Ein neues Verfahren zur Herstellung ableitfähiger Multilayerfolien hat das Laserzentrum der Fachhochschule Münster gemeinsam mit „EMPAC“ aus Emsdetten entwickelt. Statt des bislang üblichen Heißnadelperforationsverfahrens werden die Bohrungen auf den Aluminiumverbundfolien mit einem CO2-Laser gesetzt.
Schüttgüter können bald sicherer und wirtschaftlicher in Folienbeutel abgefüllt werden. Eine vom Laserzentrum am Fachbereich Physikalische Technik der Fachhochschule Münster entwickelte neue Verpackungstechnologie ermöglicht die Herstellung leistungsfähigerer und größerer Schüttgutverpackungen mit ableitfähigen Multilayerfolien. Als Industriepartner in einem öffentlich geförderten Entwicklungsprojekt fungiert dabei „EMPAC“ aus Emsdetten. Das Verpackungsunternehmen ist unter anderem auf Beutelverpackungen spezialisiert. Den Kontakt zum Industriepartner hatte die Transferagentur der Fachhochschule Münster hergestellt. EMPAC-Entwicklungsleiter Siegfried Hartmann steuerte seine Marktkenntnisse bei und erkannte schnell das Potenzial des neuen Lösungsansatzes.
Bereits im Juli 2017 – ein Jahr nach dem Start des vom Zentralen Innovationsprogramm Mittelstand (ZIM) des Bundesministeriums für Wirtschaft und Energie geförderten Projekts – ging die Fachhochschule Münster mit der bedeutenden Weiterentwicklung an die Öffentlichkeit. Damals waren noch nicht alle Patente angemeldet. Mittlerweile ist klar: Die Pilotanlage funktioniert, die Patentfragen sind geklärt, die Marktreife der von EMPAC und dem Laserzentrum gefundenen Lösung rückt näher. Derzeit steht noch die Integration der automatisierten Folienauf- und -abwicklung an. Damit ist ein externes Unternehmen beauftragt worden.
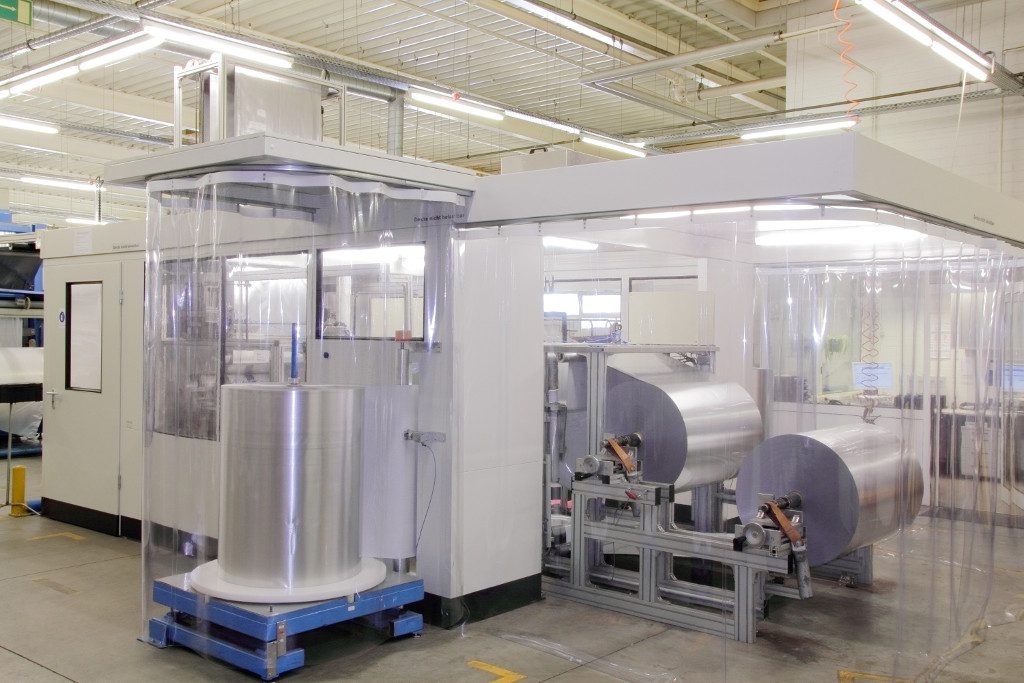
Projektziel ist eine komplette Folienfertigungsanlage ähnlich der abgebildeten, inklusive automatisierter Auf- und Abwicklung. (Foto: EMPAC)
Aluminiumverbundfolien sollen die Explosionsgefahr mindern
