Der deutsche Kofferhersteller W.AG erweitert seinen Leistungskatalog für OEM-Kunden und bietet jetzt maximalen Freiraum für die Gestaltung von maßgeschneiderter Produktverpackungen. Die Koffer werden aus recyclingfähiges Polypropylen bzw. dem Biopolymer Arboblend des deutschen Herstellers Tecnaro hergestellt.
Die Realisierung kundenorientierter und individualisierter Kofferlösungen steht bei W.AG seit jeher hoch im Kurs. Nun aber geht das Unternehmen einen Schritt weiter: Im Rahmen mittel- bis langfristiger Partnerschaften öffnet es seine Engineering- und Produktionskapazitäten für die exklusive Entwicklung und Serienfertigung OEM-spezifischer Koffer, Cases und Boxen. Damit bietet W.AG seinen Kunden einen maximalen Freiraum für die Gestaltung maßgeschneiderter Produktverpackungen mit hoher Alleinstellung.
Lösungen für OEM-Kunden
Mit zahlreichen Design-Innovationen hat sich W.AG seit der Firmengründung im Jahr 1992 einen Namen gemacht. Jetzt vollzieht das Unternehmen eine Weichenstellung, mit der es sein bisheriges Portfolio erheblich ausweitet: Neben der bis dato praktizierten Herstellung kundengerechter, individualisierter Private-Label-Lösungen positioniert es fortan einen Bereich Customer-Own-Products, der ausschließlich der Realisierung exklusiver Koffer-, Case- und Boxen-Lösungen für OEM-Kunden vorbehalten ist.
(Bild: W.AG Funktion + Design GmbH)
„Ein hohes Maß an Kundenorientierung und den konsequenten Einsatz unserer umweltschonenden Pureline- und Organicline-Werkstoffe haben wir als verbindende Elemente beider Sparten definiert. Während sich aber im Bereich Private-Label weiterhin alles um unsere etablierten Design- und Fertigungslinien drehen wird, richten wir im neuen Bereich sämtliche Entwicklungs-, Engineering- und Produktionsleistungen flexibel auf die Umsetzung eigenständiger OEM-Verpackungslösungen mit höchsten Ansprüchen an Exklusivität und Unverwechselbarkeit aus.“ Michael Müller, W.AG-Vertriebsleiter
Erste namhafte Hersteller der Werkzeugbranche und der optischen Industrie nutzen das neue Angebot bereits. „Das beginnt bei ersten Designskizzen, führt über sämtliche Iterationsstufen der Produktentwicklung – inklusive 3D CAD-Konstruktion und 3D-Printing – und mündet in der Großserien-Produktion der OEM-exklusiven Gehäuse und Inlays“, berichtet W.AG-Entwicklungsleiter Björn Ullrich.
Im Unterschied zum bisherigen Privat-Label-Geschäft lässt der thüringische Kofferspezialist in den OEM-Projekten bewusst zu, dass der bisher übliche Designrahmen gesprengt und das Thema „Nachhaltige Produktverpackung“ neu gedacht werden darf. Für das Kreativteam von Björn Ullrich kann dies sowohl die Entwicklung neuer Formensprachen und CAD-Konstruktionen miteinschließen als auch den Bau völlig neuer Werkzeuge.
Der Entwicklungschef von W.AG betont: „Höchste Priorität hat in diesen Projekten die Realisierung einer hundertprozentig kundeneigenen Mehrweg-Verpackung, die dem darin transportierten oder präsentierten Produkt einen deutlichen Wettbewerbsvorteil verleiht. Erfahrungsgemäß entsteht dabei durch die Form und Funktion der Gehäuse und Inlays, durch den Einsatz unserer nachhaltigen Werkstoffe, durch die Farbgebung sowie unsere Label- und Printvarianten der ideale Koffer, die optimale Box oder das perfekte Case.“
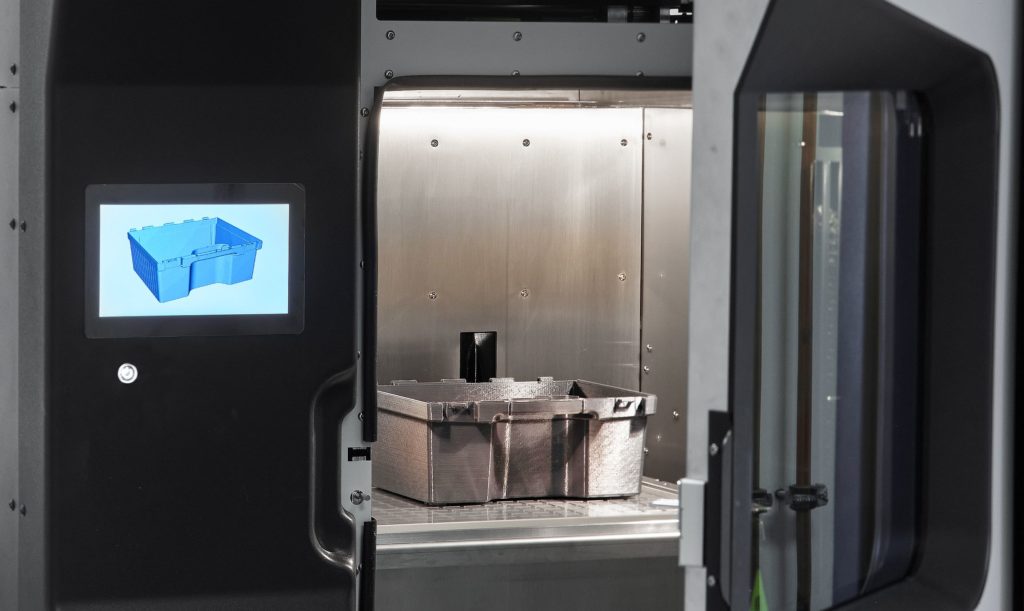
Das 3D-Printing gehört für W.AG zu den zentralen Formgebungsverfahren bei der Entwicklung kundenspezifischer Kofferlösungen. (Bild: W.AG Funktion + Design GmbH)
Innen und außen nachhaltig
Die materialtechnische Basis der Koffersysteme von W.AG bilden seit bald zwei Jahren ein hundertprozentig recyclingfähiges Polypropylen für die Pureline-Koffer sowie das Biopolymer Arboblend des deutschen Herstellers Tecnaro, das bis zu 93 Prozent aus nachwachsenden Rohstoffen besteht. Hieraus werden die Produktverpackungen der Organicline gefertigt. Aus beiden Werkstoffen entstehen nicht nur die Spritzguss-Halbschalen der Koffer, Boxen und Cases, sondern inzwischen auch ein Großteil der in automatisierten Wasserstrahl-, Laserschneid- und Fräsanlagen hergestellten Schaumeinlagen.
„Die Inlay-Fertigung erweitern wir zudem gerade durch die Tiefziehtechnik. Damit können wir auch feste und sterilisierbare Inlays realisieren, was insbesondere für Hersteller in der Medizin- und Labortechnik eine wichtige Alternative ist“, sagt Björn Ullrich. Zum äußeren und inneren Bedrucken der Koffer bietet W.AG über den Sieb- und Tampondruck hinaus zwei moderne Verfahren, mit denen sich exzellente fotorealistische Vierfarbprints erstellen lassen: Das In-Mould-Labeling und den digitalen Direktdruck.
Quelle: W.AG