Als Josef Pöppelmann vor 67 Jahren in einem Hühnerstall in Lohne eine Korkenfabrik gründete, konnte er noch nicht absehen, welche rasante Entwicklung dieser Betrieb nehmen würde. Heute fertigt die Pöppelmann GmbH & Co. KG als einer der führenden Kunststoffverarbeiter in Europa hochwertige Funktionsteile und Verpackungen – bei Bedarf auch unter Reinraumbedingungen.
Ob Flaschenverschlüsse, Schutzelemente, Pflanzentöpfe oder Laborgefäße – die Firmengruppe Pöppelmann vereint seit fast sieben Jahrzehnten in ihrem Produktportfolio Tradition und Fortschritt. Das auf Basis einer einfachen Geschäftsidee gegründete Familienunternehmen gehört heute zu den führenden Herstellern in der kunststoffverarbeitenden Industrie.
Mit seinen fünf Produktionsstandorten sowie über 550 Spritzgießmaschinen, Tiefziehanlagen und Extrudern ist Pöppelmann einer der wichtigsten Arbeitgeber in der Region und beliefert Kunden in mehr als 90 Ländern. Über 2.000 hochqualifizierte Mitarbeiter sind weltweit für den Erfolg des Unternehmens tätig.
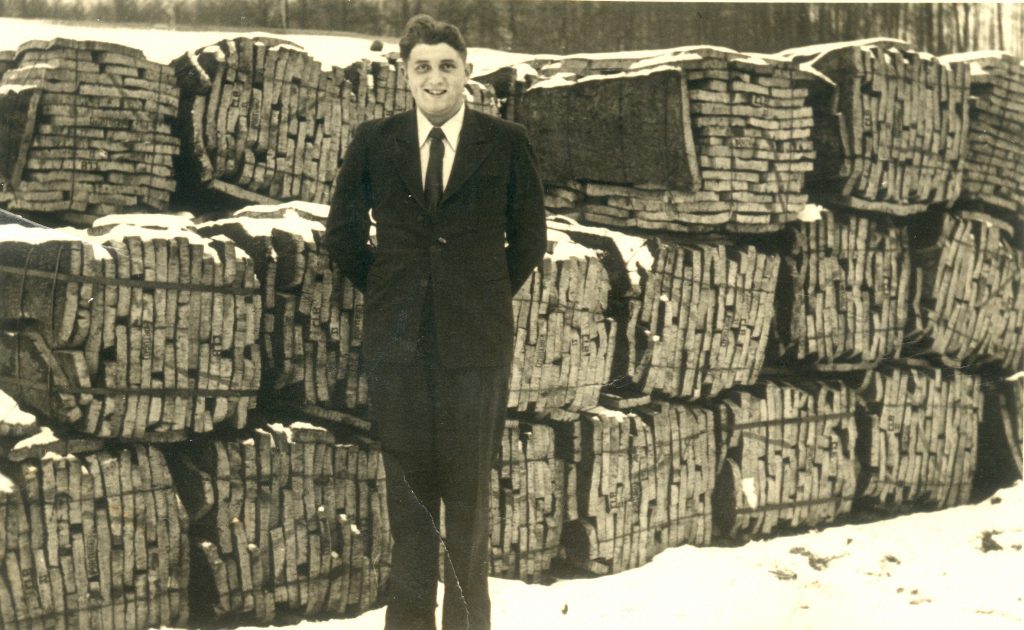
Firmengründer Josef Pöppelmann (im Bild) funktioniert gemeinsam mit seinem Bruder Hubert im Juli 1949 einen alten Hühnerstall in Lohne zur „Korkenfabrik Gebrüder Pöppelmann“ um.
Der Weg vom Kork zum Kunststoff
Im Februar 1949 stellten die Brüder Joseph und Hubert Pöppelmann einen „Antrag auf Genehmigung zur Eröffnung einer Korkenfabrik“ an die Stadtverwaltung im niedersächsischen Landkreis Vechta. „Die ersten Produkte waren Verschlüsse aus Kork von der Korkeiche, gefertigt auf einer Handschneidemaschine für Flaschenkorken“, erzählt Torsten Ratzmann, seit Anfang 2016 Vorsitzender der Geschäftsführung. „Für die jungen Unternehmer wurde ein alter Hühnerstall auf dem elterlichen Bauernhof in Brockdorf bei Lohne umfunktioniert“.
