The offset printing company Offsetdruckerei Schwarzach wanted to increase their hourly output in hot foil stamping. Now the company is the location for a beta test of the Novafoil 106 by Bobst. The machine can apply foil in both directions – inline and across the sheet running direction.
„We use the Novafoil 106 for long runs with boxes which have large surfaces that need to be embellished. The machine gives us very high productivity with impressive finished product quality,” the company’s CEO Johannes Knapp says, as he sums up the company’s experience with the new Bobst hot foil stamping machine.
He thinks the newly developed platen press is the highlight of the machine. With this, Bobst has increased the dwell time between the die with the foil and the sheets. The longer dwell time combined with an even temperature and a higher pressure perfectly enhance the high quality of the embellishment. This applies to delicate finishes as well as large-area embellishments.
“We’d been hoping that the innovative technology in the Novafoil 106 would help us increase hourly output in hot foil stamping. That’s exactly what happened. Depending on the complexity of the finish, the machine easily operates at speeds of up to 8,000 sheets per hour for large runs.”
Johannes Knapp
At all speeds, the sheets travel through the machine with absolute stability. To make that possible, Bobst adapted the gripper bar advance system to ensure even sheet travel with optimal sheet delay. In addition, the latest-generation feeder ensures constant sheet feeding and the highest register precision. For embossing, debossing or hot foil stamping, stable sheet travel is also a key factor in flawless quality and productivity.
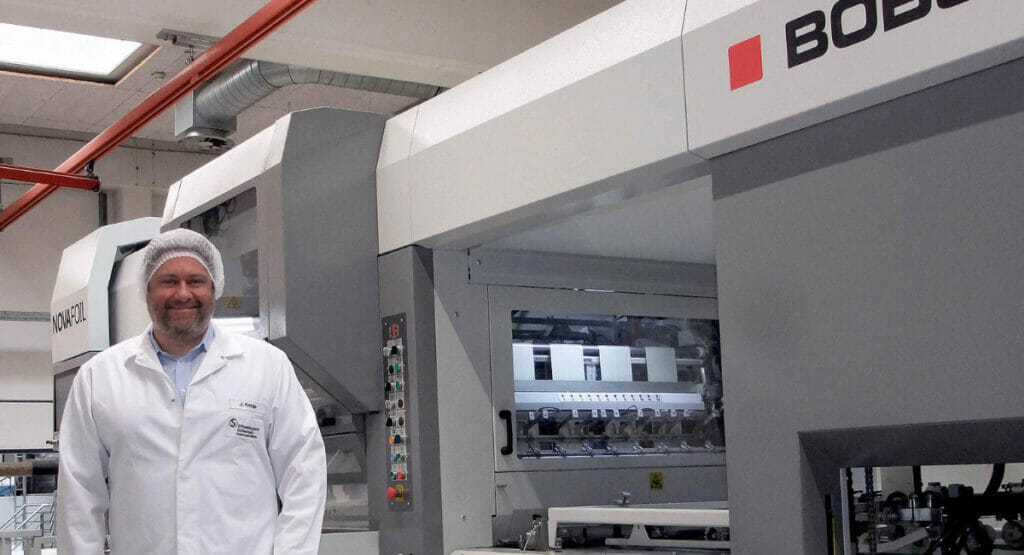
The Novafoil 106 is the first hot foil stamper from Bobst that can apply foil in both directions: inline and across the sheet running direction. The machine configuration allows hot foil stamping with up to eight reels for line and four reels for cross-foiling. This allows production of highly sophisticated packaging designs in a single machine run. The machine at the Schwarzach facility is equipped with all 12 foil reels.
“With the new hot foil stamping machine, we can run different colors inline and cross-foil. Moreover, the eight inline foil reels give us flexible options for optimizing the foil advance. On certain jobs, the use of cross foiling helps us to further optimize the foil advance and reduce foil consumption even more. Depending on the job, we may have 30 per cent to 40 per cent lower foil consumption than before.”
Johannes Knapp
Offsetdruckerei Schwarzach also achieves these savings by using the OACS system (Optimal Advance Computer System) which automatically calculates the ideal foil advance. Bobst has included this system as an option on the Novafoil 106. “The calculations are flawless. So far, there’s been no complaint that too much or too little foil was provided,” Knapp affirms.
The higher production speed also allows more sheets to be processed with the same energy consumption. “Calculated at 1,000 sheets, this machine uses 20 per cent less electricity. This is another way in which it supports our sustainability strategy,” Knapp explains.
