Für das japanische Konsumgüterunternehmen Kao und die Haarkosmetikmarke Goldwell hat Mondi eine recycelbare Verpackung entwickelt. Die Standbodenbeutel sind leicht, bestehen aus Monomaterial und sind daher recycelbar. Außerdem reduzieren sie die Kunststoffmenge um 80 Prozent.
Mondi hat sich mit Kao zusammengetan, um eine recycelbare, leichte Verpackungslösung für seine Goldwell-Haaraufhellungsprodukte zu entwickeln. Der neue Standbodenbeutel reduziert den Kunststoffverbrauch, ohne Kompromisse bei Stärke und Haltbarkeit einzugehen. Die Haaraufhellungsprodukten wurden zuvor in starren Kunststoffbehältern verpackt. Jetzt reduziert Kao die Gesamtmenge an Kunststoff in einzelnen Verpackungen um 80 Prozent.
Einfache Handhabung
Die Lösung verpackt das Pulver in flexible, wiederverschließbare Standbodenbeutel, die aus Monomaterial bestehen und somit recycelbar sind. Der Beutel wird dem Benutzer zusammen mit einer Anleitung in Papierform in einer Kartonschachtel zur Verfügung gestellt, die es ermöglicht, den Beutel bei der Lagerung zu stapeln, und führt zu einem geringeren CO2-Fußabdruck im Vergleich zu vorherigen Verpackungsalternativen.
„Die Lösung, die wir mit Kao entwickelt haben, enthält ein Produkt auf chemischer Basis, das besonders empfindlich ist, daher mussten wir Sicherheit und Qualität jederzeit berücksichtigen. Die neuen Beutel sind im befüllten Zustand absolut transportsicher und leicht zu transportieren. Kao setzt sich leidenschaftlich dafür ein, die richtigen Veränderungen für eine nachhaltigere Welt vorzunehmen und gleichzeitig die hohe Qualität und Benutzerfreundlichkeit seiner Produkte sicherzustellen, um das beste Kundenerlebnis zu bieten. Es war eine Freude, mit dem Kao-Team an der Entwicklung dieses Produkts zu arbeiten.“
Iris Ross, Regional Sales Consumer Flexibles bei Mondi
Die leeren Beutel können flach gefaltet werden, um einen effizienten Transport zur Fabrik zu gewährleisten. Im gefüllten Zustand bieten sie Schutz für das Produkt und verhindern den Kontakt mit eindringender Feuchtigkeit oder Dämpfen. Chemikalien können nicht durch die dicht verschlossenen Packungen diffundieren. Die Verpackung mit einem recycelbaren oberen Schieber und einer temperaturbeständigen Membran lässt sich bequem und einfach wieder verschließen.
„Nachhaltige Verpackungen sind eines der Schlüsselelemente unserer ESG-Strategie und die Reduktion von Plastik hat für uns oberste Priorität – was nicht produziert wird, kann keinen Schaden anrichten. Mit seinem großen Know-how und seinem professionellen Ansatz hat Mondi es uns ermöglicht, eine viel fortschrittlichere Verpackung für unser Goldwell LightDimensions SilkLift-Sortiment zu liefern, wodurch die CO2-Bilanz der Verpackung im Vergleich zu ihrer früheren Box um 65 % reduziert wurde.“
Elmar Mussenbrock, Director Sustainability, Kao Salon Division
Quelle: Mondi
Weitere Meldungen aus dem Bereich Kosmetik
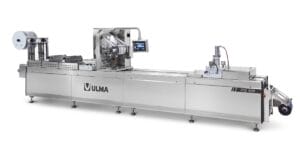
Ulma Packaging: Verpackungsmaschinen für Food und Pharma
Ulma Packaging präsentiert auf der Fachpack live seine neuesten Verpackungslösungen für Lebensmittel, Medizinprodukte und Industrieartikel.
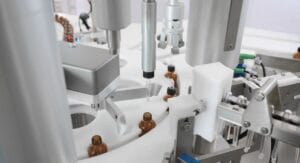
Marchesini Group zeigt Pharma- und Kosmetiklösungen
Die Marchesini Group präsentiert auf der FACHPACK 2025 in Nürnberg neue Maschinenlösungen für Pharma- und Kosmetikverpackungen. Nach Angaben des Unternehmens stehen dabei Effizienz, Recyclingfähigkeit und digitale Services im Fokus.
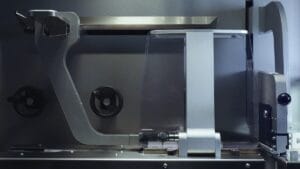
Christ Packing Systems erhält Patent für neue Siegeltechnologie
Christ Packing Systems stellt auf der FACHPACK 2025 eine neu entwickelte Siegeleinheit für die Straffbanderoliermaschine FilmTeq 250 vor. Nach Angaben des Unternehmens reduziere die patentierte Top-Down-Technologie den Kühlbedarf, spare Platz und verlängere die Lebensdauer der Komponenten.
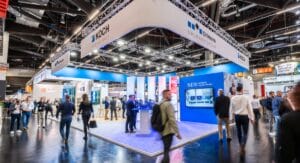
Koch bringt modulare Maschinenneuheit zur Fachpack
Koch Pac-Systeme präsentiert auf der Fachpack 2025 erstmals seine neue modulare Maschinenlösung für die Consumer- und Healthcarebranche.
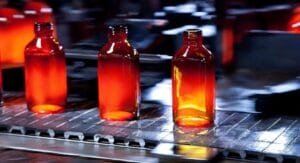
Gerresheimer spaltet Moulded-Glass-Sparte ab und bereitet Verkauf vor
Die Moulded-Glass-Sparte umfasst acht Werke in Deutschland, Belgien, Italien, den USA und Indien mit rund 3.700 Beschäftigten.
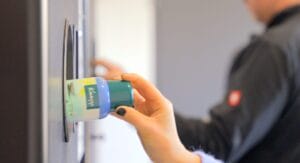
Wie eine digitale Plattform Verpackungen in Kreisläufe bringt
Das Start-up Reo hat eine digitale Plattform für zirkuläre Verpackungslösungen im Kosmetikbereich entwickelt.