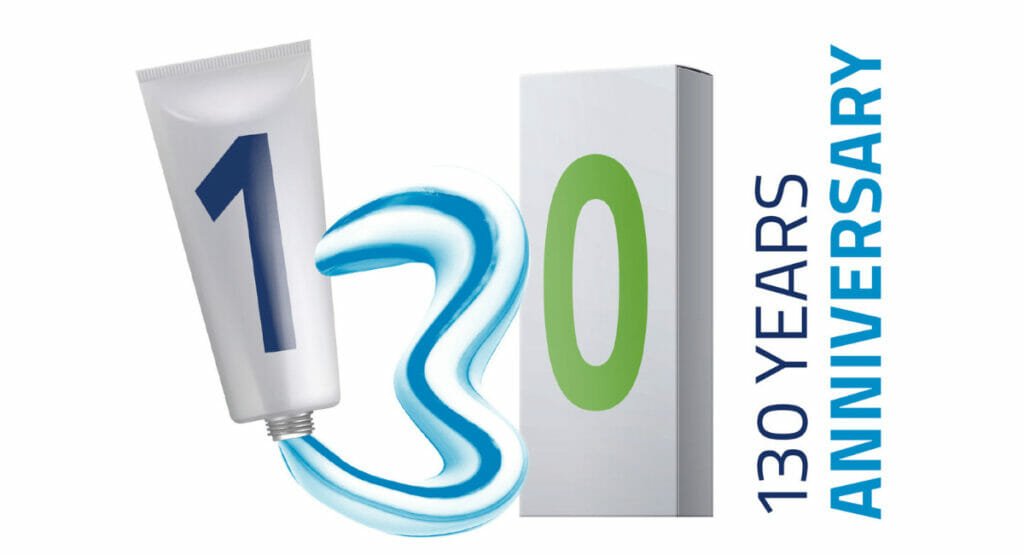
A strong brand
The economic miracle at the beginning of the 1960s in Germany brought growth and prosperity, especially in Karlsruhe. The range of goods expanded, and with it the manufacturers‘ expenses for design, packaging and advertising increased. In the 1960s, there was hardly a cosmetic, pharmaceutical, bakery or confectionery product that was not filled or packaged by IWK machines.
In 1970, KuKa GmbH merged with IWK to form „Industriewerke Karlsruhe Augsburg AG“ – IWKA for short. The company experienced a sustained growth spurt in 1979 when it moved from the centre of Karlsruhe to Stutensee-Blankenloch, just nine kilometres away. This is where the current company headquarters were built, with a production area of 11,000 square metres and 8,000 square metres of administrative space. In the 2000s, IWK introduced cycle assembly, which led to an increase in productivity and larger quantities of tube fillers and cartoners. In 2007, the sale followed and IWK was managed under the umbrella brand OYSTAR. Since 2013, IWK has belonged to the globally active ATS Corporation based in Canada and today presents itself as a globally operating company.