In die Kunststoff-Ära startete das noch junge Unternehmen im Frühjahr 1955 mit dem Kauf einer Spritzgussmaschine auf der „Deutschen Industrie-Messe Hannover“. Norbert Nobbe, der gemeinsam mit Ratzmann die Geschäfte von Pöppelmann führt, erklärt: „Damit legte Pöppelmann den Grundstock der heutigen vier Geschäftsfelder.“ In den Folgejahren wurden der Werkzeugbau und die Präsenz auf dem internationalen Kunststoffmarkt verstärkt.
- Torsten Ratzmann ist seit Anfang 2016 Vorsitzender der Geschäftsführung von Pöppelmann.
- Norbert Nobbe leitet an der Seite von Torsten Ratzmann die Geschicke des Unternehmens.
- Engelbert Rechtien leitet bei Pöppelmann FAMAC den Vertrieb.
Auf die Einführung des KAPSTO-Markenprogramms für Kappen und Stopfen folgten mit dem K-TECH-Programm die ersten technischen Kunststoff-Spritzgussteile und wenige Jahre später mit dem TEKU-Programm Pflanztöpfe aus Kunststoff.
„Die Firma hat ihre Innovationsfähigkeit stetig ausgebaut und ihre Kunststoffprodukte auf die vielseitigen Bedürfnisse verschiedener Branchen zugeschnitten“, fasst Torsten Ratzmann die Entwicklung der ersten drei Geschäftsbereiche der Unternehmensgruppe zusammen.
1955 Erste Kunststoff-Spritzgussmaschine.
1957 Aufbau von KAPSTO – Kappen und Stopfen für die industrielle Anwendung.
1962 Einführung des K-TECH-Programms – hochpräzise technische Kunststoff-Spritzgussteile.
1966 Erste Auslandsniederlassung in Frankreich (Mulhouse, Rue du Rhin).
1970 Das TEKU-Programm startet mit der Produktion der ersten Blumentöpfe.
1998 Aufbau von FAMAC – Funktionsteile und Verpackungen.
2004 Inbetriebnahme der Reinraumproduktion.
2007 Pöppelmann Plastics USA eröffnet Standort mit dem Geschäftsbereich TEKU in Claremont, North Carolina.
2014 Pöppelmann FAMAC erweitert seine Reinraum-Kapazitäten.
Funktionsteile und Verpackungen als vierter Geschäftsbereich
Mit FAMAC führen die Kunststoffexperten seit 1998 einen vierten Geschäftsbereich für Verpackungen und Funktionsteile, die in der Lebensmittel-, Pharma- und Kosmetikindustrie sowie in der Medizintechnik zum Einsatz kommen. Neben einem breitgefächerten Standardprogramm sind Sonderlösungen zu wirtschaftlichen Konditionen verfügbar.
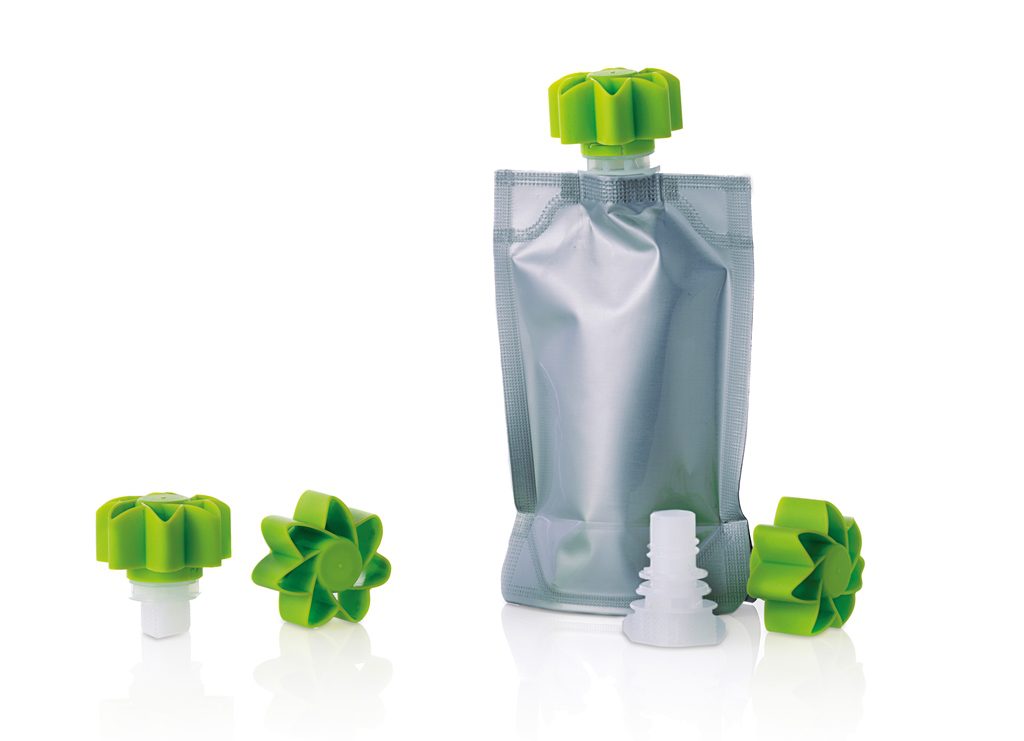
Der Einschweißausgießer wird im Kompetenzbereich Pöppelmann FAMAC® entwickelt und produziert.
