Mit Innovationskraft und Lösungskompetenz begegnen Anbieter wie das deutsche Traditionsunternehmen Uhlmann Pac-Systeme den komplexen Ansprüchen im Bereich der Pharmaverpackung. Mit dem neuen Verpackungscenter PTC 200 sowie digital basierten Services adressiert das Unternehmen aus Baden-Württemberg das komplexe Feld an strategischen Anforderungen, in dem sich Pharmaunternehmen, Generikahersteller, CDMOs und Verpackungsdienstleister heute bewegen.
Der Bereich der Pharmaverpackungen steht vor einem ganzen Bündel an strategischen und technischen Herausforderungen. Gefragt sind Lösungen, mit denen Unternehmen flexibel auf wechselnde Marktanforderungen reagieren können – und dies ohne Einbußen bei Prozessstabilität und bei der Einhaltung gesetzlicher und regulatorischer Vorgaben. Bereits vor der COVID-Pandemie und dem weltweiten Anstieg der Impfstoffentwicklung und -produktion gehörten Parenteralia zu den besonders dynamisch wachsenden Segmenten im Pharma-Markt. Das hat sich auch nach dem Abklingen der Pandemie nicht verändert: Die Anzahl und der Marktanteil von Medikamenten, die nicht über den Darm in den Organismus von Patientinnen und Patienten gelangen, sondern als Injektion, Infusion oder als Inhalation verabreicht werden, wächst ständig weiter.
Während Impfstoffe meist in relativ großen Batches hergestellt und verpackt werden, fallen viele andere parenteral verabreichte Medikamente in den Bereich der personalisierten Medizin. Das heißt: Die Mengen, die hier produziert und verpackt werden, sind deutlich kleiner als bei anderen Medikamentenklassen. Außerdem wechseln therapeutisch erfolgreiche Parenteralia im Produktzyklus oft ihre Darreichungsform: Ziel der Hersteller ist es, eine Infusion, die nur von medizinischem Fachpersonal in der Klinik angelegt werden darf, zu einem Produkt weiterzuentwickeln, das einfach in einer Arztpraxis verabreicht werden kann oder sogar zur Selbstmedikation geeignet ist. Das heißt für die abfüllenden oder verpackenden Unternehmen: Die Produkte, die über die Abfüll- und Verpackungslinien laufen, wechseln häufiger. Das bedeutet mehr Umrüstungs-, Reinigungs- und Clearance-Aufwand – und damit ein wachsendes Risiko für die Stabilität der Prozesse.
Erhöhter Druck aus Politik und Gesellschaft
Aber gerade an die Prozesssicherheit stellen Parenteralia besondere Anforderungen: Die Primärverpackungen wie Spritzen, Fläschchen, Vials und Ampullen sind oft aus Glas und zerbrechlich. Bereits geringe Unaufmerksamkeiten oder Ungenauigkeiten im Prozess können hier zu Ausfällen bei der Maschinenlaufzeit oder bei den verpackten Produkten führen. Die Wirkstoffe sind außerdem meist hochempfindlich gegen Vibration oder Temperaturschwankungen. Um die Wirksamkeit des Medikaments zu gewährleisten, müssen Verpackungslinien nicht nur entsprechend präzise und stabil arbeiten. Der gesamte Prozess muss auch lückenlos überwacht und dokumentiert werden. Dazu kommen die regulatorischen Anforderungen an das Device Tracking und die Fälschungssicherheit der Produkte: Je nach regulatorischen Vorgaben müssen alle am Produktions-, Abfüll-, Verpackungsprozess und an der Auslieferung beteiligten Unternehmen die zentralen Prozessdaten bis auf das einzelne Vial oder die einzelne Ampulle nachverfolgbar machen.
