Nicht nur medizinische Geräte und Teile, sondern auch ihre Verpackungen aus Kunststoff stehen im Fokus des Tampondrucks bei VID Völker Industrie Drucke, Heilbronn. Verpackungen mit einer glatten, konkaven oder konvexen Oberfläche können mit dieser ganz besonderen Technologie bedruckt werden.
Das Unternehmen bedruckt seit über 40 Jahren eine Vielzahl von Produkten aus verschiedenen Materialien mittels Tampondruckverfahren. Vom kleinen Drehknopf bis hin zum Sitzwürfel – schon viele außergewöhnliche Kundenwünsche wurden realisiert. Langjährige Erfahrung mit diesem Druckverfahren ermöglichen es dem Familienunternehmen, sich innovativ an Neues anzupassen.
Gut gerüstet
Heute steigen die Anforderungen an den Tampondruck immer weiter. Die Geometrie der Teile wird komplizierter und der Druck auf Kunststoffe muss extremen chemischen Belastungen standhalten. Um dies zu realisieren, wurde im Unternehmen der Fokus vermehrt auf Vor- und Nachbehandlungen sowie neue Druckfarbsystemen gelegt.
Im Jahr 2014 wurde zusätzlich die Zertifizierung nach ISO 9001:2010 eingeführt. Außerdem wurden Tampondruckmaschinen mit geschlossenen Farbsystemen und neuester Technik angeschafft. So können heute Produkte mit bis zu fünf Farben bedruckt werden.
Der Druck auf gewölbte, genarbte, glatte oder vertiefte Produkte ist im Unternehmen möglich. Die allgemeinen Druckparameter sind eine Druckbreite bis 350 Millimeter, eine Linienstärke ab 0,2 Millimeter, Druckbilddurchmesser von einem bis 170 Millimeter und eine Formteilhöhe von bis zu 400 Millimetern.
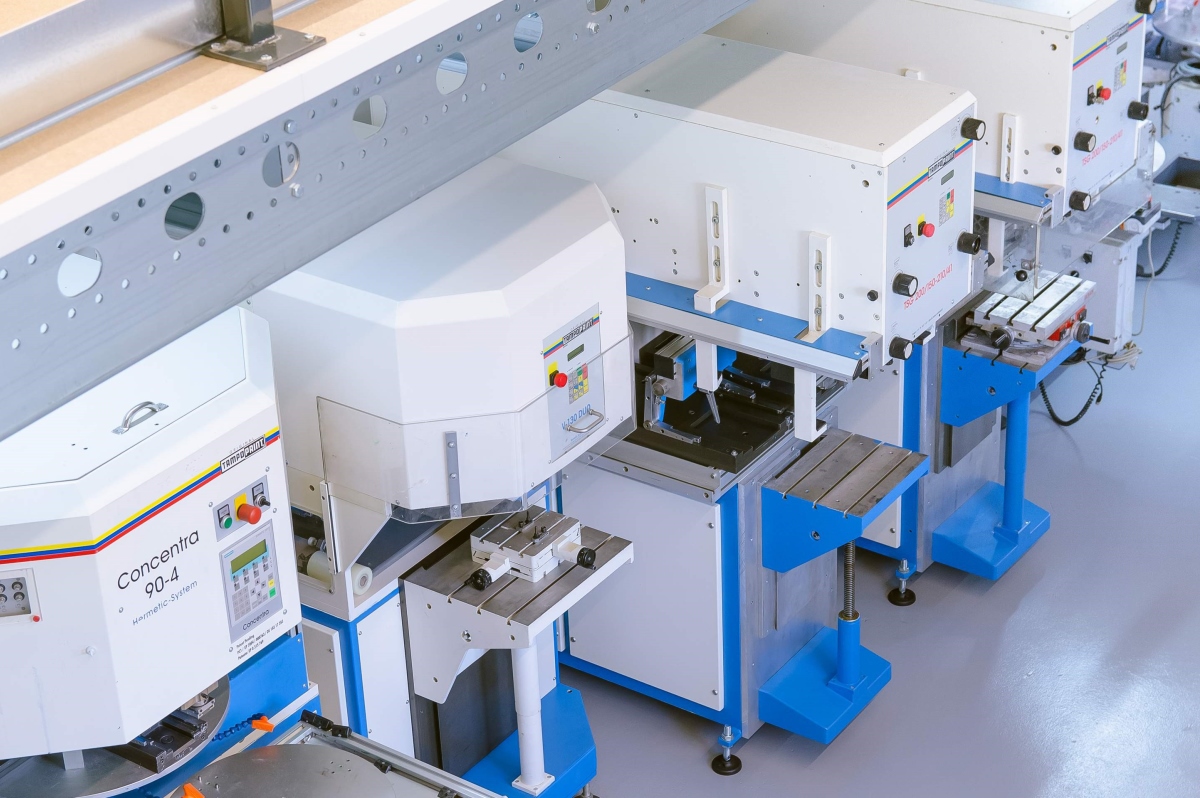
Der Maschinenpark in Heilbronn. Mit den Maschinen können eine bis vier Farben gedruckt werden. (Bild: VID)
Technischer Hintergrund
Der Tampondruck ist ein Verfahren zur Übertragung eines 2-D-Bildes auf ein 3-D-Objekt. Als indirektes Druckverfahren ist die Verwendung einer geätzten Platte (Klischee) und eines Tampons zur Übertragung des Bildes erforderlich.
