Geht es um das Zuführen, Positionieren, Spenden, Zählen, Vereinzeln von Papier und flachen Produkten, bietet die Kraus Maschinenbau GmbH aus Spaichingen die für die jeweilige Aufgabenstellung passende Lösung. Jetzt haben die Spezialisten in enger Zusammenarbeit mit den Entwicklern der Universität Jena eine Maschinenkombination entwickelt, die den erfolgreich erprobten Corona-Antikörper-Prüftest verpackt.
Mit den Anlagen und Komponenten für Zuführ- und Vereinzelungssysteme des Unternehmens lassen sich einzelne Papierbögen, Etiketten, Broschüren, Booklets, Faltschachteln, ISO-Karten (z. B. Kunden- und Wertkarten), aber auch Kunststoffprodukte, Warenproben und Sachets bis zu 30 Millimeter Dicke handhaben. Geht es um den Verpackungsprozess selbst, sind es Karton- und Faltschachtelzuschnitte, die vereinzelt und dabei für weitere Veredelungsschritte (Zählen, Drucken, Prägen, Prüfen) bis hin zur Sicherheitscodierung vorbereitet werden können. Alle Maschinen und Anlagen von Kraus stehen für Zuverlässigkeit sowie eine einfache und sichere Bedienbarkeit.
Standard- und Sonderlösungen
Häufig finden potenzielle Kunden schon bei den Standardgeräten eine wirtschaftliche und zuverlässige Lösung für die jeweilige Anwendung. Geht es um komplexe Anforderungen und neue Problemstellungen, wird die Aufgabenstellung im Projektgespräch analysiert, diskutiert und in der Umsetzung für den größtmöglichen Kundennutzen ausgelegt.
Jetzt wurden binnen kürzester Zeit zwei Maschinen so kombiniert und spezifiziert, dass erst entsprechende Teststreifen für den sogenannten Antikörpertest geschnitten, bereitgestellt und dann gemeinsam mit einer Testkassette in einen Kunststoffbeutel verpackt werden.
Nachgefragt: Joachim Kraus im Interview
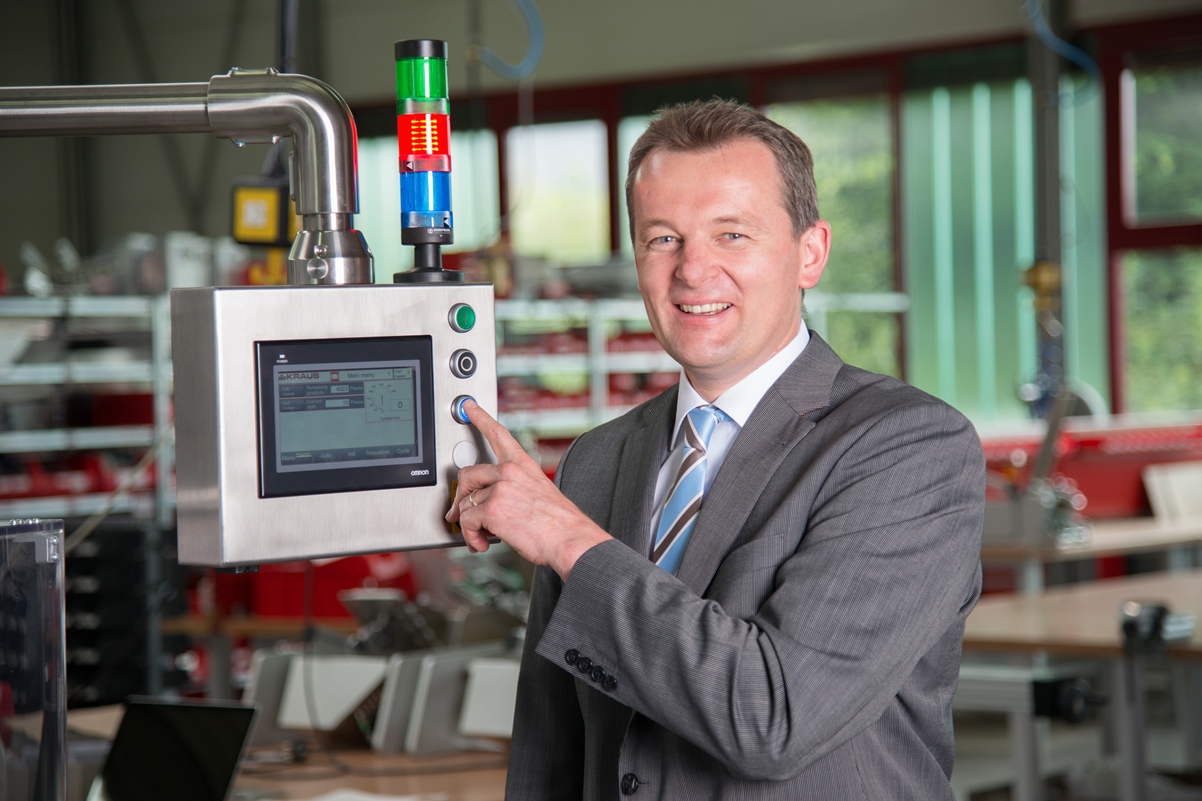
Joachim Kraus, Geschäftsführer der Kraus Maschinenbau GmbH (Bild: Kraus Maschinenbau)
Um mehr über das hochaktuelle Projekt zu erfahren, das in diesen Tagen vor dem Abschluss steht, haben wir mit Joachim Kraus, dem Geschäftsführer der Kraus Maschinenbau GmbH, gesprochen.