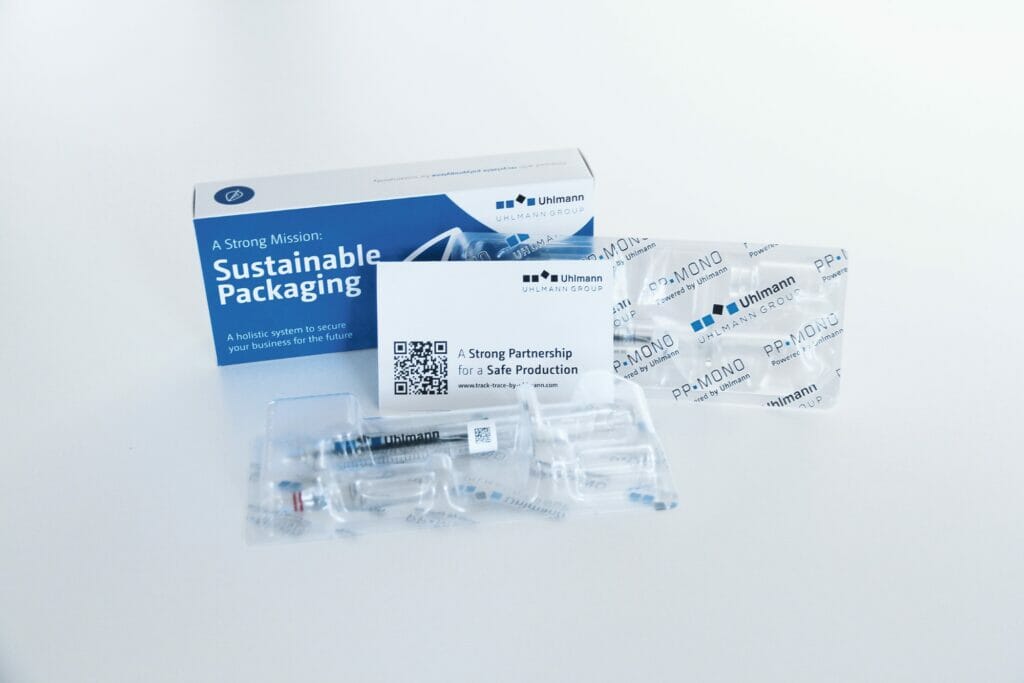
Bis vor Kurzem haben Nachhaltigkeitskriterien bei der Gestaltung und Umsetzung von Verpackungen für Parenteralia fast keine Rolle gespielt. Damit unterscheiden sich Parenteralia nicht von anderen Medikamenten und Medizinprodukten: Gerade auch regulatorisch lag der Schwerpunkt bei der Verpackungsentwicklung sinnvollerweise auf deren Schutzfunktion und der sicheren Handhabbarkeit. Hier waren konventionelle, oft schlecht recycelbare Mehrstoffverpackungen aus Kunststoffen und Karton in Sachen Kosten, Prozesssicherheit und Benutzerfreundlichkeit kaum zu schlagen. Diese Situation ändert sich gerade: Weltweit wird der Fokus auf recycelbare und umweltfreundliche Verpackungslösungen mit einem möglichst kleinen CO2-Footprint deutlich erhöht, und Pharma- und Medizinprodukte sind davon nicht mehr ausgenommen. Schließlich ist die Pharma-Industrie für mehr als vier Prozent der jährlichen Nettoemission von Treibhausgasen verantwortlich – und liegt damit sogar vor der Automobilindustrie. Mediziner, Patienten und die allgemeine Öffentlichkeit fordern immer stärker ebenfalls von der Pharmaindustrie nachhaltigere Prozesse und Lösungen.
Auch die Politik erhöht den Druck und ist dabei, neue Regularien für mehr Nachhaltigkeit auf den Weg zu bringen. Seit April 2022 gilt in Großbritannien zum Beispiel eine Plastiksteuer, in Italien und Spanien tritt eine ähnlich gelagerte Steuer 2023 in Kraft. Weitere EU-Staaten setzen auf andere finanzielle oder regulatorische Mechanismen, um die Menge an nichtrecyceltem Kunststoffabfall deutlich zu reduzieren. Die EU-Staaten reagieren damit auf eine Vorgabe der EU-Kommission im Rahmen des European Green Deal. Aber auch jenseits der EU hat die Reduktion von Kunststoff und Kunststoffverpackungen in den Klima- und Umweltstrategien vieler Staaten hohe Priorität. So sind in einigen afrikanischen Staaten bereits strenge Kunststoffverbote in Kraft. Für den asiatischen Wirtschaftsraum wird die Einführung von Steuern und Abgaben auf Kunststoffverpackungen erwartet, die schlecht oder gar nicht wiederverwertet werden können.
Medikamente flexibel verpacken dank modularem Aufbau
Bei prozesstechnisch wenig sensiblen Produkten wie Tabletten lässt sich die Umstellung auf Verpackungsmaterialien, die gut zu recyclen sind, relativ einfach bewerkstelligen. Zumal mittlerweile gerade im Bereich Monokunststoffe wie beispielsweise Mono-PP-Folie genug Anbieter am Markt sind, dass eine Second-Source-Versorgung gesichert ist. Und der Erfolg von Verpackungslösungen wie der BEC 400 von Uhlmann Pac-Systeme zeigt, dass im Bereich Solida-Blister auch das anspruchsvolle Handling von Mono-PP-Folien sicher gelöst ist.
