Mit einem kollaborierenden Roboter hat die Gustav Hensel GmbH aus Lennestadt ihre Produktionsprozesse optimiert. Ein Roboterarm von Universal Robots unterstützt die Beschäftigten beim Palettieren von fertig verpackten Kabelabzweigkästen. Nun müssen 2,5 Tonnen Paketmasse pro Schicht nicht mehr manuell bewegt werden.
Die Gustav Hensel GmbH & Co. KG im sauerländischen Lennestadt fertigt nach dem „Lean-Prinzip“. Rund 550 Mitarbeiterinnen sowie Mitarbeiter entwickeln und produzieren Elektroinstallations- und Verteilungssysteme. Automation hilft dabei, die Prozesse entlang der gesamten Wertschöpfungskette effizient zu betreiben und die Produktion am heimischen Standort zu sichern.
Auf der Suche nach weiteren Optimierungsmöglichkeiten identifizierte das mittelständische Unternehmen die Palettierung fertig verpackter Kabelabzweigkästen als Einsparpotenzial. Bislang entfielen auf diese Tätigkeit sehr viele Mannstunden. Christoph Kaiser, Leiter der Kunststofffertigung bei Hensel, betont: „Unser Ziel war es dabei, nicht die Mitarbeiter zu ersetzen, sondern vermehrt Kapazitäten für höherwertige Tätigkeiten zu schaffen. Vom Lean-Gedanken her waren das manuelle Packen und Bündeln der Kartons absolut nicht wertschöpfend.“
Um die Palettieraufgabe zu automatisieren, entschied sich Hensel für einen kollaborierenden Roboter von Universal Robots (UR). Beim Besuch einer Fachmesse stellte sich heraus, dass das Angebot des dänischen Unternehmens den Anforderungen am besten genügte. Der Roboter sollte nicht eingehaust werden. Gewünscht war vielmehr ein ständiger, direkter Zugriff. Außerdem sollte er eine recht hohe Traglast bewältigen können und eine große Reichweite haben.
Palettierroboter sollte ohne Umhausung auskommen
„Wenn der Roboter die Verpackungseinheiten ganz nach unten auf eine Palette stellen muss, ist sein umfangreicher Arbeitsradius enorm wichtig“, erklärt Christoph Kaiser. Den Anforderungen entsprach schließlich das größte Robotermodell UR10 mit einer Traglast von zehn Kilogramm und einer Reichweite von 1,3 Metern am besten.
Realisiert wurde das Projekt „Erster Cobot“ seit dem Frühjahr 2017 schließlich mithilfe des UR-Partners Dahl Automation GmbH. Das Unternehmen aus Meinerzhagen unterstützte Hensel auch bei der Risikobeurteilung für den Roboterarm. Diese war nötig, damit das System in unmittelbarer Nähe der menschlichen Kollegen arbeiten kann. Grundlage dafür sind die patentierten Sicherheitssysteme von UR.
Insgesamt dauerte die Integration des UR10 bei Hensel nur wenige Tage. André Gödde, Vertriebsleiter bei Dahl Automation, verrät: „Bevor wir einen Roboterarm von UR bei unseren Kunden in Betrieb nehmen, testen wir die Applikation in unserem eigenen Werk auf Herz und Nieren. So können wir schnell reagieren, falls beispielsweise noch Bewegungsabläufe optimiert werden müssen.“ Der Aufbau beim Kunden sei so im Durchschnitt in ein bis zwei Tagen abgewickelt.