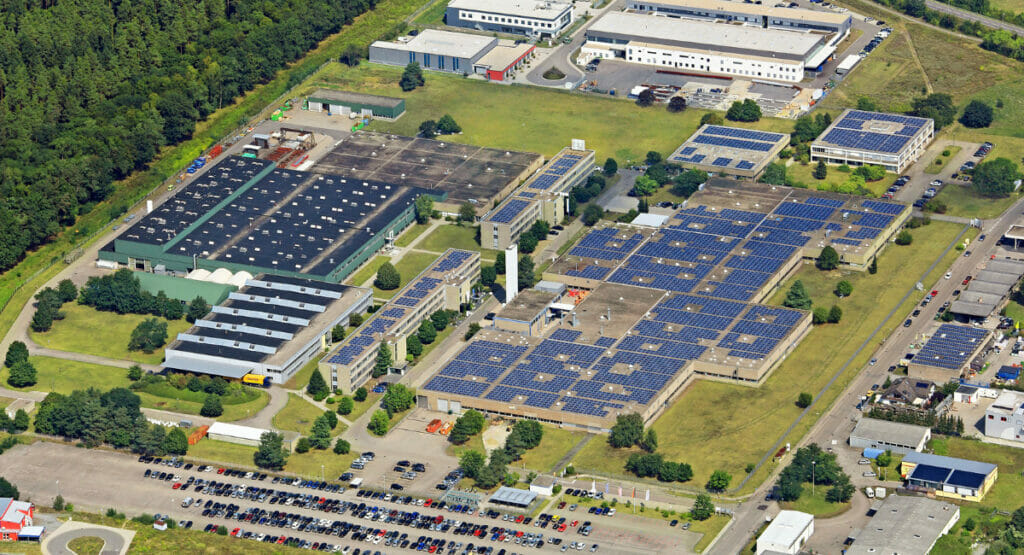
Great experiential knowledge then and now
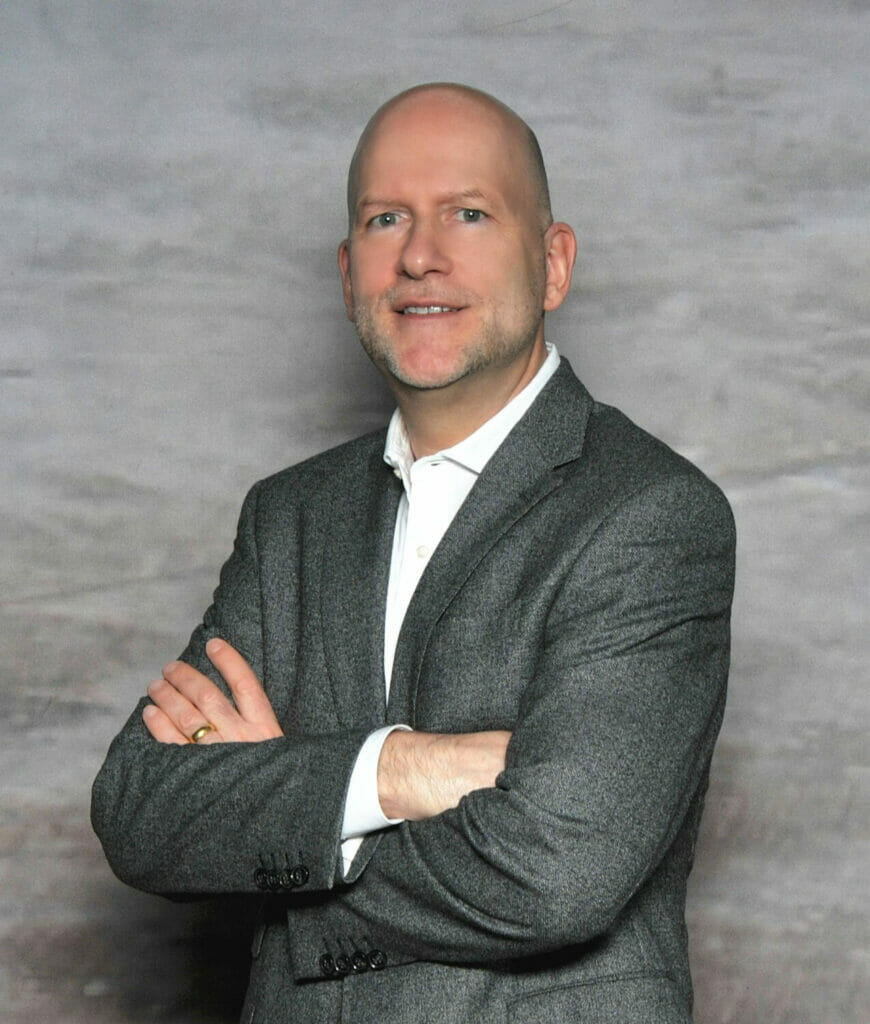
„The technical know-how gained over a century from thousands of high-quality packaging systems for filling, closing and cartoning make IWK a solution provider with a wealth of experience and a reliable and competent partner. No matter what products require a suitable packaging solution, IWK manufactures and installs individual systems or entire turnkey lines that are precisely adapted to the respective customer requirements and run reliably.“
Dr Heinrich Sielemann, President of the IWK Group
The IWK experts have mastered the complex technical processes involved in packaging sensitive products from numerous industries. The know-how acquired over the decades in the packaging sector is the basis for success. The packaging systems are mainly used in the pharmaceutical and cosmetic sectors and for food and industrial applications. Incidentally, it was also IWK that realised the technical solution for exact stripes in toothpaste.
