Mit über 30 verschiedenen Marken und Sorten trifft der global führende Bierhersteller Molson Coors weltweit den Geschmack der Konsumenten. Für eine hochflexible Endverpackungslösung hat das Entwicklungsteam der Maschinenhersteller KHS und Schubert die Expertise beider Unternehmen in einer optimalen Lösung vereint: Die Verpackungsmaschine Innopack TLM erfüllt gleich drei Aufgaben.
Für seinen neuen Produktionsstandort im kanadischen British Columbia benötigte die Brauerei Molson Coors eine neue, hochflexible Anlage, um befüllte Glasflaschen vollautomatisiert zu verpacken. Die verschiedenen Biersorten sollten unter Gewährleistung höchster Anpassungsfähigkeit an zukünftige Produkt- und Formatänderungen in eine Vielzahl unterschiedlicher Formate verpackt werden. „Es war uns sehr wichtig, eine Lösung zu finden, die Flexibilität sicherstellt, damit wir schnell auf neue Marktanforderungen reagieren können“, erinnert sich Connie Jones, Senior-Projektmanagerin bei Molson Coors.
„Jedes der Unternehmen hat seine Kernkompetenz eingebracht: KHS ist eines der innovativsten und international führenden Unternehmen in der Abfüllindustrie, und Schubert prägt die weltweite Verpackungsindustrie seit über 50 Jahren.“
Sebastian Mayer, Verkaufsgruppenleiter bei Schubert.
Bis zu 720 Flaschen pro Minute in sechs Formaten
Die Herausforderung lag darin, drei individuelle Verpackungsprozesse nahtlos in eine Verpackungsmaschine mit hoher Leistung zu integrieren. Der Schlüssel dazu war die Innopack TLM, eine hochmoderne Anlage zum Verpacken von Glasflaschen, die gemeinsam von KHS und Schubert entwickelt wurde. Beide Firmen haben ihr Know-how gebündelt, um eine platzsparende Anlage mit hoher Leistung zu entwickeln, die den KHS-Flaschenpacker nahtlos in die TLM-Verpackungsanlage von Schubert integriert.
