Systemanbieter Vahle setzt in Kooperation mit verschiedenen Herstellern von Linearmotoren und Systemintegratoren auf verschleißfreie Induktivtechnik, denn moderne Produktions- und Verpackungsprozesse werden immer komplexer und erfordern flexible und wartungsarme Systeme.
Seit Jahren gibt es in der Verpackungsindustrie einen Trend zu immer individuelleren Lösungen und Sonderformaten. Bei nahezu jedem Unternehmen steigt die Variantenvielfalt, gleichzeitig sinkt die Chargengröße pro einzelner Verpackungseinheit. Moderne Maschinen müssen deshalb ein hohes Maß an Flexibilität aufweisen und schnelle sowie einfache, bestenfalls On-the-fly-Format- oder Werkzeugwechsel ermöglichen. Und das muss möglichst reibungslos erfolgen, wofür eine sichere Energiezuführung unabdingbar ist.
Die Paul Vahle GmbH & Co. KG ist auf Energie- und Datenübertragung für mobile Industrieanwendungen spezialisiert. Mittlerweile setzt das Kamener Unternehmen vermehrt auf kontaktlose Systeme.
(Bild: Vahle)
“Unsere induktiven Lösungen sind für Hochgeschwindigkeitssysteme ausgelegt und vermeiden die Entstehung von Kohlestaub, der in der Lebensmittelindustrie nicht erlaubt ist. Konventionelle Stromschienen- und Schleifringtechnologie ist diesen Anforderungen nicht gewachsen.“ Marc Detweiler, Leiter des Produktmanagements bei Vahle
Weniger ist mehr
Der entscheidende Vorteil der Contactless-Power-Supply (CPS)-Technik ist, dass sie eine kontinuierliche Energiezuführung auf mobiler Seite gewährleistet. „Dadurch können die einzelnen Trägerfahrzeuge mit Greifern, Vakuumpumpen oder Steuerungselementen ausgerüstet werden.“ Denn mithilfe der Aktoren und Sensoren können die mobilen Teilnehmer unterschiedliche Produkte, Materialien, Formen und Größen sicher fixieren, was formschlüssige Halterungen und häufige Werkzeugänderungen für Formatwechsel gänzlich überflüssig macht. „Mit dem deutlich vereinfachten Design der mobilen Seite reduzieren wir den Engineering-Aufwand und realisieren wesentlich flexiblere Anforderungen mit unseren Kunden, wodurch die Maschinen unabhängiger und letztlich kostengünstiger werden.“
Auch die Anzahl der Carrier lässt sich beispielsweise bei gleichem Durchsatz reduzieren, denn für den Greifprozess, bei dem bislang teilweise zwei Mover benötigt werden, ist nur noch ein einzelnes Fahrzeug mit Aktorik notwendig. Dabei können die von Linearmotoren angetriebenen Schlitten komplett unabhängig voneinander bewegt werden. „Die Fixierung mit Greifern oder der Sog der Vakuumpumpen sorgen für festen Halt und wirken in Kurven der Zentrifugalkraft entgegen, damit die Elemente genau dort bleiben, wo sie hingehören. Dadurch sind schnellere Geschwindigkeiten und eine höhere Durchsatzrate möglich“, sagt Detweiler.
Leichtgewichte für maximale Leistung
Bei den leistungsstarken Pick-up-Lösungen setzt Vahle auf eine kompakte Leichtbauweise, um Gewicht zu sparen. „Gängige Carrier können beispielsweise wenige Kilogramm zusätzlich Nutzlast tragen. Belegen wir davon einen Großteil mit Elektronikkomponenten, schränkt das die Effektivität der Maschine massiv ein, was dem Endkunden schlussendlich keinen Mehrwert bietet.“ Trotz geringer Abmessungen von nur 40 Millimeter Länge, 48 Millimeter Höhe und 60 Millimeter Breite liefert beispielsweise der vPOWER U007-Pick-up eine Spitzenleistung von 70 Watt bei einer ausgehenden Gleichspannung von 24 Volt. „Der U007-Stromabnehmer wiegt gerade einmal 175 Gramm und ist damit die kompakteste bisher am Markt verfügbare Lösung. Gerade die geringe Länge ist für das sogenannte Pitchmaß der mobilen Teilnehmer essenziell.“
Für Systeme mit höherem Energiebedarf hat Vahle den etwas größeren U015-Pick-up mit einem Gewicht von 650 Gramm im Sortiment, dessen maximale Leistung bei bis zu 150 Watt liegt. Dank eines frei konfigurierbaren Kabelabgangs lassen sich beide Stromabnehmer in nahezu jede Anlage integrieren, in der die nötige präzise mechanische Führung vorhanden ist. „Dadurch erhöhen wir die Wirksamkeit und Flexibilität der Maschinen und erreichen so höhere Produktionsmengen.“ Zudem ließen sich die Pick-ups in Serie schalten, um eine erhöhte Leistungsabgabe durch 48 Volt zu kreieren.