EMPAC und das Laserzentrum lösen ein altbekanntes Problem bei der Verpackung von Schüttgut in Folienbeutel: Es kann zu Staubexplosionen kommen. Beim Befüllen und Entleeren reibt sich das verpackte Material an den Innenwänden, die sich elektrostatisch aufladen. Ein einzelner Funke kann dramatische Folgen haben. Dieser Gefahr begegnet die Verpackungsindustrie bereits jetzt mit Multilayerfolien. In der Mitte der dreilagigen Folien befindet sich leitfähiges Aluminium, das die Ableitung der Ladungsträger ermöglicht. Allein: Die bisherige Herstellungsweise im Heißnadelperforationsverfahren ist sehr aufwendig und nur bedingt zuverlässig. Im schlimmsten Fall kann sie das Risiko von Staubexplosionen sogar erhöhen, erklärt Jürgen Gröninger, Projektleiter am Laserzentrum.
Gröninger beschreibt im Gespräch mit dem „packaging journal“ das bisherige Vorgehen so: „Bei diesem Verfahren wird die Polymerfolie zwischen zwei Rollen durchgewalkt, von denen die obere mit heißen Nadeln ausgestattet ist. Diese Nadeln durchstechen die Folie und bringen so die Bohrungen ein. Anschließend wird in einem weiteren Prozess die perforierte Folie auf den Aluminiumlayer kaschiert. Der hierbei genutzte Haftvermittler setzt sich in die zuvor eingebrachten Bohrungen, sodass anschließend kein Zugang zum Aluminium besteht. Daher wird die Multilayerfolie in einem abschließenden Prozessschritt einer Hochspannung ausgesetzt, die den Haftvermittler im Bereich der Bohrungen durchschlägt und so die Zugänglichkeit des Aluminiumlayers wiederherstellt.“
Weniger Aufwand und Risiken bei Perforation mit CO2-Laser
Der technische und logistische Aufwand bei diesem Verfahren sei erheblich, so Gröninger. Zudem berge es Risiken gleich auf zwei Ebenen, weil das nachträgliche Freilegen der Bohrungen nicht immer fehlerfrei verlaufe: Zum einen könnten Bohrungen weiterhin verschlossen bleiben und es steige die Explosionsgefahr, zum anderen könne die Hochspannung gleich die gesamte Multilayerfolie perforieren. Jürgen Gröninger warnt: „Geschieht dies, ist die Folie nicht mehr diffusionsdicht, und das empfindliche Füllgut kann in Kontakt mit schädlichen Umwelteinflüssen wie beispielsweise Luftfeuchtigkeit kommen.“ Damit nicht genug: Für moderne Multilayerfolien ist die Heißnadelperforation ebenfalls nicht geeignet. Folien mit einer höheren Traglast, die aus vier Materialien aufgebaut sind, können damit gar nicht bearbeitet werden.