Modular for many uses
The portfolio of modular packaging systems is broad. From the entry-level range to the high-end version, everything is possible. IWK has solutions in its range where format changeover takes place within a few minutes. Changeover times, such as for changing packaging sizes and formats, are therefore short and the productivity of the production lines is therefore high.
Collaborative robots (cobots), can be used upstream and downstream and expand the automation of packaging processes. IWK was the first machine manufacturer in its field to pioneer the integration of cobots into production together with the employers‘ liability insurance association. Today, it is impossible to imagine uninterrupted production without cobots.
„With the market launch of the newly developed Toploader TL cartoning machine, IWK combines many technical innovations. The system is designed for the gentle packaging of sensitive pharmaceutical and medical technology products in complex box structures,“ explains Dr Heinrich Sielemann. The compact design enables flexible packaging in the smallest of spaces and thus has a space requirement that is 30 per cent significantly smaller than comparable packaging systems on the market.
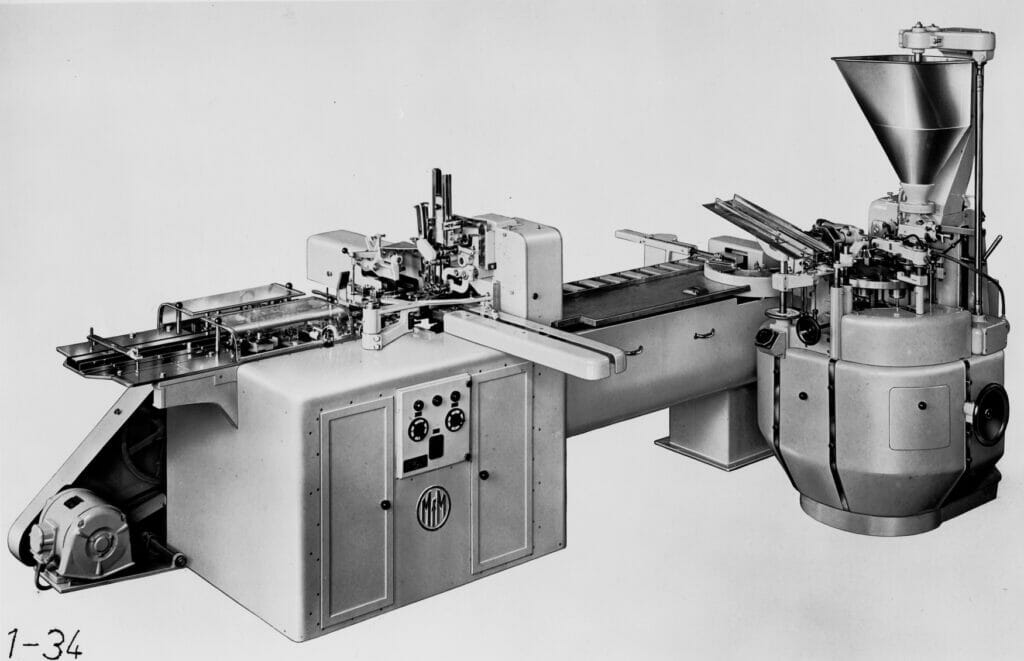
Sustainable in many areas
The topics of sustainability and resource conservation are important issues by which companies are measured worldwide. Certainly, successful entrepreneurs have already paid attention to economic efficiency and thus also to sustainability in the past. Comparable standards, such as the EcoVadis label, according to which IWK is certified, have only been around for a short time. The company takes important criteria into account when developing packaging systems, such as minimising energy consumption, the possibility of processing new types of packaging materials and considering all aspects of recycling. A concrete example here is the process-safe filling and closing of recyclable paper tubes. „In general, packaging will continue to be a key differentiator for brands. Due to consumer pressure and legislation, packaging will become more sustainable,“ emphasises Dr Heinrich Sielemann.
The company also seeks and finds ways to conserve resources in digital ways. Digital services bring customers and experts together in real time, which reduces travel and thus the CO2 footprint. The myIWK customer portal shortens communication channels and speeds up services.