pj: Herr Kraus, neben Ihren Standardmaschinen und Komponenten entwickeln und bauen Sie auch Maßkonfektion für die besonderen Bedürfnisse und Anforderungen des Marktes. Bestes Beispiel die Maschine zum Vereinzeln und Verpacken der neuen Corona-Test-Kits. Wie ist dieses Projekt in Gang gekommen?
Joachim Kraus: Unser Kunde, die Firma Senova, war auf der Suche nach einer Lösung für das Zuführen der Verpackungspouches. Gemeinsam mit dem Kunden wurde ein Gesamtkonzept für das Zuführen und Verpacken der Testkassetten für den Antikörper-Schnelltest entwickelt, das auf Anhieb überzeugte. Die aktuelle Situation erfordert eine schnelle Auslieferung. Dementsprechend straff war der Zeitplan, auf den wir uns verständigten, bevor uns der Auftrag für eine Maschine zum Verpacken von Testkassetten erteilt wurde.
Beim Design Review der Maschine ergab sich weiteres Potenzial für die Zusammenarbeit: das maßgenaue Zuschneiden der Teststreifen, die Übergabe des Abschnitts und das Einsetzen des Zuschnitts in die Testkassette. Bei einer Größe zwischen 3,5 und fünf Millimeter erwies sich das Handling der Zuschnitte als Herausforderung. Nach dem Motto: „Geht nicht, gibts nicht!“: Das Produkt wird also nicht nur von einer Maschine von Kraus Maschinenbau verpackt werden, sondern auch das Vorprodukt auf einer unserer Applikationen hergestellt.
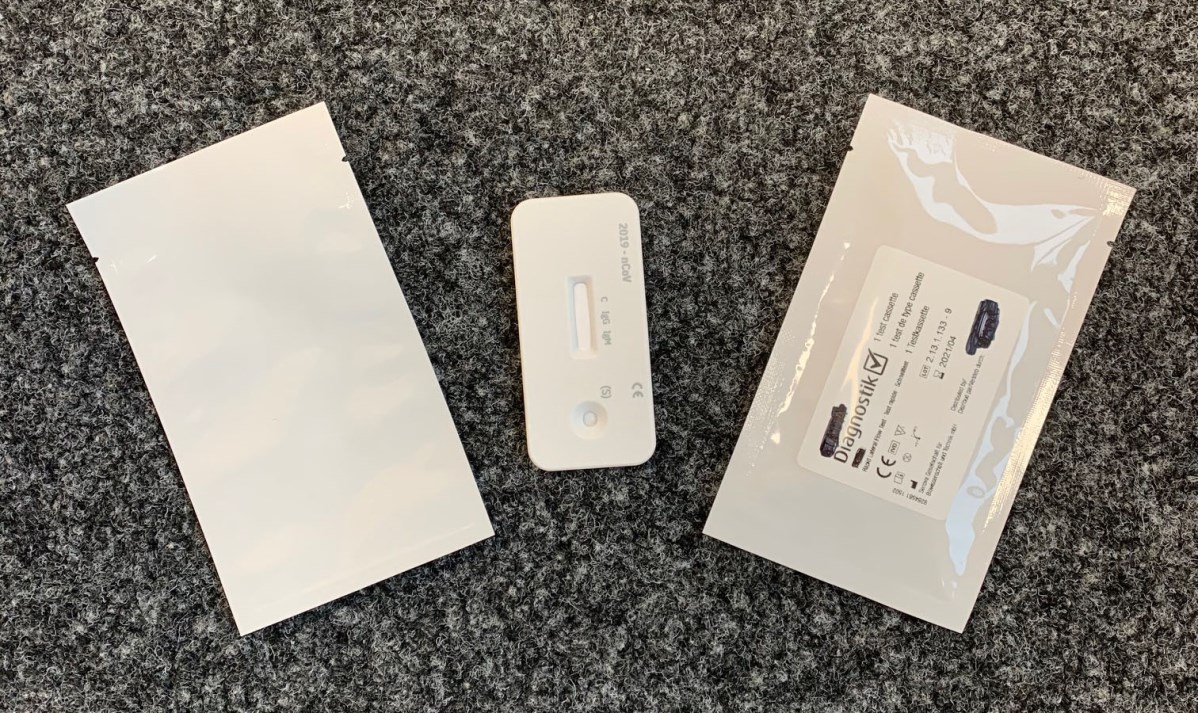
Muster für Beutel und Testkassette. (Bild: Kraus Maschinenbau)
pj: Wie arbeiten die Maschinen?