„Dabei erhalten die Kunden von der Entwicklung bis hin zur Serienfertigung alles aus einer Hand und profitieren von den Ressourcen, Partnern und Kontakten der Pöppelmann-Gruppe“, erklärt Engelbert Rechtien, der den Vertrieb bei FAMAC leitet. Für eine enge interne und externe Abstimmung sorgt ein eigener Projektleiter, der dem Auftraggeber über den kompletten Prozess hinweg als fester Ansprechpartner zur Verfügung steht.
Spritzgussprodukte aus dem Reinraum
Die Herstellung der Spritzgussprodukte erfolgt mit höchstem Anspruch nach den Regeln der Good Manufacturing Practice (GMP). „Seit 2004 fertigen wir Laborgefäße und andere Produkte sowie komplexe Baugruppen für die Medizin- und Pharmaindustrie unter Reinraumbedingungen, bei Bedarf inklusive der jeweiligen Primärverpackung“, betont Engelbert Rechtien.
Produziert wird in zwei Reinräumen nach DIN EN ISO 14644 Klasse 7 und GMP-Standard – C mit separatem Klimatisierungs- und Filtersystem. Ein zertifiziertes Qualitäts- sowie ein Hygienemanagementsystem bieten dabei zusätzlich Sicherheit.
Die Mitarbeiter tragen besondere Schutzkleidung und sind entsprechend geschult. Regelmäßige Kontrollen gewährleisten einen Partikel- und Keimanteil gemäß der implementierten Standards.
„Speziell bei Produkten für die Pharmaindustrie und Medizintechnik werden vom Start der Bauteilentwicklung bis zur Freigabe der Werkzeugkonstruktion höchste Anforderungen an die Technik und Qualität gestellt, Kriterien, die wir bei FAMAC aufgrund unserer Kompetenzen sicher und immer im Sinne des Kunden umsetzen“, ergänzt Rechtien.
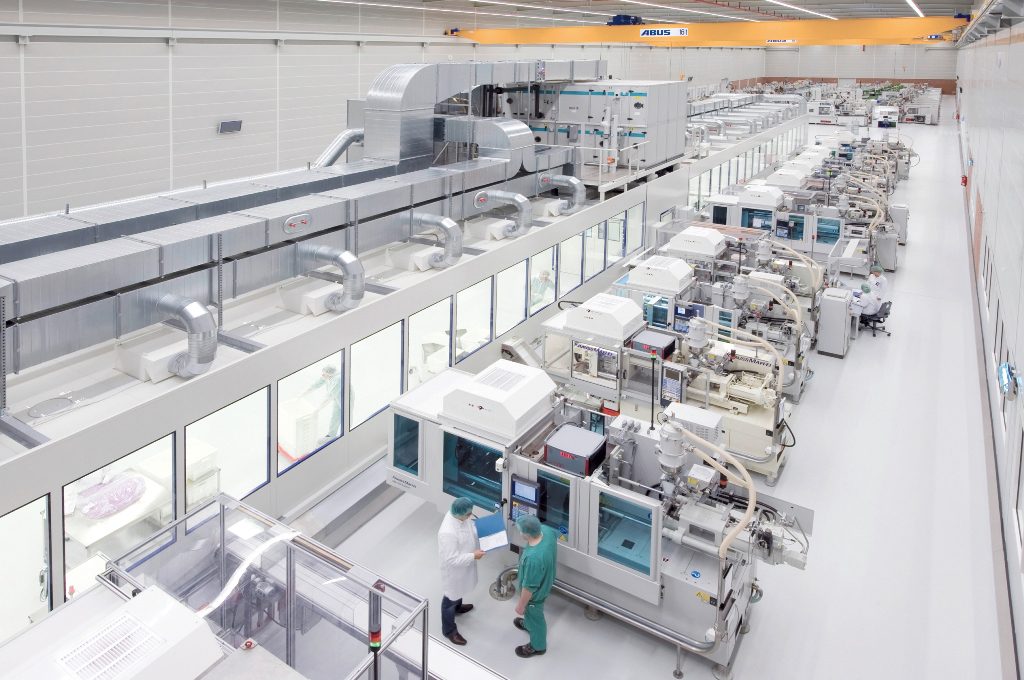
Um den Anforderungen an hygienischen Verpackungen im Medizin- und Pharmabereich gerecht zu werden, fertigt Pöppelmann auf Kundenwunsch auch unter Reinraumbedingungen.