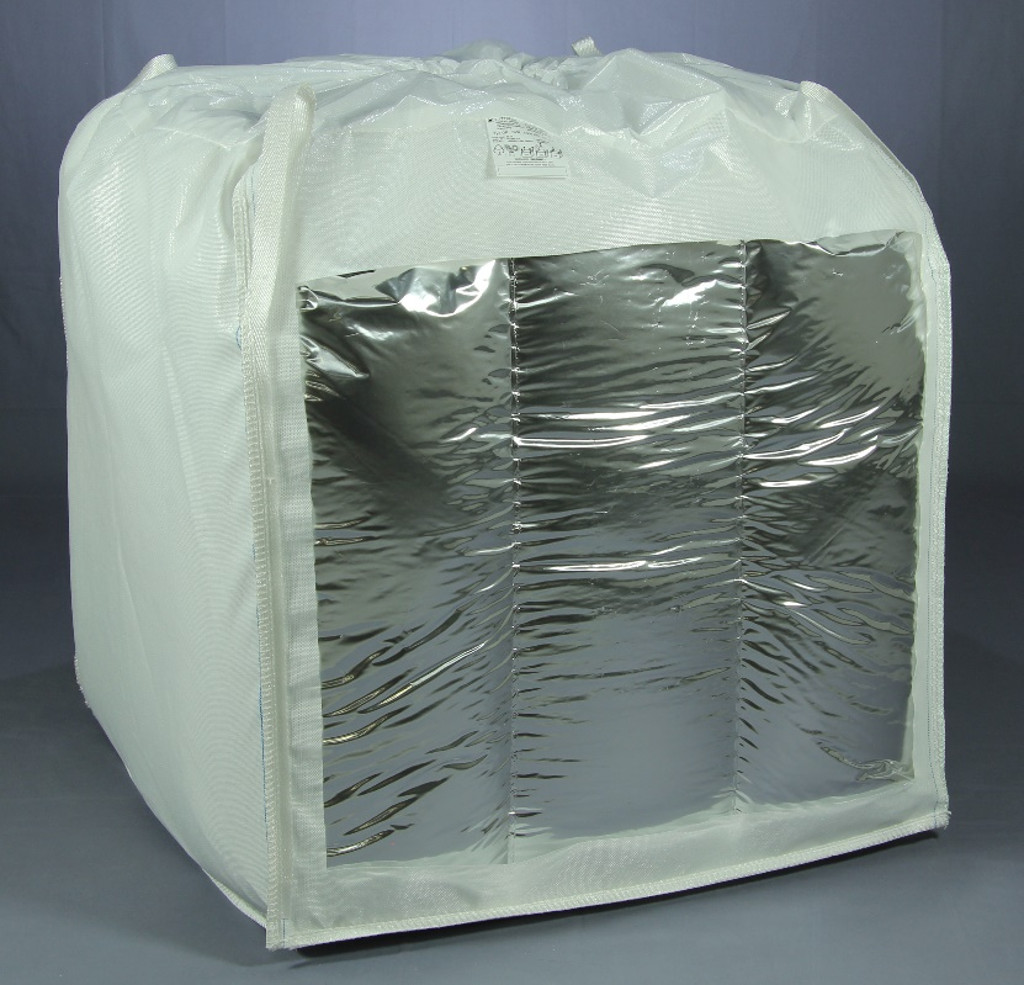
Formstabile Verpackungen wie die abgebildete mit einem Füllgewicht von mehr als einer Tonne können künftig mit ableitfähigen Multilayerfolien hergestellt werden. (Foto: EMPAC)
All diese Einschränkungen beseitigt das vom Laserzentrum und EMPAC entwickelte neue Verfahren. Die benötigten Bohrungen werden nun nicht mehr am Anfang der Folienproduktion gesetzt, sondern im letzten Schritt auf der fertigen Multilayerfolie. Zum Einsatz kommt dabei ein CO2-Laser. Damit werden die Bohrungen im wahrsten Sinne des Wortes punktgenau gesetzt. Ein Risiko, dass weitere Folienschichten zerstört werden, besteht nicht.
Die Einrichtung des CO2-Lasers war besonders herausfordernd, berichtet Jürgen Gröninger dem „packaging journal“. Dauer und Leistungsspitzen des Laserpulses mussten so konfiguriert werden, dass tatsächlich nur die etwa 150 Mikrometer dünne Folienschicht bis zum Aluminiumlayer perforiert wurde. Neben der Fokussierung des Lasers musste hier besonders darauf geachtet werden, dass die Folie mit gleichbleibender Spannung und unverändertem Abstand am Laser vorbeigeführt wurde. Anwendbar ist diese Art der Laserperforation für Folien mit einer Dicke von bis zu 0,4 Millimetern.
Neues Verfahren ist flexibler und auch für andere Anwendungsbereiche geeignet
Welche Vorteile bietet das neue Perforationsverfahren? Jürgen Gröninger fällt als Antwort auf diese Frage vor allem die größere Flexibilität ein. Bisher wurden die Bohrungen am Beginn des Produktionsprozesses gesetzt. Nun können Aluminiumverbundfolien nach einem gemeinsamen Standard hergestellt werden. Erst vor der Anwendung wird dann entschieden, ob daraus eine ableitfähige Folie werden soll oder nicht.