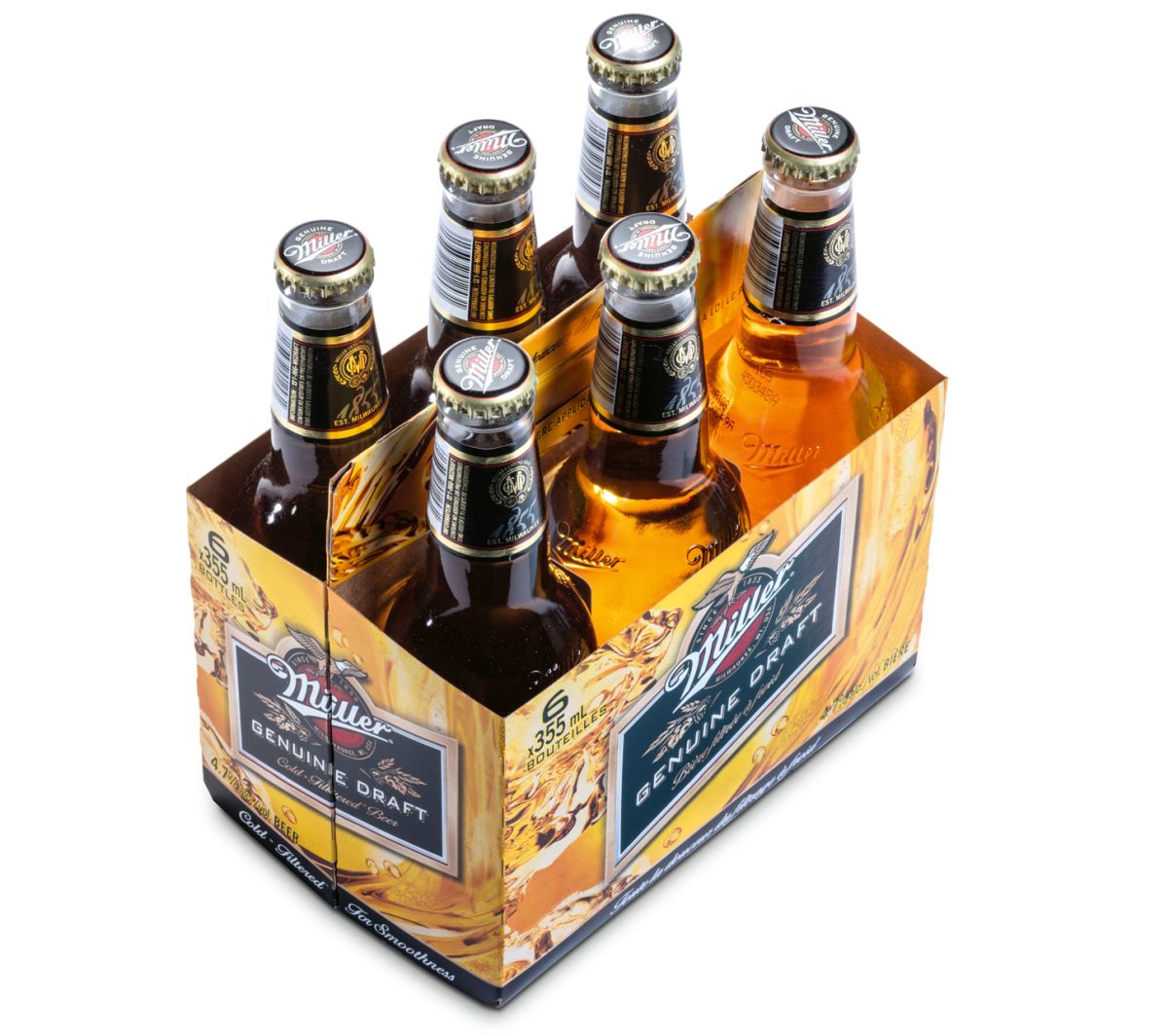
Leere Sechserpack-Baskets werden aufgerichtet, in bereits aufgerichtete RSC-Kartons platziert und dann mit Flaschen von KHS befüllt. Anschließend werden die RSC-Kartons durch zwei Schubert-F2-Roboter verschlossen. (Bild: Gerhard Schubert GmbH)
Die Innopack TLM bietet einen reibungslosen Prozess mit minimalen Umrüst- und Anlaufzeiten. „Herkömmliche Produktionslinien sind in der Regel durch Transportbänder miteinander verbunden. Dagegen integriert die Innopack TLM die individuellen Module in einer einzigen Linie und bietet dadurch ein deutlich höheres Maß an Flexibilität“, erklärt Max Schwaiger, Product Support bei KHS.
Die neue Verpackungsanlage für Molson Coors verpackt mit einer beeindruckenden Leistung von bis zu 720 Flaschen pro Minute sechs unterschiedliche Formate: Sechserpacks in Kartontrays, 12er-, 15er- und 18er-Packs in Kartons sowie Sechserpack-Baskets in RSC-Kartons oder Wrap-around-Kartons. Aktuell werden Flaschengrößen von 341 und 355 Milliliter verpackt, weitere Größen sind möglich.
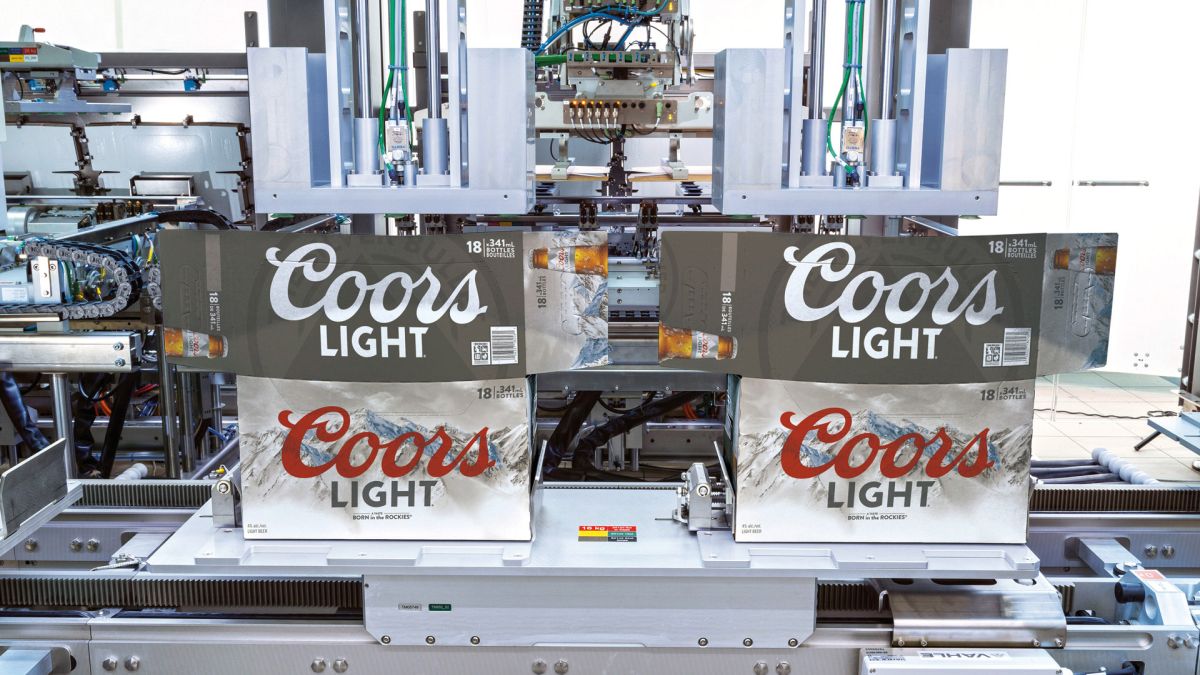
Der Transmodul-Transportroboter von Schubert befördert die Flaschen und Kartons durch die gesamte Verpackungsanlage und ermöglicht somit eine nahtlose Integration der drei Prozessschritte in ein System. (Bilder: Gerhard Schubert GmbH)