Die Spritzgussmaschinen produzieren von außen in den Reinraum hinein. Bei Bedarf können sie abgekoppelt werden, um in anderen Produktionsbereichen zum Einsatz zu kommen. Die Werkzeuge werden in einem eigenen abgesonderten Bereich des Pöppelmann-Formenbaus hergestellt.
Dieser Formenbau ist seit über 50 Jahren für die Konstruktion der Spritzgieß- und Thermoformwerkzeugen für alle Geschäftsbereiche zuständig und umfasst heute rund 130 Formenbauer und Werkzeugkonstrukteure. Die Bandbreite bei den Spritzgießformen reicht von standardisierten Kontureinsätzen bis hin zu Etagenwerkzeugen.
Mit Rapid Prototyping schneller zur Serienreife
Der hauseigene Werkzeugbau ermöglicht auch ein Arbeiten mit Versuchs- und Vorserienwerkzeugen. Dank Rapid Prototyping per Stereolithographie, Selektives-Laser-Sintern und PolyJet-Matrix-Technologie stehen bei Pöppelmann bereits in frühen Entwicklungsphasen individuelle Erprobungsmuster in unterschiedlichen Materialien zur Verfügung. „Wenn wir eine Anfrage für ein Produkt bekommen, entwickeln wir daraus nicht nur eine Zeichnung, sondern produzieren innerhalb von Stunden einen Prototypen, den der Kunde anfassen, prüfen, begreifen kann“, erläutert Engelbert Rechtien das Prinzip.
Die von Pöppelmann im 3D-Druck erzeugten Muster kommen der endgültigen Lösung bereits „so nah, dass der Kunde seine Funktionen unter realistischen Bedingungen testen kann. So kann er sofort erkennen, ob seine Erwartungen erfüllt werden und welche Fehler eventuell noch ausgemerzt werden müssen“, erklärt der Vertriebsleiter weiter.
Nach der engen Abstimmung mit dem Kunden wird die Prozessfähigkeit des Bauteils hinsichtlich der Applikationsanforderungen unter die Lupe genommen. Ziel dieser Funktionsprüfung ist immer die Serienreife. Erst wenn diese erreicht ist, wird mit der Anfertigung eines Werkzeugs für die Serienproduktion begonnen.