Joachim Kraus: Die Vorprodukte zur Herstellung der Teststreifen werden von unserem Reibanleger JoKer auf die Linie zugeführt. Die etwa 500 Millimeter langen Zuschnitte des Ausgangsmaterials werden prozesssicher vereinzelt, positioniert und anschließend in einer Servolineareinheit abgelegt. Über das HMI an der Maschine kann das Schnittmaß für verschiedene Arten von Covid-19-Tests definiert werden. Durch einen exakten Vorschub wird das Produkt unter dem Schnittmesser positioniert und der Streifen passgenau geschnitten.
Ein ausgeklügeltes Übernahmesystem positioniert den Abschnitt zur Übernahme durch einen Roboter. Dieser setzt den Zuschnitt dann in die Testkassette ein. Beim Kunden erfolgen weitere Prozessschritte, um aus den von der Kraus-Applikation zugeschnittenen Vorprodukten den funktionsfähigen Antikörper-Schnelltest zu machen.
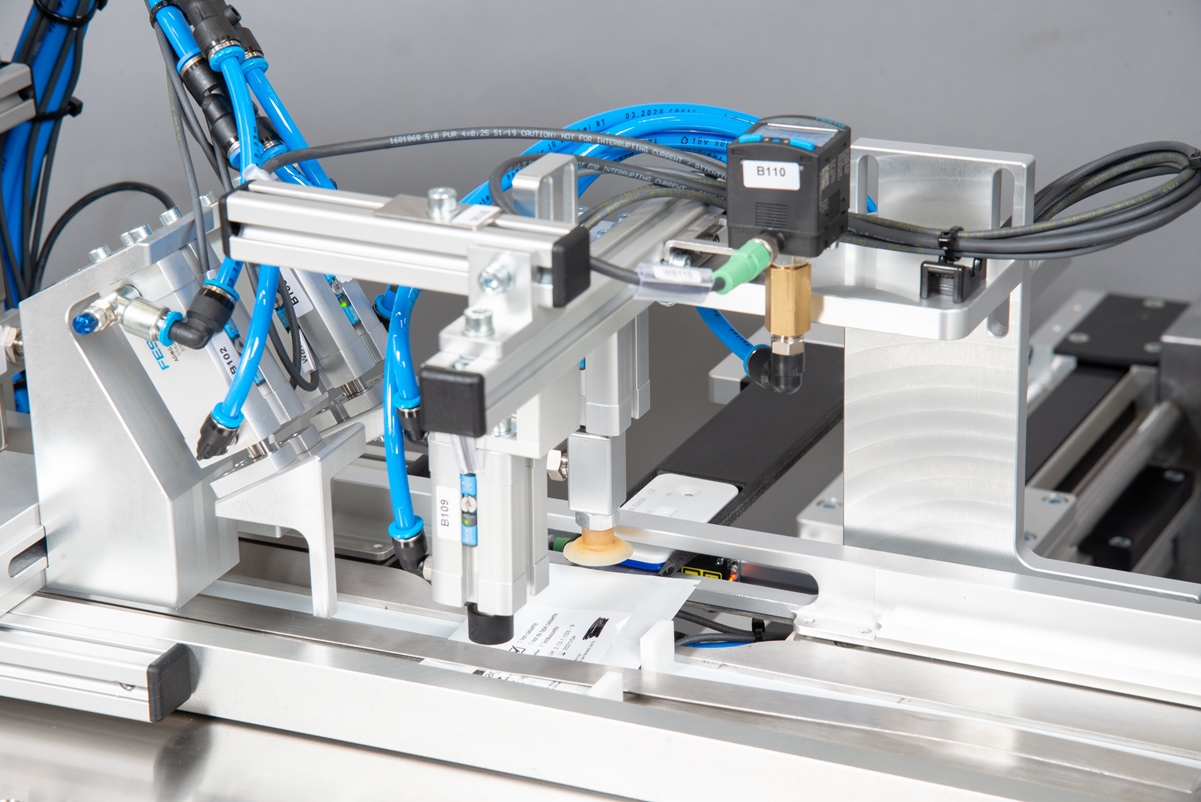
Die Testkassette wird in den Beutel geschoben. (Bild: Kraus Maschinenbau)
Die Maschine zum Verpacken der Antikörper-Schnelltests übernimmt anschließend die Testkassetten. Die vorkonfektionierten Beutel werden über einen JoKer vereinzelt und in die Verpackungsmaschine gespendet. Im Durchlauf werden Etiketten mit den produktrelevanten Daten produziert und auf den Pouch appliziert, der dann über Vakuumsauger geöffnet und in Position gebracht wird.