Im ersten Schritt wird aus einer grafischen Vorlage ein Mattfilm mit dem jeweiligen Druckmotiv erstellt, der als Grundlage für die Herstellung des Klischees dient. Anschließend wird dieses Klischee auf der Maschine montiert und mit einem Farbtopf besetzt, der mit einem integrierten Rakelmesser zugleich als Dichtung fungiert.
Das Klischee bewegt sich nun unter dem (Rakel-)Topf vor und zurück und sorgt dafür, dass nur die benötigte Farbe in die Vertiefung (Druckmotiv) des Klischees gelangt. Der aus elastischem Silikon bestehende Tampon nimmt im Anschluss die Farbe aus dem Klischee auf und gibt sie auf dem Bedruckstoff ab.
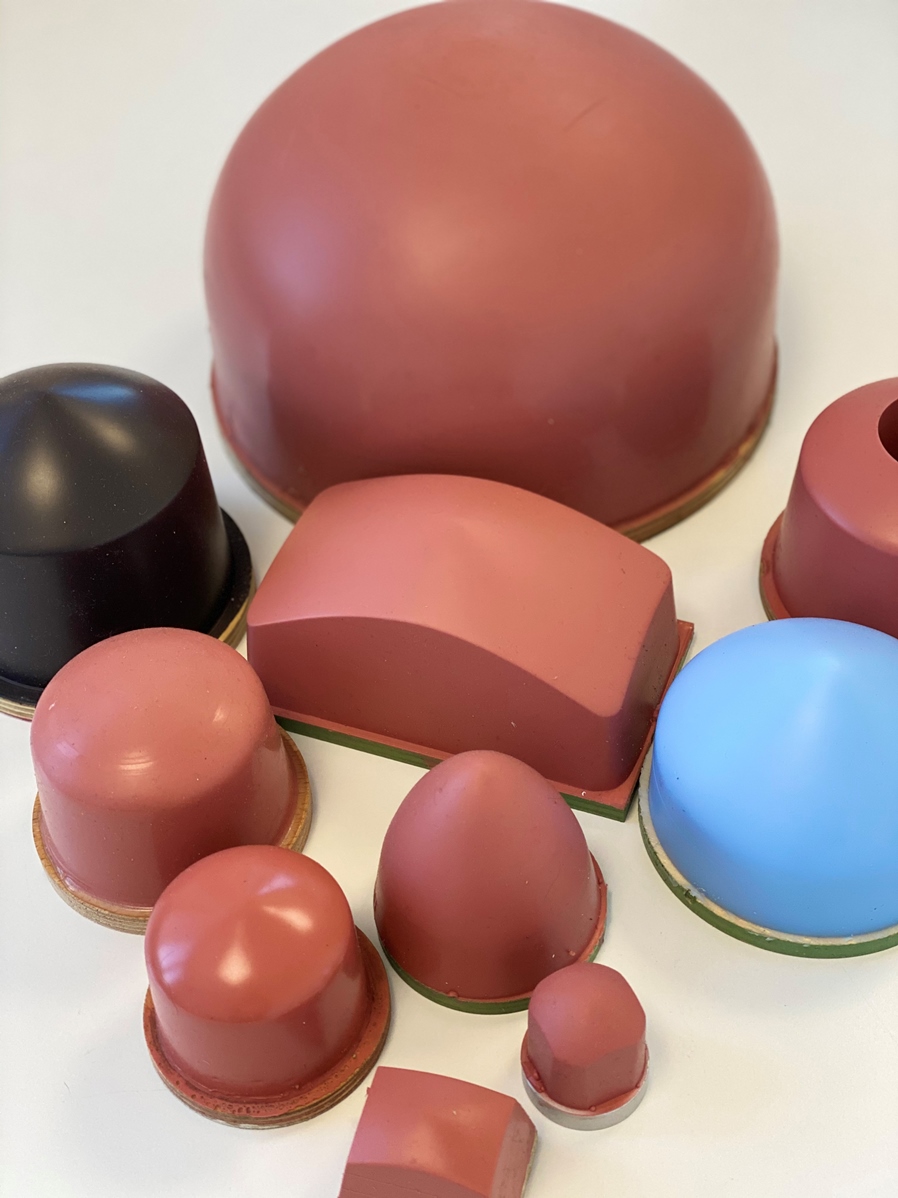
Die flexiblen Silikontampons gibt es in verschiedenen Shorehärten und Größen. Dies ermöglicht eine optimale Anpassung an den jeweiligen Bedruckstoff. (Bild: VID)
Durch die hohe Flexibilität des Silikons kann sich der elastische Tampon optimal dem zu bedruckenden Stoff anpassen. Natürlich stehen dem Ganzen auch Vor- und Nachbehandlungsverfahren zur Verfügung, um eine langlebige Druckqualität zu gewährleisten.
Eine Vielzahl unterschiedlicher Maschinentypen wurde in den letzten 40 Jahren entwickelt – von der Einfarben-Tischmaschine bis hin zum Roboter-geführten Druck. Das Druckverfahren wird häufig für Objekte mit komplizierten dreidimensionalen Geometrien oder unregelmäßigen Formen sowie bei strukturierten Oberflächen eingesetzt.