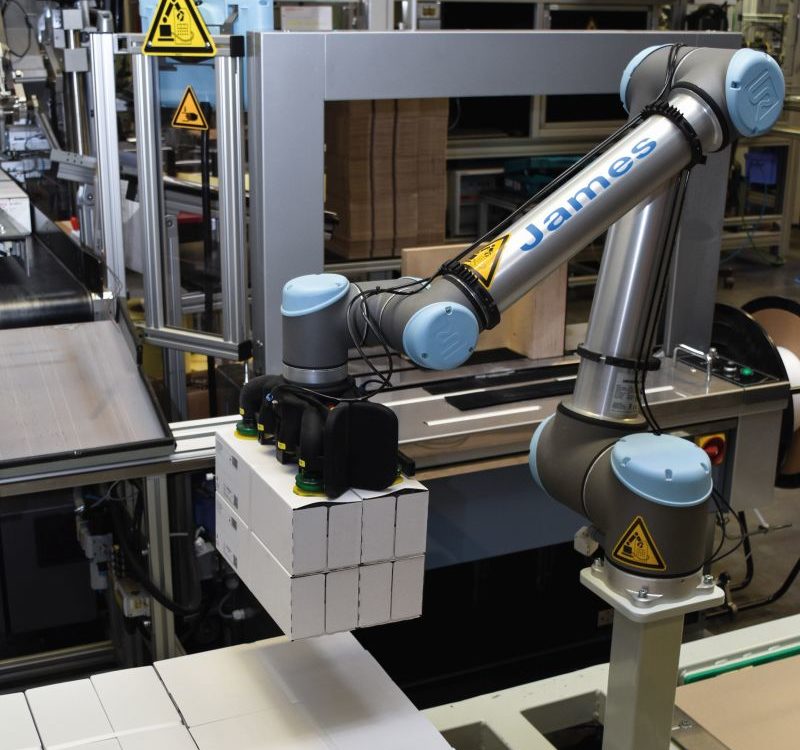
Der Sauggreifer des UR10 wurde durch die Dahl Automation GmbH eigens für Hensel entwickelt. (Bild: Universal Robots)
Kollaborierender Roboter schafft 1.200 Verpackungseinheiten pro Schicht
Mittlerweile palettiert der UR-Roboter im Zweischichtbetrieb 1.200 Verpackungseinheiten pro Schicht. Der UR10 ist die letzte Komponente in einer komplexen, vollautomatischen Anlage aus Montage- und Verpackungsmaschinen zur Herstellung von Kabelabzweigkästen. Die Anlage stellt dem Roboterarm jeweils zwei fertig verpackte Produkte bereit. In einem ersten Schritt greift der UR10 die beiden Kartons mit einem speziell von Dahl Automation angefertigten Sauggreifer und setzt sie in eine Umreifungsmaschine. Nachdem er dort ein weiteres Paketpaar zur Bündelung in eine Vierereinheit abgestellt hat, umreift die Maschine diese. Im Anschluss stapelt der Roboterarm die Kartonbündel auf einer Europalette ab. „Knapp zehn Kilogramm hebt der UR10 bei diesem letzten Vorgang, womit wir seine Traglast voll ausnutzen“, sagt Christoph Kaiser.
Zur weiteren Effizienzsteigerung stellt Hensel dem UR-Roboter gleich zwei Europaletten bereit. Ist eine davon voll, stapelt der UR10 automatisch am anderen Palettenplatz weiter. „Der Mitarbeiter muss dann nur noch die volle Europalette rausfahren und eine nächste für den UR-Roboter bereitstellen“, weist Kaiser auf die optimale Auslastung der Applikation hin.
Je nach Bedarf kann der Roboterarm vier verschiedene Kartongrößen verarbeiten. Dafür lässt er sich in unter drei Minuten mit nur wenigen Klicks umprogrammieren.
„Unsere tägliche Arbeit ist körperlich deutlich leichter, allerdings auch durch moderne Fertigungsmethoden wie die Automatisierung anspruchsvoller geworden.“
Lydia Reichling arbeitet als Schichtarbeiterin ständig mit dem Cobot „James“ zusammen.
Palettierroboter erspart monotones und belastendes Stapeln
Die Entlastung der Beschäftigten bei Hensel fällt deutlich aus. Der UR10 übernimmt das monotone und belastende Stapeln der Kartons auf die Paletten – und wurde deswegen von seinen menschlichen Kollegen „James“ getauft. „Etwa 2,5 Tonnen Paketmasse mussten pro Schicht bewegt werden“, erinnert sich Christoph Kaiser.
Für die Bedienung des Palettierroboters wurden zunächst zwei Fertigungsmitarbeiter bei Hensel online in der „Universal Robots Academy“ geschult. Tiefer gehendes Robotik-Know-how brachte Dahl Automation den Anwendern dann in einer weiteren Tagesschulung bei.
Insgesamt zeichnet sich der UR10 durch seine leichte Bedienbarkeit aus. Gelegentliche Unterbrechungen des Roboterbetriebs können die beiden Schichtarbeiterinnen, die im Produktionsalltag mit dem Roboter interagieren, selbst beheben.
Wenn jemand etwa versehentlich an den Roboterarm stößt und die integrierte Funktion zum Sicherheitsstopp von UR greift, starten die Kolleginnen ihn mit nur zwei Klicks auf dem Teach Panel neu. Der UR10 ist dabei so konzipiert, dass er im Anschluss seinen normalen Zyklus reibungslos weiter ausführt.
Zweiter Cobot hat bereits seinen Dienst aufgenommen
Das Projekt des ersten Cobots war erfolgreich, ist man sich bei Hensel einig. Bei den Mitarbeiterinnen kommt die „Hilfe“ des Automationssystems gut an. Denn während der UR10 beständig palettiert, können sie sich nun noch intensiver mit der Optimierung der Montageanlagen selbst befassen. Das steigert insgesamt die Produktivität in der Herstellung der Kabelabzweigkästen.
Die guten Erfahrungen mit dem UR10 haben die Verantwortlichen ermutigt, einen weiteren Cobot einzusetzen. Seit Herbst 2018 unterstützt ein neuer Roboterkollege die Belegschaft im Hensel-Zweigwerk Würdinghausen nicht nur bei der Palettierung, sondern auch in der Qualitätsprüfung von Membranen