Nahtlose Integration durch das Transmodul
Das Verpackungssystem kombiniert drei Hauptfunktionen: das Aufrichten der Verpackungszuschnitte, das Befüllen der Verpackungsformate mit den Flaschen sowie das Verschließen der befüllten Verpackung. Die Prozesse Aufrichten und Verschließen übernimmt die TLM-Verpackungsmaschine von Schubert, das Befüllen der Kartons mit den Bierflaschen wird vom KHS-Flaschenpacker realisiert.
Der Transportroboter Transmodul von Schubert ermöglicht die schnittstellenfreie Kombination beider Systeme: Er befördert die Flaschen und Verpackungen innerhalb der gesamten Linie. Die Maschine verfügt über zwei Transmodulstrecken mit mehreren Transmodulen je Strecke. Jedes einzelne Transmodul ist mit einer leicht wechselbaren Formatplatte ausgestattet. Die Individualisierung dieser Formatplatten bietet dem Kunden vielfältige Möglichkeiten und hohe Flexibilität. Durch die Blocklösung der Komponenten von KHS und Schubert fallen lange Transfersysteme sowie separate Zuführ- und Auslaufbänder weg. Verschleiß, Wartungskosten sowie Energieverbrauch werden dadurch reduziert. Die kompakte Anlage benötigt lediglich einen Maschinenbediener.
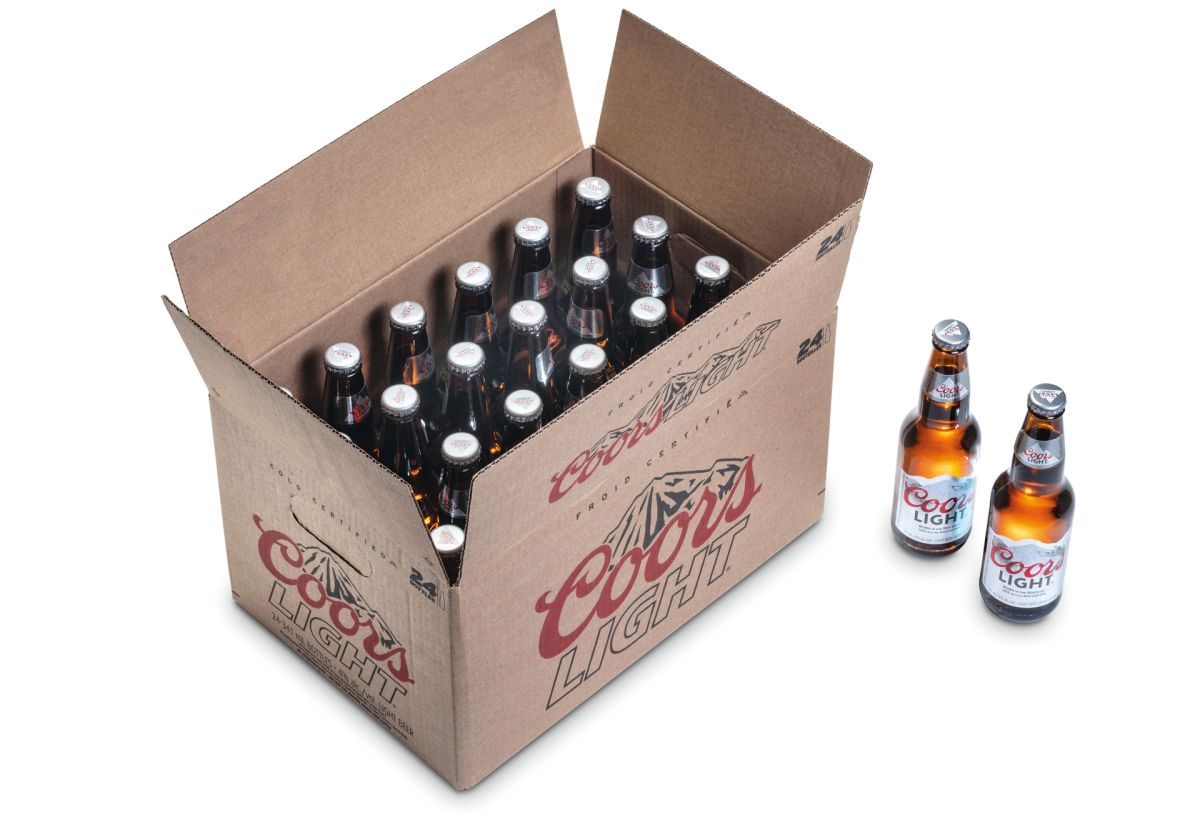
RSC-Karton mit 24 Coors-Light-Einzelflaschen. (Bild: Gerhard Schubert GmbH)
Maschinentechnik mit maximaler Flexibilität
Die Schubert-Aufrichtestation umfasst zwei F2-Roboter für das Aufrichten von RSC-Kartons sowie vier F2-Roboter für die Baskets oder Wrap-around-Kartons. Zusätzlich werden zwei F3-Roboter für das Entstapeln der Kartonzuschnitte eingesetzt. Die aufgerichteten Kartons