Verpackungen für Parenteralia nachhaltig zu gestalten, stellt noch einmal höhere Anforderungen an Prozess und Material. Denn die bereits beschriebenen Parameter der Parenteralia-Verpackung verändern sich nicht: fragile Primärverpackungen, empfindliche Wirkstoffe, hohe Anforderungen an Track-and-Trace-Verfahren, kleinere Batches sowie wechselnde Produktformate. Mit dem Parenteral Tray Center PTC 200 steht Pharma-Herstellern und -Dienstleistern nun eine Kartonierlösung zur Verfügung, mit der sich eine Vielzahl von Verpackungsmaterialien, Formaten und Verschlussmechanismen sowie bis zu sechs Parenteral-Produkte verarbeiten lassen.
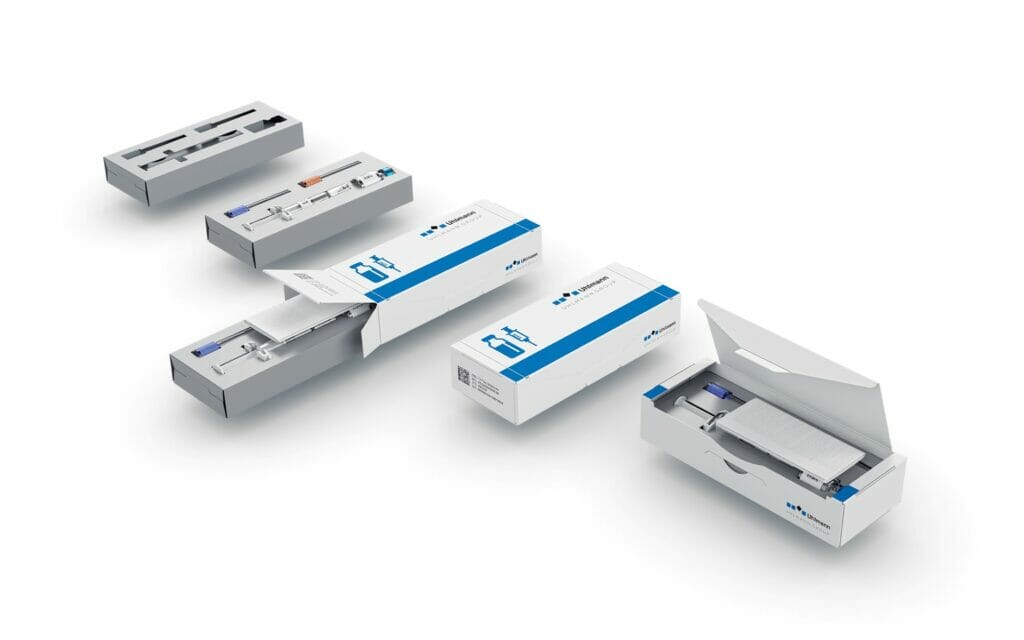
Der Gewinn in Sachen Nachhaltigkeit liegt vor allem in der Flexibilität beim Verpackungsmaterial: Das PTC 200 bestückt Kunststofftrays genauso zuverlässig und sicher wie Trays aus Karton oder Papierfaser. Karton- oder Papierfaser-Trays sind in zahlreichen Formaten verfügbar und auf internationale Richtlinien zum Klimaschutz – wie das Carbon Disclosure Project (CDP), die United Nations Global Compact (UNGC) und die Global Reporting Initiative (GRI) – abgestimmt.
Aber auch darüber hinaus beeindruckt die Flexibilität des Maschinenkonzepts: Der modulare Aufbau der Maschine ermöglicht den Einsatz von bis zu drei verschiedenen Zuführmodulen und bis zu sechs verschiedenen automatischen oder manuellen Produktzuführsystemen. Durch die unterschiedlichen, schnell zu wechselnden Zuführsysteme verpackt das PTC 200 Spritzen und Nadeln, Vials, Ampullen und Karpulen genauso sicher wie Pens, Injektoren oder andere Produkte. Damit lässt sich der komplette Lebenszyklus eines Medikaments abdecken. Ähnlich breit aufgestellt sind Kunden mit dem PTC 200 bei den Verschlussmöglichkeiten: Steckverschluss sowie manipulationssichere Verschlüsse mit Hotmelt-Standard bis zur vierten Lasche sind möglich, ebenso wie von oben zu öffnende Faltschachteln.
Eingerichtet oder umgestellt auf neue Produkt- oder Verpackungsformate, ist das PTC 200 erstaunlich schnell: Eine komplette Umstellung ist mit zwei Personen in einer halben Stunde möglich. Beim Betrieb des PTC 200 wird vom Personal an der Maschine keine besondere Ausbildung benötigt. Das Bediensystem SmartControl leitet die Bedienperson intuitiv durch die Formatwechsel und unterstützt im laufenden Betrieb. Das sorgt für eine optimale Prozesssicherheit und eine schnelle Inbetriebnahme auch durch weniger erfahrene Mitarbeiterinnen und Mitarbeiter.