Mit der Erfindung des Drahtwälzlagers ist die Franke GmbH Spezialist für rotative und lineare Bewegungen. Seit 1954 ist nicht nur das Produktportfolio gewachsen, sondern auch die Zahl der Mitarbeiter und Mitarbeiterinnen. Das erfordert mehr Fläche, deshalb gab es nun den Spatenstich für das neue Werk 6.
Bei Franke entstehen leise Präzisionslager für Computertomographen genauso wie leichte Lager aus dem 3D-Drucker. Die Lager finden sich in der Medizintechnik, in Strickmaschinen oder in Werkzeugwechslern. Sie bestücken Leiterplatten in Höchstgeschwindigkeit oder drehen zu tausenden riesige Solarpanel dem Lauf der Sonne hinterher. Gegenwärtig wird wieder gebaut: Bis Mitte 2024 entsteht das neue Werk 6.
Die Möglichkeiten zur Herstellung von Produkten sind heute vielfältiger als je zuvor. Moderne Materialien und Methoden bieten einen reichen Fundus an Produktionsmöglichkeiten, angefangen von einfacher Handarbeit bis hin zur additiven Fertigung mittels 3D-Druck. Franke Drahtwälzlager besitzen Laufringe aus Stahldraht, die als Laufbahn für Kugeln dienen. Ihre Herstellung erfolgt nach traditionellen Methoden. Die Gehäuseteilen der Lager werden auf modernen, programmierbaren CNC-Maschinen gefertigt und sowohl einzeln als auch in großen Serien hergestellt. So treffen im Produktionsprozess Manufaktur und CNC-Technologie direkt aufeinander.
Die Digitalisierung ist auch ein Thema. Gemeinsam mit den Teams konnten die Prozesse in der internen Wissensdatenbank Franke-WIKI abgebildet werden. Das Unternehmen arbeitet daher an der Feinplanung von Aufträgen, der Schaffung eines Kundenportals auf der Website sowie der Umstellung des internen Dokumenten-Managements und der Kollaboration auf das Cloud-basierte Microsoft 365.
Mit Blick auf das Thema Nachhaltigkeit strebt das Unternehmen die Klimaneutralität bis 2025 an. Bereits im Jahre 2019 wurde erstmals ein CO² Fußabdruck berechnet, dieser lag damals bei 990 Tonnen. Des weiteren wurde der CO² Fußabdruck eines der Kernprodukte ermittelt: des Hauptlagers für Computertomographen. Hierbei stellte sich heraus, dass 80 Prozent der Emissionen des Produktes in vor- oder nachgelagerten Prozessen stattfinden. Daraufhin wurden gemeinsam mit Zulieferern nach Wegen gesucht, um auf klimafreundliche Prozesse umzustellen und diese zu etablieren.
Quelle: Franke GmbH
Weitere Meldungen aus den Unternehmen
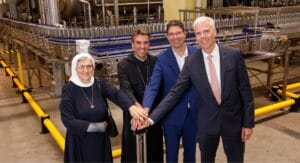
Adelholzener nimmt neue Abfüllanlage in Betrieb
Mit einer Kapazität von bis zu 36.000 Flaschen pro Stunde und einer möglichen Jahresproduktion von 100 Millionen Flaschen erweitert das Unternehmen seine Abfüllkapazitäten damit deutlich.
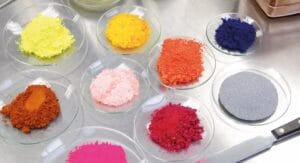
Siegwerk baut seine Präsenz im Nahen Osten aus
Das Unternehmen wird mit dem neuen Büro- und Lagergebäude in Dubai die Verpackungsindustrie im Nahen Osten besser bedienen können.
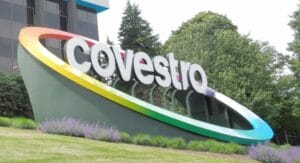
Covestro stärkt Geschäft mit Spezialfolien
Der Kaufpreis wurde nicht bekannt gegeben. Die Finanzierung erfolgt laut Covestro aus Barmitteln.
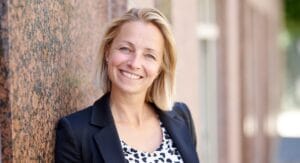
European Bioplastics verlegt Hauptsitz nach Brüssel
European Bioplastics (EUBP) hat seinen Hauptsitz offiziell nach Brüssel verlegt und ernennt Lorenza Romanese zur neuen Generalsekretärin.
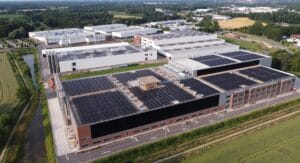
Pöppelmann eröffnet neue Produktionshalle in Lohne
In der neuen Halle 43 am Standort Lohne-Brockdorf sind künftig die Division Kapsto sowie die Kleinteilefertigung des Unternehmens angesiedelt.
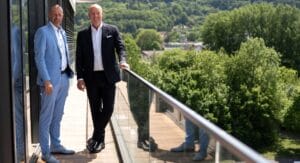
Prodinger feiert 100-jähriges Bestehen und begrüßt neuen CEO
Die Prodinger Gruppe feiert am 1. Juli ihr 100-jähriges Jubiläum und begrüßt mit Markus Ettlin einen neuen CEO, der fortan an der operativen Spitze des Familienunternehmens steht.