Im Tampondruck bedruckte Objekte finden sich in einer Vielzahl von Industrien, wie z. B. Luftfahrt, Medizin, Automobil, Werbeartikel, Haushaltsgeräte, Spielzeug und Sportartikel. Aber auch im Verpackungsbereich nimmt diese Technologie Fahrt auf.
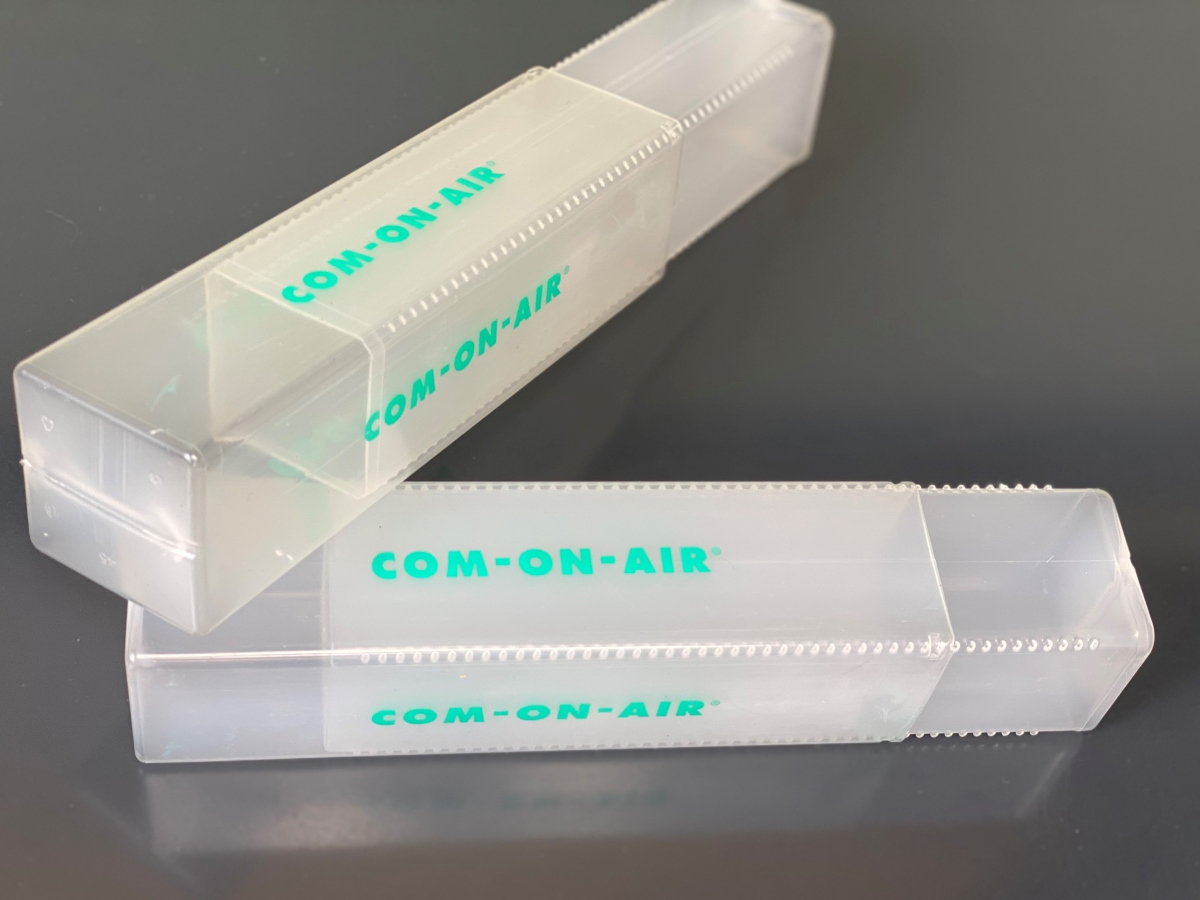
Verpackung „Tube“, mit einem Primer vorbehandeltes l PP, bedruckt mit einer Tampoprint Vario 90/10. (Bild: VID)
Herausforderung Kunststoffverpackungen
Richtlinien und Normen auf dem Gebiet der Medizin verlangen Sachkenntnis im Druckverfahren. Mit immer individuell auf das jeweilige Produkt abgestimmten Druckfarben können selbst auf den schwierigsten Materialien beeindruckende Ergebnisse erzielt werden, die gegen eine Vielzahl chemischer Beanspruchungen beständig sind.
Doch wie sieht das bei Kunststoffen genau aus? Viele Ausgangsmaterialien sind aufgrund ihrer Zusammensetzung ohne Vorbehandlung zu bedrucken wie beispielsweise ABS, Polycarbonat (PC), PMMA oder Polyester. Kunststoffe wie Polyamid (PA), Polypropylen (PP), Boltaron, Lexan oder Polyethylen (PE) hingegen müssen durch eine entsprechende Vorbehandlung erst bedruckbar gemacht werden.