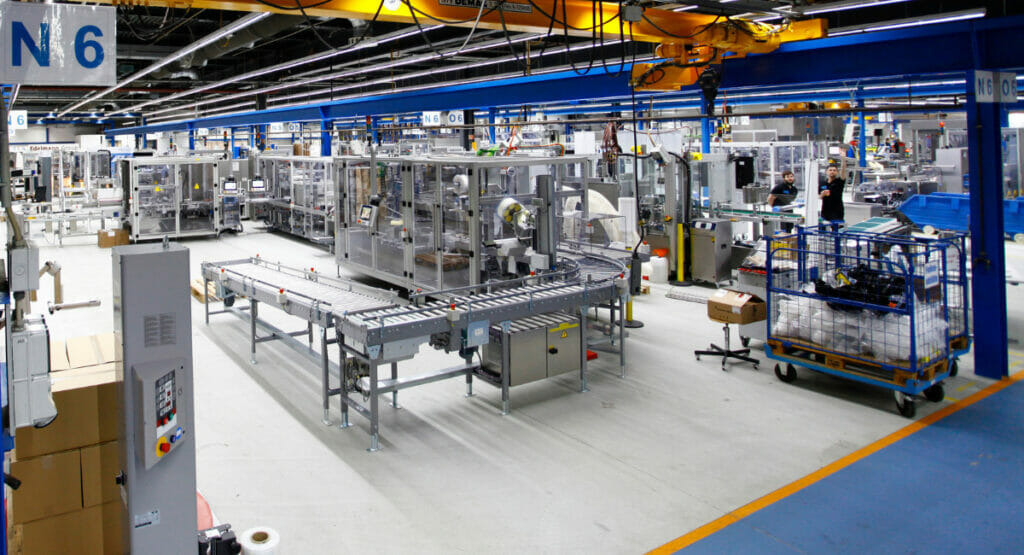
Changes as challenges
Innovations are the key to first-class technical solutions. This applies in particular to ever more extensive customer requirements and applications with special properties. Experts at IWK’s Packaging Competence Center PAC2 provide far-sighted advice and guide customers safely through the optimisation of their existing packaging or their new development. Thanks to many years of know-how in mechanical engineering, IWK engineers find the tailor-made packaging system for all technical requirements.
„We will see some changes in our industry. The topics of sustainability and energy efficiency will continue to challenge us and drive our developments.“
Dr Heinrich Sielemann
This pioneering spirit, combined with in-depth know-how and reliable service, is appreciated by IWK’s customers worldwide – since 1893.
More packaging news
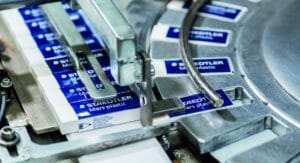
A contract with a handshake is valid
Managing director Tina Gerfer of Wilhelm Rasch Spezielmaschinenfabrik has modernized the company and successfully guided it through difficult times.
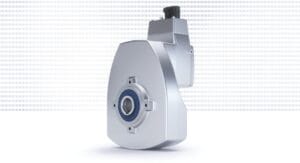
Asynchronous servo solutions for the packaging industry
From primary packaging to final packaging, electric drives play an important role. With a broad portfolio, Nord Drivesystems supports customers.
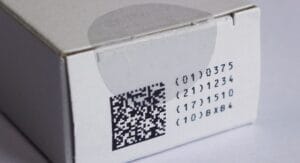
Label Durability
Labels offer many functions which can get lost due to label removal. PTS assesses labels and cardboard for durability and tamper evidence.
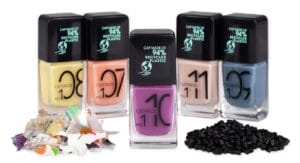
More design for recycling for cosmetics packaging
Packaging for decorative cosmetics is very special. The Forum Rezyklat calls for the recyclability of packaging to be taken into account when designing it.
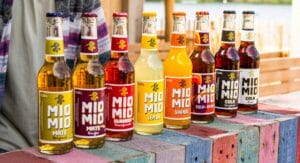
Innovation Barometer 2024
According to a survey conducted by Aktionsforum Glasverpackung 2024 is set to be a highly innovative year for glass packaging.
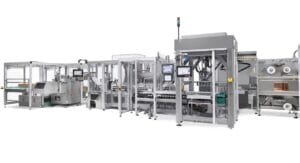
Flexible packaging system for natural cosmetics
Sustainability is part of Weleda’s identity. IWK is also contributing to this with its new flexible packaging line for many natural cosmetic products.