werden auf den Transmodulen platziert. Pro Strecke fahren zwei Transmodule in den KHS-Flaschenpacker, der sie mit den Bierflaschen befüllt. Abweichend davon werden die Zuschnitte beim Verpacken von Baskets zunächst aufgerichtet und anschließend in einem RSC-Karton platziert. Danach befüllt die KHS-Einheit den RSC-Karton mit den Flaschen. Die Werkzeuge der Systemkomponenten aller drei Module lassen sich jederzeit einfach und schnell wechseln: Eine Formatumstellung der Anlage ist somit problemlos möglich.
Nach dem Befüllen erreichen die Transmodule die Verschließeinheit, in der sich zwei F2-Verschließroboter befinden. Die verschlossenen RSC-Schachteln verlassen anschließend die Anlage. Die Wrap-around-Kartons werden entweder ebenfalls entladen oder durch zwei F2-Transferroboter in zuvor aufgerichtete Trays gesetzt und danach auf dem Auslaufband platziert.
Mit der hochleistungsstarken Innopack-TLM-Anlage gelingt es Molson Coors, die wachsenden Marktanforderungen und Erwartungen der Konsumenten weiterhin zu erfüllen, und dem Wettbewerb stets einen Schritt voraus zu sein.
Weltweit bekannte Marke startete 1786
Seit den Anfängen 1786 hat sich die Molson Coors Brewing Company zu einem der weltweit größten und erfolgreichsten Bierhersteller entwickelt. Die führenden Marken des Unternehmens sind Bierliebhabern auf der ganzen Welt bekannt. Mit insgesamt sieben Produktionsstandorten und 3.000 Mitarbeitern setzt sich das Unternehmen Molson Coors aus den Gesellschaften Molson Coors Canada, MillerCoors, Molson Coors Europe und Molson Coors International zusammen.