Beispiel für den Druck im Medizinbereich
Vorbehandlung – kurz vor dem Druck wird die Oberfläche gereinigt, um eine fett- und fusselfreie Oberfläche zu erhalten.
Druckfarbe – entsprechend den chemischen Beanspruchungen des Produkts erfolgt eine Auswahl.
Druck – das Objekt wird in zwei Druckdurchgängen auf der Vorder- und Rückseite mit einem definierten Abstand bedruckt.
Endkontrolle – nach dem Druckvorgang erfolgt die Überprüfung der Haftung und Optik, um eine 100%ige Qualität zu gewährleisten.
Bei VID gibt es Erfahrungen mit unterschiedlichen Verpackungsvarianten, so für Multiboxen für Pipettenspitzen, Verpackungen für Poliersets im Dentalbereich, für Abdeckwachs für die Kieferchirurgie oder Verpackungen für die Langzeitprobenarchivierung sogenannte Röhrchenracksysteme.
Mensch statt Maschine
Was bei VID schon immer im Vordergrund steht, ist die Kompetenz der Mitarbeiter und die Produktion im eigenen Haus. Durch den kontinuierlichen Verbesserungsprozess mit geschultem Personal können Ideen und Innovationen gemeinsam entwickelt werden. Zudem wird mit dem Vieraugenprinzip und Sichtkontrolle jedes Teils gearbeitet, und deshalb kann die Nullfehler-Philosophie zielstrebig verfolgt werden.