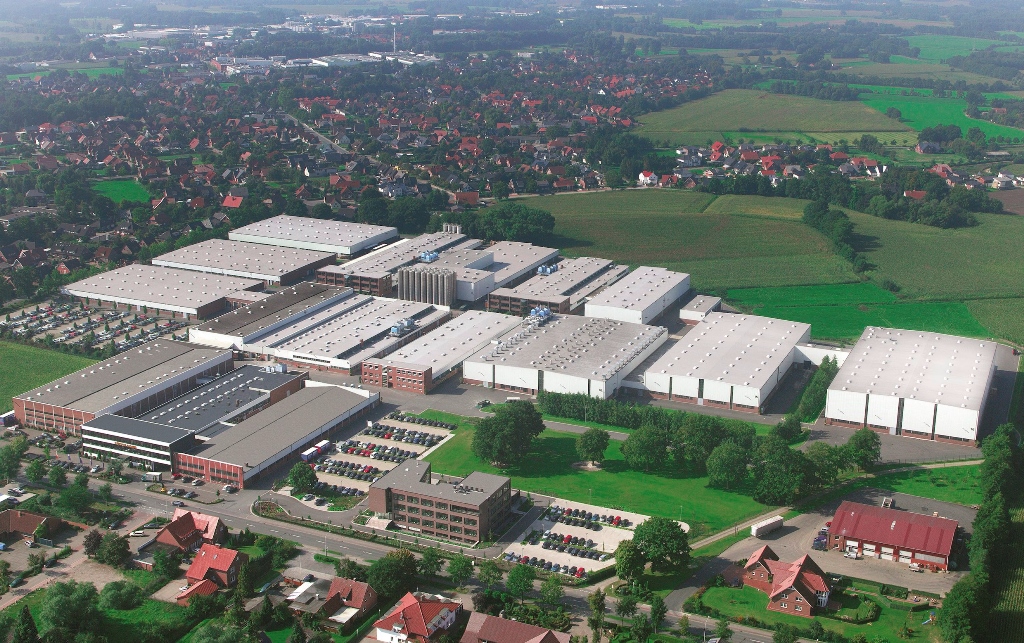
47 Jahre nach der Firmengründung wird das Werk 2 in Brockendorf fertiggestellt. Hier findet fortan die Produktion der KTECH-Sparte statt.
Multifunktion durch modernes Equipment
Für die Herstellung der Verpackungen und Funktionsteile kommt bei Pöppelmann FAMAC ein moderner Maschinenpark mit Schließkräften zwischen 250 und 13.000 kN zum Einsatz. Ausgestattet mit Spritzgussanlagen in unterschiedlichen Dimensionen und Ausführungen ermöglicht er die wirtschaftliche Produktion durch das Zweikomponenten-Spritzgießen. „Dieses Verfahren erlaubt uns das Verbinden von unterschiedlichen Kunststoffen mit gegensätzlichen Eigenschaften zu einem Bauteil“, erläutert Rechtien.
Dadurch lassen sich harte und weiche oder verstärkte und gleitoptimierte Kunststoffe kombinieren. Außerdem sind mehrfarbige Teile sowie die formschlüssige Verbindung zweier nichthaftender Kunststoffe möglich. „Kommen dafür zwei konventionelle Standard-Spritzgussmaschinen zum Einsatz, entsteht das Zweikomponententeil durch Umsetzen des Vorspritzlings auf die zweite Maschine für den zweiten Kunststoff“, schildert Engelbert Rechtien den Vorgang.
Die nächste Stufe bilden Spritzgussmaschinen mit zwei Einspritzeinheiten für beide Materialien. Hier entsteht der Vorspritzling in der ersten Werkzeugstation. Dann öffnet sich das Werkzeug und dreht sich auf einer Indexplatte, sodass der Vorspritzling in die zweite, vergrößerte Kavität gelangt. Das Werkzeug schließt und der zweite Kunststoff wird eingespritzt. Das Produkt lässt sich in einem Ablauf fertigstellen; der Aufwand für Montage und Nachbearbeitung entfällt.
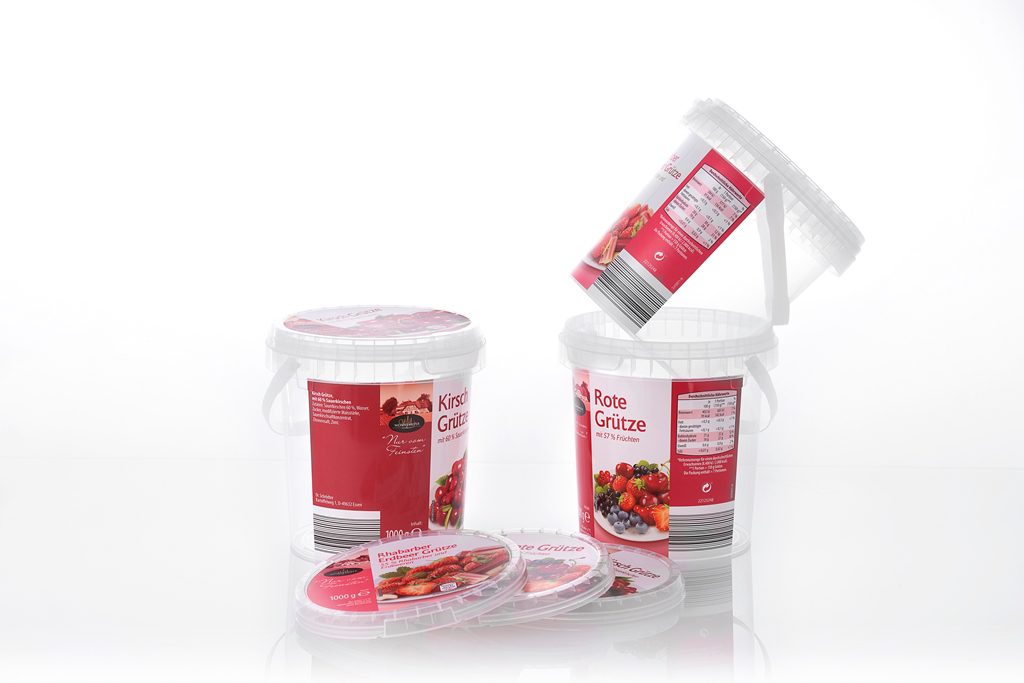
Durch IML werden Behälter oder Deckel, wie z. B. beim Rundeimer, direkt bei der Formgebung mit einem Etikett versehen.