Easy handling for machine operators
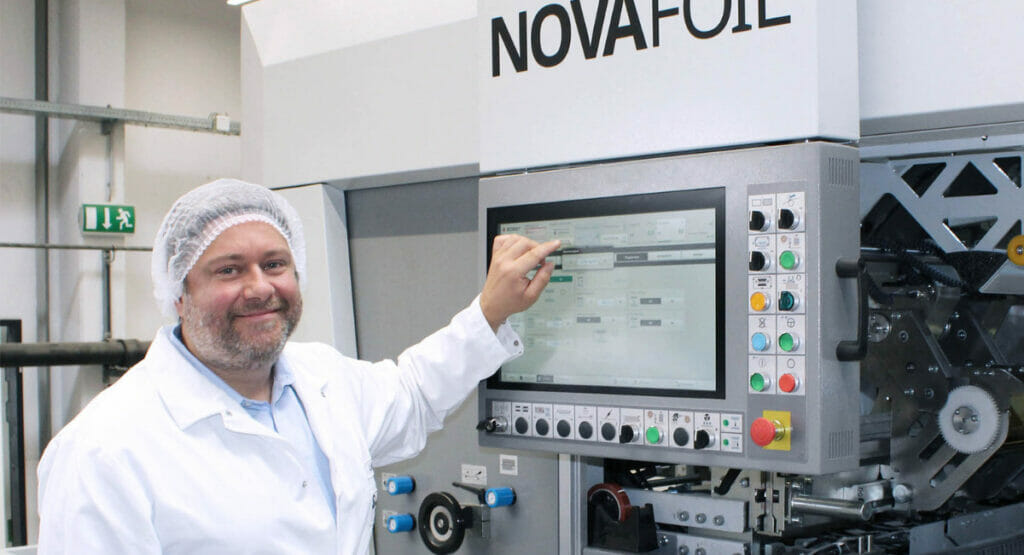
A specially developed lift system for heavy foil reels facilitates the work of machine operators, as they do not have to lift the reels into the machine. With this, and the high level of automation associated with the Novafoil 106 – for example with the semi-automatic foil reel change – setup and changeover times have been shortened.
The Sphere human-machine interface provides easy, intuitive navigation through the functionalities. Repeat orders are up automatically. Ergonomics and user-friendliness allow easy access to all functions and settings, including the platen section. For quality control, operators can safely and easily remove samples from the machine without stopping it.
“Of course, from an economic point of view, we also need mass production business — which requires technology that allows the highest quality and efficiency. Even in that regard, the Novafoil 106 fits seamlessly into our process.”
Johannes Knapp
The same goes for the machine’s 1,060 x 760 mm sheet format, which the packaging manufacturer also prints and cuts. They generally use the Novafoil 106 to process solid cardboard in weights of 300 to 400 g/m2. That includes recycled cardboard.
Source: Bobst
More packaging news
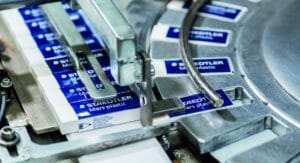
A contract with a handshake is valid
Managing director Tina Gerfer of Wilhelm Rasch Spezielmaschinenfabrik has modernized the company and successfully guided it through difficult times.
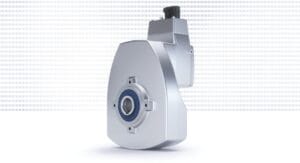
Asynchronous servo solutions for the packaging industry
From primary packaging to final packaging, electric drives play an important role. With a broad portfolio, Nord Drivesystems supports customers.
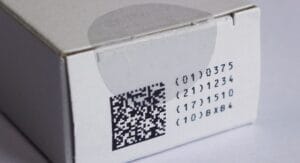
Label Durability
Labels offer many functions which can get lost due to label removal. PTS assesses labels and cardboard for durability and tamper evidence.
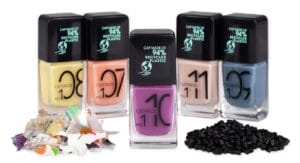
More design for recycling for cosmetics packaging
Packaging for decorative cosmetics is very special. The Forum Rezyklat calls for the recyclability of packaging to be taken into account when designing it.
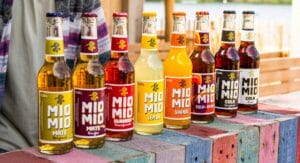
Innovation Barometer 2024
According to a survey conducted by Aktionsforum Glasverpackung 2024 is set to be a highly innovative year for glass packaging.
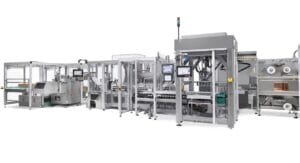
Flexible packaging system for natural cosmetics
Sustainability is part of Weleda’s identity. IWK is also contributing to this with its new flexible packaging line for many natural cosmetic products.