Angela Völker, CEO & Produktmanagement VID Völker Industrie Drucke (Bild: VID)
„Wir verwirklichen seit über 40 Jahren die unterschiedlichsten Kundenwünsche mit Engagement und Zielstrebigkeit. Dabei stehen Kunde, Produkt und Innovation ausnahmslos im Zentrum unserer täglichen Arbeit“, betont Angela Völker.
Vorteil eines mittelständischen Unternehmens ist die kurze Reaktionszeit, mit der neuen Herausforderungen begegnet werden kann. Kleine Wege und gute Absprachen sowie die eigene Produktion der Klischees gewährleisten Qualität und agile Arbeitsweisen.
Angela Völker im Interview
Nach 30 Jahren stetigem Wachstum übernahm Angela Völker, die Tochter des Gründers Willi Völker, vor zehn Jahren erfolgreich die Geschäftsführung des Familienunternehmens.
pj: Frau Volker, wie sind Sie eigentlich zum Tampondruck gekommen?
Angela Völker: Schon als kleines Kind durfte ich meinem Vater bei der Arbeit zusehen und später auch mitarbeiten. Ich war begeistert von der Vielfalt und Abwechslung, die diese Branche mit sich bringt. Täglich kommen wir mit unzähligen, bedruckten Produkten in Berührung. Sei es der Flugzeugsitz auf dem Weg in den Urlaub oder die Thermoskanne, in die wir gerade unseren Tee gefüllt haben. Die Drucktechnik hat mich daher schon von klein auf fasziniert.
pj: Und wie hat es vor 40 Jahren angefangen?
Angela Völker: VID startete eigentlich als Werbeartikel-Großhandel in Oberstenfeld in Baden-Württemberg. Aus der Not heraus, einen preiswerten und qualitativ hochwertigen Drucker zu finden, kam Willi Völker 1977 in Kontakt mit dem Entwickler der ersten Tampondruckmaschine, Wilfried Philipp. So wurde ein Teil des Lagers ausgeräumt und die ersten Bedruckungsversuche mit der eigenen Tampondruckmaschine begannen: Der Grundstein eines Familienunternehmens mit Tradition wurde gelegt.
pj: Wer waren die ersten Kunden?
Angela Völker: Mein Vater erkannte früh das große Potenzial des Lohndrucks. Das Produktportfolio erweiterte sich von der Bedruckung von Werbemitteln sehr schnell auf die Bedruckung von Haushaltsgeräten, und nach kurzer Zeit folgten Teile für die Automobilindustrie. Der Werbeartikel-Großhandel wurde eingestellt, und das Unternehmen konzentrierte sich fortan ausschließlich auf die Bedruckung von Industrieteilen.
pj: Ihr Vater hat also komplett auf den Tampondruck gesetzt?
Angela Völker: Das ist richtig. Obwohl der Tampondruck noch in den Kinderschuhen steckte, scheute er weder Zeit noch Mühen, auch die Weiterentwicklung der Bedruckung von konvexen und konkaven Teilen voranzutreiben. Einen Support, wie wir ihn heute kennen, gab es damals noch nicht, und autodidaktische Fähigkeiten waren gefragt.
pj: Willi Völker und seine Ehefrau Margit Völker machten sich einen Namen in der Branche und mit steigenden Aufträgen konnten weitere Tampondruckmaschinen angeschafft werden. Wie ging und geht es weiter?
Angela Völker: Da der Platz in den Räumen zu eng wurde, folgte 1985 der Umzug in neue Räume nach Steinheim an der Murr. Das Portfolio der Bedruckung erweiterte sich auf Produkte der Elektro- und Medizinindustrie.
Nachdem auch dort die Produktionsfläche knapp wurde, wechselte das Unternehmen 1992 nach Ilsfeld und erweiterte dort seine Produktionsstätte. Durch die verbesserte Verkehrsanbindung und die größere Lagerfläche konnten auch Produkte aus Luftfahrtunternehmen bedruckt werden. Seit 2010 ist unser Standort in Heilbronn am Neckar. Inzwischen liegt der Fokus auch im Bedrucken von Kunststoffverpackungen im industriellen sowie im medizinischen Bereich.