Ein Roboter übernimmt die Testkassette von der Vormaschine und übergibt sie in eine Kunststoffform. Diese wird in den Pouch eingeschoben. Die Komplexität der Kunststoffform hatte zur Folge, dass auf ein 3-D-Druckverfahren zurückgegriffen werden musste. An der letzten Station der Verpackungsmaschine wird der Beutel durch thermisches Schweißen verschlossen.
pj: Wie viele Test können pro Minute/pro Stunde verpackt werden?
Joachim Kraus: Die Maschine stellt 30 Verpackungen pro Minute her. Diese Taktung resultiert aus der Verknüpfung mit der Vormaschine und der Übergabe an den Roboter. Im Bereich der Beutelzuführung haben wir mit unserem Reibanleger JoKer bereits Anwendungen installiert, mit denen bis zu 300 Takten pro Minute realisiert werden. Welche Leistung möglich/nötig ist, hängt immer von den Kundenspezifikationen ab.
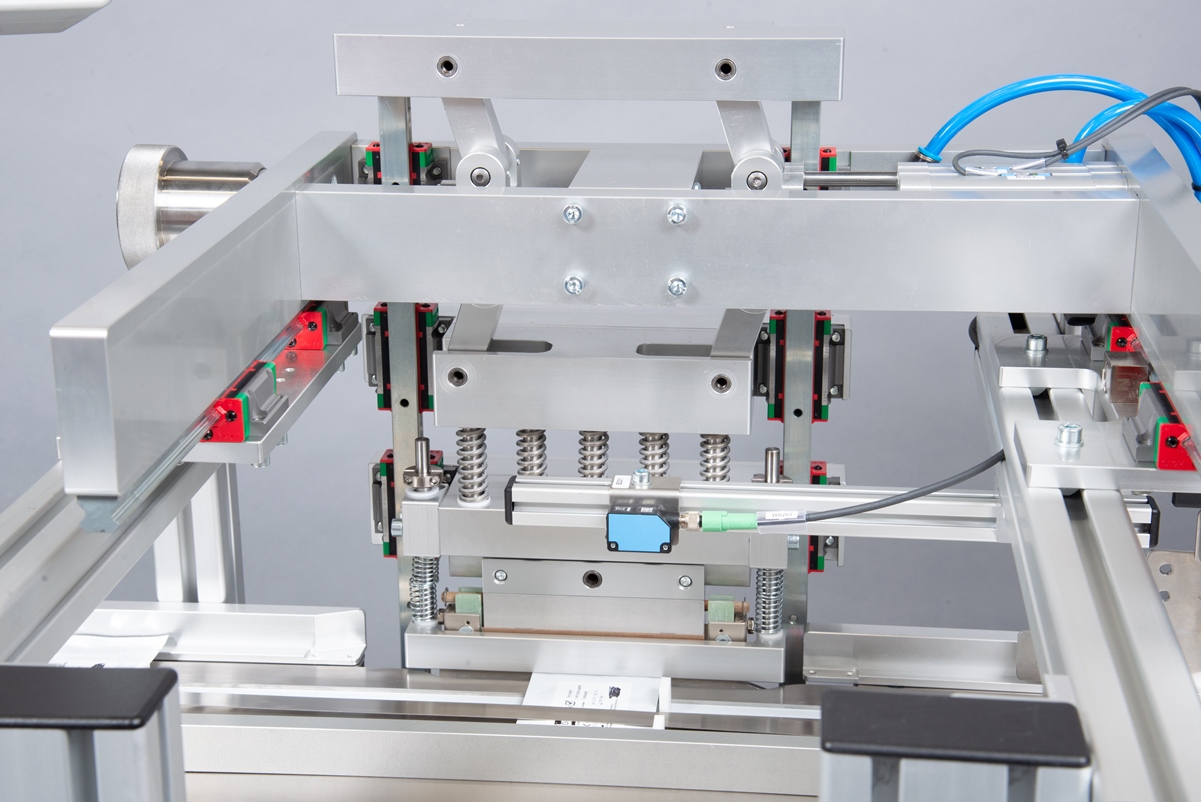
Für das thermische Verschweißen des Verbundmaterials kommen spezielle Komponenten zum Einsatz. (Bild: Kraus Maschinenbau)
Kurze Entscheidungswege waren gefordert
pj: Wie lange hat die Entwicklung bzw. Anpassung gedauert?