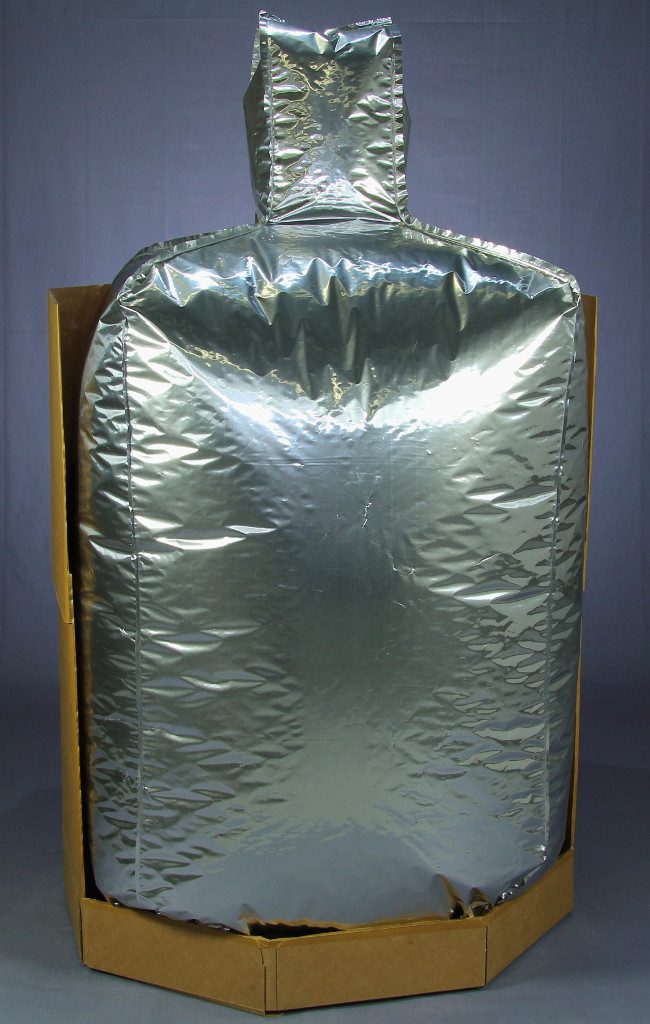
Dieser „Big Bag“ mit Aluminiumverbundfolien-Inliner ist etwa 1.000 x 1.000 x 1.200 Millimeter groß. Nach Abschluss des Entwicklungsprojekts kann er erstmals in einer ableitfähigen Ausführung für feinpulvrige, zündfähige Schüttgüter hergestellt werden. (Foto: EMPAC)
Insgesamt geht die Produktion der ableitfähigen Multilayerfolie schneller vonstatten, da viele Arbeitsschritte eingespart werden, die teilweise von Zulieferern erledigt werden müssen. Das führt natürlich zu einer wesentlichen Kostenersparnis.
„Das neue Verfahren eröffnet uns als Verpackungshersteller zusätzliche Anwendungen und ganz neue Horizonte“, sagt EMPAC-Entwicklungsleiter Siegfried Hartmann. „Dadurch sind zukünftig neue Produkte und eine erhebliche Qualitätssteigerung möglich.“ Grundsätzlich eigne sich das gemeinsam entwickelte Verfahren für die Verpackung aller Arten von Schüttgut. Aber auch zur Verpackung von Substanzen mit zündwilligen Lösemittelresten, wie sie in der chemischen Industrie vorkommen, kann es genutzt werden.
Als besonders interessant schätzen die Produktentwickler aus dem Münsterland neben der gesteigerten Prozesssicherheit die Belastbarkeit der neuartigen, ableitfähigen Multilayerfolien ein. Daraus gefertigte Verpackungen könnten doppelt so hohe Traglasten verkraften wie bisher übliche Produkte. Auch formstabile Verpackungen mit einem Füllgewicht von bis zu 1,5 Tonnen können nun hergestellt werden. Das Aussehen dieser Verpackungen beschreibt Jürgen Gröninger so: „Die äußere Form ähnelt dann einer großen Vakuum-Kaffeeverpackung.“