Mit Innovationen Trends setzen
Durch den Einsatz neuer Technologien bringt Pöppelmann regelmäßig innovative Verpackungslösungen auf den Markt. Nicht selten kommt am Ende des Entwicklungs- und Designprozesses eine prämierte Lösung heraus. So erhielt FAMAC mit dem Snack-Besteck Göffel, einer Alternative zu herkömmlichen Einwegbestecken, den Deutschen Verpackungspreis 2014.
„Um unseren Kunden aus der Lebensmittelindustrie bestmögliche Voraussetzungen für ein erfolgreiches Bestehen im Markt zu bieten, achten wir bei FAMAC auf intuitives Design, individuell hochwertige Optik und hervorragende Maschinengängigkeit“, sagt Rechtien.
Für die Dekoration verfügt Pöppelmann mit dem In-Mould-Labeling (IML) über eine wirtschaftliche Lösung. Bei dieser Art der Dekoration erfolgt das Aufbringen des Labels während des Spritzgießvorgangs. Dazu positioniert ein Roboter die bedruckte Kunststoff-Folie (< 50 µm) im Werkzeug. Dort wird sie fixiert und mit dem Behältermaterial hinterspritzt. Nach dem Spritzgießprozess bilden Etikett und Formteil eine untrennbare Einheit mit durchgehender Oberfläche. Das Verfahren bietet den Vorteil einer deutlichen Zeit- und Kostenersparnis. Zudem lassen sich IML-dekorierte Verpackungen problemlos recyceln.
Regional verankert in die Zukunft
Wie zu Zeiten des 1983 verstorbenen Joseph Pöppelmann ist stetiger Fortschritt bis heute ein Kernbestandteil der Unternehmensphilosophie. Mit Tochtergesellschaften und Niederlassungen in Frankreich, Spanien, England, Dänemark, Belgien und den Niederlanden ist Pöppelmann europaweit in der Kunststoffverarbeitung präsent. Geblieben sind die Bodenständigkeit und die Standorttreue zu Lohne. Das regional stark verankerte Unternehmen bildet seine Fachkräfte seit 1956 weitgehend selbst aus.
„In Zeiten zunehmender Automatisierung wird es immer wichtiger, hoch qualifiziertes Personal im eigenen Unternehmen zu fördern und weiterzuentwickeln“, betont Torsten Ratzmann.
Pöppelmann stellt sich dieser Herausforderung durch die Ausbildung engagierter junger Menschen in den Bereichen Entwicklung, Werkzeugmaschinenbau, Logistik und Vertrieb sowie durch strukturierte Weiterbildungsmöglichkeiten. „Mit aktuell mehr als 170 Auszubildenden sind wir einer der größten Ausbildungsbetriebe in der Region Oldenburger Münsterland“, sagt Ratzmann. Insgesamt hat das Unternehmen in den vergangenen Jahren über 1.200 junge Menschen in verschiedenen Berufen ausgebildet. „Sie tragen wie alle Pöppelmänner und Pöppelfrauen weltweit maßgeblich zum Erfolg der Unternehmensgruppe bei“, so der vorsitzende Geschäftsführer.