Erster Transportroboter für Verpackungsmaschinen
Seit mehr als zehn Jahren arbeiten Vahle und die Gerhard Schubert GmbH an gemeinsamen Projekten. Schubert gilt mit seinen modularen Top-Loading-Maschinen (TLM), die aus standardisierten Systemkomponenten bestehen, als einer der Technologiepioniere der Branche. Im Rahmen der Zusammenarbeit mit Vahle wurde unter anderem der weltweit erste Transportroboter für Verpackungsmaschinen entwickelt, dabei stellt das Transmodul von Schubert einen besonderen Anwendungsfall dar.
Das Transmodul fährt mit einer Geschwindigkeit von bis zu 4,5 Meter pro Sekunde auf einem Schienensystem durch die verschiedenen Teilmaschinen. Mithilfe eines Vakuumgebläses, das einen Unterdruck von 0,04 Bar erzeugt, werden die Schachteln und Produkte während des Transports gehalten.
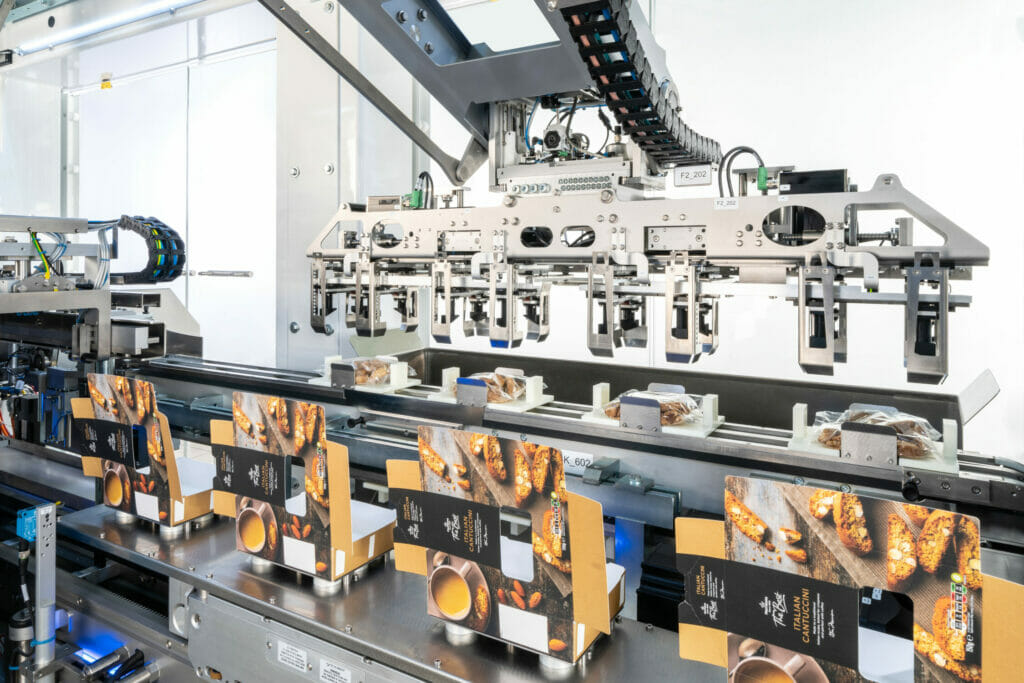
Mithilfe des Transmoduls, das Vahle gemeinsam mit der Gerhard Schubert GmbH entwickelt hat, können verschiedene Produkt- und Verpackungsgrößen in ein und derselben Maschine verarbeitet werden. (Bild: Gerhard Schubert)
Die Transportroboter werden induktiv mit Energie versorgt und bewegen sich in einem Kreislauf durch die Anlage. Am Ende der Oberspur drehen sie mitsamt des Schienenelements um 180 Grad entlang ihrer Längsachse und fahren auf der Unterspur wieder zum Ausgangspunkt zurück. „Um das zu ermöglichen, wurde ein sogenannter Drehübertrager entwickelt, der das Herzstück der Kundenlösung darstellt“, berichtet Detweiler.
Die Anwendungsbereiche für induktive Systeme sind vielfältig. In Zukunft, so erwartet man bei Vahle, werden die Einsatzmöglichkeiten durch neue Add-ons sogar noch wachsen. Die Coronapandemie hat dazu geführt, dass sich Unternehmen vermehrt mit dem Thema auseinandersetzen. „Wie in anderen Automatisierungsbereichen spüren wir aktuell eine besondere Nachfrage.“