Joachim Kraus: Die ersten Gespräche mit dem Kunden fanden Mitte März statt. Der Weg von der Konzeptionierung bis hin zur Bestellung durch den Kunden war von einem straffen Terminplan und hohen Projektanforderungen geprägt.
Wir hatten am 18. März das Angebot eingereicht, das dann am 23. März beauftragt wurde. In einem dreiwöchigen Kraftakt war es gelungen, die Anlage zu entwickeln. Zwei Entwicklerteams haben in Schichten an dem Projekt gearbeitet und die einzelnen Schritte jeweils mit dem Kunden abgestimmt.
Um Zeit zu sparen, wurde nicht abgewartet, bis alles entwickelt war. Sobald eine Baugruppe fertig konstruiert war, wurde der Einkauf mit der Beschaffung aktiv. Dies entspricht nicht unserer üblichen Arbeitsweise, da das Risiko, falsche Komponenten zu ordern, hoch ist. Ich glaube, ich gehe nicht zu weit, wenn ich behaupte, dass ein gesellschaftliches Interesse an den Corona-Schnelltests besteht, weshalb es richtig ist, dieses Risiko einzugehen.
Die Verzahnung, Kommunikation und Zusammenarbeit von Konstruktion, Einkauf und Montage verkürzte nicht nur den Liefertermin, sondern stellte auch eine hohe Qualität sicher. Klar ist, dass die Corona-Schnelltests dringend gebraucht werden.
pj: Welche Arbeitsschritte waren besonders anspruchsvoll?
Joachim Kraus: Die Herausforderungen liegen meist bei der Integration unserer Maschinen in die gesamte Produktionslinie. Bei den Schnittstellen müssen wir uns an die Vorgaben des Kunden halten. Die Abstimmung mit Herrn Söffing, dem Geschäftsführer von Senova, war sehr professionell und unkompliziert, und notwendige Entscheidungen wurden in Rekordzeit getroffen.
Für das thermische Verschweißen des Verbundmaterials kommen spezielle Komponenten zum Einsatz. Dafür mussten wir einen leistungsstarken Partner finden. ROPEX konnte uns in kürzester Zeit ein maßgeschneidertes System liefern. Der Hinweis auf den Corona-Schnelltest sorgte für höchstes Engagement unserer Projektpartner. Bei unserer Zusammenarbeit mit Senova musste außerdem zusätzlich beachtet werden, dass die gesamte Produktion im Reinraum stattfindet.
pj: Wann geht die erste Maschine in Betrieb?
Joachim Kraus: Die erste Maschine wurde bereits Mitte Mai ausgeliefert. Vorher mussten mit dem Kunden noch die Details und die Sicherheitsvorkehrungen in Corona-Zeiten für den Besuch unserer Techniker abgestimmt werden.
pj: Wie geht es weiter?
Joachim Kraus: Wie Sie sich sicherlich vorstellen können, ist die Nachfrage nach den Tests aktuell enorm, sodass die Produktionskapazitäten den aktuellen Bedarf nicht abdecken können. Somit sind weitere Linien in Planung, und entsprechende Gespräche stehen kurz vor dem Vertragsabschluss. Wir freuen uns und sind auch ein wenig stolz, dass wir in diesen schwierigen Zeiten einen kleinen Betrag zur Bewältigung der Situation beitragen können. Kurze Entscheidungswege bei Kraus ermöglichten ein Abweichen von den gewohnten Prozessen, um die Lieferfähigkeit des Kunden zu beschleunigen.